Heat exchangers are an integral part of various industrial processes and systems, playing a critical role in transferring heat from one fluid to another. Finned tubes, also known as finned tube coils, are a key component of heat exchangers that enhance their heat transfer capabilities. The choice of fin material in these tubes can significantly impact the performance, longevity, and cost-effectiveness of a heat exchanger. In this article, we will explore the advantages and disadvantages of three common fin materials: aluminum, copper, and stainless steel, to help you make an informed decision when choosing the right finned tube for your specific application.
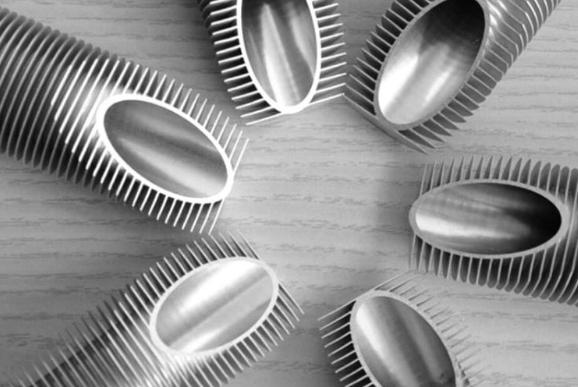
What is a Finned Tube?
Before diving into the different fin materials, it’s important to understand what a finned tube is. A finned tube is a heat exchanger component consisting of a tube with extended surfaces or fins attached to the outer surface. These fins serve to increase the surface area available for heat transfer between the tube’s contents and the surrounding environment. By doing so, they enhance the efficiency of heat transfer, making them invaluable in a wide range of applications.
Factors to Consider When Choosing a Fin Material
When choosing a fin material, the following factors should be considered:
- Heat transfer coefficient: The heat transfer coefficient is a measure of how well a material can transfer heat. Copper has the highest heat transfer coefficient of the three materials, followed by aluminum and stainless steel.
- Corrosion resistance: Copper and aluminum are both susceptible to corrosion, while stainless steel is highly resistant to corrosion.
- Cost: Copper is the most expensive of the three materials, followed by aluminum and stainless steel.
What are the Different Types of Fin Materials?
Finned tubes come in various materials, but three of the most commonly used are aluminum, copper, and stainless steel. Each material has its unique properties that make it suitable for specific applications. Let’s delve into each of these materials to understand their advantages and disadvantages.
1. Aluminum Finned Tubes
Advantages of Aluminum Finned Tubes
- Thermal Conductivity: Aluminum is an excellent conductor of heat, allowing for efficient heat transfer. It is ideal for applications where rapid heat exchange is essential, such as in HVAC systems and automotive radiators.
- Lightweight: Aluminum is relatively lightweight compared to copper and stainless steel, making it a preferred choice when weight is a critical factor.
- Corrosion Resistance: Aluminum naturally forms a protective oxide layer, which provides good resistance to corrosion in many environments.
Disadvantages of Aluminum Finned Tubes
- Lower Strength: Aluminum has lower mechanical strength compared to copper and stainless steel, which may limit its use in high-pressure or heavy-duty applications.
- Limited Temperature Range: Aluminum has a lower melting point and may not be suitable for applications involving very high temperatures.
2. Copper Finned Tubes
Advantages of Copper Finned Tubes
- Excellent Thermal Conductivity: Copper is one of the best heat conductors among common metals, making it highly efficient in transferring heat.
- Corrosion Resistance: Copper exhibits good corrosion resistance, especially in water-based environments, making it suitable for various applications, including refrigeration systems and solar water heaters.
- Longevity: Copper finned tubes have a long lifespan, contributing to their cost-effectiveness over time.
Disadvantages of Copper Finned Tubes
- Higher Cost: Copper is more expensive than aluminum, which can impact the initial cost of the heat exchanger.
- Susceptible to Galvanic Corrosion: Copper can experience galvanic corrosion when in contact with certain dissimilar metals, requiring careful material selection.
3. Stainless Steel Finned Tubes
Advantages of Stainless Steel Finned Tubes
- Corrosion Resistance: Stainless steel is highly resistant to corrosion, making it suitable for applications in corrosive environments, such as the chemical processing and food and beverage industries.
- Strength and Durability: Stainless steel offers excellent mechanical strength and durability, making it suitable for high-pressure and heavy-duty applications.
- Wide Temperature Range: Stainless steel can withstand a broad temperature range, making it versatile for various temperature-sensitive applications.
Disadvantages of Stainless Steel Finned Tubes
- Lower Thermal Conductivity: Stainless steel has lower thermal conductivity compared to copper and aluminum, which can result in lower heat transfer efficiency.
- Heavier: Stainless steel is heavier than both aluminum and copper, which may impact the overall weight of the heat exchanger system.
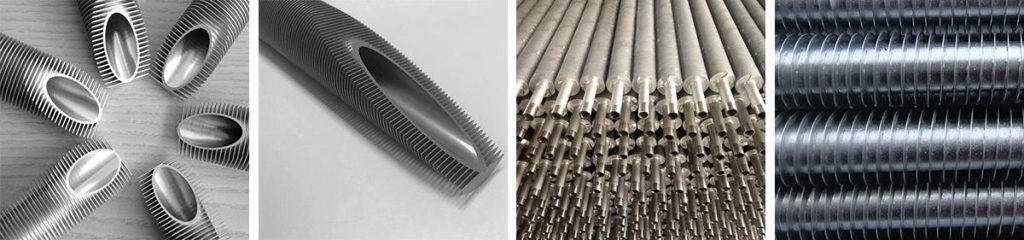
Which Fin Material is Right for You?
The choice of fin material depends on several factors, including the specific application requirements, budget considerations, and environmental conditions. Let’s explore these factors in more detail.
Applications of Each Fin Material
The following table shows some common applications of each fin material:
Fin Material | Applications |
Aluminum | Air conditioners, refrigerators, other appliances, food processing, chemical processing |
Copper | Power plants, chemical plants, and other industrial applications |
Stainless steel | Desalination plants, food processing plants, and other applications where corrosion resistance is important |
Cost Considerations
Copper is the most expensive of the three materials, followed by aluminum and stainless steel. However, the cost of the fin material is only a small part of the overall cost of a heat exchanger. Other factors, such as the cost of the tube material and the cost of manufacturing the heat exchanger, are also important.
Other Factors to Consider
- Environmental Conditions: Consider the operating environment, including temperature, humidity, and the presence of corrosive substances. Stainless steel may be the best choice for highly corrosive environments.
- Weight Restrictions: If weight is a concern, aluminum’s lightweight nature may be advantageous.
- Mechanical Strength: Evaluate the mechanical strength requirements of your application. Copper and stainless steel are stronger than aluminum and can handle higher pressure loads.
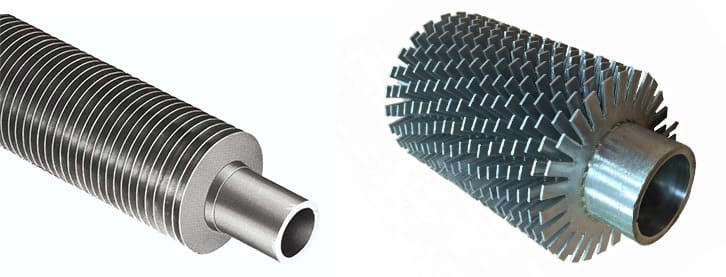
Conclusion
In conclusion, choosing the right fin material for your heat exchanger is a critical decision that can impact efficiency, longevity, and overall costs. Each material—aluminum, copper, and stainless steel—has its unique advantages and disadvantages. Consider the specific requirements of your application, environmental conditions, and budget constraints when making your selection. Consulting with experts in the field can also provide valuable insights into the best finned tube material for your needs. By carefully weighing these factors, you can ensure that your heat exchanger performs optimally and efficiently in its intended application.