Aluminum foil, that silvery, shimmering shield we encounter daily, isn’t just a convenient way to keep leftovers fresh. Its malleable form and remarkable barrier properties have earned it a starring role in two distinctly different worlds: food and pharmaceutical packaging. While both rely on this versatile material, the specific requirements and nuances behind each type of aluminum foil packaging are as diverse as the products they protect. Let’s embark on a journey to unveil the hidden differences between these two champions of packaging.
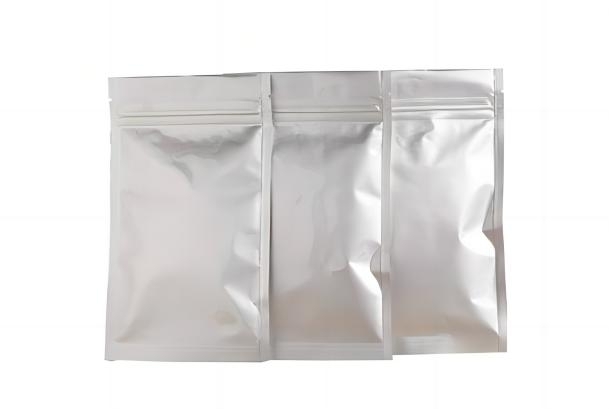
Composition and Purity: A Matter of Degrees
At the heart of these disparities lies the very essence of the foil itself – its composition and purity. Aluminum foil for food packaging, generally less stringent in its requirements, allows for trace amounts of other metals within safe limits. These alloys enhance specific qualities, like increased strength or heat resistance, crucial for grilling foil or oven-friendly trays.
On the other hand, aluminum foil for pharmaceutical packaging demands a different level of dedication. Imagine delicate tablets entrusted to their foil shield. Here, purity reigns supreme. Pharmaceutical-grade foil boasts a staggering 99.5% or higher aluminum content, meticulously crafted to minimize the risk of even trace metal leaching into medications. This rigorous purity standard safeguards patient health and ensures the integrity of sensitive drugs.
Thickness: A Tale of Two Tins
Picture a hefty burger wrapped in its foil armor compared to a slender blister containing a single pill. These contrasting images perfectly illustrate the difference in thicknesses between food and pharmaceutical foils. Food applications often embrace sturdier foils, like the ones used for heavy-duty grilling, designed to withstand direct heat and mechanical stress.
In stark contrast, pharmaceutical aluminum foil adopts a delicate persona. Thin and precise, it seamlessly molds into blister packs, preserving medication potency and ensuring tamper-evident seals. This slim profile doesn’t compromise quality; pharmaceutical foils leverage advanced laminates and coatings to compensate for their reduced thickness, maintaining their essential barrier properties.
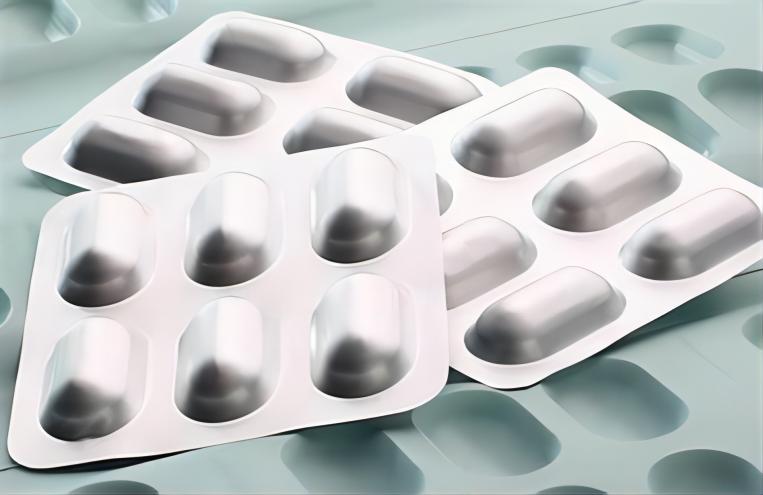
Migration and Leaching: When Every Atom Counts
Food and pharmaceuticals have vastly different concerns when it comes to the potential migration of aluminum. Imagine a tangy tomato sauce slowly dissolving the foil enclosing it. For food packaging, regulations focus on preventing aluminum migration exceeding safe limits, especially for acidic or salty foods. Coatings and treatments come into play here, acting as vigilant sentinels guarding against unwanted interactions.
However, the stakes elevate considerably in the realm of pharmaceutical aluminum foil packaging. Here, migration concerns become a matter of patient safety. Stringent regulations dictate rigorous testing and meticulous production processes to guarantee that even minute amounts of aluminum remain safely within the foil, never breaching the delicate boundaries of the enclosed medications.
Surface Treatments: Beyond the Shimmer
While both types of foils flaunt their silvery sheen, their surface treatments tell a different story. Food-grade foils may boast heat-sealing coatings for convenient closure or non-stick finishes for hassle-free cooking. These treatments enhance functionality and user experience.
Meanwhile, pharmaceutical aluminum foil dons a more intricate coat. Additional layers and laminates bolster its barrier properties, protecting medications from moisture, light, and oxygen degradation. Specialized coatings also enhance printability, allowing for clear identification and dosage instructions on the foil itself.
Sterilization: Ensuring Purity from Start to Finish
Imagine a world where the foil protecting your food harbors unseen contaminants. For food packaging, sterilization requirements vary depending on the application. However, for pharmaceutical aluminum foil, the equation is non-negotiable. Every roll, every sheet, undergoes rigorous sterilization processes to eradicate any potential microbes or contamination, ensuring the utmost purity and safeguarding patient health.
Regulations and Standards: A Web of Safety
Both food and pharmaceutical packaging navigate a complex web of regulations and standards designed to ensure consumer safety and product integrity. However, the stakes and intricacies escalate for aluminum foil for pharmaceutical packaging. Stringent regulations like the Current Good Manufacturing Practices (cGMP) dictate every aspect of production, from raw material sourcing to sterilization and packaging. These protocols leave no room for compromise, ensuring the highest levels of quality and safety for every blister pack and medication seal.
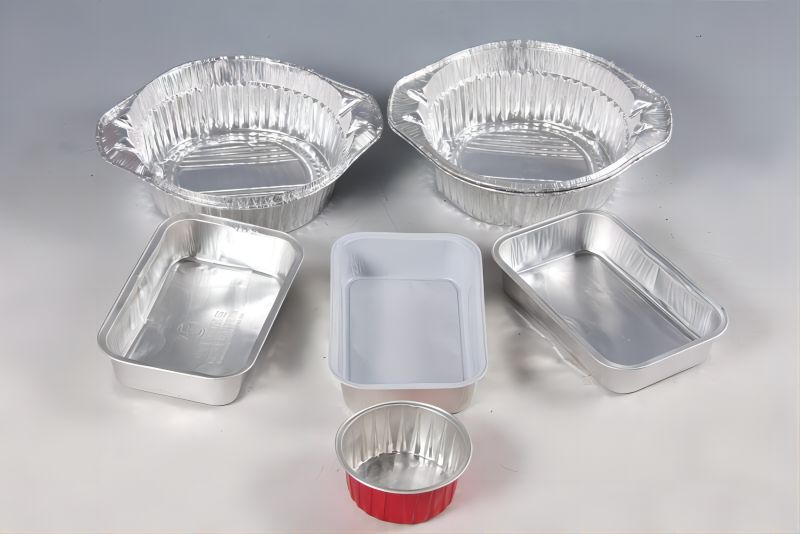
Conclusion: Foil Fit for Purpose
Choosing the right aluminum foil for the job is not just a matter of convenience, it’s a critical decision with implications for health, safety, and product quality. Understanding the key differences between food-grade and pharmaceutical-grade aluminum foil packaging – in terms of composition, thickness, migration, surface treatments, and sterilization – empowers us to make informed choices. Ultimately, aluminum foil, in its diverse forms, serves as a silent guardian, ensuring the freshness and safety of our food and the purity and efficacy of our medications. It’s a testament to human ingenuity, demonstrating how a simple material can play a vital role in protecting what matters most.