Aluminum alloys are widely used in various applications, thanks to their desirable properties such as high strength-to-weight ratio, good corrosion resistance, ease of processing, and low cost. To achieve the desired properties and performance, proper heat treatment of these alloys is essential. In this article, we will explore the different alloying elements used in the formation of aluminum alloys and classify them based on the types of aluminum alloys. Additionally, we will discuss the significance of heat treatment in enhancing the strength and hardness of aluminum alloys.
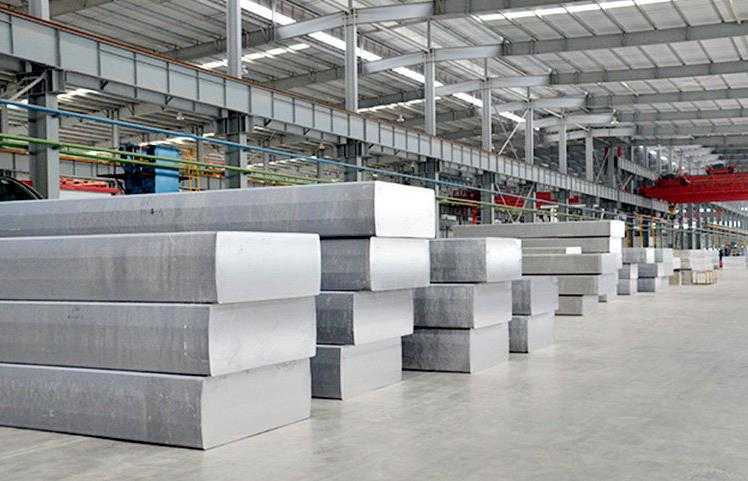
Alloy Elements and Classification
Aluminum alloys used for casting and forging are typically categorized as heat-treatable (precipitation hardenable) or non-heat-treatable aluminum alloys. Heat-treatable aluminum alloys undergo solid solution strengthening, quenching, and subsequent aging to increase their strength and hardness. Non-heat-treatable aluminum alloys, on the other hand, primarily rely on cold working to improve their strength.
The most commonly used elements for strengthening commercial aluminum alloys are copper, magnesium, manganese, silicon, and zinc. Other minor alloying elements, such as iron, lithium, titanium, boron, zirconium, chromium, vanadium, scandium, nickel, tin, and bismuth, are added for specific properties or metallurgical effects. Silicon, which forms a eutectic reaction, is particularly added to improve the flowability during the casting process, making it a common alloy component in casting alloys.
Primary aluminum alloying elements that form secondary phases with lower solubility include iron, nickel, titanium, manganese, and chromium, either individually or in combinations. Manganese and chromium are part of the primary elements forming secondary phases.
Copper is one of the most important alloying elements in aluminum as it exhibits significant solubility and precipitation-hardening effects. The binary aluminum-copper system is a classic example of precipitation hardening, and it has been extensively studied for age hardening in aluminum-copper alloys.
Most commercial Al-Cu alloys contain other alloying elements. Aluminum-copper alloys with copper content ranging from 2% to 10% form an important alloy family. The aluminum-copper system serves as the basis for forging 2xxx series and casting 2xx.x series alloys, and copper is also included in many other heat-treatable alloys along with other alloying elements such as magnesium.
The addition of magnesium to aluminum-copper alloys offers the advantage of increased strength after solid solution treatment and quenching. In casting and forging alloys, even a small amount of magnesium (0.05%) can effectively modify their aging characteristics.
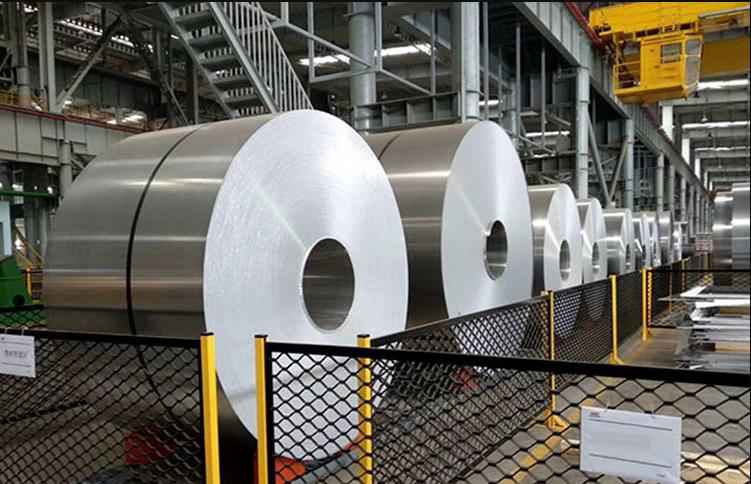
The Al-Mg system forms the basis of the 5xx and 5xx.x casting non-heat-treatable aluminum alloys. The addition of magnesium provides solid solution strengthening without compromising ductility. Al-Mg alloys offer an excellent combination of solid solution strengthening, corrosion resistance, and the ability to be further strengthened through cold working in forging alloys.
Silicon is a common impurity found in commercial aluminum alloys. The silicon impurity content in industrial electrolytic aluminum ranges from 0.01% to 0.15% by weight, and the presence of iron significantly reduces the solubility of silicon in aluminum.
When added as an alloying element, silicon exhibits the notable effect of improving the castability of aluminum and its alloys. Aluminum-silicon alloys without copper can be used when both good castability and excellent corrosion resistance are required.
Aluminum-copper-silicon alloys are the most widely used casting aluminum alloys. The dominant component varies significantly between alloys, with some alloys being copper-dominant and others silicon-dominant. Copper contributes to strength, while silicon improves castability and reduces hot cracking. Aluminum-copper-silicon alloys are commonly used in various industries, including automotive, aerospace, and consumer electronics, where a balance between strength, castability, and corrosion resistance is required.

Significance of Aluminum Heat Treatment
Heat treatment plays a crucial role in enhancing the mechanical properties of aluminum alloys. By subjecting the alloy to controlled heating and cooling processes, the microstructure of the material can be modified, leading to improved strength, hardness, and other desirable characteristics.
The heat treatment of aluminum alloys typically involves three main steps: solution heat treatment, quenching, and aging. During the solution heat treatment, the alloy is heated to a temperature where the alloying elements dissolve into the aluminum matrix, forming a solid solution. This process helps in the homogenization of the alloy composition and reduces the segregation of alloying elements.
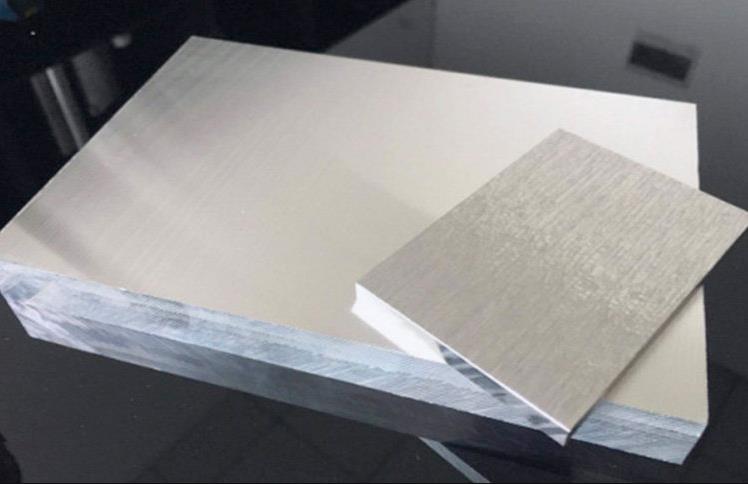
After the solution heat treatment, the alloy is rapidly quenched by immersing it in a cooling medium such as water or oil. Quenching results in the formation of a supersaturated solid solution, where the alloying elements are retained in a metastable state. This rapid cooling prevents the formation of equilibrium phases, leading to a high-strength, but relatively soft material.
The final step in the heat treatment process is aging, which involves heating the quenched alloy to a lower temperature for a specific duration. During aging, the supersaturated alloy undergoes a precipitation process, where fine particles of the alloying elements precipitate out and form secondary phases within the aluminum matrix. These precipitates act as obstacles to dislocation movement, resulting in increased strength and hardness of the material.
The choice of aging temperature and duration depends on the specific alloy composition and desired mechanical properties. Different aluminum alloys require different aging treatments to achieve optimal strength and hardness. For instance, 2xxx series alloys (aluminum copper) are typically aged at relatively low temperatures, while 7xxx series alloys (aluminum-zinc) are aged at higher temperatures.
It’s worth noting that the heat treatment process can also affect other properties of aluminum alloys, such as corrosion resistance and formability. Improper heat treatment parameters or deviations from the recommended procedures can lead to undesirable effects, such as over-aging, under-aging, or the formation of undesirable phases.
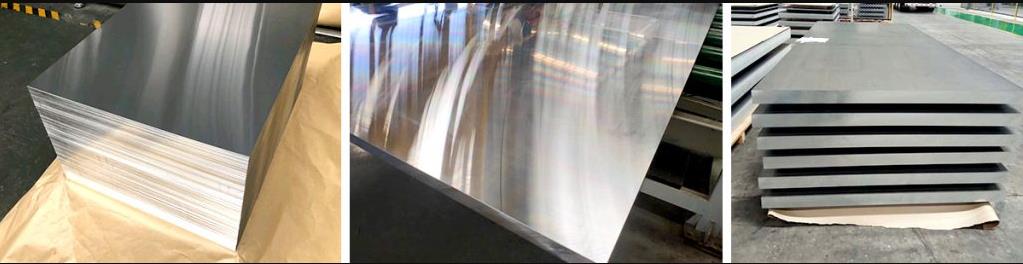
Conclusion
Aluminum alloys are widely used in various industries due to their favorable properties, and heat treatment is a critical process to enhance their mechanical properties. The addition of alloying elements and the careful control of heating, cooling, and aging processes allow for the optimization of strength, hardness, and other desired characteristics.
Understanding the alloying elements and their effects on the microstructure of aluminum alloys is essential for selecting the appropriate heat treatment process. Proper heat treatment not only improves the strength and hardness but also influences other properties such as corrosion resistance and formability, making it a key factor in the successful application of aluminum alloys in different industries.
By utilizing the knowledge and techniques of aluminum heat treatment, engineers and manufacturers can produce aluminum components and products with superior performance, durability, and reliability. Continuous research and development in this field will further advance our understanding of aluminum heat treatment and contribute to the development of innovative aluminum alloys for future applications.