Aluminum and its alloys have become indispensable materials in modern industry due to their unique combination of properties, including lightweightness, corrosion resistance, and good formability. Within the realm of aluminum-processed materials, deep drawing aluminum strips hold a significant position. These strips, specifically designed for intricate forming operations, play a crucial role in enhancing production efficiency and ensuring the quality of a wide array of industrial and consumer products. This article aims to provide a comprehensive overview of deep drawing aluminum strips, encompassing their industrial standing, material composition, manufacturing processes, and diverse applications.
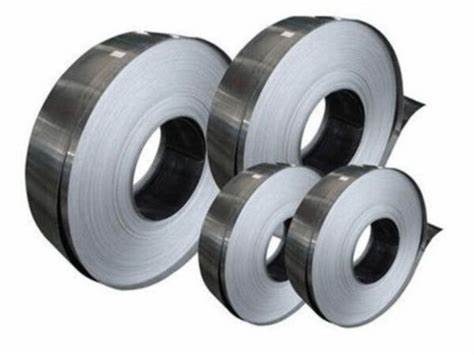
The Industrial Significance and Role of Deep Drawing Aluminum Strips
Aluminum processed materials encompass a broad spectrum of forms, including sheets, strips, foils, and extrusions, each tailored for specific applications. Deep drawing aluminum strips stand out due to their optimized properties for severe plastic deformation without fracturing. Their inherent advantages, such as a high strength-to-weight ratio and excellent corrosion resistance, make them a preferred choice over other materials in numerous sectors.
The Importance of Deep Drawing Performance
Deep drawing is a metal forming process where a sheet metal blank is radially drawn into a forming die by the mechanical action of a punch. This process is essential for creating cup-shaped, box-shaped, or other complex geometric parts. Superior deep drawing performance is critical for achieving intricate designs, minimizing material waste due to tearing or wrinkling, increasing production speeds, and ultimately reducing manufacturing costs. The ability of an aluminum strip to undergo significant plastic deformation without failure is a key determinant of its suitability for deep drawing applications.
The Role of Deep Drawing Aluminum Strips in Industrial Production
Deep drawing aluminum strips serve as a fundamental raw material in the manufacturing of complex-shaped components across various industries. Their application spans from automotive body panels and household appliance casings to packaging containers and electronic device housings. By enabling the production of lightweight yet robust parts, they contribute significantly to fuel efficiency in vehicles and energy savings in appliances. Furthermore, the use of aluminum promotes sustainability due to its recyclability. The precise formability offered by deep drawing aluminum strips also leads to improved product performance and enhanced reliability.
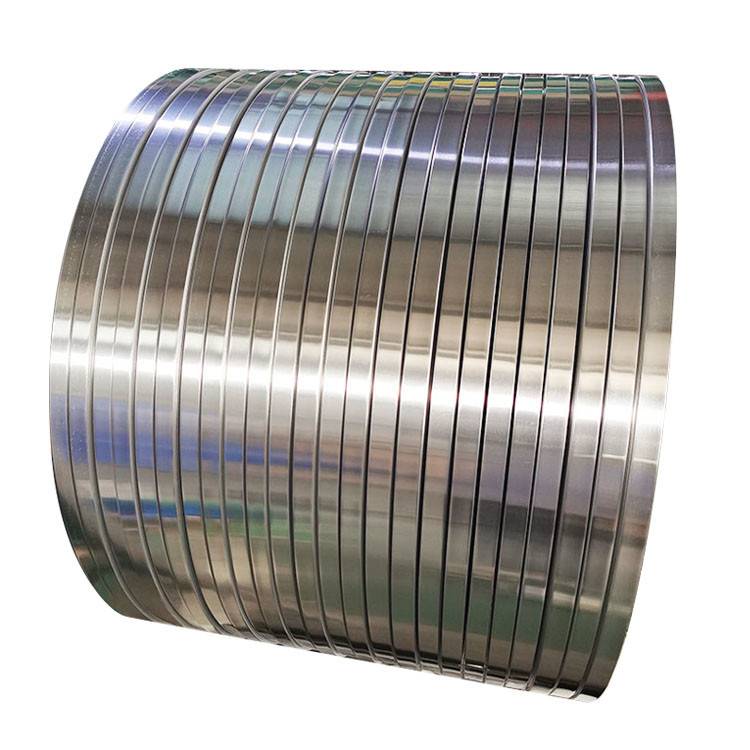
Material and Composition of Deep Drawing Aluminum Strips
1. Common Alloy Series for Deep Drawing Aluminum Strips
The selection of the appropriate aluminum alloy is paramount for achieving optimal deep drawing performance. Several aluminum alloy series are commonly employed, each with distinct characteristics:
1xxx Series (Pure Aluminum): Characterized by high purity, excellent ductility, and corrosion resistance, but lower strength. While not ideal for high-strength deep-drawn parts, they are used in applications requiring exceptional formability and corrosion resistance, such as certain packaging materials and heat exchangers.
3xxx Series (Aluminum-Manganese Alloys): These alloys offer a good balance of formability, moderate strength, and corrosion resistance. Manganese addition enhances strength without significantly compromising ductility, making them suitable for a wider range of deep drawing applications, including beverage cans and some automotive interior parts.
5xxx Series (Aluminum-Magnesium Alloys): Known for their higher strength, good weldability, and excellent corrosion resistance, while still exhibiting good formability. Magnesium is a key strengthening element. These alloys are widely used in automotive exterior panels, appliance housings, and structural components requiring both strength and good deep drawing characteristics.
Other Potential Alloy Series: Certain alloys from the 6xxx series (Aluminum-Magnesium-Silicon) can also be used for deep drawing applications, particularly when combined with appropriate heat treatments to optimize their formability.
2. Influence of Key Alloying Elements on Deep Drawing Performance
The addition of specific alloying elements significantly impacts the deep drawing behavior of aluminum.
Alloying Element | Primary Effect | Influence on Deep Drawing Performance |
Magnesium (Mg) | Increases strength and hardness, improves work hardening. | Can enhance drawability in certain ranges but excessive amounts can reduce ductility. Influences anisotropy. |
Manganese (Mn) | Increases strength and corrosion resistance, refines grain size. | Improves formability by promoting more uniform deformation and reducing grain boundary sliding. |
Copper (Cu) | Increases strength. | Generally reduces ductility and corrosion resistance, limiting its use in critical deep drawing alloys. |
Silicon (Si) | Improves fluidity during casting. | Indirectly affects deep drawing by influencing the initial microstructure of the cast ingot. |
Iron (Fe), Silicon (Si) (as impurities) | Decrease ductility and formability. | Negatively impact deep drawing performance; their levels are tightly controlled during production. |
Zirconium (Zr), Titanium (Ti) (as micro-additions) | Refine grain size. | Can improve formability and strength by controlling the grain structure. |
3. Balancing Alloy Selection and Deep Drawing Performance
The selection of the optimal aluminum alloy for a specific deep drawing application requires a careful balance between strength, ductility, corrosion resistance, and cost. Applications demanding intricate shapes necessitate alloys with high formability, even if it means compromising slightly on strength. Conversely, structural components might prioritize higher strength while still requiring adequate deep drawing capabilities.
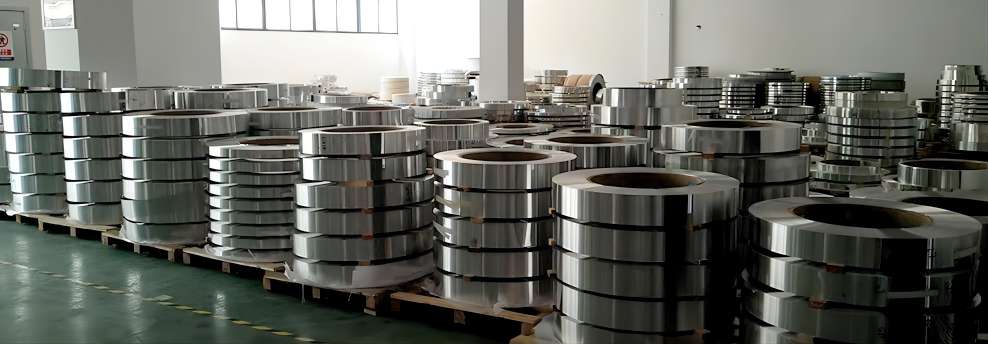
Manufacturing Processes of Deep Drawing Aluminum Strips
1. Melting and Casting Processes
The production of high-quality deep drawing aluminum strips begins with the melting and casting of the chosen alloy. Raw materials are carefully selected and pre-treated to remove impurities. The melting process, carried out in specialized furnaces under controlled temperatures, involves degassing and slag removal to ensure melt purity. Casting methods, such as continuous casting and rolling (CCR) or semi-continuous casting, directly influence the quality of the initial billet or slab. Stringent quality control measures are implemented to ensure chemical homogeneity, uniform microstructure, and a defect-free surface of the cast ingot.
2. Rolling Processes
The cast ingot undergoes a series of rolling operations to achieve the desired thickness and mechanical properties for deep drawing.
- Hot Rolling: The primary objective of hot rolling is to break down the coarse cast structure and improve the material’s plasticity. This process is performed at elevated temperatures, with key parameters including initial and final rolling temperatures, reduction ratios per pass, and rolling speed. The microstructure evolves significantly during hot rolling, leading to grain refinement.
- Cold Rolling: Following hot rolling, cold rolling is performed at room temperature to further reduce the thickness, enhance strength through work hardening, improve surface finish, and achieve precise dimensional tolerances. Total and per-pass reduction rates, rolling speed, and lubrication are critical parameters in cold rolling. The microstructure and mechanical properties are significantly altered during this stage.
- Quality Control During Rolling: Throughout the rolling process, rigorous quality control measures are employed to ensure flatness, uniform thickness, and a defect-free surface. Techniques such as automatic gauge control (AGC) and shape control systems are used to maintain dimensional accuracy and prevent defects.
3. Influence of Heat Treatment on Performance
Heat treatment plays a crucial role in tailoring the microstructure and, consequently, the deep drawing performance of aluminum strips.
- Annealing: Annealing is performed to relieve internal stresses induced during cold rolling, soften the material, and improve ductility. The annealing temperature, holding time, and cooling rate are critical parameters that influence the final microstructure and mechanical properties. Different aluminum alloys require specific annealing cycles.
- Solution Treatment and Age Hardening (for heat-treatable alloys): For certain aluminum alloys, such as some 6xxx series alloys, solution treatment followed by aging (natural or artificial) can significantly increase strength. However, the formability in the peak-aged condition might be reduced. Therefore, a balance needs to be struck based on the specific deep drawing requirements.
- Mechanisms of Heat Treatment’s Influence on Deep Drawing Performance: Heat treatment affects the grain size, texture, and dislocation density of the aluminum, all of which are critical factors influencing deep drawing behavior. For instance, a finer grain size generally improves formability. Controlled heat treatment can also optimize the crystallographic texture, leading to improved earing behavior during deep drawing.
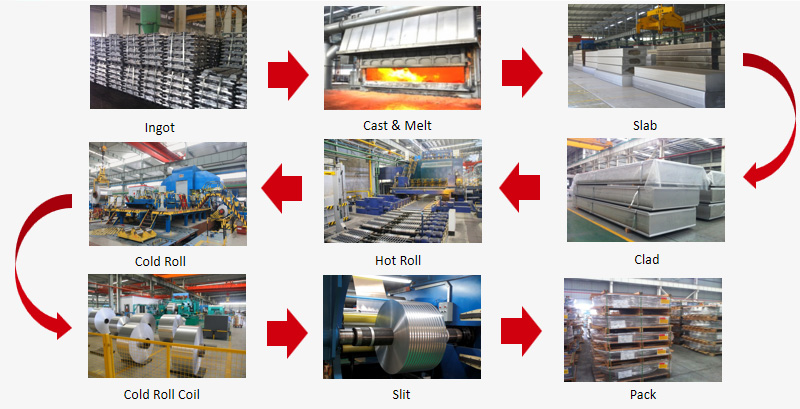
Applications of Deep Drawing Aluminum Strips
Due to their favorable properties, deep drawing aluminum strips are used across various industries. These applications leverage the material’s ability to form into complex shapes without cracking, while also ensuring longevity and aesthetic appeal.
Industry | Applications | Benefits |
Automotive Industry | Fuel tanks and battery housings | Lightweight and corrosion-resistant, High precision and seamless structure integration |
Structural reinforcements and brackets | ||
Decorative trim and interior panels | ||
Home Appliances | Washing machine drums and front panels | Smooth surface finish, Resistance to household chemicals |
Microwave and oven liners | ||
Refrigerator components | ||
Lighting and Electronics | LED housings, reflectors, and casings for electronic devices | Excellent thermal conductivity, Electromagnetic shielding |
Heat sinks and electronic enclosures | ||
Capacitor cans and battery shells | ||
Construction and Architecture | Ceilings, wall claddings, and decorative fixtures | Aesthetic appeal, Reduced structural loads |
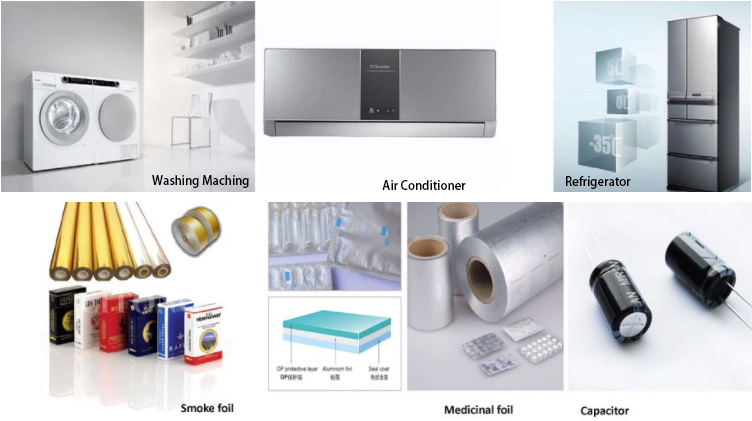
Conclusion and Outlook
Deep drawing aluminum strip continues to evolve with advancements in metallurgy, processing technology, and industrial design requirements. As industries shift toward lighter, more sustainable materials, aluminum strip is gaining prominence as a go-to solution.
Key trends shaping the future include:
- Material Lightweighting: Particularly in transportation sectors, where reducing weight translates to lower energy consumption and emissions.
- Enhanced Alloy Development: Innovations in alloy composition to achieve higher formability and strength without sacrificing ductility.
- Intelligent Manufacturing: Incorporation of AI and sensor technologies in production lines for real-time quality control and process optimization.
- Sustainability Focus: Greater use of recycled aluminum and closed-loop production systems to reduce environmental impact.
With its unique combination of performance, versatility, and recyclability, deep drawing aluminum strip will remain a cornerstone material in precision manufacturing for years to come.