5083 aluminum alloy has become a widely used material in the aerospace, shipbuilding, and automotive industries due to its excellent corrosion resistance, weldability, and moderate strength. However, its forging process presents some challenges, including temperature control, mold design, and crack prevention. This article delves into the forging characteristics of 5083 aluminum alloy, analyzes the difficulties involved, and proposes corresponding solutions.
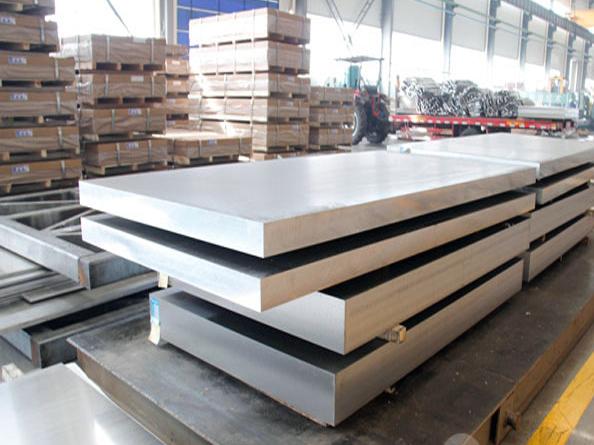
Physical and Chemical Properties of 5083 Aluminum Alloy
The main alloying element of 5083 aluminum alloy is magnesium, with a content of 4.0% to 4.9%. The addition of magnesium significantly improves the corrosion resistance and weldability of aluminum alloys, while also endowing them with certain strength. In addition, 5083 aluminum alloy also contains a small amount of elements such as silicon and manganese, which helps to improve the material’s processing and mechanical properties.
Forging process Challenges for 5083 Aluminum
1. Temperature Control
The forging temperature range of 5083 aluminum alloy is relatively narrow, usually between 450 ℃ and 520 ℃. Excessive or insufficient temperature can affect the fluidity and plasticity of materials, leading to a decrease in the quality of forgings. Therefore, precise control of heating temperature is crucial in the forging process of 5083 aluminum alloy. In practical operation, the temperature should be strictly controlled according to the process regulations, and combined with online monitoring technology, the heating parameters should be adjusted in real time to ensure that the material is in the optimal forging state.
2. Mould Design
Mold design is crucial for the forging process of 5083 aluminum alloy. Due to the poor fluidity of 5083 aluminum alloy, the mold must have sufficient strength and stiffness to withstand the material’s flow pressure, while also ensuring the dimensional accuracy and surface quality of the formed part. In addition, the selection of mold materials and surface treatment are also key factors affecting the performance of forgings. High quality mold materials can improve the service life of molds, while appropriate surface treatment can reduce material adhesion and wear.
3. Crack Prevention
5083 aluminum alloy is prone to cracking during the forging process, especially during the cooling stage. Cracks not only affect the mechanical properties of parts, but also reduce their corrosion resistance. Therefore, how to effectively prevent the formation of cracks is another important challenge in the forging process of 5083 aluminum alloy. In practical operation, the risk of cracking can be reduced by optimizing forging process parameters (such as reducing forging speed, controlling cooling speed) and taking appropriate post-treatment measures (such as stress relief heat treatment).
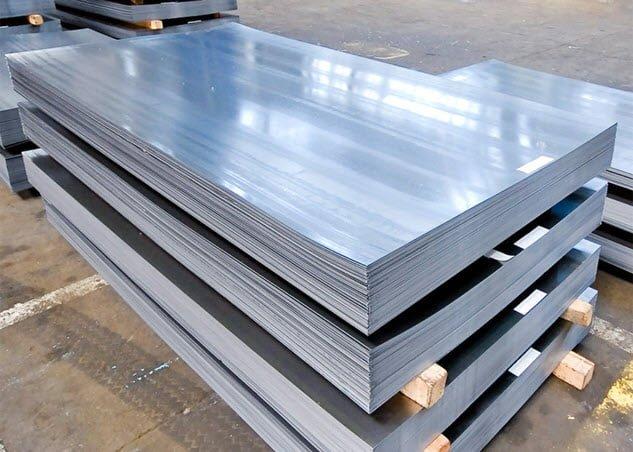
Forging Performance Evaluation for 5083 Aluminum
The evaluation of forging performance of 5083 aluminum alloy is mainly based on its mechanical properties, microstructure, and processing performance. Mechanical properties include tensile strength, yield strength, elongation, etc., reflecting the performance of materials under load. By testing and analyzing these performance indicators, the performance of 5083 aluminum alloy under different forging conditions can be evaluated. Observation of microstructure helps to understand the crystal structure and defect situation of materials, thus evaluating their performance. The machining performance includes cutting force, surface roughness, etc., which affect the performance of the material in subsequent machining processes. By measuring and analyzing these performance indicators, the feasibility of 5083 aluminum alloy in actual processing can be evaluated.
Solutions and Prospects
1. Material Pretreatment
By conducting appropriate pre-treatment of raw materials, such as annealing, their plasticity can be improved and the tendency to crack during the forging process can be reduced. Annealing treatment can eliminate internal stresses and defects in materials, enabling them to achieve a better plastic state, which is beneficial for subsequent forging processing.
2. Process Optimization
By using advanced forging techniques such as isothermal forging, materials can be formed at lower temperatures, thereby reducing the risk of thermal damage and cracking. Isothermal forging is a special forging process carried out at a constant temperature. It can effectively control the deformation behavior of materials and reduce the generation of cracks.
3. Die Materials and Coatings
The use of high-strength and wear-resistant mold materials, as well as the application of special coatings on the mold surface, can improve the service life of the mold and reduce material adhesion. These coatings can reduce friction between materials and molds, reduce adhesion, and improve the corrosion resistance of molds.
4. Post-processing Technology
By controlling the cooling rate and adopting appropriate heat treatment processes, the microstructure of materials can be optimized and their mechanical properties improved. For example, by controlling the cooling rate, different microstructures can be obtained to regulate the performance of the material. In addition, appropriate heat treatment processes can also eliminate the stress generated during forging and improve the toughness of the material.
5. Computer Simulation
Using computer-aided engineering (CAE) software for simulation analysis can optimize forging process parameters, predict material behavior, and guide actual production processes. Through simulation analysis, the deformation behavior and crack formation trend of materials can be predicted before actual production. This can optimize process parameters, reduce the number of experiments, and lower production costs.
6. Continuous Research and Development
With the continuous development of science and technology, new alloy formulas and processing technologies are constantly emerging. Through continuous research and development efforts, new 5083 aluminum alloy materials can be developed to improve their forging performance and meet a wider range of application needs. For example, introducing new alloying elements or adopting innovative grain refinement techniques can potentially improve the malleability and mechanical properties of 5083 aluminum alloy.
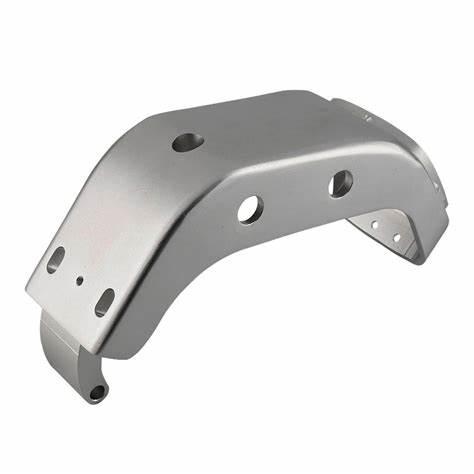
Conclusion
Although there are challenges in forging 5083 aluminum alloy, these difficulties can be effectively solved through scientific and reasonable process selection and technological innovation. Future research can further explore new alloy formulations and processing technologies to improve the forging performance of 5083 aluminum alloy and broaden its application areas. In addition, with the advancement of computer technology and artificial intelligence, intelligent manufacturing will become an important development direction for the future manufacturing industry, providing novel solutions and development opportunities for 5083 aluminum alloy forging.