Metal forging is a time-tested manufacturing method that continues to play a central role in modern industrial production. Among the metals used in forging, aluminium stands out for its excellent strength-to-weight ratio, corrosion resistance, and electrical conductivity. These properties make aluminium a material of choice in sectors ranging from automotive and aerospace to electronics and consumer goods.
When it comes to aluminium forging, two major methods dominate the field: cold forging and hot forging. Each uses different temperature ranges and techniques to shape aluminium into durable, high-performance components. This article provides an in-depth comparison between the two processes, examining their mechanics, benefits, limitations, and practical applications to help manufacturers select the ideal method for their specific requirements.
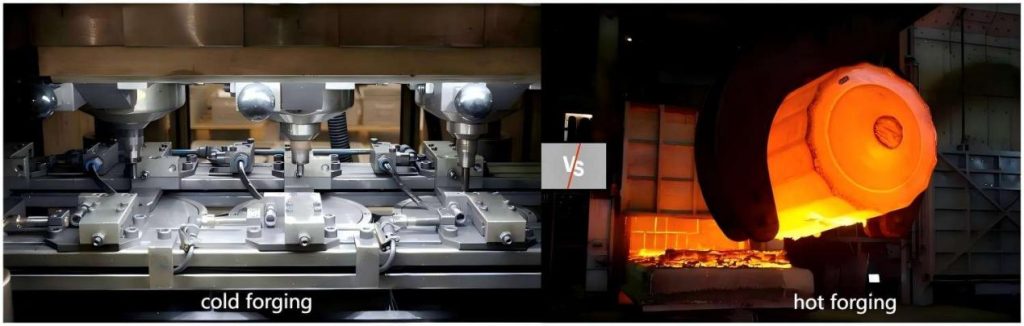
What is Aluminium Cold Forging?
1. Process of Aluminium Cold Forging
Aluminium cold forging is a precision forming process conducted at or near ambient temperature. Unlike hot forging, it leverages the inherent ductility of aluminium to undergo plastic deformation under immense pressure without the need for preheating. The typical steps involved in aluminium cold forging are as follows:
- Material Preparation: Aluminium billets, bars, or wire rods are precisely cut to the required dimensions. Often, a pre-treatment process like annealing is employed to maximize the material’s malleability and ensure uniform deformation.
- Die Placement: The prepared aluminium workpiece is carefully positioned within a meticulously designed die. This die, a custom-engineered tool, contains the negative impression of the final part geometry.
- Applying Pressure: A powerful mechanical or hydraulic press, equipped with a precisely shaped punch, exerts significant compressive force on the aluminium. This pressure compels the metal to flow and conform intimately to the intricate contours of the die cavity.
- Ejection: Once the desired shape has been achieved through plastic deformation, the forged component is mechanically ejected from the die.
- Finishing (Minimal): A key advantage of cold forging is the often minimal requirement for subsequent finishing operations. The process inherently produces parts with excellent dimensional accuracy and a smooth surface finish, reducing or eliminating the need for machining.
2. Advantages of Aluminium Cold Forging
The advantages of aluminium cold forging are substantial and contribute to its suitability for specific applications:
- High Precision and Tight Tolerances: The controlled deformation at lower temperatures allows for the production of components with exceptionally accurate dimensions and tight tolerances, critical for applications demanding precise fit and function.
- Superior Surface Finish: Cold-forged parts typically exhibit a smoother surface finish compared to those produced by hot forging, often negating the need for costly secondary surface treatments and improving wear resistance.
- Improved Mechanical Properties: The cold working process induces strain hardening within the aluminium, leading to an increase in its strength and hardness. Furthermore, the controlled metal flow within the die can orient the grain structure to enhance strength in critical load-bearing directions.
- Material Savings: Cold forging is an efficient process that generates minimal material waste compared to subtractive manufacturing methods like machining, leading to significant cost savings, especially in high-volume production.
- High Production Rates: The relatively rapid cycle times associated with cold forging make it well-suited for mass production, allowing for the efficient manufacture of large quantities of parts.
- No Heating Required: Eliminating the heating stage results in significant energy savings and eliminates the risk of oxidation or scaling on the workpiece, a common issue in hot forging.
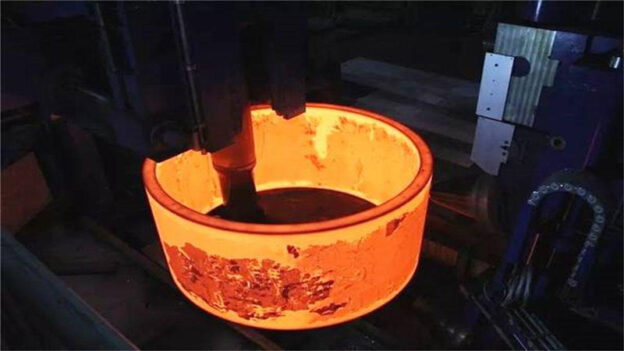
3. Limitations of Aluminium Cold Forging
However, aluminium cold forging also presents certain limitations:
- Limited Shape Complexity: The lower ductility of aluminium at room temperature restricts the complexity of shapes that can be achieved. Intricate geometries or those requiring extensive material flow may be challenging or impossible to produce effectively.
- High Tooling Costs: The production of the high-precision, high-strength dies required for cold forging involves significant initial investment. This makes the process most economically viable for large production runs where the tooling costs can be amortized over a substantial number of parts.
- Potential for Residual Stress: The intense plastic deformation inherent in cold forging can introduce residual stresses within the component. In critical applications, stress-relieving heat treatments may be necessary to mitigate these internal stresses.
- Material Limitations: While various aluminium alloys are suitable for cold forging, the process is generally limited to ductile materials capable of undergoing significant deformation without fracturing at lower temperatures.
4. Common Applications of Aluminium Cold Forging Parts
Aluminium cold forging finds extensive applications across diverse industries, including:
- Automotive: Manufacturing of gears, shafts, anti-vibration mounts, components for alternators and starter motors, and various parts for motorcycles.
- Aerospace: Production of high-precision fasteners, brackets, structural elements, and certain engine components where tight tolerances and high strength are crucial.
- Electronics: Fabrication of heat sinks for thermal management, electrical connectors, and terminals requiring dimensional accuracy and good conductivity.
- Hardware: Mass production of bolts, screws, rivets, hand tools, components for locks and hinges, leveraging the process’s efficiency and precision.
- Medical: Manufacturing of certain surgical instruments and implant components where material integrity and precise dimensions are paramount.
- Consumer Goods: Production of decorative items and low-pressure-bearing components where surface finish and dimensional accuracy are important.
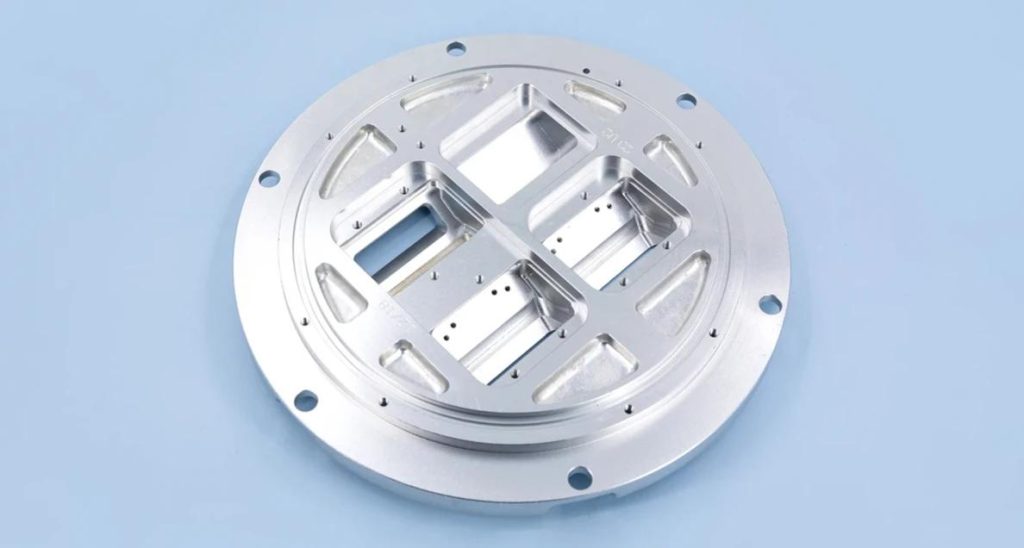
What is Aluminium Hot Forging?
1. Process of Aluminium Hot Forging
Aluminium hot forging involves shaping aluminium alloys at elevated temperatures, typically ranging from 350°C to 500°C (662°F to 932°F), exceeding the material’s recrystallization temperature. This heating process significantly enhances the aluminium’s ductility, reducing its resistance to deformation under applied pressure. The typical steps in aluminium hot forging are as follows:
- Material Preparation: aluminium billets or stock forms are cut to the required size and carefully cleaned to remove any surface contaminants.
- Heating: The prepared aluminium workpiece is heated in a controlled furnace to the pre-determined forging temperature. Precise temperature control is critical to ensure uniform heating and prevent overheating, which can damage the material’s microstructure.
- Die Lubrication: The forging dies are thoroughly lubricated with specialized compounds to prevent the hot aluminium from sticking to the die surfaces and to facilitate smooth metal flow during the forging process. In some cases, the dies themselves are also preheated.
- Forging: The heated aluminium is strategically placed within the forging die, and significant compressive force is applied using powerful hammers or presses. This force compels the softened aluminium to flow and completely fill the intricate contours of the die cavity, achieving the desired shape. Complex parts may require multiple forging steps using different die impressions to progressively achieve the final geometry.
- Ejection: Once the forging operation is complete, the formed component is mechanically ejected from the die.
- Trimming: Excess material, known as flash, which is squeezed out between the die halves during the forging process, is trimmed off using specialized trimming dies.
- Heat Treatment (Often Required): Hot-forged aluminium parts frequently undergo subsequent heat treatment processes, such as solution treating and aging, to optimize their mechanical properties, particularly strength, hardness, and fatigue resistance.
- Finishing (May be Required): Depending on the specific application requirements, further finishing operations may be necessary, including machining to achieve tighter tolerances or improved surface finish, and surface treatments like anodizing or painting to enhance corrosion resistance or aesthetics. Rigorous inspection is also typically performed to ensure quality and dimensional accuracy.
2. Advantages of Aluminium Hot Forging
Aluminium hot forging offers a distinct set of advantages:
- Improved Ductility and Formability: Heating the aluminium significantly reduces its resistance to deformation, allowing for the creation of more complex and intricate shapes that would be impossible to achieve through cold forging.
- Reduced Forging Force: The enhanced malleability at elevated temperatures means that lower forces are required to deform the aluminium, potentially allowing for the use of smaller and less powerful forging equipment for certain applications.
- Enhanced Mechanical Properties: The hot forging process refines the grain structure of the aluminium, leading to improved strength, toughness, and fatigue resistance. It can also effectively eliminate internal defects that may have been present in the initial material.
- Near Net Shape Forming: Hot forging can produce parts with dimensions closer to the final requirements, minimizing the amount of subsequent machining needed, resulting in material savings and reduced manufacturing time.
- No Work Hardening: Unlike cold forging, hot forging avoids significant work hardening, allowing for substantial deformation without the need for intermediate annealing steps to restore ductility.
- Suitability for Larger Parts: Hot forging is generally more suitable for producing larger and more substantial aluminium components that exceed the capacity of cold forging equipment or the material’s cold formability limits.
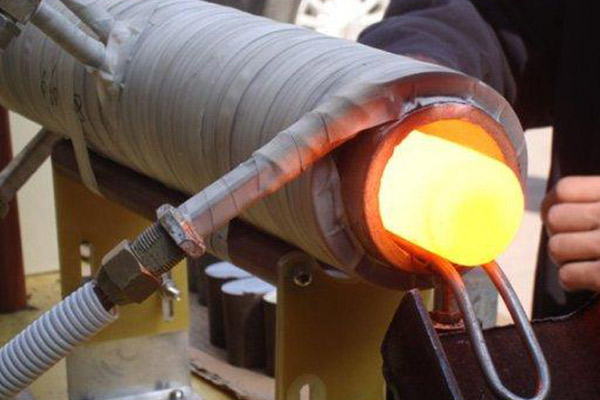
3. Limitations of Aluminium Hot Forging
However, aluminium hot forging also presents certain disadvantages:
- Lower Dimensional Accuracy and Surface Finish (Compared to Cold Forging): The thermal expansion and contraction associated with the heating and cooling cycles can lead to less precise dimensional control compared to cold forging. Additionally, oxidation that occurs at high temperatures often results in a rougher surface finish, typically requiring subsequent machining.
- Higher Energy Consumption: The energy required to heat the aluminium to the necessary forging temperatures significantly increases the overall production costs.
- Tooling Costs: Similar to cold forging, the design and manufacture of the robust dies required for hot forging, especially for complex shapes, can involve substantial initial investment.
- Potential for Warping and Distortion: Uneven cooling of the forged parts can lead to warping or distortion, necessitating careful process control and potentially additional straightening operations.
- Oxidation and Scaling: The high temperatures involved can cause the aluminium surface to oxidize, forming scale that needs to be removed through cleaning processes.
- Shorter Tool Life (Compared to Cold Forging in Some Cases): The combination of high temperatures and significant forging forces can lead to greater wear and tear on the forging dies compared to the conditions encountered in cold forging.
4. Common Applications of Aluminium Hot Forging Parts
Aluminium hot forging is a critical manufacturing process for producing high-strength, lightweight aluminium components across a wide range of demanding industries, including:
- Aerospace: Manufacturing of critical structural components such as wing spars, frames, and ribs, as well as landing gear parts, engine components like turbine blades and discs, and missile bodies.
- Automotive: Production of high-stress suspension parts (control arms, knuckles), steering components, engine parts (pistons, connecting rods), wheels, and chassis components.
- Defense: Fabrication of components for missile systems, armored vehicles, and various weapon systems requiring high strength and durability.
- Transportation: Manufacturing of critical components for ships, trains, and other heavy vehicles, where structural integrity and weight are important considerations.
- Machinery: Production of robust parts for heavy equipment, hydraulic systems, and other industrial machinery.
- Medical: Manufacturing of certain surgical instruments and orthopedic implants requiring high strength and biocompatibility.
- Consumer Goods: Production of high-performance components for sporting equipment, like bicycle frames and durable cookware.
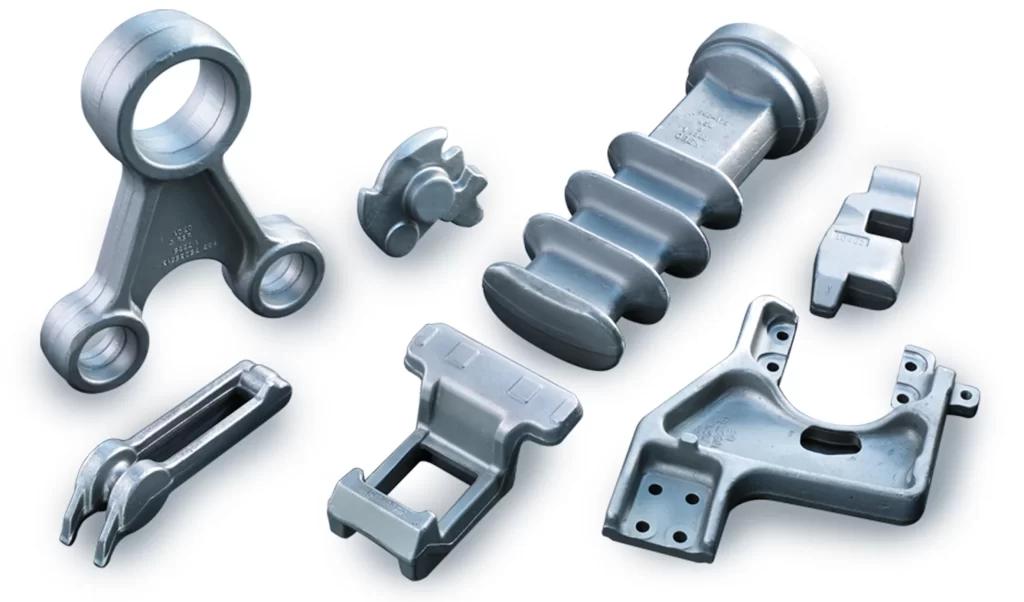
Aluminium Cold Forging vs. Aluminium Hot Forging: Key Differences Summarized
Feature | aluminium Cold Forging | aluminium Hot Forging |
Temperature | Near room temperature | Elevated temperatures (350°C – 500°C) |
Shape Complexity | Generally limited to simpler geometries | Capable of producing more complex and intricate shapes |
Dimensional Accuracy | Typically high, yielding tight tolerances | Generally lower than cold forging due to thermal effects |
Surface Finish | Typically superior, often requiring minimal finishing | Generally rougher, often requiring secondary machining |
Mechanical Properties | Enhanced through strain hardening and grain flow control | Enhanced through grain refinement and controlled cooling |
Material Waste | Minimal due to near-net-shape forming at lower temps | Moderate due to flash formation requiring trimming |
Production Rate | Generally high, suitable for mass production | Moderate to high, depending on part complexity and size |
Energy Consumption | Lower due to the absence of a heating stage | Higher due to the energy required for heating the metal |
Tooling Costs | High initial investment, most economical for large runs | High initial investment |
Part Size Suitability | Best suited for smaller to medium-sized components | More suitable for medium to larger-sized components |
Critical Factors for Aluminium Forging Process Selection
Choosing between aluminium cold and hot forging necessitates a careful evaluation of the specific requirements of the application. Key factors to consider include:
- Part Geometry and Complexity: Intricate designs with significant material flow requirements often necessitate the enhanced formability of hot forging. Simpler geometries may be efficiently produced through cold forging.
- Dimensional Tolerances and Surface Finish Requirements: Applications demanding high precision and smooth surface finishes often favor cold forging. If subsequent machining is acceptable, hot forging can be considered for complex shapes.
- Mechanical Property Requirements: The desired strength, hardness, fatigue resistance, and other mechanical properties will influence the choice, as each process imparts distinct metallurgical characteristics.
- Production Volume: The initial tooling costs for both processes are significant, making them most economical for large production runs. However, cold forging often exhibits higher production rates, making it advantageous for very high volumes of simpler parts.
- Material Grade and Ductility: The specific aluminium alloy being used and its inherent ductility at different temperatures will influence its suitability for either cold or hot forging.
- Budget Constraints: The overall budget, including tooling costs, energy consumption, and secondary processing requirements, must be carefully considered.
- Part Size and Weight: The size and weight of the final component can also dictate the preferred process, as hot forging is generally better suited for larger, more substantial parts.

Conclusion: Selecting the Optimal Path for Forged aluminium Excellence
Both cold and hot forging offer distinct advantages for aluminium part production.
Cold forging provides exceptional precision, surface quality, and material efficiency for simpler shapes produced at scale.
Hot forging offers unmatched formability and mechanical strength for larger or more complex components.
Ultimately, the choice between the two processes depends on the specific requirements of your component, including its geometry, mechanical performance, surface quality, and production scale. By aligning the process with these criteria, manufacturers can achieve optimized performance, cost-efficiency, and quality in their forged aluminium parts.