Aluminum, with its remarkable properties, has become a cornerstone material across various industries. Among its diverse alloys, 3105 aluminum sheet stands out for its exceptional attributes and wide-ranging applications. This alloy, primarily composed of aluminum and manganese, offers a unique blend of strength, formability, and corrosion resistance, making it indispensable in numerous sectors. In this article, we delve into the composition, manufacturing process, advantages, and applications of 3105 Aluminum sheets.
What is 3105 Aluminum Sheet?
3105 aluminum sheet is a metal alloy composed primarily of aluminum (around 98%) with minor additions, typically manganese (around 1.2%). These additions enhance its strength compared to purer aluminum alloys like 1100 and 3003.
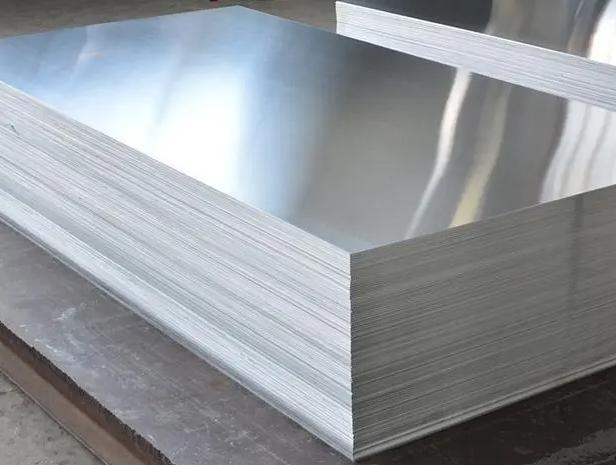
Properties of 3105 Aluminum Sheet:
- High Formability: 3105 aluminum sheet excels in being easily shaped due to its excellent formability. This makes it ideal for applications requiring intricate bends or deep draws.
- Enhanced Strength: Compared to purer aluminum alloys, 3105 offers superior strength thanks to the presence of manganese.
- Weldability: Joining 3105 sheets using welding techniques is straightforward, making it suitable for projects requiring strong and seamless connections.
- Corrosion Resistance: Inherently resistant to corrosion, 3105 aluminum sheet performs well in environments prone to rust or degradation.
- Electrical Conductivity: While not as conductive as copper, 3105 offers a moderate level of electrical conductivity for specific applications.
Overall, the combination of strength, formability, corrosion resistance, and weldability makes 3105 aluminum sheets a versatile material and contributes to its reputation as a reliable and cost-effective solution for diverse engineering and design challenges.
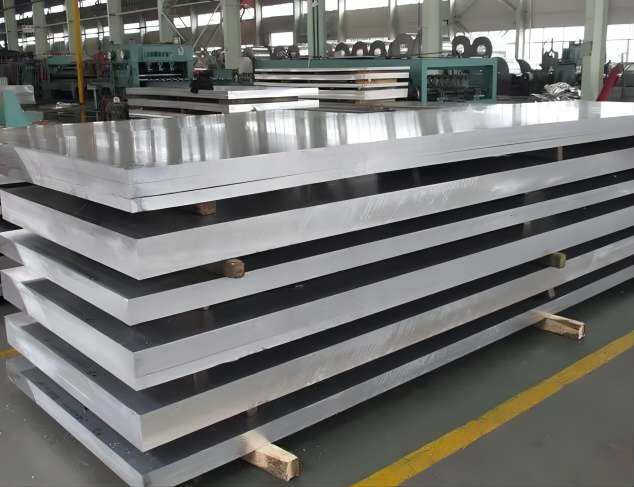
How 3105 Aluminum Sheet is Manufactured?
The manufacturing process of 3105 aluminum sheet involves several stages, including casting, rolling, annealing, and finishing. Here is an overview of the typical manufacturing process:
1. Alloying and Casting
The process begins with the selection and blending of raw materials to achieve the desired chemical composition, including aluminum and alloying elements such as manganese (Mn).
Then the alloy mixture is melted in a furnace at high temperatures.
Once molten, the alloy is cast into ingots or billets of specific sizes using molds. This initial casting stage ensures the alloy’s composition and facilitates subsequent processing.
2. Hot Rolling
The cast ingots or billets are heated to high temperatures to make them malleable.
The heated aluminum is then passed through a series of rolling mills, where it is gradually reduced in thickness and elongated in length through a series of rolling passes.
Hot rolling helps to refine the microstructure of the alloy, improve its mechanical properties, and achieve the desired thickness and dimensions for the final product.
3. Cold Rolling
After hot rolling, the aluminum sheet undergoes cold rolling to further reduce its thickness and improve its surface finish.
Cold rolling involves passing the aluminum sheet through a series of rollers at ambient temperature, gradually reducing its thickness to the desired gauge while maintaining tight dimensional tolerances.
Cold rolling also imparts a smoother surface finish and enhances the sheet’s mechanical properties, including strength and formability.
4. Annealing
Annealing is a crucial step in the manufacturing process of 3105 aluminum sheet. After cold rolling, the sheet may undergo annealing to relieve internal stresses and improve its ductility and formability.
During annealing, the aluminum sheet is heated to a specific temperature and held for a predetermined period before slowly cooling down. This process helps to recrystallize the grain structure and enhance the sheet’s mechanical properties.
5. Finishing and Surface Treatment
Once the aluminum sheet is annealed, it may undergo additional finishing processes to achieve the desired surface texture, flatness, and appearance.
Finishing operations may include trimming, cutting, slitting, and edge conditioning to meet customer specifications. 3105 aluminum sheets typically have smooth and uniform surfaces, which are conducive to surface treatments like brushing, polishing, and painting.
6. Quality Control and Inspection
Throughout the manufacturing process, quality control measures are implemented to ensure the integrity, dimensional accuracy, and mechanical properties of the 3105 aluminum sheet.
Inspection procedures may include visual inspection, dimensional measurements, mechanical testing, and chemical analysis to verify compliance with industry standards and customer requirements.
By adhering to stringent manufacturing practices and quality assurance protocols, producers can consistently produce high-quality 3105 aluminum sheet tailored to the diverse needs of various industries and applications.
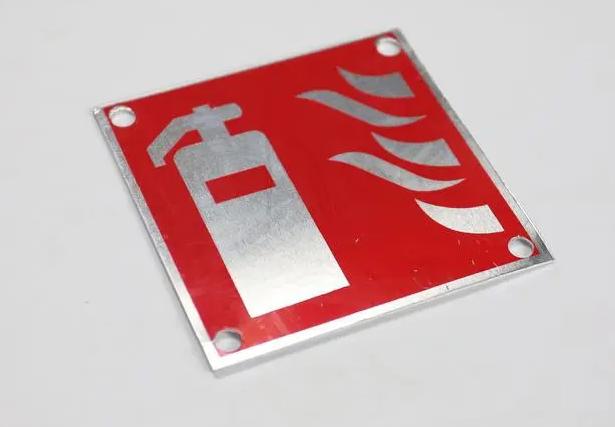
Advantages and Applications of 3105 Aluminum Sheet
The combination of properties offered by 3105 aluminum sheet makes it a popular choice across various industries. Here are some of its key advantages and applications:
1. Superior Formability and Workability
Due to its high purity (around 98% aluminum), 3105 is very easy to shape, bend, and stamp into complex designs without compromising its strength. This makes it ideal for manufacturing products requiring intricate forms, such as:
- Sheet metal work: This could involve fabricating air ducts, enclosures, and other custom metal components.
- Sign making: 3105’s ability to be formed into letters, logos, and other shapes is valuable for creating signs.
2. Excellent Corrosion Resistance
The minimal alloying elements don’t hinder the inherent corrosion resistance of aluminum. This makes 3105 suitable for applications exposed to weather or moisture, such as:
- Residential siding: It can withstand outdoor elements without rusting or degrading quickly.
- Mobile home construction: The corrosion resistance protects the structures from rain and humidity.
- Rain carrying products: Gutters, downspouts, and other elements that channel rainwater can benefit from this property.
3. Good Weldability
3105 aluminum can be joined securely using various welding techniques. This allows for fabrication of complex structures from multiple sheet pieces, beneficial for applications like:
- Building and construction: Cladding, roofing panels, and other architectural elements can be assembled using welds.
- Sheet metal work: Creating complex enclosures or vessels might involve welding multiple pieces of 3105 sheets.
While not a major advantage, it’s worth noting that 3105 also offers good electrical conductivity. This can be a secondary benefit in some applications.
Overall, 3105 aluminum sheet strikes a good balance between affordability, formability, corrosion resistance, and weldability, making it a popular choice for various sheet metal applications and non-critical building components.
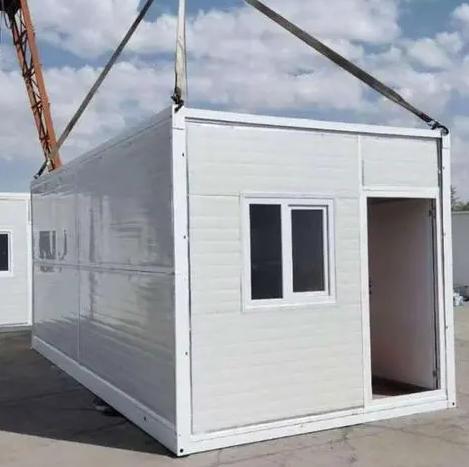
Conclusion
3105 aluminum sheet offers a balance of strength, formability, corrosion resistance, and weldability. This combination makes it a cost-effective and versatile material for a wide range of applications across various industries. By understanding its properties and how it’s manufactured, you can make informed decisions about whether 3105 aluminum sheet is the right choice for your project. If you are looking for a 3105 aluminum sheet supplier, please feel free to contact CHAL..