Aluminum finned tubes play a vital role in this domain by enhancing heat dissipation through their extended surface area. These tubes comprise a hollow core pipe, typically made of copper, stainless steel, or other suitable materials, surrounded by fins – thin, elongated protrusions – crafted from aluminum due to its excellent thermal conductivity. The fins significantly augment the heat exchange surface area compared to a bare tube, promoting efficient heat transfer between the fluid flowing within the tube and the surrounding environment. The design and configuration of these fins significantly influence the performance of the aluminum finned tube. Several key parameters impact heat transfer efficiency, pressure handling capabilities, and even the lifespan of the tube. Understanding these parameters and their impact is crucial for selecting the most suitable aluminum finned tube for a specific application.
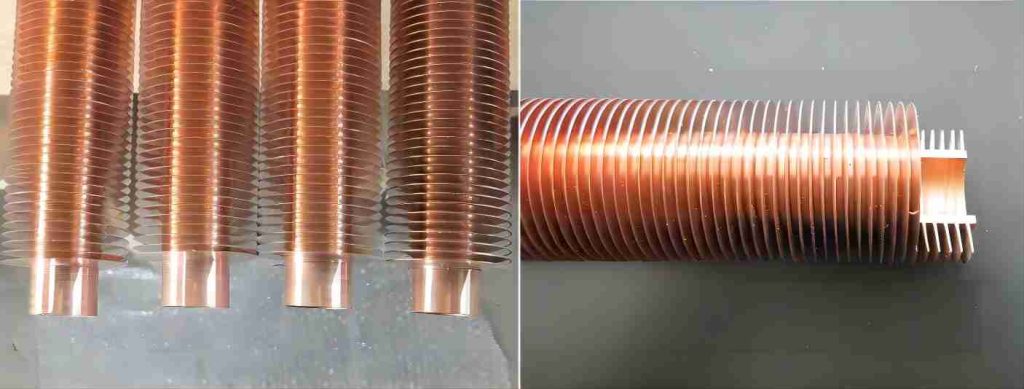
Key Parameters of Aluminum Finned Tubes
1. Fin Height
Fin height, denoted by the distance between the tip of the fin and the external surface of the tube, is typically measured in millimeters (mm). The selection of fin height is a balancing act between maximizing heat transfer performance, air velocity, and air flow pattern.
- Impact on Heat Transfer: Taller fins create a larger heat exchange surface area, promoting enhanced heat transfer from the fluid within the tube to the surrounding air. However, excessively tall fins can hinder air circulation, leading to a counterproductive effect.
- Air Velocity and Flow Pattern: The effectiveness of heat transfer depends on the air velocity across the fins. Higher air velocity allows for greater heat removal; however, excessively tall fins can create significant air resistance, requiring a stronger fan to maintain adequate airflow. Additionally, the air flow pattern around the fins is crucial. Turbulent air flow can offer better heat transfer compared to laminar flow, but it also increases air resistance. Fin height can be adjusted to influence the air flow pattern and achieve optimal heat transfer.
2. Fin Thickness
Fin thickness, measured in millimeters (mm), plays a crucial role in balancing heat transfer performance, structural strength, and cost.
- Heat Transfer: Thicker fins offer a larger conductive path for heat transfer from the tube to the fins. However, excessively thick fins can impede heat transfer from the fin itself to the surrounding air, reducing overall efficiency.
- Strength: Fintubes are subjected to various forces during operation, including pressure from the internal fluid and external wind loads. Thicker fins offer greater structural integrity, but they also add weight and increase material costs.
- Cost: Fin thickness directly impacts the material consumption and manufacturing cost of the finned tube. Selecting an optimal fin thickness requires balancing heat transfer performance, structural needs, and economic considerations.
3. Fin Spacing
Fin spacing, measured in millimeters (mm), refers to the distance between adjacent fins. Similar to the other parameters, fin spacing requires careful consideration to optimize performance.
- Heat Transfer: Closer fin spacing creates a larger heat exchange surface area, potentially enhancing heat transfer. However, excessively close spacing can restrict air flow, hindering heat removal from the fins.
- Air Resistance: Wider fin spacing allows for better air flow, reducing air resistance and facilitating heat removal by the air stream. However, wider spacing reduces the heat exchange surface area, potentially affecting overall heat transfer performance.
Finding the optimal fin spacing involves balancing these opposing factors. In some cases, utilizing fins with varying spacing along the length of the tube can be beneficial. For example, wider spacing at the inlet can promote air flow, while closer spacing near the outlet can maximize heat transfer from the warmer fluid.
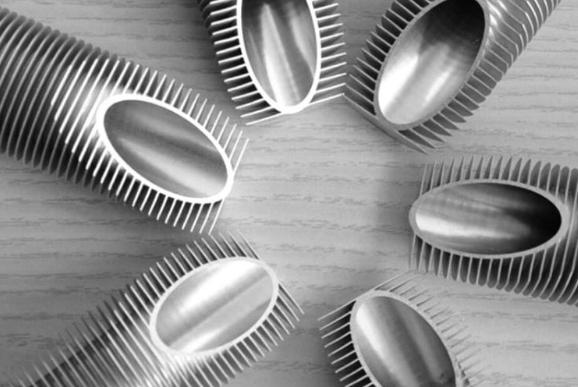
4. Tube Diameter
The tube diameter, measured in millimeters (mm), refers to the internal diameter of the aluminum finned tube. Selecting the appropriate tube diameter is crucial for optimizing fluid flow, pressure handling capabilities, and even heat transfer performance.
- Fluid Flow: A larger tube diameter allows for a higher flow rate of the fluid within the tube. This is important for applications requiring high heat transfer rates. However, a larger diameter also reduces the surface area available for heat transfer with the fins.
- Pressure Capacity: The tube diameter plays a significant role in determining the pressure the finned tube can withstand. Thicker tubes offer greater pressure handling capabilities, making them suitable for high-pressure applications.
- Heat Transfer: While a larger tube diameter allows for higher flow rates, it also reduces the surface area for heat exchange with the fins. This can be a trade-off in some applications. In such cases, utilizing multiple smaller diameter tubes within a single finned structure can provide a balance between maximizing flow rate and maintaining sufficient heat exchange surface area.
Additional Considerations
- Material Selection: The choice of material for the core tube of the aluminum finned tube is critical. Common materials include copper, stainless steel, and various alloys. Each material offers unique advantages and disadvantages. Copper offers excellent thermal conductivity but may be susceptible to corrosion in specific environments. Stainless steel provides good corrosion resistance but has a lower thermal conductivity compared to copper. The selection of the core tube material should be based on factors like thermal conductivity, corrosion resistance, pressure requirements, and compatibility with the working fluid.
- Fin Types: Aluminum finned tubes come in various fin configurations, each offering distinct advantages. Popular types include:
- Extruded Fin Tubes: These tubes are manufactured by forcing aluminum through a die, forming continuous fins around the core tube. They offer good heat transfer performance and are cost-effective for mass production.
- Mechanically Bonded Fin Tubes: Pre-formed fins are mechanically attached to the core tube using press-fit or other methods. This allows for greater flexibility in fin design but may be slightly less cost-effective than extruded fins.
- Welded Fin Tubes: Fins are welded directly onto the core tube, providing a strong and leak-proof bond. This option is suitable for high-pressure applications but can be more expensive compared to other methods.
The choice of fin type depends on factors like desired heat transfer performance, pressure requirements, cost considerations, and the specific application.
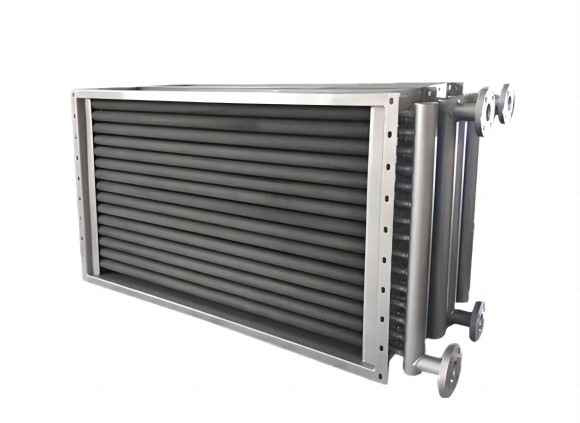
Applications of Aluminum Finned Tubes
Aluminum finned tubes play a vital role in numerous heat exchange applications due to their exceptional thermal performance and lightweight design. Their ability to efficiently transfer heat while maintaining minimal weight makes them a highly sought-after choice across various industries. Let’s delve deeper into some of the most common applications of aluminum finned tubes:
- Air Conditioning Systems: In the condenser coils of air conditioners, aluminum finned tubes are instrumental in facilitating heat transfer. Hot refrigerant gas, carrying heat extracted from the indoor environment, flows through the core tubes. The fins significantly increase the surface area exposed to the surrounding air, allowing efficient heat dissipation from the refrigerant to the external environment. This process is crucial for the proper functioning of air conditioning systems by ensuring effective heat removal and maintaining a comfortable indoor temperature.
- Automotive Radiators: Car radiators rely heavily on aluminum finned tubes to manage heat generated by the engine. The engine coolant, absorbing heat during engine operation, circulates through the core tubes of the radiator. The extensive surface area provided by the fins allows efficient heat transfer from the hot coolant to the surrounding air flowing through the radiator. This heat dissipation process is critical for maintaining optimal engine operating temperature and preventing overheating, which can lead to severe engine damage.
- Heat Exchangers: Aluminum finned tubes are a mainstay component in various industrial heat exchangers. These heat exchangers facilitate the transfer of thermal energy between two fluids at different temperatures. They find application in a wide range of industrial processes, including:
- Oil Coolers: Engine oil in machinery can reach extremely high temperatures during operation. Oil coolers utilize aluminum finned tubes to transfer heat from the hot oil to a coolant fluid, typically air or water. This prevents excessive oil temperatures, which can deteriorate the oil’s lubricating properties and lead to increased wear and tear on engine components.
- Power Plant Condensers: In power plants, steam generated during electricity production needs to be converted back into water for recirculation. Aluminum finned tubes within condensers facilitate heat transfer from the exhaust steam to cooling water, condensing the steam back into liquid water. This process is essential for maintaining efficient power generation cycles.
- Chemical Processing Equipment: Chemical reactions often generate significant heat. Heat exchangers with aluminum finned tubes are employed in chemical processing plants to control reaction temperatures and prevent overheating, ensuring safe and efficient chemical production processes.
- Electronic Cooling: The ever-increasing miniaturization and processing power of electronic components necessitate efficient thermal management solutions. Aluminum finned tubes are frequently used in heat sinks for electronic devices. These heat sinks are attached to electronic components that generate significant heat, such as processors and power supplies. The fins efficiently dissipate heat generated by the components to the surrounding air, preventing overheating and ensuring reliable operation of the electronics.
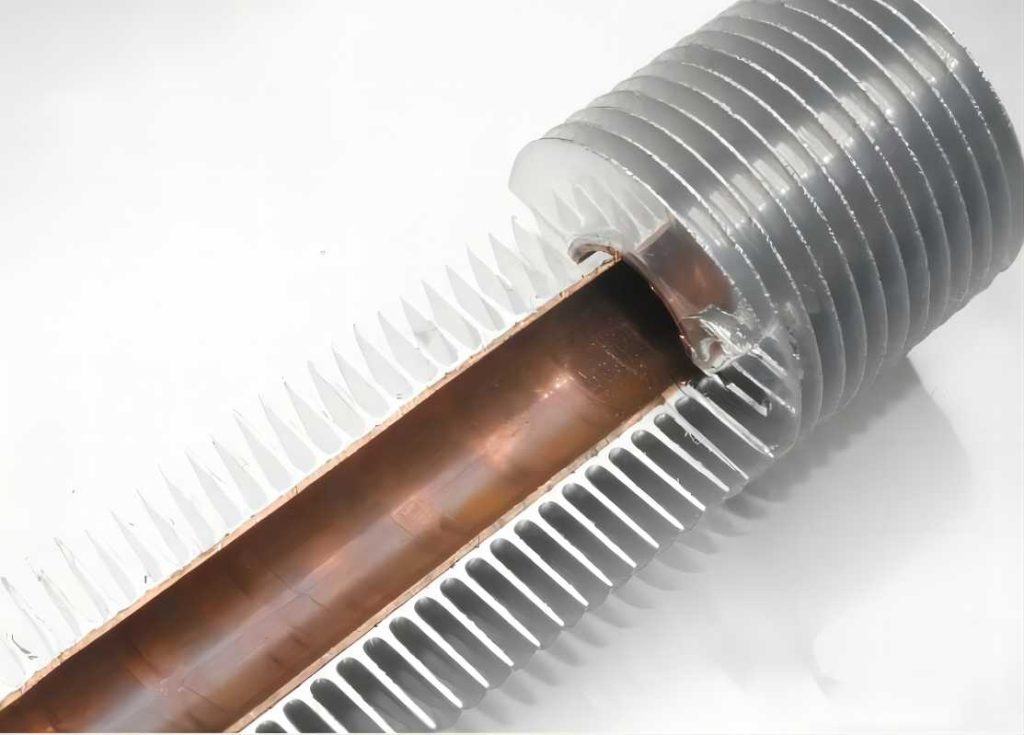
Conclusion
Understanding the key parameters of aluminum finned tubes – fin height, thickness, spacing, and tube diameter – empowers engineers to select the most suitable option for a specific application. By carefully considering the trade-offs between heat transfer performance, pressure handling capabilities, and other factors, the optimal selection of these parameters ensures efficient and reliable heat exchange in various industrial and commercial applications. Furthermore, advancements in manufacturing techniques and material science continue to expand the capabilities and applications of aluminum finned tubes, making them a valuable tool for effective thermal management.