Aluminum bars are versatile components used in various industries for a wide range of applications. They offer lightweight, corrosion-resistant, and durable solutions for construction, manufacturing, and design needs. Understanding the different types of aluminum bars available is crucial for selecting the right one for specific projects. In this article, we will explore the various types of aluminum bars, their characteristics, applications, and how to choose the right type for your requirements.
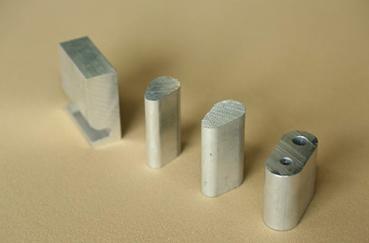
Types of Aluminum Bars
Aluminum bars come in various shapes and sizes, each tailored to specific applications. Let’s delve into the different types:
1. Rectangular Aluminum Bars:
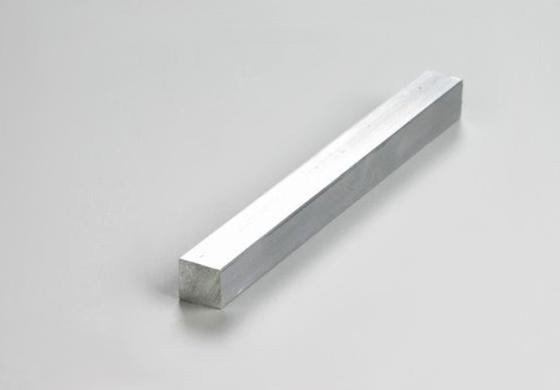
Features: Rectangular aluminum bars are characterized by their elongated shape with straight sides and sharp corners. They are commonly extruded or cold-finished, providing a smooth surface finish. Their rectangular profile offers excellent strength and stability, making them suitable for structural applications.
Applications: These bars are often used in construction, aerospace, automotive components, and machinery where load-bearing capacity and durability are essential. Additionally, their sleek appearance makes them popular in architectural designs.
2. Round Aluminum Bars:
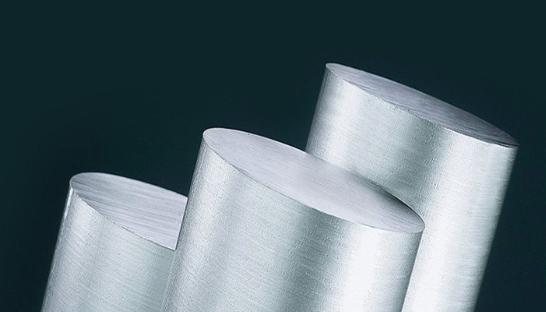
Features: Round aluminum bars feature a cylindrical shape with a smooth, circular cross-section. They are manufactured through hot rolling or extrusion processes, ensuring uniformity and precision. Round bars offer excellent machinability and weldability, making them ideal for various fabrication processes.
Applications: They find extensive use in the manufacturing of shafts, fasteners, handles, and architectural components. Their rounded profile also minimizes stress concentrations, enhancing their fatigue resistance.
3. Square Aluminum Bars:
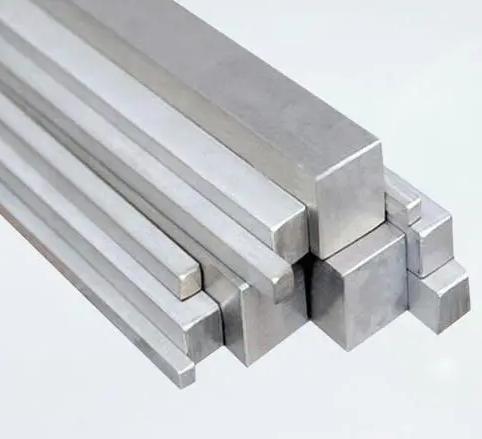
Features: Square aluminum bars boast a square-shaped cross-section with equal sides and sharp edges. They are manufactured through extrusion or cold drawing processes, ensuring dimensional accuracy and surface finish.
Applications: Square bars offer high strength and stiffness, making them suitable for structural frameworks, frames, and support beams. Their geometric symmetry facilitates precise assembly and alignment, especially in modular constructions. Additionally, they are favored in furniture making, decorative elements, and DIY projects due to their aesthetic appeal and ease of handling.
4. Flat Aluminum Bars:
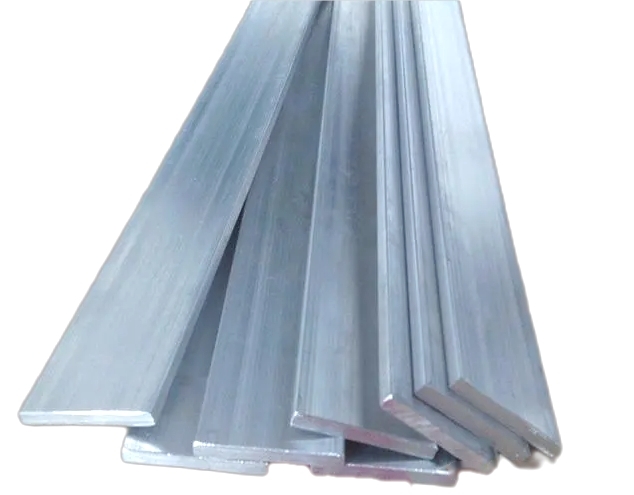
Features: Flat aluminum bars feature a rectangular cross-section with significantly reduced thickness compared to their width. They are typically produced through hot rolling or cold drawing processes, ensuring uniform thickness and smooth surfaces. Flat bars offer excellent versatility, being readily bent, formed, and machined to suit specific requirements.
Applications: They are commonly used in fabrication projects requiring flat surfaces, such as brackets, braces, trim, and base plates. Their low weight and corrosion resistance make them suitable for outdoor applications, including marine environments and architectural cladding.
5. Other Types of Aluminum Bars:
In addition to the more common shapes, there are several specialized types of aluminum bars designed to meet specific needs and applications:
Hexagonal Aluminum Bars:
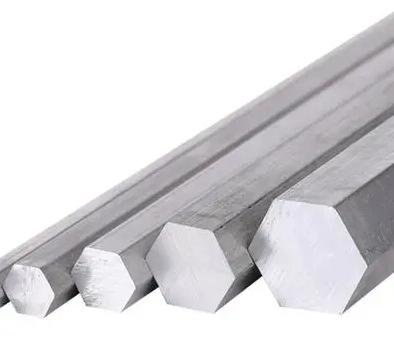
Hexagonal aluminum bars feature a six-sided cross-section, offering unique advantages over traditional round or square bars. Their design provides increased surface area for gripping and torque transmission, making them ideal for use in fasteners, tool handles, and mechanical components requiring precise control.
Hexagonal bars are favored in industries such as aerospace, automotive, and construction for their exceptional strength-to-weight ratio and resistance to deformation under load. Their geometric symmetry ensures uniform stress distribution, enhancing performance in high-stress applications.
T-Bar Aluminum Bars:
T-bar aluminum bars, also known as T-sections, feature a T-shaped profile with a vertical stem and a horizontal flange. These bars are commonly used in structural applications, providing excellent load-bearing capacity and torsional stiffness. The vertical stem serves as a support or attachment point, while the horizontal flange offers increased surface area for connecting components or mounting fixtures.
T-bars are widely employed in building construction, infrastructure projects, and industrial machinery where structural integrity and dimensional stability are paramount. Their versatility allows for easy integration into various designs, facilitating efficient assembly and installation processes.
Angle Aluminum Bars:
Angle aluminum bars, also referred to as angle sections or L-bars, feature an L-shaped profile with two perpendicular legs. These bars are designed to provide structural reinforcement, support, and bracing in diverse applications. The 90-degree angle between the legs offers stability and rigidity, making angle bars ideal for corner reinforcement, framing, edging, and alignment purposes.
They are commonly used in building construction, fabrication projects, and infrastructure development to create robust frameworks, trusses, supports, and protective enclosures. Angle bars can be easily cut, drilled, and welded to suit specific requirements, offering versatility and customization options in structural designs.
Custom Extruded Aluminum Bars:
Custom extruded aluminum bars encompass a wide range of specialized profiles tailored to unique design requirements and applications. These bars are produced through extrusion processes, allowing for the creation of complex cross-sectional shapes with precise dimensions and tolerances.
Custom extrusions offer limitless possibilities in product development and innovation, catering to diverse industries such as aerospace, automotive, electronics, and consumer goods. They can be engineered to incorporate features such as grooves, slots, channels, ribs, and flanges, enhancing functionality and performance in specific applications. Custom extruded bars enable manufacturers to optimize material usage, reduce waste, and achieve cost-effective solutions for their projects, fostering creativity and flexibility in design processes.
In summary, the variety of aluminum bars demonstrates the versatility and adaptability of aluminum as a structural material. Each type offers unique characteristics and benefits, empowering engineers, designers, and manufacturers to create innovative solutions tailored to diverse needs and requirements across industries.
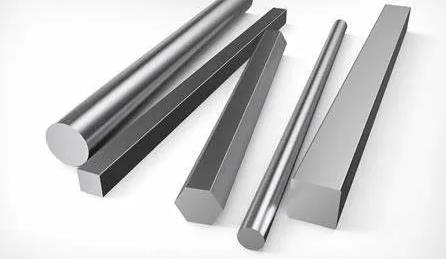
How to Choose the Right Aluminium Bar Types?
Choosing the right type of aluminum bar involves considering several factors to ensure optimal performance and suitability for your specific application. Here are some key considerations to help guide your decision:
- Application Requirements: Identify the primary purpose of the aluminum bar within your project or application. Consider factors such as load-bearing capacity, structural stability, corrosion resistance, and aesthetic appearance.
- Mechanical Properties: Evaluate the mechanical properties required for your application, including tensile strength, yield strength, hardness, and ductility. Different aluminum alloys offer varying levels of these properties, so choose the alloy that best matches your requirements.
- Shape and Size: Determine the most suitable cross-sectional shape and size of the aluminum bar based on your application’s structural and dimensional requirements. Consider factors such as strength-to-weight ratio, ease of fabrication, and compatibility with existing components.
- Environmental Conditions: Consider the operating environment in which the aluminum bar will be used. Assess factors such as exposure to moisture, temperature fluctuations, chemical exposure, and UV radiation. Select an aluminum alloy and surface finish that offer adequate corrosion resistance and durability in the given environment.
- Fabrication Processes: Take into account the fabrication processes involved in shaping and assembling the aluminum bar into its final form. Consider the machinability, weldability, and formability of the chosen alloy to ensure compatibility with your manufacturing techniques and equipment.
- Regulatory Requirements: Ensure compliance with relevant industry standards, codes, and regulations governing the use of aluminum bars in your specific application. Consider any certification or quality requirements that may be necessary to meet regulatory standards and ensure product performance and safety.
- Cost Considerations: Evaluate the cost-effectiveness of different aluminum alloys and bar types based on their initial purchase price, as well as long-term maintenance and replacement costs. Consider factors such as material availability, production volume, and overall project budget.
- Supplier Reliability: Choose a reputable and reliable supplier with a proven track record of delivering high-quality aluminum bars that meet your specifications and deadlines. Consider factors such as lead times, product availability, technical support, and customer service.
By carefully considering these factors, you can make an informed decision when choosing the right type of aluminum bar for your specific application, ensuring optimal performance, durability, and cost-effectiveness.
Here we compare the various types of aluminum bars, highlighting their respective pros and cons, common applications, and typical grades used. Hope they can give you some suggestions.
Type of Aluminum Bar | Pros | Cons | Applications | Common Grades |
Rectangular Aluminum Bar | High strength and stability, Well-suited for load-bearing applications | Limited aesthetic appeal | Structural frameworks Automotive components Machinery parts | 6061, 6063 |
Round Aluminum Bar | Excellent machinability and weldability, Uniform stress distribution | Limited load-bearing capacity | Shafts Fasteners Handles | 6061, 6063, 7075 |
Square Aluminum Bar | High strength and stiffness, Geometric symmetry facilitates assembly | Sharp edges may require additional finishing | Structural frames Support beams Architectural elements | 6061, 6063, 6082 |
Flat Aluminum Bar | Versatile, can be easily bent and formed, Suitable for outdoor applications due to corrosion resistance | Lower load-bearing capacity compared to other shapes | Brackets Trims Base plates | 6061, 6063, 7075 |
Hexagonal Aluminum Bar | Increased surface area for gripping and torque transmission, Uniform stress distribution | Limited availability compared to other shapes | Fasteners Tool handles Mechanical components | 6061, 6063 |
T-Bar Aluminum Bar | Excellent load-bearing capacity, Versatile, suitable for various mounting and attachment applications | Structural frameworks Industrial machinery Building Construction | Structural frameworks Industrial machinery Building construction | 6061, 6063, 6082 |
Angle Aluminum Bar | Provides structural reinforcement and stability, Easy to cut, drill, and weld | Limited applications compared to other shapes | Corner reinforcement Framing Edging | 6061, 6063, 6082 |
Conclusion
In conclusion, understanding the various types of aluminum bars available is crucial for selecting the right material for different applications. Whether you require the strength of rectangular bars, the precision of round bars, the versatility of square bars, or the sleekness of flat bars, there is an aluminum option to meet your needs. When choosing aluminum bars, consider factors such as application requirements, alloy selection, and machining capabilities to ensure optimal performance and durability. For high-quality aluminum bars and expert guidance, trust a reputable aluminum bar supplier to provide reliable products and support for your projects.