Aluminum High Frequency Welded Tube (HFW Pipe) refers to a type of tubing made from aluminum alloy that is created using the high frequency welding process. It is a specialized manufacturing technique that involves joining aluminum strips or sheets together through the application of high-frequency electrical current and pressure.
Aluminum High Frequency Welded Tubes offer several advantages over other welding techniques. They have a smooth and consistent surface finish, high dimensional accuracy, and excellent mechanical properties. The tubes exhibit good strength and ductility, corrosion resistance, electrical conductivity, and heat transfer efficiency, making them suitable for a wide range of applications such as automotive, HVAC systems, aerospace, aviation, and renewable energy sectors.
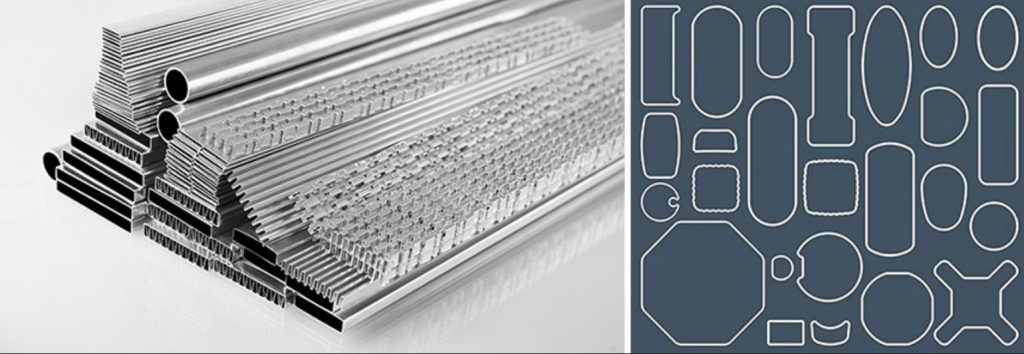
Aluminum High Frequency Welded Tube offers distinct advantages compared to other welding techniques commonly used for aluminum tubing. Let’s compare it with two commonly used methods: TIG welding and MIG welding.
Advantages of TIG Welding (Tungsten Inert Gas Welding):
- Precision and Control: TIG welding provides excellent control and precision, allowing for high-quality welds with minimal distortion. It is often preferred for intricate or critical applications.
- Manual Operation: TIG welding is a manual process, requiring skilled operators to manipulate the torch and filler rod simultaneously. This can increase labor costs and reduce production efficiency.
- Heat Input: TIG welding generates a concentrated heat source, resulting in localized heating. This can lead to a higher risk of distortion and warping, especially in thin-walled aluminum tubing.
- Post-Weld Cleaning: TIG welding produces a weld bead that often requires additional cleaning and smoothing to achieve a desired surface finish.
Advantages of MIG Welding (Metal Inert Gas Welding):
- High-Speed Operation: MIG welding is a semi-automatic or automatic process that offers faster welding speeds compared to TIG welding. It is suitable for high-volume production.
- Welding Efficiency: MIG welding allows for continuous feeding of filler wire, reducing the need for frequent filler rod changes. This increases welding efficiency and productivity.
- Lack of Precision: MIG welding may not provide the same level of precision as TIG welding. The weld bead can be wider and less controlled, resulting in lower aesthetic appeal.
- Shielding Gas Requirement: MIG welding requires a shielding gas to protect the molten weld pool from atmospheric contamination, adding to the cost and complexity of the process.
Advantages of Aluminum High Frequency Welded Tube
- Speed and Efficiency: High frequency welding offers high-speed production, making it suitable for mass production applications.
- Consistency and Precision: The process ensures consistent weld quality, resulting in uniform tube dimensions, smooth surface finish, and tight tolerances.
- Minimal Distortion: The localized heat input of high frequency welding reduces the risk of distortion and warping, particularly in thin-walled aluminum tubing.
- Reduced Post-Weld Processing: The welded tubes often require minimal post-weld cleaning or smoothing, saving time and labor costs.
It’s important to note that the selection of the welding technique depends on the specific application requirements, production volumes, and available resources. Each method has its own strengths and considerations, and the choice should be made based on factors such as weld quality, production speed, precision, and cost-effectiveness.