The automotive industry is constantly evolving, driven by the need for innovation, efficiency, and sustainability. One material that has gained significant traction in recent years is aluminum. Its lightweight nature, coupled with impressive strength properties, makes it an ideal choice for various automotive components. In particular, the application of aluminum high frequency welded tubes (HFW pipes) has revolutionized the industry, offering a multitude of advantages over traditional materials.

Properties and Advantages of Aluminum High Frequency Welded Tube
Aluminum high frequency welded tube possesses several key properties that make it highly suitable for automotive applications. First and foremost is its lightweight characteristic, which helps reduce the overall weight of vehicles. This, in turn, improves fuel efficiency and reduces emissions, aligning with the industry’s shift toward sustainability. Additionally, aluminum exhibits a high strength-to-weight ratio, making it capable of withstanding rigorous demands while maintaining structural integrity.
Furthermore, aluminum boasts exceptional corrosion resistance, ensuring the longevity and durability of automotive components. This resistance to rust and degradation is vital in harsh environments, such as those encountered in exhaust systems and undercarriage components. Moreover, aluminum high frequency welded tube possesses excellent heat dissipation properties, making it ideal for applications where temperature management is crucial, such as radiators and cooling systems.
Another advantage of high frequency welding aluminum tubes is their superior formability and flexibility. This allows manufacturers to create intricate designs and shapes, enabling innovative solutions for automotive structures. Moreover, the energy efficiency of aluminum contributes to overall vehicle performance by reducing power consumption.
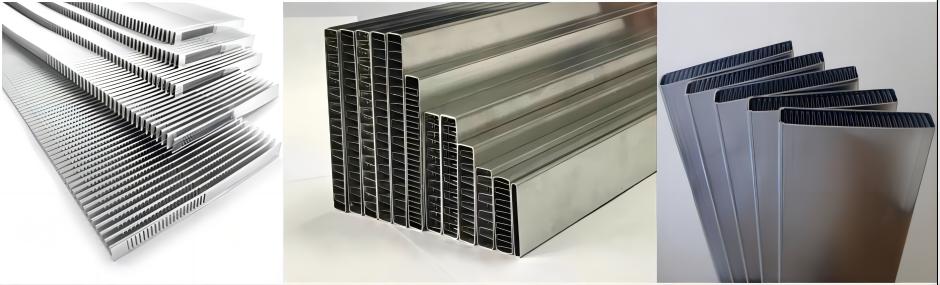
Applications of Aluminum High Frequency Welded Tube in the Automotive Industry
The automotive industry has embraced high frequency welding of aluminum pipe across various applications. One notable area is radiators and cooling systems, where aluminum’s efficient heat transfer and dissipation properties play a vital role. By utilizing aluminum high frequency welded tubes, manufacturers can achieve lightweight designs, resulting in improved fuel efficiency and reduced energy consumption.
Additionally, aluminum finds its place in exhaust systems, where its corrosion resistance ensures a prolonged lifespan even in extreme conditions. The high thermal conductivity of aluminum high frequency welded tube further enhances the performance of exhaust systems, contributing to efficient emission control and optimized engine performance.
High frequency welding aluminum tube is also extensively used in structural components such as chassis and body frame reinforcements. Its lightweight nature helps enhance vehicle handling and maneuverability while ensuring passenger safety. Additionally, aluminum’s formability allows for the creation of sophisticated crash management systems, improving occupant protection in the event of collisions.
Fuel systems benefit from the application of aluminum high frequency welded tubes, as it enables the production of lightweight fuel tanks. Furthermore, aluminum pipes and tubes provide a reliable and efficient solution for fuel delivery and distribution within vehicles.
Air conditioning systems in automobiles utilize aluminum high frequency welded tubes for condenser and evaporator tubing. The excellent heat transfer properties of aluminum facilitate efficient cooling, enhancing overall comfort for passengers while reducing energy consumption.
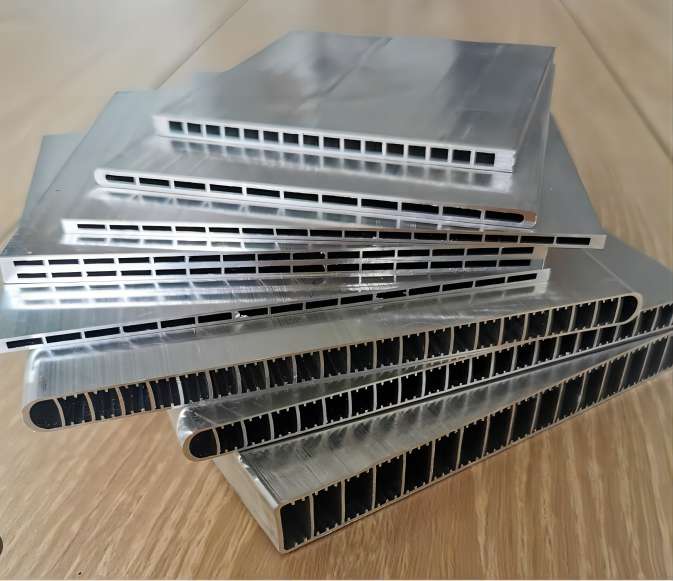
Advancements and Innovations in Aluminum High Frequency Welded Tube
Continuous advancements and innovations in aluminum high frequency welded tubes have further expanded its applications in the automotive industry. Improved welding techniques ensure stronger joints, increasing the overall durability and reliability of aluminum structures. Moreover, ongoing research focuses on developing new alloy compositions tailored for specific automotive applications, further optimizing performance and cost-effectiveness.
Surface treatments and coatings are being explored to enhance the already impressive properties of aluminum high frequency welded tubes. These treatments can improve corrosion resistance, thermal management, and even aesthetics. Additionally, the integration of aluminum with other materials, such as composites, offers hybrid solutions that provide a unique combination of properties to meet specific automotive requirements.
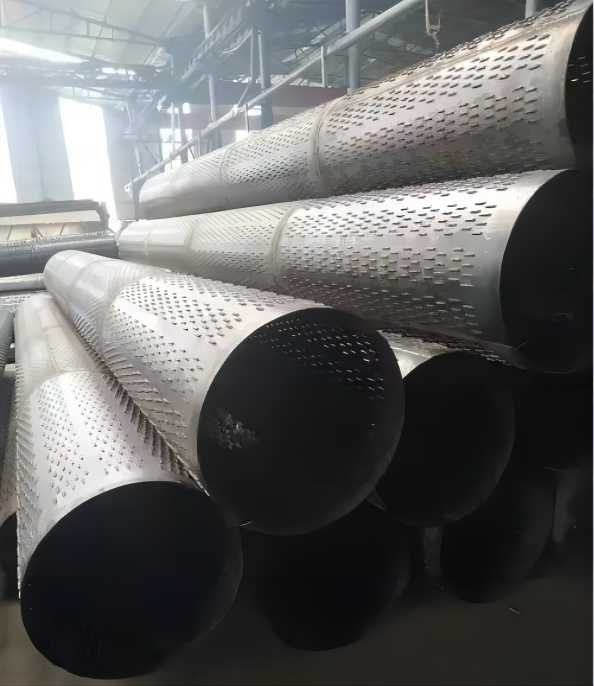
Challenges and Limitations
Despite the many benefits, there are certain challenges and limitations associated with using HFW Pipe in the automotive industry. One primary consideration is the cost. Although the price of aluminum has become more competitive over the years, it is still relatively higher than traditional materials like steel. However, the long-term benefits, such as improved fuel efficiency and reduced emissions, often offset the initial investment.
Another challenge is joining dissimilar materials. In automotive manufacturing, different materials are often used in combination to achieve the desired balance of strength, weight, and cost. Joining aluminum with other materials can be technically challenging and requires specialized techniques and expertise to ensure reliable and durable connections.
Manufacturing complexities also exist when working with HFW Pipe. The production process requires precise control of parameters such as temperature, pressure, and weld quality to achieve optimal results. Additionally, the availability of specialized equipment and skilled labor can pose challenges for manufacturers looking to incorporate this technology into their production lines.
Furthermore, it is important to consider the environmental impact of aluminum production. While aluminum is highly recyclable, the energy-intensive process of extracting and refining aluminum can contribute to carbon emissions. However, advancements in sustainable practices and increased recycling efforts are continuously being pursued to mitigate these environmental concerns.
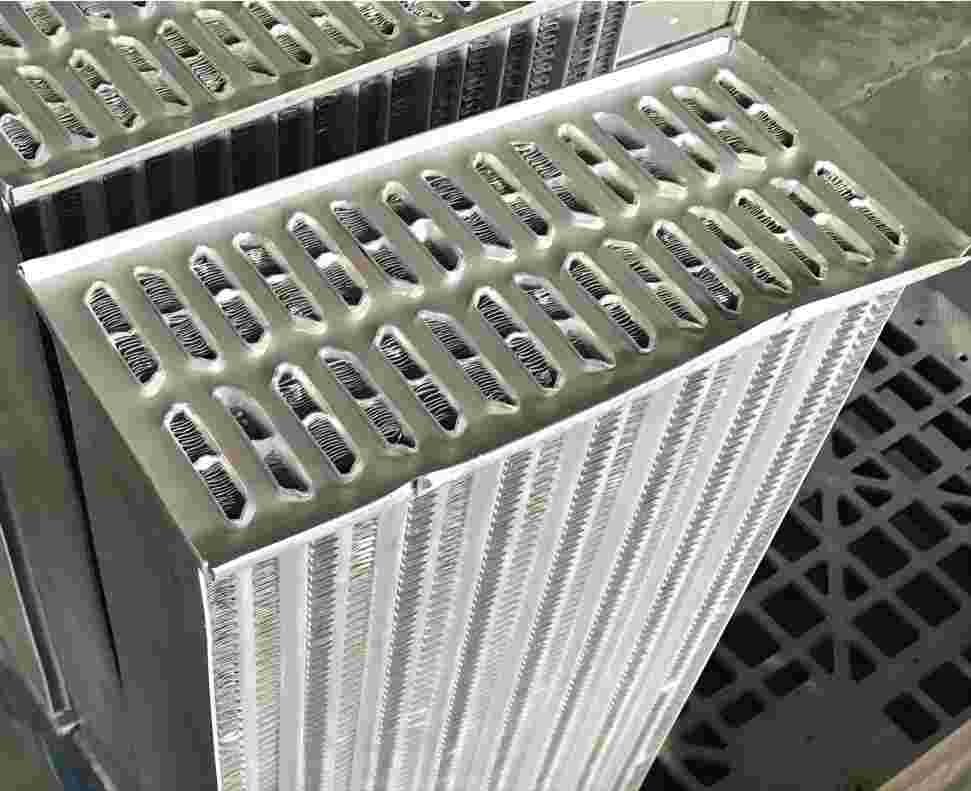
Conclusion
The application of aluminum high frequency welded tubes (HFW Pipe) has had a significant impact on the automotive industry. Its lightweight nature, combined with excellent strength, corrosion resistance, and formability, has made it a preferred choice for various automotive components. From radiators and cooling systems to exhaust systems, structural components, fuel systems, and air conditioning systems, HFW Pipe offers numerous advantages and contributes to improved vehicle performance, efficiency, and sustainability.
Continuous advancements in welding techniques, alloy compositions, surface treatments, and hybrid solutions further expand the possibilities and performance of HFW Pipe in the automotive industry. Despite challenges such as cost considerations, joining dissimilar materials, manufacturing complexities, and environmental impact, the overall benefits and ongoing research and development efforts suggest a promising future for HFW Pipe in the automotive sector.
As the automotive industry continues to embrace lightweight materials and sustainable practices, aluminum high frequency welded tube stands as a key solution, paving the way for safer, more efficient, and environmentally friendly vehicles. With ongoing innovation and collaboration between manufacturers, suppliers, and researchers, the application of HFW Pipe in the automotive industry is set to advance further, shaping the future of mobility.