An aluminum plate or aluminum strip made of aluminum is the main raw material mixed with other alloying elements. Aluminum strip is an essential basic material for developing my country’s national economy and is widely used in aviation, aerospace, construction, printing, transportation, electronics, chemicals, food, medicine, and other industries.
Driven by the rapid development of the economy, the investment in aluminum plates and strips in my country has continued to heat up, and the consumption of aluminum plates and strips has continued to grow steadily. The demand for exterior building and interior decoration, aluminum foil manufacturing, printing, PS plate, manufacturing, home appliances, food packaging, and other industries has further increased, becoming the main driving force for the growth of aluminum sheet and strip consumption. At the same time, the transportation industry is becoming a new consumption growth point.
Already know much about economic aluminum, how much do you know about Aluminium production? Keep read on this article, and you will know.
General Aluminium Alloy Production Process
Aluminum alloy cold rolling is generally divided into casting – hot rolling – cold rolling – finishing.
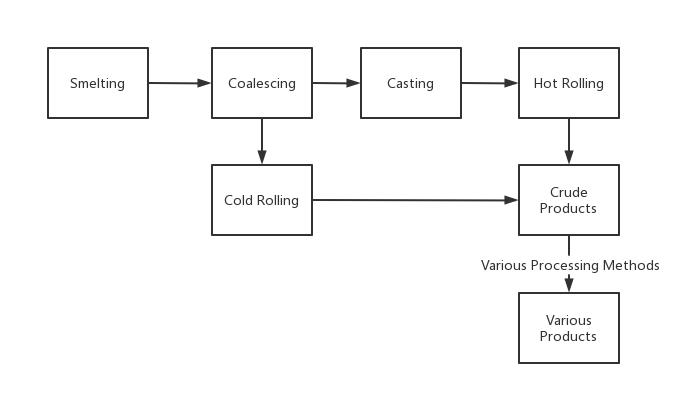
Purpose of Smelting and Casting
The purpose of smelting and casting is to produce alloys with satisfactory composition and high melt purity and create favorable conditions for casting alloys of various shapes.
The steps of the melting and casting process: batching – feeding – melting – stirring after melting, slag removal – pre-analysis and sampling – adding alloy to adjust the composition, stirring – refining – standing – guiding furnace casting.
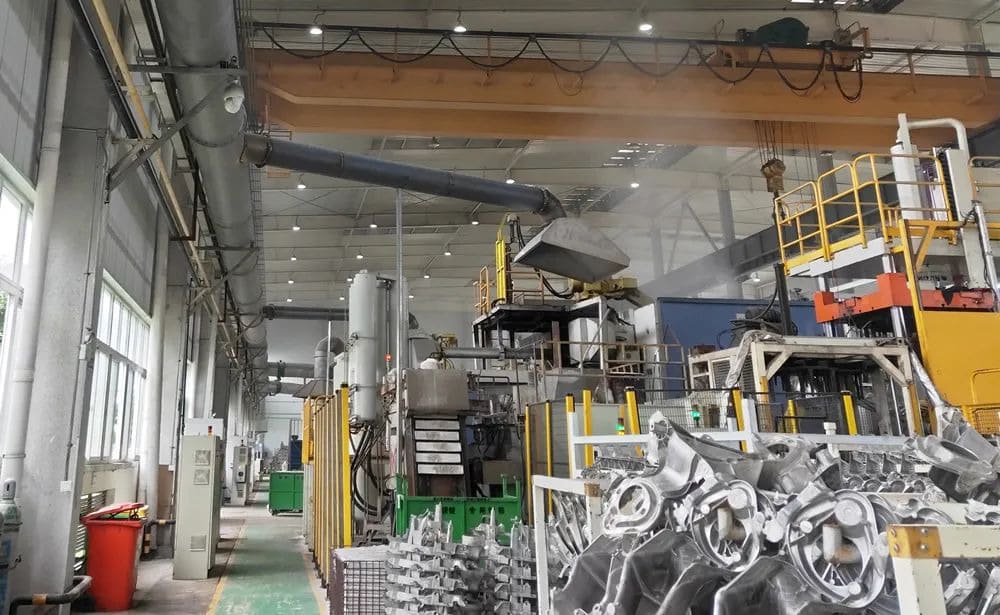
Process of Hot Rolling
1. Hot rolling generally refers to rolling performed above the metal recrystallization temperature;
2. During the hot rolling process, the metal has a process of hardening and softening simultaneously. Due to the influence of the deformation speed, as long as the recovery and recrystallization process is too late, there will be a certain amount of work hardening;

3. The metal recrystallization after hot rolling is incomplete. That is, the recrystallization structure and the deformed structure coexist;
4. Hot rolling can improve the processing performance of metals and alloys and reduce or eliminate casting defects.
Casting Process
Casting and rolling process: liquid metal, front box (liquid level control), casting and rolling mill (lubricating system, cooling water), shearing machine, cooler.
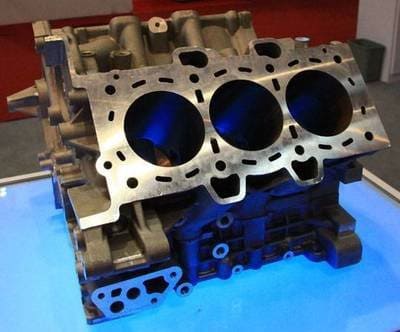
1. The casting and rolling temperature are generally between 680 °C and 700 °C; the lower, the better, the stable casting and rolling line generally stops once a month or more to re-stand the plate. During the production process, it is necessary to strictly control the liquid level of the front box to prevent low liquid level;
2. Lubrication uses C powder with incomplete combustion of gas for lubrication, which is also one of the reasons that the surface of the casting and rolling stock is dirty;
3. The production speed is generally between 1.5m/min-2.5m/min;
4. The surface quality of products produced by casting and rolling is generally relatively low and generally cannot meet the requirements of special physical and chemical properties.
Cold Rolling Process
1. Cold rolling refers to the rolling production method below the recrystallization temperature;
2. There will be no dynamic recrystallization during the rolling process, the temperature will rise to the recovery temperature at most, the cold rolling will appear to work hardening, and the work hardening rate will be large;
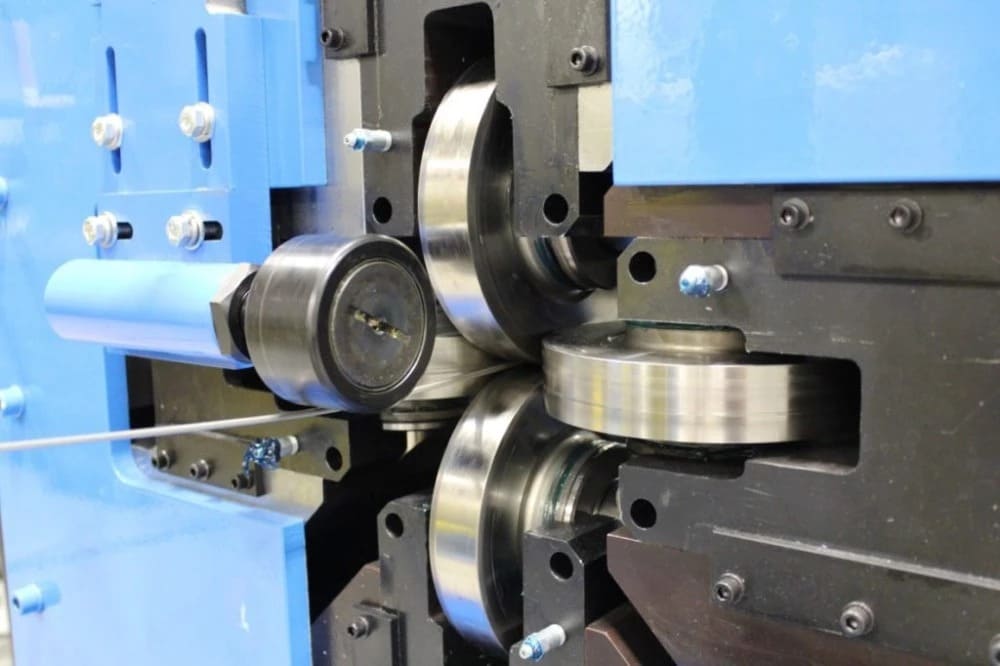
3. The cold-rolled sheet and strip have high dimensional accuracy, good surface quality, uniform structure and performance, and products in various states can be obtained with heat treatment;
4. Cold rolling can roll out thin strips, but it has the disadvantages of large deformation energy consumption and many processing passes.
Additional Precision Processing Methods
1. Finishing is a processing method to make the cold-rolled sheet meet the customer’s requirements or a processing method to facilitate the subsequent processing of the product;
2. The finishing equipment can correct the defects in the production process of hot rolling and cold rolling, such as cracked edges, oil strips, poor shape, residual stress, etc. It needs to ensure that no other defects are introduced in the production process;
3. Various finishing equipment includes cross-cutting, longitudinal shearing, bending and straightening, annealing furnace, slitting machine, etc.
Conclusion
At Chal, all aluminium alloys are made through the above fine processes. We focus on every product provided to our customers and pay much more attention to the satisfaction of our clients than benefits. Please do not hesitate to contact us for your desired products.