In the realm of industrial applications, the choice of tubing can make a significant impact on performance, efficiency, and cost-effectiveness. While circular tubes have long been a staple in various industries, aluminum oval tubes are emerging as a compelling alternative, offering a range of advantages that go beyond traditional cylindrical designs. In this article, we explore the characteristics, benefits, and common questions surrounding aluminum oval tubes, shedding light on why they are gaining traction in the industrial landscape.
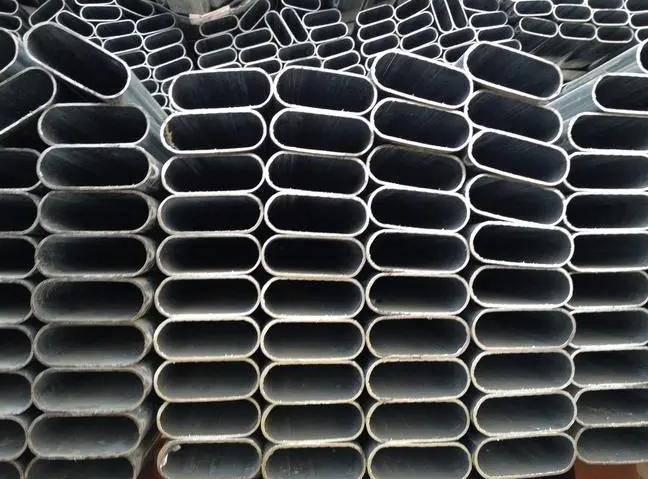
What are Aluminum Oval Tubes?
Aluminum oval tubes are extruded aluminum profiles with an oblong, elliptical cross-section. Unlike conventional circular tubes, which feature a uniform circumference, oval tubes boast a flattened profile, come with the width typically being greater than the height. They providing unique properties and come in a variety of sizes that make them suitable for diverse applications.
Characteristics of Aluminum Oval Tubes:
- Strength and Durability: Despite their sleek and slender profile, aluminum oval tubes maintain exceptional strength and durability, making them suitable for demanding industrial environments.
- Lightweight: Like all aluminum products, oval tubes are lightweight, facilitating easier handling, transportation, and installation.
- Corrosion Resistance: Aluminum’s inherent corrosion resistance ensures that oval tubes remain robust and reliable even in harsh operating conditions.
- Aesthetic Appeal: The distinctive oval shape adds a touch of elegance to structures and products, making them visually appealing for architectural and design applications.
- Versatility: Aluminum oval tubes are highly versatile, suitable for a wide range of uses.
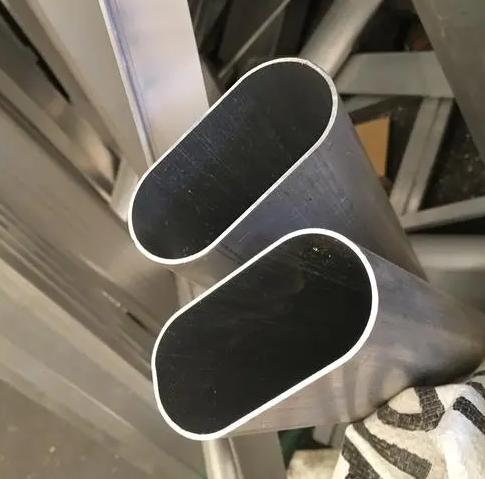
Advantages of Aluminum Oval Tubes
The adoption of aluminum oval tubes in industry brings forth a host of benefits:
- Improved Strength-to-Weight Ratio: Aluminum oval tubes offer a superior strength-to-weight ratio compared to traditional circular tubes. The oval shape distributes loads more efficiently along its longer axis, enhancing structural integrity without adding unnecessary weight. This makes them ideal for applications where lightweight yet robust materials are required, such as in aerospace, automotive, and marine industries.
- Enhanced Aesthetics and Design Flexibility: The elliptical profile of aluminum oval tubes provides a sleek and modern aesthetic compared to conventional circular tubes. This distinctive appearance adds visual interest to products and structures, making them stand out in architectural, interior design, and consumer product applications. Additionally, the elongated shape offers greater design flexibility, allowing for innovative and creative solutions in various industries.
- Increased Fluid Dynamics Efficiency: The streamlined design of aluminum oval tubes promotes smoother fluid flow compared to circular tubes. This reduces turbulence and pressure drop in fluid handling systems, resulting in improved efficiency and performance. As a result, aluminum oval tubes are commonly used in applications where fluid dynamics play a crucial role, such as in HVAC systems, hydraulic systems, and piping networks.
- Cost-Effectiveness and Material Savings: Aluminum oval tubes offer cost-effective solutions for manufacturers due to their efficient use of materials. The flattened profile allows for optimized material utilization, reducing waste and minimizing production costs. Additionally, aluminum’s recyclability further enhances cost-effectiveness and sustainability, making oval tubes an environmentally friendly choice for various industries.
- Versatile Applications: Aluminum oval tubes find applications across a wide range of industries due to their versatile properties. They are commonly used in aerospace for aircraft structures and components, in automotive for vehicle chassis and body framing, in construction for architectural features and structural elements, and in recreational equipment for lightweight and durable frames. Their versatility makes them indispensable in industries that demand high performance and reliability.
- Corrosion Resistance: Aluminum naturally forms a protective oxide layer on its surface, providing excellent corrosion resistance in various environments. This inherent property makes aluminum oval tubes suitable for outdoor applications where exposure to moisture, chemicals, and harsh weather conditions is a concern. Additionally, aluminum can be further enhanced with coatings or anodizing processes to improve its corrosion resistance and durability, extending the lifespan of products and structures.
- Ease of Fabrication and Installation: Aluminum oval tubes are relatively easy to fabricate, weld, and install compared to other materials such as steel or stainless steel. They can be bent, cut, and shaped to custom specifications using standard fabrication techniques, reducing production lead times and costs. Additionally, their lightweight nature simplifies handling and transportation, making them an attractive choice for manufacturers and contractors alike.
In summary, aluminum oval tubes offer a multitude of advantages, including improved strength-to-weight ratio, enhanced aesthetics, increased fluid dynamics efficiency, cost-effectiveness, versatile applications, corrosion resistance, and ease of fabrication and installation. These advantages make them a preferred choice for designers, engineers, and manufacturers seeking high-performance solutions across various industries.
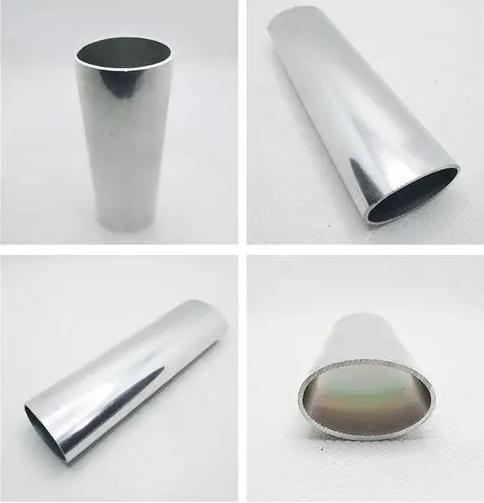
Common Asked Questions about Aluminum Oval Tube
Q1: What are the common grades of aluminum oval tubes through different applications?
Aluminum oval tubes are available in a variety of grades, each with its own unique properties suited for specific applications. Some common grades of aluminum used in oval tubes include:
Grade | Applications | Representative Components |
Aluminum 6061 | Aerospace, automotive, structural | Aircraft fuselage components, automotive chassis, structural beams |
Aluminum 6063 | Architectural, decorative, construction | Architectural trims, window frames, curtain walls |
Aluminum 5083 | Marine, naval architecture | Boat hulls, decks, marine structures |
Aluminum 7075 | Aerospace, high-performance | Aircraft wing spars, bicycle frames, high-stress components |
The choice of grade depends on factors such as desired strength, corrosion resistance, formability, and specific application requirements. Manufacturers and designers select the appropriate grade based on the performance characteristics needed for their particular application.
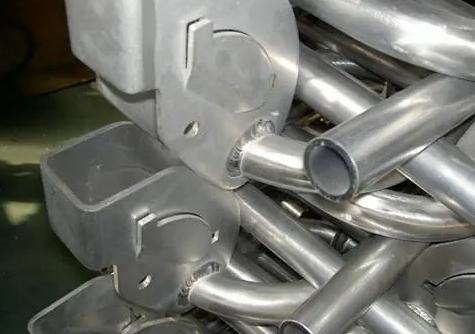
Q2: Can aluminum oval tubes be welded or bent easily?
Yes, aluminum oval tubes can be welded and bent with relative ease using standard fabrication techniques. Aluminum’s inherent properties, such as high formability and weldability, make it well-suited for these processes.
- Welding: Aluminum oval tubes can be welded using various methods, including TIG (Tungsten Inert Gas) welding, MIG (Metal Inert Gas) welding, and arc welding. TIG welding is commonly preferred for its precise control and clean welds, while MIG welding offers higher productivity for larger-scale production. Proper cleaning, preparation, and shielding gas selection are essential to achieve strong and reliable welds.
- Bending: Aluminum oval tubes can be bent to custom shapes and angles using specialized bending equipment. The process involves applying controlled force to the tube to deform it to the desired curvature without causing cracking or distortion. Proper tooling and bending techniques are crucial to maintain the structural integrity and dimensional accuracy of the tubing.
Overall, with the right equipment and expertise, welding and bending aluminum oval tubes can be accomplished efficiently, allowing for the fabrication of complex and customized structures.
Q3: Are there any limitations or considerations when designing with aluminum oval tubes?
While aluminum oval tubes offer numerous advantages, there are some limitations and considerations to keep in mind during the design process:
- Bending Radius: Aluminum oval tubes have a minimum bending radius that should be adhered to during fabrication to prevent cracking or distortion. Designers should consult with bending specialists to determine the appropriate bending radius for their specific application.
- Material Thickness Variations: The thickness of aluminum oval tubes may vary along their length, particularly in extruded or formed sections. Designers should account for these variations and ensure adequate strength and structural integrity in areas of thinner material.
- Welding Considerations: When designing structures or components with welded aluminum oval tubes, factors such as joint design, filler material selection, and welding process parameters should be carefully considered to ensure strong and reliable welds. Proper surface preparation and shielding gas selection are also critical to prevent defects and ensure weld quality.
- Support and Fixturing: Aluminum oval tubes may require additional support or fixturing during fabrication and assembly to prevent distortion or misalignment. Designers should incorporate provisions for adequate support and fixturing to maintain dimensional accuracy and structural integrity throughout the manufacturing process.
By addressing these limitations and considerations during the design phase, designers can optimize the performance and manufacturability of structures or components utilizing aluminum oval tubes, ensuring successful implementation in various applications.
Conclusion
Aluminum oval tubes represent a compelling alternative to traditional circular tubes in various industrial applications. Their unique characteristics, including enhanced strength, aesthetics, fluid dynamics efficiency, and cost-effectiveness, make them an attractive choice for designers and manufacturers looking to optimize performance and innovation. By understanding the advantages and considerations associated with aluminum oval tubes, industries can harness their full potential to drive progress and efficiency in the modern industrial landscape.