Aluminum is a versatile material widely used in various industries for its lightweight, corrosion resistance, and excellent formability. When it comes to selecting the right aluminum alloy for a particular application, one often faces the choice between 3003 aluminum and 6061 aluminum. Each alloy possesses distinct properties and characteristics that make it suitable for different purposes. In this article, we’ll delve into the comparison of 3003 aluminum vs. 6061 aluminum to help you make an informed decision.
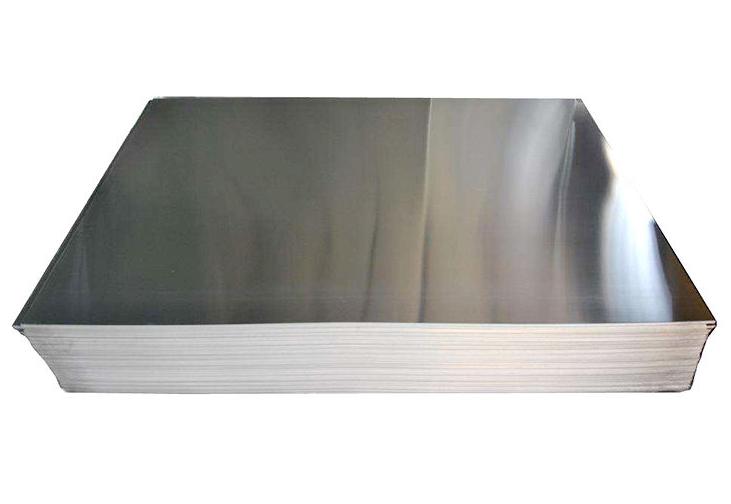
6 Key Differences Between 3003 and 6061 Aluminum
3003 aluminum and 6061 aluminum are two different alloy grades with distinct properties and applications. Here are some key differences between them:
1. Alloy Composition of 3003 vs. 6061
- 3003 Aluminum: It is a non-heat-treatable alloy primarily composed of aluminum (approximately 98.6%) and manganese (about 1.2%). It also contains small amounts of other elements like copper and iron.
- 6061 Aluminum: This is a heat-treatable alloy composed mainly of aluminum (about 97.9%), with significant amounts of magnesium (around 1%), silicon (around 0.6%), and small traces of copper, chromium, and other elements.
2. Strength and Hardness of 3003 vs. 6061
- 3003 Aluminum: It is a relatively soft alloy with low tensile strength and low hardness. It is often used for applications that do not require high strength.
- 6061 Aluminum: 6061 is known for its high strength and hardness, making it suitable for a wide range of structural and load-bearing applications.
3. Heat Treatment of 3003 vs. 6061
- 3003 Aluminum: It is a non-heat-treatable alloy, which means its mechanical properties cannot be significantly improved through heat treatment processes.
- 6061 Aluminum: 6061 can be heat-treated to increase its strength and hardness. It can be aged to achieve various levels of temper, including T6, T651, and others, which provide different combinations of strength and ductility.
4. Weldability of 3003 vs. 6061
- 3003 Aluminum: It has good weldability and is commonly used in applications where welding is required.
- 6061 Aluminum: While 6061 can be welded, it is not as easily weldable as 3003 due to its higher magnesium content. Special care and welding techniques may be needed to avoid cracking.
5. Corrosion Resistance of 3003 vs. 6061
- 3003 Aluminum: It has good resistance to corrosion, especially in mildly corrosive environments.
- 6061 Aluminum: 6061 offers reasonable corrosion resistance but may not be as corrosion-resistant as 3003 in some conditions.
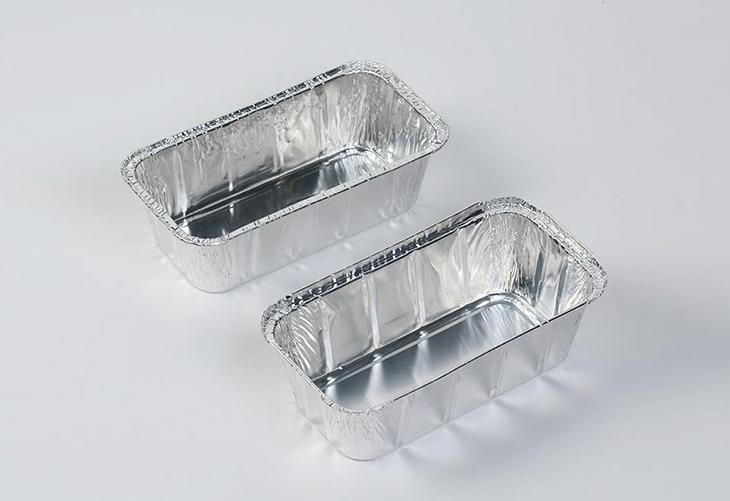
6. Common Applications of 3003 vs. 6061
- 3003 Aluminum: It is often used for applications such as cooking utensils, food packaging, heat exchangers, and general sheet metal work.
- 6061 Aluminum: 6061 is commonly used in aerospace components, automotive parts, structural components, bike frames, marine applications, and other high-stress applications.
In summary, 3003 aluminum is a softer, non-heat-treatable alloy with good corrosion resistance, while 6061 aluminum is a heat-treatable alloy with higher strength and hardness, suitable for more demanding structural and load-bearing applications.
How to Choose the Right 3003 aluminum and 6061?
The decision between 3003 aluminum and 6061 aluminum ultimately hinges on the specific requirements of your project or application. Here are some key considerations to guide your choice:
- Strength Requirement: If your application demands high strength and hardness, 6061 aluminum is the better choice. It’s particularly suitable for load-bearing and structural components.
- Formability: On the other hand, if formability and ease of fabrication are your top priorities, 3003 aluminum’s exceptional formability makes it a preferred option.
- Corrosion Resistance: Consider the environmental conditions your aluminum parts will face. If exposure to moisture and corrosion is a concern, 3003’s corrosion resistance may be advantageous.
- Welding Needs: If welding is a critical aspect of your project, both alloys can be welded, but 3003 may offer easier weldability.
- Cost: 3003 aluminum is generally less expensive than 6061, so budget considerations may also influence your decision.
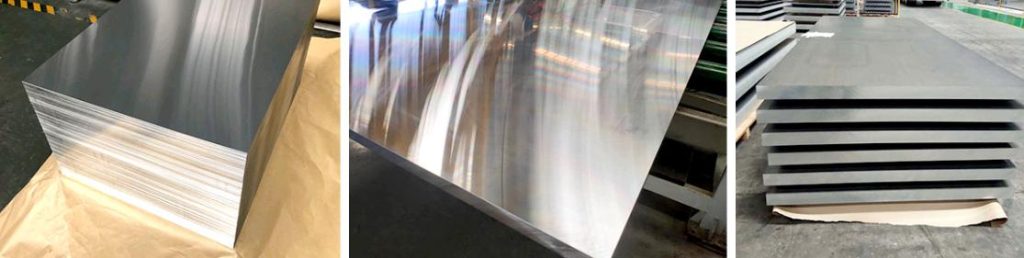
Conclusion
In conclusion, the choice between 3003 aluminum and 6061 aluminum comes down to your specific project requirements. Both alloys have their own set of advantages and limitations, so carefully assess your needs and consult with experts if necessary. By considering factors like strength, formability, corrosion resistance, and welding requirements, you can select the aluminum alloy that best suits your application, ensuring a successful and efficient outcome.