Within the realm of aluminum, specific alloys are designated as “marine grade” to ensure optimal performance in harsh aquatic conditions. These alloys are formulated with specific elements to enhance their corrosion resistance in saltwater. This article delves into two prevalent marine grade aluminum plates: 5052 and 5083. We’ll explore their key properties and how they differ to guide boat builders in selecting the most suitable material for their specific applications.
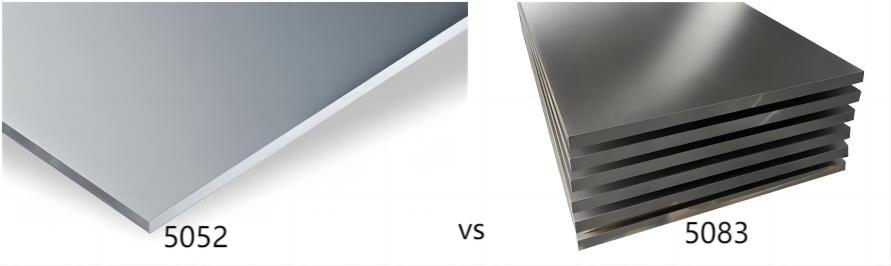
What is Marine Grade Aluminum?
Marine grade aluminum refers to specific aluminum alloys formulated for exceptional performance in saltwater environments. These alloys belong primarily to the 5XXX series, identified by the presence of magnesium as a key ingredient.
Here’s a breakdown of how magnesium contributes to marine grade aluminum’s properties:
- Enhanced Corrosion Resistance: Magnesium reacts with aluminum to form a thin, invisible layer of magnesium oxide on the surface. This layer acts as a barrier, significantly reducing the rate at which saltwater corrodes the aluminum. The higher the magnesium content in the alloy, the thicker and more effective this protective layer becomes.
- Trade-off Between Properties: While magnesium improves corrosion resistance, it does affect other properties. Increasing the magnesium content strengthens the aluminum, but it also makes it less workable and bendable. This creates a trade-off: more corrosion resistance comes at the expense of formability.
In essence, marine grade aluminum alloys are specifically designed to prioritize corrosion resistance in saltwater environments. However, there’s a balance to be struck between this crucial property, strength, and the ease with which the material can be shaped.
Properties of 5052 Aluminum Plate
5052 aluminum plate is a popular choice for applications where formability is paramount. Due to its lower magnesium content (around 2.8% compared to other marine grade alloys), it exhibits excellent bending and shaping characteristics. This makes it ideal for non-structural components like decks, superstructures, and other areas requiring curved shapes. Additionally, 5052 offers decent corrosion resistance, making it suitable for freshwater environments or saltwater applications with limited exposure.
Here’s a breakdown of the key properties of 5052 aluminum plate:
- Excellent Formability: Due to its lower magnesium content, 5052 is highly workable and can be easily bent and shaped without cracking. This makes it a preferred choice for fabricating curved components and intricate shapes.
- Moderate Strength: Compared to other marine grade alloys, 5052 has a lower tensile strength. While sufficient for non-structural applications, it’s not ideal for high-stress areas.
- Decent Corrosion Resistance: The presence of magnesium provides a layer of protection against corrosion. However, 5052 offers less resistance compared to higher magnesium alloys like 5083.
Applications of 5052 Aluminum Plate in Boat Building
- Decks and Superstructures: Due to its excellent formability, 5052 is well-suited for constructing decks, cabin tops, and other non-structural elements requiring shaping.
- Hatches and Doors: The ability to bend and form 5052 makes it a good choice for fabricating hatches, access panels, and other movable components.
- Interior Components: 5052 can be used for non-structural interior elements like shelves, lockers, and decorative panels.
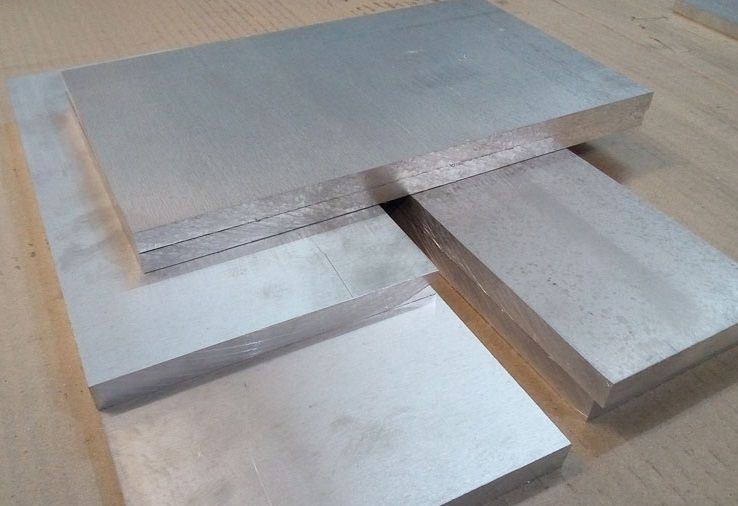
Properties of 5083 Aluminum Plate
5083 aluminum plate prioritizes strength and superior corrosion resistance. With a higher magnesium content (around 4.9%), it offers enhanced protection against saltwater corrosion, making it the preferred choice for applications directly exposed to seawater. Additionally, 5083 possesses higher strength compared to 5052, making it suitable for structural components.
Here’s a breakdown of the key properties of 5083 aluminum plate:
- High Strength and Hardness: The increased magnesium content contributes to greater strength and hardness compared to 5052. This makes 5083 ideal for structural components that need to withstand significant loads.
- Superior Corrosion Resistance: The higher magnesium content in 5083 translates to exceptional resistance against saltwater corrosion, making it the preferred choice for hulls, bulkheads, and other constantly submerged components.
- Reduced Formability: Due to its higher magnesium content, 5083 is less formable than 5052. Bending and shaping becomes more challenging, and it’s not recommended for applications requiring intricate curves.
Applications of 5083 Aluminum Plate in Boat Building
- Hulls and Bulkheads: The high strength and superior corrosion resistance of 5083 make it the primary choice for constructing boat hulls, bulkheads, and other structural components that experience significant stress and constant saltwater exposure.
- Stringers and Transoms: 5083’s strength makes it suitable for building stringers (longitudinal support beams) and transoms (the rearmost section of a boat) that require high load-bearing capacity.
- Masts and Booms (with limitations): While 5083 offers good strength, its reduced formability might limit its use for complex mast designs requiring intricate shaping. However, it can be a suitable choice for smaller masts or applications where straight sections dominate the design.
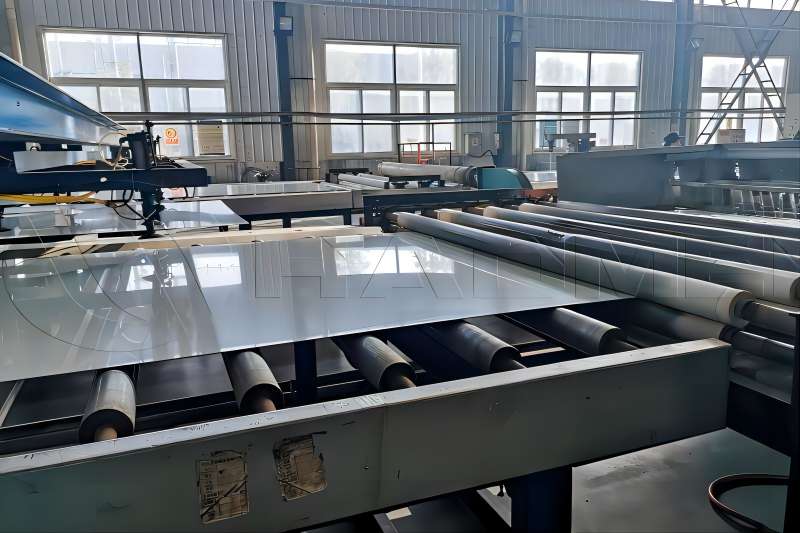
Choosing the Right Aluminum Plate: 5052 vs 5083
Selecting the appropriate aluminum plate hinges on understanding the specific application and its requirements. Here are some key factors to consider:
- Formability vs. Strength: If the primary concern is shaping and bending the material for curved components, 5052 is the clear choice due to its superior formability. However, if strength is crucial for structural components that need to withstand significant loads, 5083 is the better option.
- Saltwater vs. Freshwater Environment: For boats primarily used in freshwater environments with limited saltwater exposure, the decent corrosion resistance of 5052 might suffice. However, for saltwater applications where constant exposure is a concern, the superior corrosion resistance of 5083 becomes essential.
Additional Considerations
- Temper Designation: Both 5052 and 5083 come in various temper designations (e.g., H32, H34) that affect their strength and formability. The temper designation indicates the specific heat treatment process the material has undergone. H32 represents a work-hardened condition offering higher strength but reduced formability, while H34 signifies a solution-treated and naturally aged condition providing a balance between strength and formability. Consulting a qualified professional to determine the most suitable temper designation for your project is recommended.
- Cost: Generally, 5052 is slightly less expensive than 5083 due to its lower magnesium content. However, the cost difference might be negligible compared to the overall boat building budget.
As we’ve explored the properties of 5052 and 5083 aluminum plates in detail, it’s now easier to compare their key differences and understand which material might be more suitable for a specific boat building application. Here’s a table summarizing the critical aspects to consider when choosing between 5052 and 5083:
Feature | 5052 Aluminum Plate | 5083 Aluminum Plate |
Magnesium Content | Lower (around 2.8%) | Higher (around 4.9%) |
Formability | Excellent – Bends and shapes easily | Reduced – More challenging to bend and shape |
Strength | Moderate | High |
Corrosion Resistance | Decent – Suitable for freshwater or limited saltwater exposure | Superior – Excellent resistance to saltwater corrosion |
Applications (Boat Building) | Decks, superstructures, hatches, doors, interior components | Hulls, bulkheads, stringers, transoms (with limitations on complex designs) |
Cost | Slightly less expensive | Slightly more expensive |
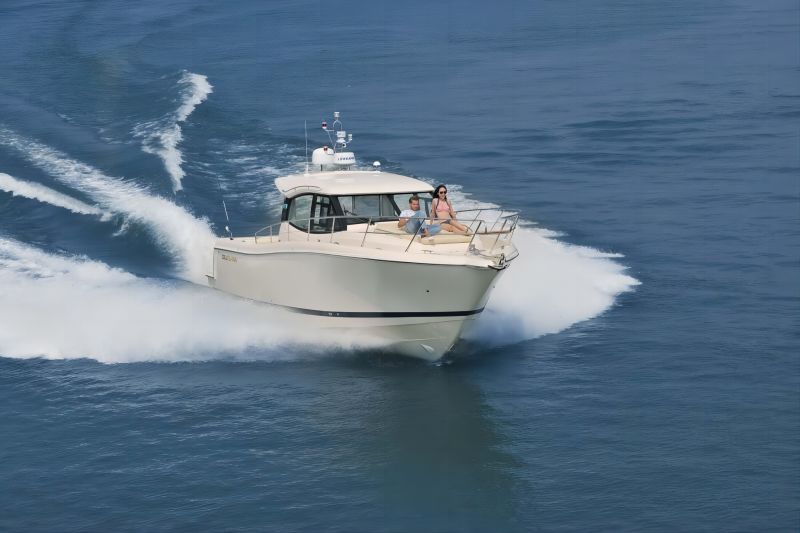
Conclusion
5052 and 5083 aluminum plates offer distinct advantages for boat building. By understanding their key properties – formability, strength, and corrosion resistance – boat builders can make informed decisions. 5052 shines in applications requiring easy shaping and decent corrosion resistance, while 5083 excels in structural components demanding high strength and superior saltwater protection. Ultimately, the right choice hinges on the specific needs of your boat and its intended use.