Drawn aluminum tubes, also known as DOM (drawn over mandrel) tubes, are a type of seamless aluminum tubing produced through a cold drawing process. This process involves pulling a heated aluminum billet through a series of dies, gradually reducing its diameter and achieving precise dimensional tolerances. Drawn aluminum tubes are known for their superior strength, uniformity, and surface finish compared to extruded aluminum tubes.
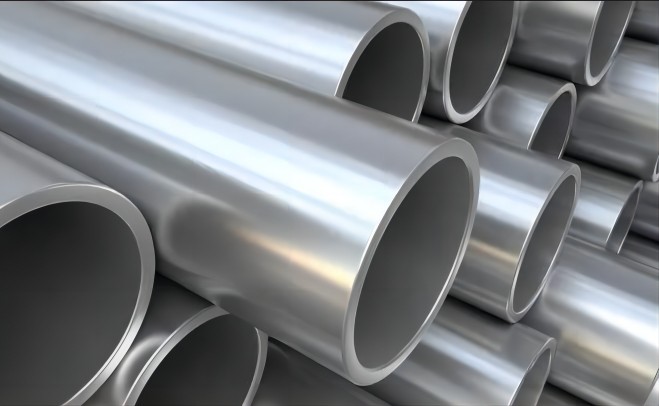
Advantages and Applications of Drawn Aluminum Tubes
Drawn aluminum tubes offer several advantages, making them suitable for a wide range of applications:
- High Strength-to-Weight Ratio: Drawn aluminum tubes exhibit exceptional strength while maintaining lightweight properties, making them ideal for applications where weight reduction is crucial.
- Dimensional Accuracy: The cold drawing process ensures precise dimensional tolerances, critical for applications requiring tight fitting or close tolerances.
- Smooth Surface Finish: Drawn aluminum tubes possess a smooth, uniform surface finish, enhancing their appearance and reducing friction.
- Corrosion Resistance: Aluminum is naturally corrosion-resistant, making drawn aluminum tubes suitable for use in harsh environments.
- Weldability: Drawn aluminum tubes can be readily welded, expanding their versatility.
Manufacturing Process of Drawn Aluminum Tubes
The manufacturing process of drawn aluminum tubes involves the following steps:
- Billet Preparation: The starting point for drawn aluminum tubes is an aluminum billet, a cylindrical or rectangular cast of aluminum alloy. The billet is carefully selected based on the desired alloy composition and dimensions. It is then heated to a specific temperature to soften the aluminum and make it more malleable for the drawing process.
- Lubrication: To minimize friction and prevent galling during drawing, the heated billet is thoroughly coated with a high-performance lubricant. The lubricant acts as a protective layer between the billet and the dies, reducing wear and tear on both surfaces.
- Breaking Down: The drawing process begins with breaking down the billet through a series of progressively smaller dies. Each die is designed with a specific diameter slightly smaller than the previous one. The billet is forced through each die, gradually reducing its diameter and elongating its shape.
- Mandrel Drawing: To maintain the internal diameter and ensure uniformity throughout the drawing process, a mandrel is inserted into the tube. The mandrel is a rigid rod or bar, typically made of polished steel or tungsten carbide, that provides support and prevents the tube from collapsing.
- Annealing: After multiple passes through the dies, the drawn tube may undergo annealing, a heat treatment process that relieves internal stresses and restores the tube’s ductility. Annealing is crucial for achieving the desired mechanical properties, such as formability and tensile strength.
- Finishing: The final steps in the manufacturing process involve straightening the drawn tube to remove any residual curvature and cutting it to the desired length. The surface finish may also be refined through processes like polishing or honing, depending on the application requirements.
Factors Influencing the Quality and Properties of Drawn Aluminum Tubes
Several factors influence the quality and properties of drawn aluminum tubes:
- Billet Material: The purity and alloy composition of the aluminum billet significantly impact the tube’s strength, formability, and corrosion resistance.
- Drawing Process Parameters: The temperature, speed, and reduction ratio during drawing affect the tube’s grain structure, mechanical properties, and dimensional tolerances.
- Mandrel Material and Surface: The material and surface finish of the mandrel influence the tube’s internal surface quality and prevent internal defects.
- Heat Treatment: Proper heat treatment can enhance the tube’s strength, ductility, and stress-relieving properties.
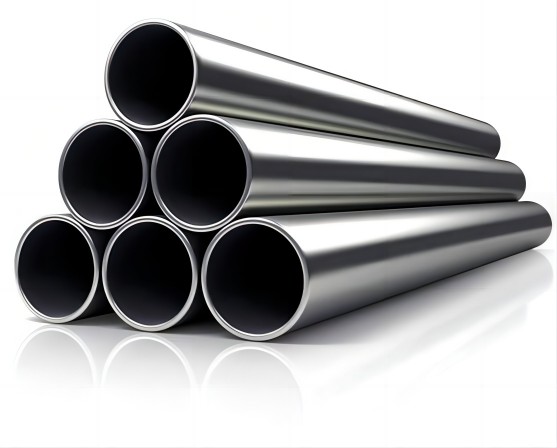
Factors Affecting the Cost of Drawn Aluminum Tubes
The cost of drawn aluminum tubes is a complex interplay of several factors, each contributing to the overall price of these high-quality tubes. Understanding these factors is crucial for manufacturers, distributors, and end-users alike, as it provides insights into the cost structure and helps make informed purchasing decisions.
- Raw Material Costs: The foundation of any manufacturing process is the raw material, and the cost of drawn aluminum tubes is significantly influenced by the price of aluminum alloys. Aluminum prices fluctuate based on market conditions, supply and demand dynamics, and global economic factors. Fluctuations in aluminum prices can have a direct impact on the cost of drawn aluminum tubes.
- Manufacturing Process Costs: The manufacturing process itself contributes a substantial portion to the overall cost of drawn aluminum tubes. The complexity of the drawing process, the number of dies required, the labor costs associated with operating the machinery, and the energy consumption all play a role in determining the manufacturing expenses. Manufacturers strive to optimize their processes to minimize costs while maintaining quality and efficiency.
- Quality Standards and Certifications: The pursuit of high-quality drawn aluminum tubes often involves adherence to stringent quality standards and certifications. These standards, such as ISO 9001, impose rigorous quality control procedures, extensive testing, and comprehensive documentation. While adhering to these standards increases production costs, it also enhances the value and credibility of the tubes, assuring customers of their consistent quality and reliability.
- Economy of Scale: The volume of production plays a significant role in determining the cost per unit of drawn aluminum tubes. As production volumes increase, manufacturers can spread out fixed costs over a larger number of units, leading to lower costs per tube. This concept of economy of scale is particularly relevant for large production runs and standardized tube sizes.
- Customer-Specific Requirements: In addition to the aforementioned factors, customer-specific requirements can also influence the cost of drawn aluminum tubes. Special dimensions, tolerances, surface finishes, or testing requirements may necessitate additional processing steps or specialized equipment, increasing the overall cost. Manufacturers work closely with customers to understand their specific needs and provide cost-effective solutions.
Selecting a Reliable Drawn Aluminum Tube Manufacturer
Choosing a reliable drawn aluminum tube manufacturer is crucial for ensuring quality, consistency, and timely delivery. Key considerations include:
- Experience and Expertise: Evaluate the manufacturer’s experience in producing drawn aluminum tubes, their knowledge of aluminum alloys, and their ability to meet specific requirements.
- Reputation and Customer Reviews: Assess the manufacturer’s reputation in the industry, their track record of customer satisfaction, and any available customer reviews or testimonials.
- Quality Assurance and Testing: Verify the manufacturer’s quality assurance procedures, in-house testing capabilities, and adherence to industry standards.
- Customer Service and Support: Evaluate the manufacturer’s communication responsiveness, willingness to address customer concerns, and technical support capabilities.
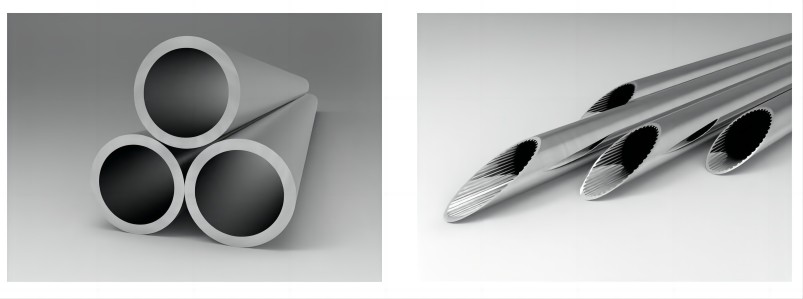
Summary
Drawn aluminum tubes offer a combination of superior strength, dimensional accuracy, and surface finish, making them suitable for various applications. The manufacturing process involves cold drawing through a series of dies, influenced by billet material, drawing parameters, mandrel characteristics, and heat treatment. The cost of drawn aluminum tubes is affected by raw material prices, manufacturing process complexity, and quality standards. Selecting a reliable manufacturer involves evaluating their experience, reputation, quality assurance, and customer service.