Modern commercial aluminum comes in many types, called alloys, each offering unique benefits, depending on the alloy chosen. Alloys are reinforced engineering materials made by adding unique elements to base metals. In this paper, the base metal in question is aluminum, while these unique elements can be silicon, copper, zinc, and/or many other metallic elements. These “alloyed” elements can improve the strength, electrical conductivity, resilience or chemical properties of the parent material, making it more versatile as an engineering material. Aluminum is easily alloyed, so the Aluminum Association (AA Inc.) organizes many series of aluminum alloys based on their alloying elements, each with a four-digit name.
5052 Aluminum alloy is the focus of this article, it comes from the 5XXX series aluminum alloy, or aluminum alloy with magnesium as the main alloy element (for a better understanding of aluminum alloy naming, please visit our article on aluminum alloy 6061). This paper will focus on the physical, mechanical and chemical properties of 5052 Aluminum Coil to show that it is an invaluable resource in some important applications.
Physical Properties of 5052 Aluminum
As mentioned earlier, aluminum alloys have specific alloying element percentages to improve material properties; These percentages are important because they can distinguish between different alloys, especially within the same series. Type 5052 Aluminum coil contains 97.25% Al, 2.5%Mg, 0.25%Cr and has a density of 2.68 g/cm3 (0.0968 lb/ In3). In general, 5052 aluminum alloy is stronger than other commonly used alloys such as 3003 aluminum alloy, and because its composition does not contain copper, its corrosion resistance has also been improved.
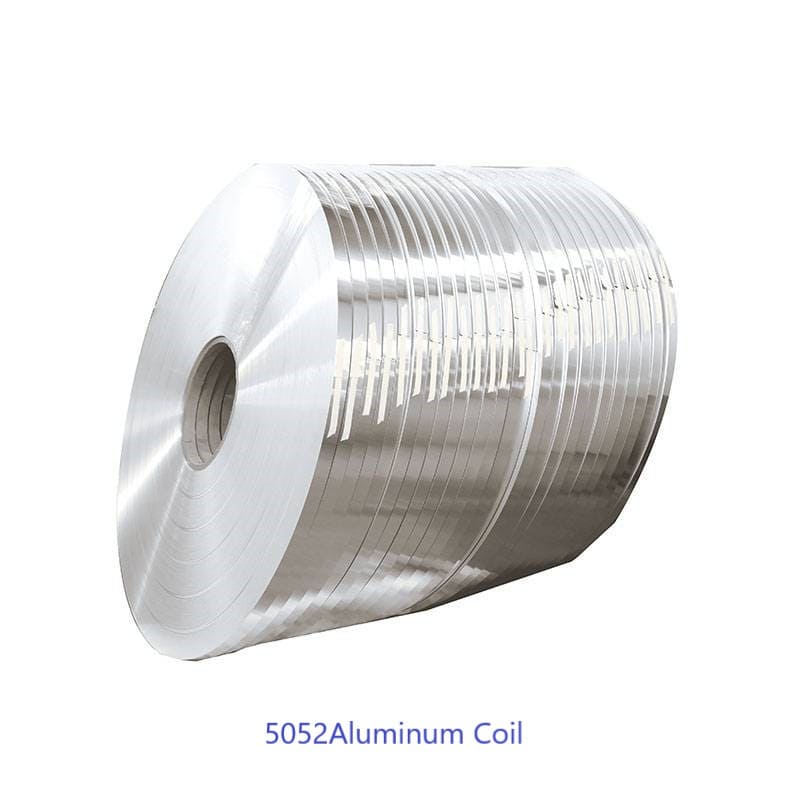
The properties of 5052 Aluminum alloy are different due to its cold working or work hardening process. When processed or permanently altered in shape (e.g. bending, forming, rolling, etc.), a metal (e.g. aluminum) increases in strength but decreases in ductility. This is the result of the molecular structure of the metal, but for the sake of simple explanation, just know that there are mechanical ways to make aluminum alloys stronger. There are several different ways to process quenched 5052 Aluminum alloy, but the strength value of H32 quenched 5052 Aluminum alloy (5052-H32) is used in this paper. Please note that this alloy cannot be strengthened using a heat treatment process, whereas other aluminium alloys such as 7075 or 6061 would benefit from this (more information on heat treatment can be found in these related articles).
Mechanical Properties
There are some important indicators to be aware of in understanding the mechanical properties of engineered materials, which are summarized in Table 1 below.
The first two important values are elastic modulus and shear modulus, which represent the response of the material to axial (pull/push) and shear (torsional/cutting) forces, respectively. The experimental results show that the elastic modulus and shear modulus of 5052 Aluminum coil are 70.3 GPa (10,200 kSi) and 25.9 GPa (3,760 KSi), respectively.
Yield strength and ultimate strength are also central values that need to be known when specifying materials. They represent the maximum forces that cause elastic (non-permanent) and plastic (permanent) deformations. For a more in-depth understanding of these values, please visit our article all about 7075 aluminum alloy. Yield strength is usually the most important value in static applications, where materials can never deform permanently (as in structural applications). However, the ultimate force may be necessary in a particular situation, so it may not hurt to know it. 5052 Aluminum alloy has a yield strength of 193mpa (28,000 psi) and ultimate tensile strength of 228mpa (33,000 psi), which means it is moderately strong compared to some other popular alloys.
Shear strength is the strength of a material when it is “cut” by opposing forces on a plane. 5052 Aluminum alloy is often exposed to this stress because it is usually stamped from a sheet of metal. Essentially, the force of stamping is the opposite of the force of the plate at the working surface, shearing (or cutting) the metal through the vertical plane (or the thinnest size of the sheet metal). For a more intuitive understanding of these values, please visit our article all about 6061 aluminum alloy. 5052 has a shear strength of 138 MPa (20,000 psi), which is also slightly stronger than some other common alloys.
Corrosion Resistance
Aluminum 5052 is particularly useful because it increases resistance to corrosive environments. All aluminum alloys in the presence of air/water form an oxide layer that protects chemically active aluminum from further reaction with the external environment. The amount of corrosion resistance depends on temperature, chemicals in the air, and the working environment near the end; However, 5052 Aluminum coil holds up very well under environmental conditions. Type 5052 Aluminum coil does not contain any copper, which means it is not susceptible to corrosion in a saltwater environment, thus attacking and weakening copper metal composites. Therefore, 5052 Aluminum alloy is the preferred alloy for Marine and chemical applications, while other aluminum will weaken over time. The presence of aluminum in alkaline soils may cause corrosive effects such as pitting, but this is difficult to generalize due to the highly variable composition of the soil.
Due to its high magnesium content, 5052 is particularly resistant to concentrated nitric acid, ammonia and ammonium hydroxide. Any other corrosive effects can be mitigated/removed by using a protective coating, making 5052 aluminum coil very attractive for applications that require inert but tough materials.
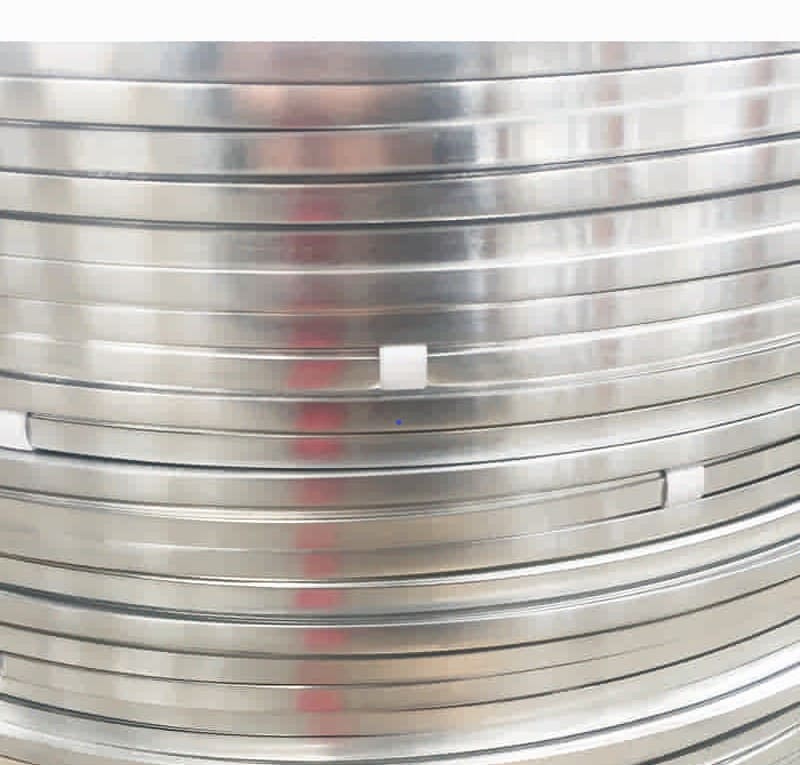
Applications of 5052 Aluminum
5052 aluminum coil is stronger than other commonly used alloys and has higher corrosion resistance. These properties make 5052 aluminum coil an advantage in the Marine industry as well as in electronic and chemical applications. 5052 aluminum coil has a wide range of uses, but some notable applications include:
- Pressure vessels
- Marine equipment
- Electronic enclosures
- Electronic chassis
- Hydraulic tubes
- Medical equipment
- Hardware signs
- To name a few common examples
Summary
Among is a brief summary of the properties, strength, and applications of 5052 aluminum. For information on other products, see our additional guide or visit the Thomas Supplier Discovery platform to locate potential sources of supply or to view details on specific products. We also have guides for other types of aluminium including 6061, 7075 and 3003.