The plastic deformation of the aluminum alloy at room temperature and moderate stress is mainly caused by dislocation slip. In contrast, plastic deformation at high temperatures and low stress is caused by dislocation creep and diffusion flow. In general, regardless of the working temperature, the deformation resistance of the alloy is mainly determined by the ease of dislocation movement. Therefore, aluminum alloy’s resistance to dislocation movement is called aluminum alloy strengthening.
There are many strengthening and classification methods for aluminum alloys, which are generally divided into two categories: work hardening and alloying strengthening. The strengthening methods of aluminum alloys can be subdivided into seven categories: work hardening, solid solution strengthening, heterogeneous strengthening, dispersion strengthening, precipitation strengthening, grain boundary strengthening, and composite strengthening. In practical application, several reinforcement methods often work at the same time.
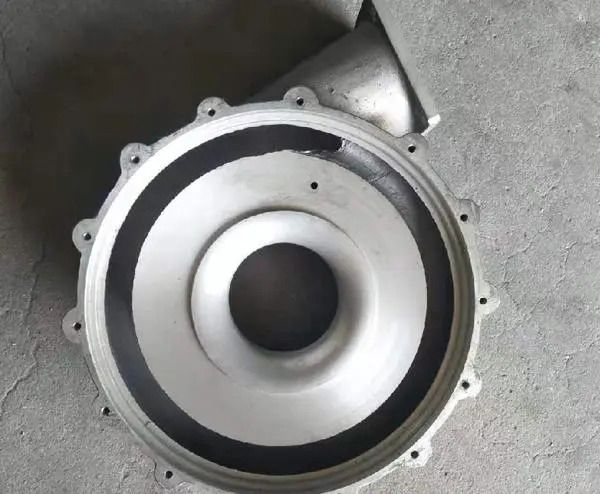
Processing and strengthening of aluminum alloys
The method of obtaining high strength in an alloy by plastic deformation (rolling, extrusion, forging, drawing, etc.) is called work hardening. The increase of dislocation density during plastic deformation is the essence of alloy work hardening. According to statistics, after the metal is strongly deformed, the dislocation density can increase from 106 pieces/cm2 to more than 1012 pieces/cm2. Because the greater the dislocation density in the alloy, the more opportunities for the dislocations to transfer to each other in the slip process when the deformation continues, and the greater the mutual resistance, and thus the greater the deformation resistance, the alloy is strengthened.
The reason for the processing and strengthening of metal materials is that the dislocations are unevenly distributed when the metal is deformed. First, they are entangled in groups in a chaotic manner, forming dislocation entanglements. It is transformed into a cellular substructure, and the deformed grain is composed of many small units called “cells”; high-density dislocation entanglements are concentrated around the cells to form envelopes, and the dislocation density inside the cells is very low. These cellular structures impede the movement of dislocations so that the number of dislocations that cannot move increases so much that more force is required to move the dislocations over the obstacles. The greater the deformation, the smaller the substructure, the greater the ability to resist continuous deformation, the more obvious the work hardening effect, and the higher the strength. The generation of substructures is also called substructure strengthening.
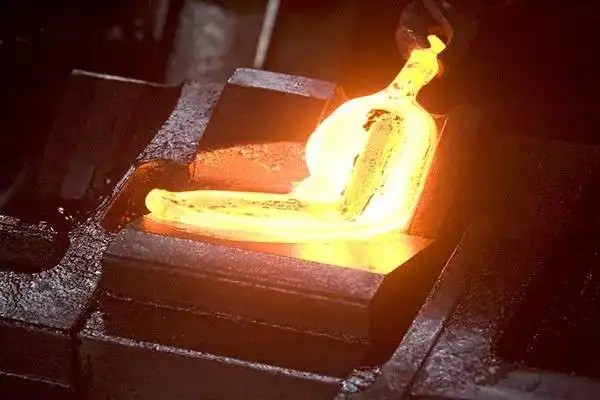
The degree of work strengthening varies with the deformation rate, deformation temperature, and the properties of the alloy itself. When the same alloy material is cold deformed at the same temperature, the greater the deformation rate, the higher the strength, but the plasticity decreases with the increase of the deformation rate. The deformation conditions of the alloy are different, and the dislocation distribution is also different.
When the deformation temperature is low (such as cold rolling), the dislocation activity is poor, and the dislocations are mostly disordered and irregularly distributed after deformation, forming dislocation entanglement. At this time, the alloy has a good strengthening effect, but the plasticity is also strongly reduced. When the deformation temperature is high, the dislocation activity is large, and cross-slip occurs, dislocations can locally aggregate, entangle, form dislocation clusters, and substructure and strengthen. At that time, the strengthening effect is not as good as cold deformation, but the plasticity was lossless.
Work hardening or substructural strengthening is a very effective strengthening method at room temperature, suitable for industrial pure aluminum, solid solution alloys, and multiphase aluminum alloys that cannot be strengthened by heat treatment, but usually contribute to strength due to recovery and recrystallization at high temperatures significantly smaller.
When some aluminum alloys are cold-deformed, they can form a better texture and strengthen in a certain direction, which is called texture strengthening.
Solid solution strengthening of aluminum alloys
When the alloy elements are dissolved in the base metal (solvent) to form a solid solution, the strength and hardness of the alloy are generally improved, which is called solid solution strengthening. All soluble alloying components and even impurities can produce solid solution strengthening. What is particularly valuable is that when the alloy is a solid solution strengthened, the strength and hardness are improved while the plasticity can be maintained at a good level, but this method alone cannot obtain particularly high strength.
After the alloying elements dissolve into the base metal, the dislocation density of the base metal increases, and the lattice is distorted at the same time. The stress field generated by the distortion interacts with the elastic stress field around the dislocation, causing the atoms of the alloying elements to gather near the dislocation line to form a so-called “air mass”.
For dislocations to move, they must overcome the pinning effect of the air mass, move with the air mass, or break free from the air mass, thus requiring greater shear stress. In addition, the atoms of alloying elements can also change the elastic coefficient, diffusion coefficient, cohesion, and atomic arrangement defects of the solid solution, so that the dislocation line becomes bent and the resistance of dislocation movement increases, including the long-range interaction between dislocation and solute atoms and short-range interactions, thereby strengthening the material.
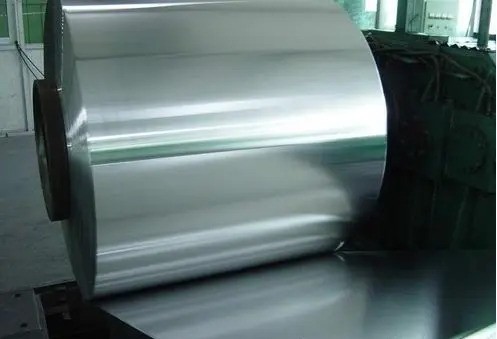
The magnitude of solid solution strengthening depends on the concentration of solute atoms, the relative size of atoms, the type of solid solution, electronic factors and elastic modulus. Generally speaking, the higher the concentration of solute atoms, the greater the strengthening effect; the greater the difference in atomic size, the greater the strengthening effect on the replacement solid solution; the greater the difference in the number of valence electrons between solute atoms and aluminum atoms, the greater the solid solution strengthening effect. The bigger the difference, the better the strengthening effect is.
When using solid solution strengthening alloying, those elements with a high strengthening effect should be selected as alloying elements. But it is more important to select those elements with high solid solubility in the base metal as alloying elements, because the strengthening effect of the solid solution increases with the increase of the content of solid solution elements. Only those elements with high solid solubility in the base metal can be added in large quantities. For example, copper and magnesium are the main alloying elements of aluminum alloys; aluminum and zinc are the main alloying elements of magnesium alloys, all because of the high solid solubility of these elements in the base metal.
When solid solution strengthening is carried out, the principle of complex alloying with multiple elements and small amounts is often used (that is, multiple alloying elements are added at the same time, but each element is added in a small amount) to complicate the composition of the solid solution, which can make the strengthening effect of the solid solution higher. And can be maintained at a higher temperature.
Aluminum alloy precipitation strengthening
The process of precipitation of a stable second phase from a supersaturated solid solution to form a transition phase in a metastable region enriched by solute atoms is called precipitation.
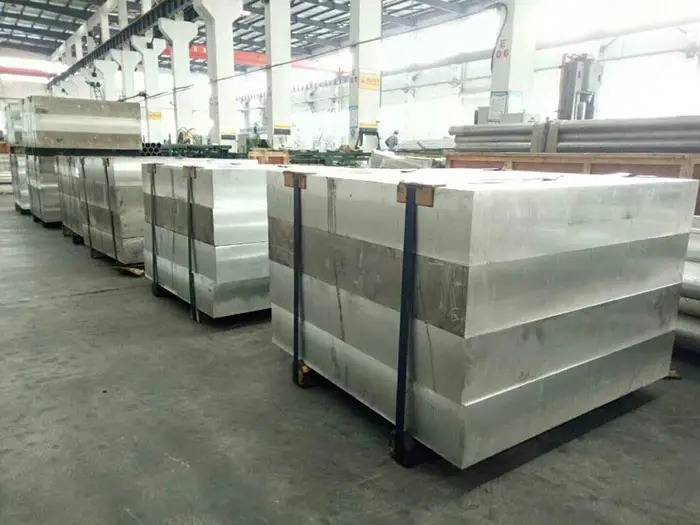
Any alloy with a change in solid solubility will precipitate when it enters the two-phase region from the single-phase region. The supersaturated solid solution is obtained during the solution treatment of the aluminum alloy, and then heated at a certain temperature, precipitation occurs to form a coherent metastable phase particle, this process is called aging.
The strengthening caused by precipitation or aging is called precipitation strengthening or aging strengthening. The precipitation process of the second phase is also called precipitation, and its strengthening is called precipitation strengthening. The particles precipitated by aluminum alloy aging are generally G.P region, coherent or semi-coherent transition phase, and the size is 0.001~0.1μm, which belongs to the third type of particles.
These soft points have three strengthening effects, namely strain strengthening, dispersion strengthening, and chemical strengthening. The aging-strengthened particles are evenly distributed in the matrix so that the deformation tends to be uniform, so the plasticity loss caused by aging-strengthening is smaller than that of work-hardening, dispersion-strengthening, and hetero-phase strengthening.
Through precipitation strengthening, the strength of the alloy can be increased by tens to hundreds of times. Therefore, precipitation strengthening is an effective strengthening method commonly used for non-ferrous metal materials such as Ag, Mg, Al, and Cu.
The effect of precipitation strengthening depends on the composition of the alloy, the supersaturation of the solid solution after quenching, the characteristics, distribution, and dispersion of the strengthening phase, and the heat treatment system. The alloy with the best strengthening effect is located in the limiting solubility composition, where the maximum volume fraction of the precipitated phase can be obtained.