In the intricate world of thermal management, heat exchangers reign supreme. Their effectiveness hinges on a critical component – the aluminum finned tube. These seemingly simple structures, with their extended fins gracing the central tube, play a pivotal role in maximizing heat transfer and ultimately influencing the efficiency of the entire system. However, selecting the optimal aluminum finned tube for your specific project demands a nuanced understanding of the interplay between various factors and their impact on heat exchanger performance.
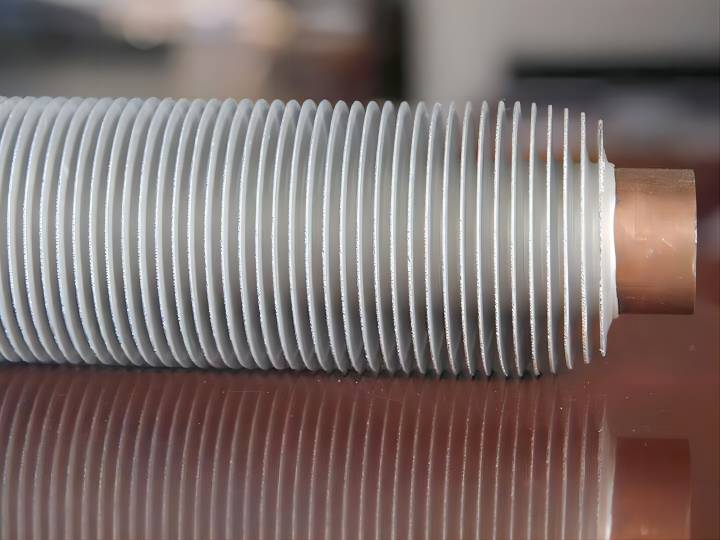
What Factors of the Aluminum Finned Tube Will Influence the Heat Exchanger Efficiency?
The intricate dance of heat transfer within a heat exchanger is orchestrated by a complex interplay of factors, many of which are directly influenced by the chosen aluminum finned tube. Let’s dissect these determinants and their impact:
1. Tube Properties
- Material: The thermal conductivity of the tube material sets the stage for overall heat transfer. Aluminum shines in this arena, boasting a conductivity approximately four times that of steel, significantly accelerating heat exchange. Furthermore, the tube’s thickness and surface roughness influence heat transfer. A thinner tube wall minimizes thermal resistance, while a rougher surface enhances contact with the fins, thereby improving heat transfer efficiency.
- Diameter: The tube diameter plays a crucial role in balancing surface area and flow resistance. A larger diameter increases the surface area available for heat transfer, but it also elevates the pressure drop within the tube. Conversely, a smaller diameter minimizes pressure drop but restricts heat transfer potential. Finding the optimal diameter requires a careful analysis of the specific fluid properties and flow rates involved in your project.
2. Fin Design and Configuration
- Fin-tastic Materials and Geometry: The material chosen for the fins, alongside their geometry, significantly impacts heat transfer and pressure drop. While aluminum fins reign supreme due to their high thermal conductivity, copper fins offer even greater conductivity but come at a higher cost. In terms of geometry, flat fins provide a simple yet effective solution, while wavy or serrated fins offer enhanced surface area and turbulence, leading to improved heat transfer but potentially increasing pressure drop.
- Spacing and Thickness Symphony: The spacing and thickness of the fins orchestrate a delicate balance between heat transfer and pressure drop. Closer spacing increases the surface area and potential for heat exchange, but it also elevates the pressure drop due to increased flow restriction. Conversely, thicker fins offer greater structural stability and thermal capacity but may impede heat transfer due to reduced surface area. Finding the optimal spacing and thickness necessitates meticulous consideration of the specific flow rates and fluid properties.
- Fin Attachment Fusion: The method employed to attach the fins to the tube plays a crucial role in thermal contact and durability. Mechanical bonding, brazing, and welding each offer unique advantages and disadvantages. Mechanical bonding offers ease of assembly but may compromise thermal contact, while brazing and welding provide superior thermal contact but require specialized equipment and expertise. Choosing the appropriate attachment method requires careful consideration of the desired thermal performance, budget constraints, and operational environment.
3. Operating Conditions
- Fluid Flow Finesse: The thermal conductivity, viscosity, and flow rate of the hot and cold fluids flowing through the heat exchanger significantly influence efficiency. Matching the fin design to the specific fluid properties is paramount. For fluids with high viscosity or low flow rates, fins with increased surface area and turbulence may be necessary to overcome thermal resistance, while for fluids with low viscosity and high flow rates, simpler fin geometries may suffice.
- Temperature and Pressure: The operating temperatures and pressures within the heat exchanger impose limitations on the materials and design of the aluminum finned tubes. Exceeding the material’s thermal expansion or pressure limits can lead to deformation or even failure. Therefore, careful selection of materials and fin designs able to withstand the specific operating conditions is crucial.
- Fouling and Corrosion: The potential for fouling and corrosion poses a significant threat to heat exchanger efficiency. Fouling, the buildup of deposits on the fins, impedes heat transfer, while corrosion weakens the tube and fins, compromising their structural integrity. Choosing materials and coatings resistant to fouling and corrosion in the specific operating environment is essential for maintaining long-term performance.
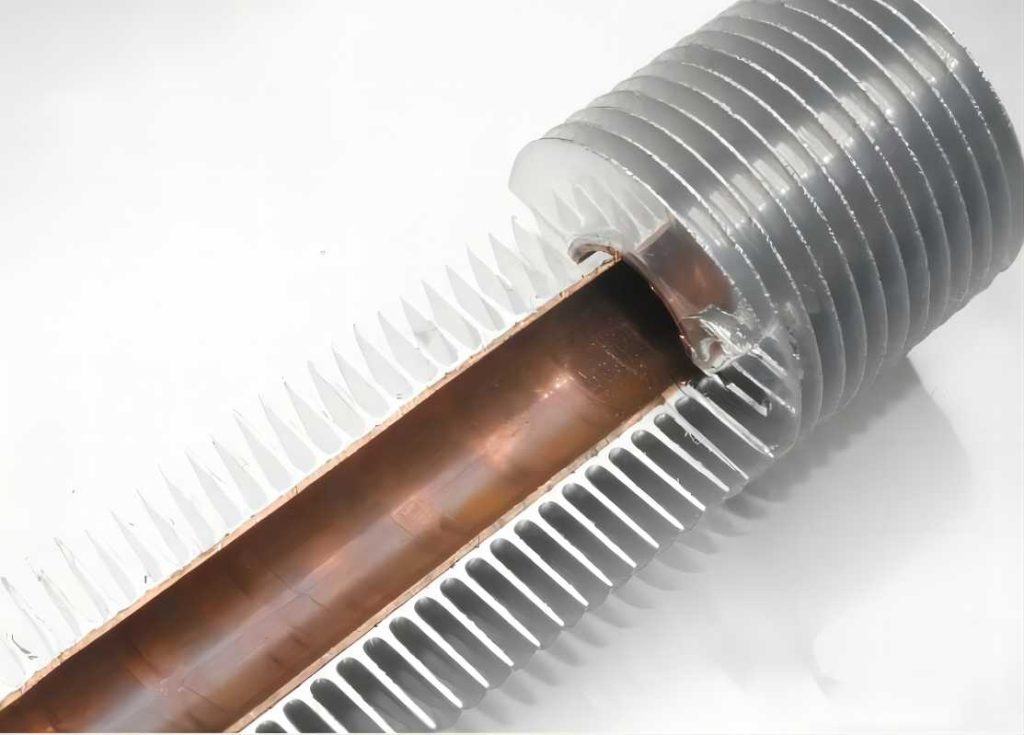
How to Choose the Right Aluminum Finned Tubes for Your Projects?
Selecting the optimal aluminum finned tube for your project demands a meticulous, multi-faceted approach that balances the desired thermal performance with critical constraints. This involves a carefully orchestrated dance between heat transfer capacity, pressure drop limitations, material compatibility, and budgetary considerations. To navigate this complex process, follow these key steps:
1. Define Project Requirements
- Heat Transfer Quantification: Clearly define the desired heat removal or addition duty of the heat exchanger. This necessitates specifying the inlet and outlet temperatures of both fluids, the target heat transfer rate, and the heat transfer fluid properties (specific heat capacity, density, etc.).
- Flow Rate and Pressure Drop Constraints: Establish the maximum allowable flow rate through the tubes and the acceptable pressure drop across the heat exchanger. Consider the pumping power available and any downstream limitations imposed by the system.
- Material Compatibility: Identify the compatibility of the finned tube material with both fluids and the operating environment. Evaluate factors such as corrosion resistance, thermal expansion coefficients, and potential fouling tendencies.
- Budgetary Considerations: Determine the budget allocated for the finned tube component and ensure your selection aligns with cost constraints while meeting the desired performance objectives.
2. Evaluate Finned Tube Options
- Fin Geometry Analysis: Compare different fin types (flat, serrated, wavy) and their impact on surface area, heat transfer coefficient (HTC), and pressure drop. Consider the trade-off between enhanced heat transfer and increased flow resistance.
- Material Selection: Analyze the thermal conductivities of various fin and tube materials (aluminum, copper, stainless steel) and their influence on overall HTC. Weigh the cost-performance trade-offs and potential corrosion resistance requirements.
- Fin Thickness and Spacing Optimization: Evaluate the impact of fin thickness and spacing on heat transfer and pressure drop. Thicker fins offer greater structural integrity but may limit heat transfer, while closer fin spacing increases surface area but elevates pressure drop.
3. Leverage Computational Tools
- Manufacturer Data: Utilize manufacturer-provided performance data and design charts for specific finned tube configurations under various operating conditions. This data can offer valuable insights into heat transfer potential and pressure drop characteristics.
- Heat Exchanger Simulation Software: Employ specialized software tools to simulate the thermal performance of different finned tube options within your specific heat exchanger design. These tools can predict heat transfer rates, pressure drops, and fluid outlet temperatures, providing a comprehensive picture of performance under real-world conditions.
4. Seek Expert Guidance
- Consult with Heat Exchanger Engineers: Collaborate with experienced heat exchanger engineers to leverage their expertise in finned tube selection and heat exchanger design. They can provide valuable insights into optimal material choices, fin configurations, and potential challenges to overcome.
- Manufacturer Technical Support: Utilize the technical support offered by finned tube manufacturers to address specific questions and concerns regarding their products. They can provide detailed information on material properties, performance data, and fabrication options.
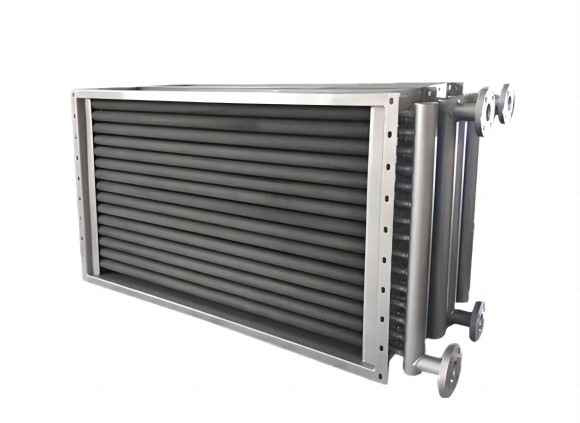
Conclusion
Optimizing heat exchanger efficiency through the strategic selection of aluminum finned tubes is a delicate art, demanding a deep understanding of the interplay between various factors. By delving into the tube properties, fin design complexities, and operating conditions, you can unlock the full potential of your heat exchanger and achieve exceptional thermal performance. Remember, choosing the right aluminum finned tube is not simply about selecting a product; it’s about investing in a solution that delivers optimal efficiency, maximizes energy savings, and ensures the long-term success of your project.