Typically, tubes equipped with surface intensifiers, such as fins or grooves, are used where heat exchange is required between two fluids whose heat transfer capacities are far apart. For example, for water/air exchange, the local exchange coefficient on the waterside is much higher than that on the airside. Fins are therefore added to surfaces in contact with air to increase the density of the heat flux between the two fluids.
As the only interface between heat and cold sources, the extruded fin tube is the core of heat transfer. Its mass is critical to the exchanger’s ability to transfer heat energy efficiently between the two fluids. More precisely, the way the fins are attached to the tube affects the efficiency of the exchanger in the short, medium, and long term.
In fact, studies have shown that the main reason for the efficiency loss of heat exchangers is the deterioration of the connection quality between fins and pipes. In fact, after several thermal cycles, a gap can develop between the fin and the tube due to thermal expansion and vibration. The tube-fin bonding can be affected by galvanic corrosion between the two materials. There are so many kinds of material, why choose aluminum for finned tube making?
Why are finned tubes used in various materials?
A variety of materials are available depending on the application and operation of heat exchange.
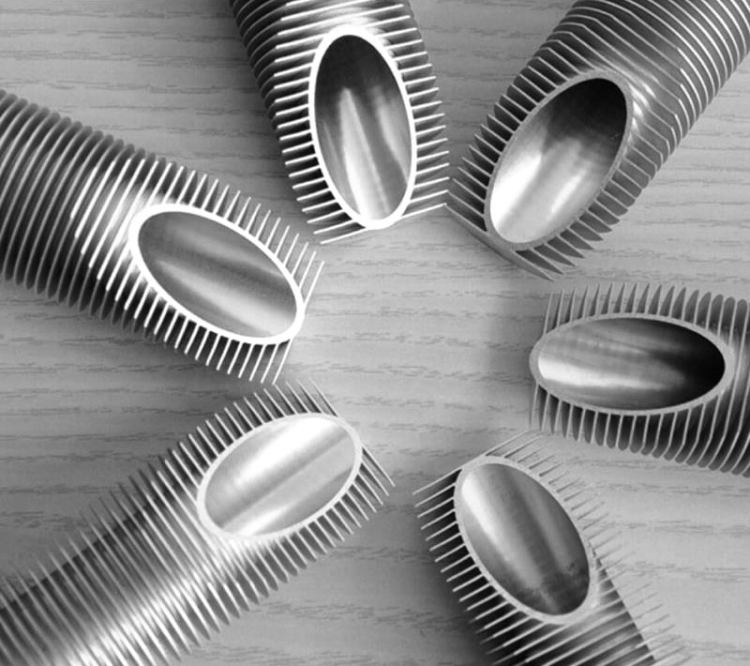
Common aluminum, alloy, copper, brass, nickel, titanium, stainless steel, carbon steel, etc., with aluminum and alloy most.
The finned tube should own the basic performance as weldability and formability, high mechanical strength, good corrosion resistance and thermal conductivity. Nevertheless, aluminum and alloys are also characterized by elongation at lower temperatures and higher tensile strength increases. They are widely used worldwide, especially in low temperature and compact heat exchange.
Aluminum forms the fine thick finned tube
The choice of fin thickness depends on the corrosion and wear of the fluid gas. Thicker fins are usually used in sites where corrosion is severe.
Aluminum also forms the fine high finned tube
When the fin root is grounded on the bare tube at the base, the heat will be transferred from the fin root along the fin height in the case of heat from inside out. It is also continuously transferred to the surrounding fluid by convection heat transfer. As a result, the fin temperature decreases gradually along with the height. This also indicates that the difference between fin temperature and ambient fluid temperature is gradually decreasing, and the change of unit heat is shrinking. Therefore, the effect of fin surface area on enhanced heat transfer is decreasing. The higher the fin, the less contribution the increased area makes to heat exchange.
Generally speaking, when the fin height is 15mm, the fin efficiency of high-frequency welded fin tube used in engineering projects is about 0.8; When the fin height is 20mm, the fin efficiency decreases to 0.7. Based on this, 15mm is the optimal height. If the fin height is above 20mm, the fin efficiency will be very poor, so it is generally not used. However, for aluminum fins on air coolers, since aluminum has much better thermal conductivity than carbon steel, a height of 22-25mm is usually used.
Let’s look at the characteristics of aluminum
1. Low density
Through alloying and heat treatment, it can achieve the structure of construction steel. Suitable for all kinds of vehicles, especially small vehicles, reduce weight and consumption.
2. Good corrosion resistance
The aluminum oxide material is non-toxic under severe conditions. Aluminum heat exchange, do not worry about the internal air or liquid for a long time will be destroyed by oxide.
3. Good thermal conductivity
Especially suitable for heat dissipation fin, heat transfer evaporator and condenser.
4. High yield, die-cutting resistance
Easy to process and form.
As a professional finned tube manufacturer, our main product is aluminum finned tube. If you have any interest, please contact us for more information.
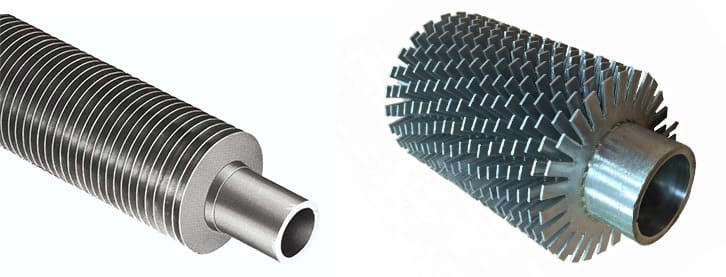
How will fin pitch affect fin ratio?
Usually, a smaller pitch can effectively increase the fin ratio. The following factors should be taken into account when considering the nature of flowing gas and ash accumulation.
1. Severe ash deposition
Such as iron and steel plant furnace, converter and industrial cellar furnace exhaust, ash weight. If finned tubes are used for heat exchange, a larger fin spacing is recommended. For example, if the spacing is more than 10mm, you need to add a vent and choose a fan.
2. Occasions where there is a small amount of dust accumulation but attention should also be paid.
Take the exhaust of factory boiler and industrial boiler as an example, the fin spacing of 8mm is appropriate, but should be designed with self-blowing ability.
3. Dust-free or light dust-free occasions.
Such as combustion of natural gas equipment or air cooler exhaust, fin spacing 4-6mm can be. For aluminum air cooler, fin spacing is also selected 3mm.
Conclusion
Aluminum makes finned tube performs at a higher level, and it enhances the efficiency, it is the best material in both views from the material of cost. If you are looking for a professional aluminum finned tube manufacturer, contact us, we have a professional team with decades of experience in producing aluminum tubes, we can support you with the best aluminum tube from China.