Aluminum has long been a favorite in various industries due to its lightweight, corrosion-resistant, and malleable nature. Among the many aluminum alloys available, the 5052 aluminum sheet stands out for its exceptional properties and a wide range of applications. In this article, we will delve into the world of 5052 aluminum sheet, exploring its characteristics, different states and hardness levels, chemical composition, mechanical properties, and the differences between the H32 and H34 states.
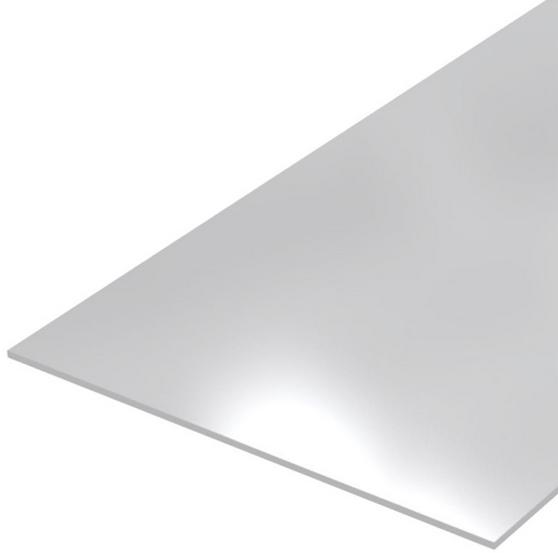
What is 5052 Aluminum Sheet?
5052 aluminum sheet is a popular choice when corrosion resistance and versatility are critical. It’s commonly used in applications spanning from ships and machinery to electronics, chemicals, construction, and decoration. Understanding the properties of the 5052 aluminum sheet is crucial to harness its full potential.
Common States and Hardnesses of 5052 Aluminum Sheet
The state of a 5052 aluminum sheet refers to the heat treatment it has undergone, which significantly influences its mechanical properties. The most common states for this alloy are O, H112, H32, and H34. Each state offers unique attributes suitable for specific applications:
- O State: In this state, the aluminum sheet is fully annealed. It is soft and easy to form but lacks the strength and hardness required for many industrial applications.
- H112 State: H112 is a state characterized by improved formability and corrosion resistance. It is used when some work hardening and additional strength are needed.
- H32 State: The H32 state is a partially annealed and strain-hardened condition, making it one of the most widely used states for 5052 aluminum sheet. It offers a good balance of strength and workability, making it suitable for a range of applications.
- H34 State: H34 is a state with higher hardness and better corrosion resistance compared to H32. It is ideal for applications where enhanced strength and resistance to harsh environmental conditions are essential.
The hardness of the 5052 aluminum sheet is indicated by the number following the H. A higher number signifies a harder sheet, and each hardness level is suited to specific requirements.
Chemical Composition and Mechanical Properties of 5052 Aluminum Sheets
Understanding the chemical composition and mechanical properties of the 5052 aluminum sheet is crucial in selecting the right material for a given application. The chemical composition of 5052 aluminum includes:
- Aluminum: Balance
- Silicon: ≤0.25%
- Copper: ≤0.10%
- Magnesium: 2.2-2.8%
- Zinc: ≤0.10%
- Manganese: ≤0.10%
- Chromium: 0.15-0.35%
- Iron: ≤0.40%
The high aluminum content, coupled with magnesium and chromium, provides the alloy’s corrosion-resistant properties. Silicon and copper are present in trace amounts to enhance the alloy’s workability and formability. The low levels of zinc and manganese contribute to its overall strength and resistance to stress.
The mechanical properties of the 5052 aluminum sheet are as follows:
- Tensile Strength: 170-305 MPa
- Yield Strength: ≥65 MPa
- Modulus of Elasticity: 69.3-70.7 GPa
These mechanical properties make 5052 aluminum an excellent choice for a wide range of applications, as it balances strength with formability.
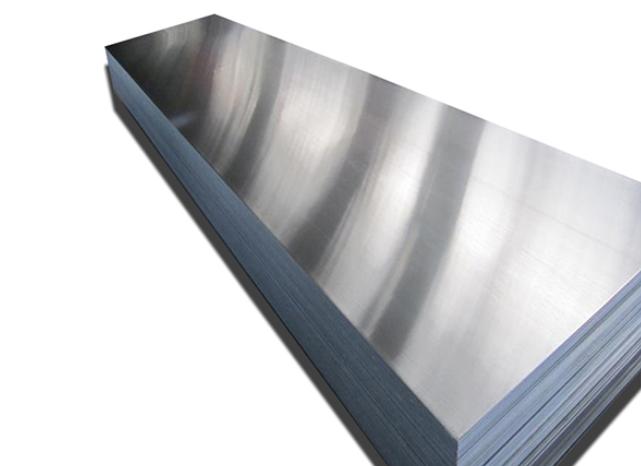
Comparison of 5052-H32 and 5052-H34
Understanding the differences between 5052-H32 and 5052-H34 is crucial, as it allows you to select the most suitable state for your specific needs.
Hardness
Hardness is a measure of a material’s resistance to indentation. 5052-H34 is harder than 5052-H32 because it has been strain-hardened to a greater extent. This means that it is more difficult to deform and less likely to dent or scratch.
Non-Proportional Elongation
Non-proportional elongation is a measure of a material’s ability to withstand plastic deformation without necking. 5052-H34 has a higher non-proportional elongation than 5052-H32, which means that it can be deformed more before it fails. This makes it a good choice for applications where the material will be subjected to high levels of stress.
Bending Radius
The bending radius is the minimum radius around which a material can be bent without cracking. 5052-H34 has a larger bending radius than 5052-H32, which means that it can be bent more tightly without cracking. This makes it a good choice for applications where the material will be subjected to complex bending operations.
The following table summarizes the key differences between 5052-H32 and 5052-H34 aluminum sheet:
Property | 5052-H32 | 5052-H34 |
Hardness | Half hard | Three-quarter hard |
Non-proportional elongation | ≥130 MPa | ≥150 MPa |
Bending radius | 1.5t | 2.0t |
Applications of 5052-H32 and 5052-h34 Aluminum Sheets
H32 5052 aluminum sheet is commonly used for applications where good formability and machinability are required, such as aircraft skins, automotive parts, and electronic enclosures. H34 5052 aluminum sheet is commonly used for applications where higher strength and hardness are required, such as structural components, machine parts, and aerospace components.
The choice between H32 and H34 ultimately depends on the specific requirements of your project. Consider factors like load-bearing capacity, desired formability, and resistance to deformation when making your decision.
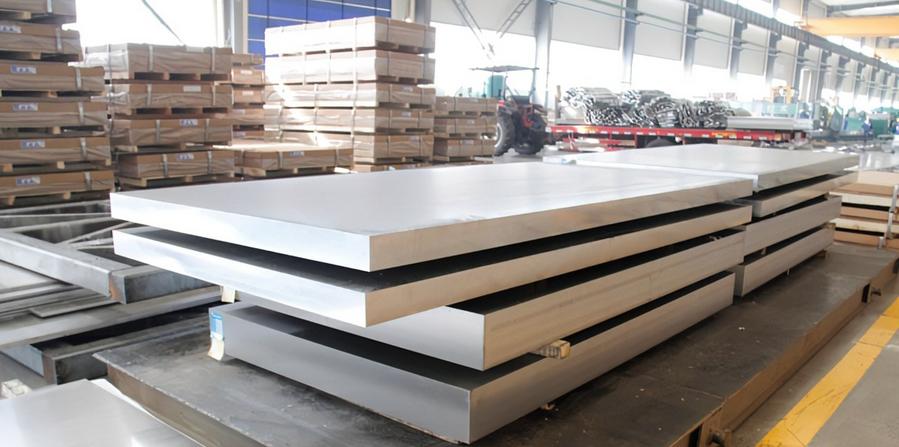
Conclusion
In conclusion, 5052 aluminum sheet is a versatile material with a wide range of applications. It offers an excellent balance between formability and strength, making it suitable for various industries. Whether you need a sheet for marine applications, machinery, electronics, construction, or decoration, understanding the different states and hardness levels of 5052 aluminum is crucial. By carefully considering your project’s specific requirements, you can harness the full potential of this remarkable aluminum alloy.