Metal stamping is a metalworking process that forms various parts and products from sheet metal. It accommodates a wide range of materials, including aluminum, stainless steel, low-carbon steel, copper and brass.
Aluminum is highly suitable for stamping operations due to its strength and workability. Stamped aluminum components find application in nearly every industry, including aerospace, automotive, electronics, marine, medical, and more. Below we provide an overview of the aluminum stamping process, including typical metal stamping materials employed and the properties they exhibit.
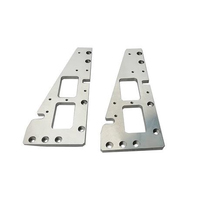
Definition of stamping process
The stamping process is a metal processing method, which is based on the plastic deformation of the metal, using the mold and stamping equipment to exert pressure on the sheet, so that the sheet is plastically deformed or separated, to obtain a product with a certain shape, size, and performance. parts (stampings).
The stamping forming process occupies an important position in the automobile body manufacturing process, especially the large-scale covering parts of the automobile body, because most of them have complex shapes, and large structural dimensions and some are spatial curved surfaces, and the surface quality requirements are high, so stamping processing methods are used. Making these parts is unmatched by other processing methods. The cab of the truck, the front sheet metal parts, the cargo panel, the various body panels of the car, and the various skeletons of the bus are almost all made by stamping.
Materials for metal stamping processes
The most common metals used in metal stamping include aluminum, stainless steel, mild steel, copper, and brass.
1. Aluminum
Aluminum is a non-ferrous metal that is relatively inexpensive and has an excellent strength-to-weight ratio, making parts durable, strong, and lightweight. Another advantage of using aluminum in metal stamping is that it is corrosion-resistant and non-toxic. It also has the added benefit of not requiring coating during finishing, although it can be anodized to enhance its appearance and increase its corrosion resistance. Aluminum’s lightweight strength is critical to the automotive and aerospace industries, where eliminating excess weight improves fuel economy.
2. Stainless steel
Stainless steel is a ferrous metal that contains large amounts of chromium, molybdenum, and nickel. Stainless steel offers ideal properties for metal stamping, including corrosion resistance, non-magnetic, very good wear resistance, no need for plating, and heat treatable.
Stainless steel is often the material of choice for metal stampings when used in the aerospace and defense, lawn and garden sealing equipment, and piping and valve industries.
3. Low-carbon steel
There are two types of low-carbon steel materials, flat and coiled. Mild steel offers several benefits for metal stamping, including being a low-cost, high-strength material. It can be used to manufacture multiple parts at a lower unit price. Mild steel is an extremely durable metal commonly used in sealing technology, automotive, and lawn, and garden applications.
4. Copper and brass
Copper is easy to form, making it ideal for rapid production of one-piece, seamless components, and compatible with the cold forming process, which hardens the metal. Copper is a low-maintenance durable metal that resists corrosion and has natural hygienic properties for use in the medical, food, and beverage industries.
Brass is a copper-zinc alloy that retains many of the beneficial properties of copper. Brass has a smooth surface, resists corrosion, and provides electrical conductivity, making it suitable for a wide range of electronic applications.
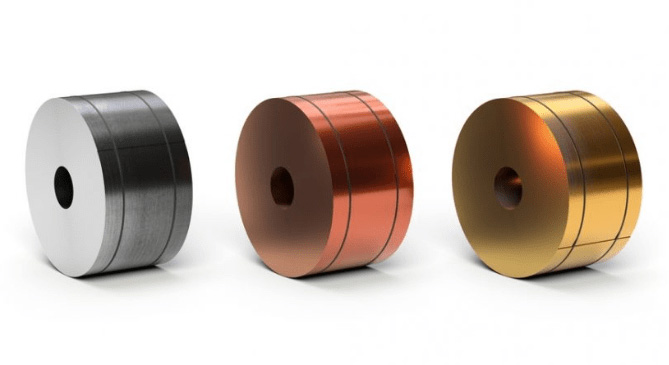
Aluminum alloys commonly used in metal stamping operations
For stamping operations, pure aluminum is often alloyed with other metals to add or enhance certain material properties to improve the performance of the end product. Typical alloying materials include copper, iron, magnesium, manganese, silicon, and zinc. Each alloy is assigned a unique four-digit number, the first digit of which is determined by the primary alloying element. For example:
- 1xxx aluminum is used for 99% pure aluminum with no alloying element.
- 2xxx aluminum is used for aluminum alloyed with copper.
- 3xxx aluminum is used for aluminum alloyed with manganese.
- 4xxx aluminum is used for aluminum alloyed with silicon.
- 5xxx aluminum is used for aluminum alloyed with magnesium.
- 6xxx aluminum is used for aluminum alloyed with magnesium and silicon.
- 7xxx aluminum is used for aluminum alloyed with zinc.
- 8xxx aluminum is used for aluminum alloyed with other elements.
The four-digit number may also include a letter tagged on end. This letter is indicative of the alloy’s temper designation. For example, fabricated is represented by F, annealed is denoted by O, strain hardened is represented by H, solution heat-treated is represented by W, and heat treated (not applicable to F, O, or H designations) is represented by T.
Some of the most commonly used aluminum alloys in metal stamping operations are:
- 1100: This commercially pure aluminum exhibits high ductility, material softness, and workability. It is ideal for forming operations involving intricate parts or product designs, such as flatware or decorative components.
- 3003: This aluminum-manganese alloy has greater strength than aluminum 1100. It also demonstrates good corrosion resistance and workability. Some of its typical applications include cooking instruments, kitchen equipment, and chemical handling products.
- 5052: This aluminum-magnesium alloy has higher strength than any of the other common non-heat-treatable variations. It also offers better fatigue strength, high corrosion resistance, and good workability and finishing characteristics. Typical use cases include aircraft parts, home appliances, and heavy-duty cooking implements.
- 6061: This aluminum alloy is heat treatable. It is highly versatile due to its numerous advantageous mechanical and chemical properties, including corrosion resistance, formability, and weldability. It is widely used for making structural parts such as the bodies and frames of automobiles.
Common characteristics of aluminum alloys
As mentioned above, aluminum alloys may exhibit different properties depending on the exact composition. However, there are some shared properties between material groups, including:
- high strength to weight ratio
- Flexibility and Extensibility
- electrical and thermal conductivity
- Corrosion resistance
- Low temperature resistance
- Smooth, shiny finish that requires little maintenance