An inner grooved tube refers to a type of tube that features longitudinal grooves or ridges on its inner surface. These grooves are intentionally designed to increase the surface area available for heat transfer or fluid flow. Inner grooved tubes are commonly used in heat transfer applications where efficient heat exchange or fluid movement is crucial.
Both inner grooved copper tubes and aluminum inner grooved tubes are designed to maximize heat transfer efficiency by increasing the available surface area for heat exchange. While copper tubes offer superior thermal conductivity and corrosion resistance, aluminum tubes provide the advantage of lightweight construction. The choice between these two types of inner grooved tubes depends on the specific application requirements, including thermal performance, weight considerations, and system compatibility.
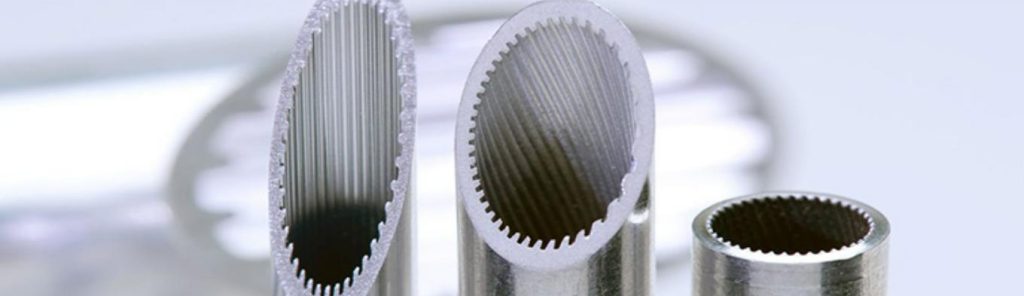
6 Considerations for Choosing Between Inner Grooved Copper Tube and Aluminum Inner Grooved Tube
When deciding between inner grooved copper tubes and aluminum inner grooved tubes for a specific application, several considerations should be taken into account. Here are some key factors to consider:
- Thermal Performance: Evaluate the heat transfer requirements of your application. Copper has higher thermal conductivity than aluminum, which results in better heat transfer efficiency. If maximizing heat transfer is crucial, inner grooved copper tubes may be the preferred choice. However, if the thermal requirements can be met with the lower thermal conductivity of aluminum, it may be a more cost-effective option.
- Corrosion Resistance: Consider the environmental conditions and the fluid that will come into contact with the tube. Copper has excellent corrosion resistance, making it suitable for applications involving corrosive fluids or environments. Aluminum, while generally corrosion-resistant, may require additional protective coatings or treatments in certain situations. Assess the level of corrosion resistance needed for your application and choose accordingly.
- Weight Considerations: Determine whether weight reduction is a significant factor in your application. Aluminum is significantly lighter than copper, making it advantageous in weight-sensitive applications such as automotive, aerospace, or portable systems. If reducing weight is a priority, aluminum inner grooved tubes may be the preferable choice.
- Cost: Evaluate your budget constraints and project requirements. Copper is generally more expensive than aluminum. Consider the cost-effectiveness of each option, including material costs, fabrication expenses, and long-term maintenance costs. Assess whether the additional benefits of copper justify the higher cost in your specific application.
- Fabrication and Manufacturing: Consider the ease of fabrication and manufacturing processes. Copper tubes are less malleable and require specialized equipment and techniques for bending and shaping. Aluminum, on the other hand, is more malleable and easier to fabricate. Assess your manufacturing capabilities and the complexity of the desired tube shapes to determine which material aligns better with your fabrication requirements.
- Compatibility with System Components: Evaluate the compatibility of the chosen material with other system components. Copper is widely used and compatible with various fittings, joints, and brazing techniques commonly used in heat transfer systems. Aluminum may require specific considerations and compatibility checks, as it has different material characteristics and may necessitate different joining methods or specialized components.
By carefully considering these factors, you can make an informed decision regarding the most suitable choice between inner grooved copper tubes and aluminum inner grooved tubes for your specific heat transfer application. Or if you still cannot make a decision, please feel free to contact us, and we will give you professional suggestions.