In the ever-evolving realm of electronic devices, engineers continually seek innovative materials to enhance performance, efficiency, and functionality. One such material gaining significant attention is thin aluminum foil. Its versatility and unique properties make it a valuable component in various electronic applications. This article delves into the applications of thin aluminum foil in electronic devices, exploring its properties, advantages, and impact on performance and efficiency.
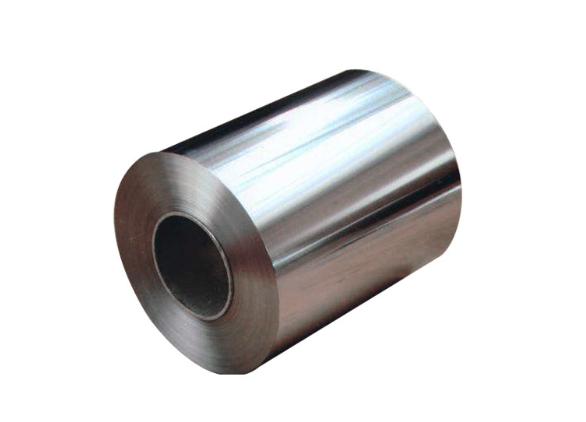
What is the Aluminum Foil in Electronics?
Aluminum foil, typically manufactured in thin sheets, is a lightweight metallic material composed primarily of aluminum. While commonly associated with food packaging and insulation, its application in electronics is becoming increasingly prevalent. Thin aluminum foil, often less than 0.2 millimeters in thickness, is used in electronic components, circuits, and packaging due to its exceptional conductivity, flexibility, and corrosion resistance.
In the realm of electronic devices, the utilization of thin aluminum foil presents a notable departure from traditional foil thicknesses. While conventional aluminum foil serves its purpose in numerous applications, the advent of thinner variants has introduced a new dimension to electronic engineering. Thin aluminum foil offers enhanced flexibility and adaptability, making it particularly well-suited for intricate electronic components and circuits. Moreover, its reduced thickness facilitates more precise control over electrical properties, contributing to improved performance and efficiency in electronic devices.
Advantages of Using Thin Aluminum Foil
The adoption of thin aluminum foil confers a multitude of advantages, underscoring its significance in modern technological advancements.
- High Conductivity: Aluminum boasts excellent electrical conductivity, second only to copper among commonly used metals. Its low resistance facilitates efficient transmission of electrical signals and currents within electronic devices.
- Flexibility: Thin aluminum foil can be easily manipulated and shaped to fit diverse electronic components and configurations, offering flexibility in design and manufacturing.
- Lightweight: Aluminum’s lightweight nature minimizes the overall weight of electronic devices, crucial for portable and handheld gadgets where weight is a determining factor.
- Corrosion Resistance: Aluminum foil is highly resistant to corrosion, ensuring the longevity and reliability of electronic components, even in harsh environmental conditions.
- Cost-Effectiveness: Aluminum foil is relatively inexpensive compared to other metals like copper, contributing to cost-effective manufacturing processes for electronic devices.
Collectively, these attributes position thin aluminum foil as a cornerstone material in the evolution of electronic devices, offering unparalleled versatility and performance.
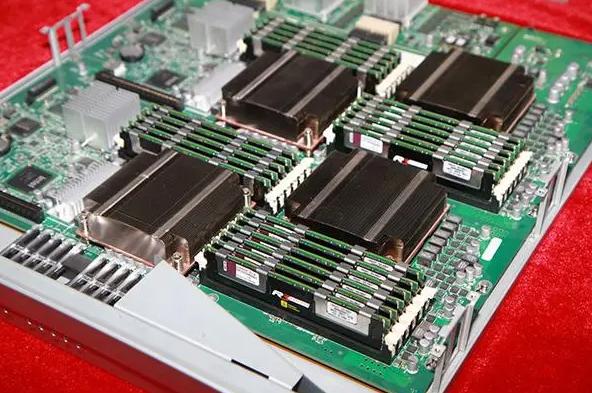
Impact on Electronic Device Performance and Efficiency
Thin aluminum foil can impact electronic device performance and efficiency in several ways:
- Electromagnetic Interference (EMI) Shielding: Thin aluminum foil can be used as an effective EMI shielding material. By wrapping or lining electronic devices with aluminum foil, electromagnetic interference from external sources can be minimized, leading to improved signal integrity and reduced electromagnetic pollution. This is particularly important in sensitive electronic equipment where EMI can disrupt operation or cause errors.
- Heat Dissipation: Aluminum foil can also serve as a heat sink or thermal conductor in electronic devices. When properly applied, it can help dissipate heat generated by components such as processors, graphics cards, and power regulators. Effective heat dissipation is crucial for maintaining optimal operating temperatures and preventing thermal throttling, which can degrade performance.
- Component Protection: Thin aluminum foil can be used to protect electronic components from environmental factors such as moisture, dust, and mechanical damage. By encapsulating or covering vulnerable parts of a device with foil, it can prevent corrosion, short circuits, and physical wear, thereby enhancing device reliability and longevity.
- Flexible Substrates: In flexible electronics applications, thin aluminum foil can serve as a substrate material for printed circuit boards (PCBs) or interconnects. Its flexibility allows for the creation of bendable and conformable electronic devices, which can be advantageous in wearable technology, flexible displays, and other portable applications. Flexible electronics enable innovative form factors and designs while maintaining performance and efficiency.
- Electrostatic Discharge (ESD) Protection: Aluminum foil can help mitigate the risk of electrostatic discharge damage to electronic components during handling and assembly. By grounding or shielding sensitive areas with foil, static charges can be safely dissipated, preventing potential damage to integrated circuits, memory modules, and other susceptible parts.
- Cost-Efficiency: Thin aluminum foil is relatively inexpensive compared to other materials used in electronic device manufacturing, such as copper. Its cost-effectiveness makes it an attractive option for various applications where performance and efficiency are paramount but budget constraints need to be considered.
Overall, thin aluminum foil can play a crucial role in enhancing electronic device performance and efficiency by providing EMI shielding, heat dissipation, component protection, flexible substrates, ESD protection, and cost-effective solutions for a wide range of applications.
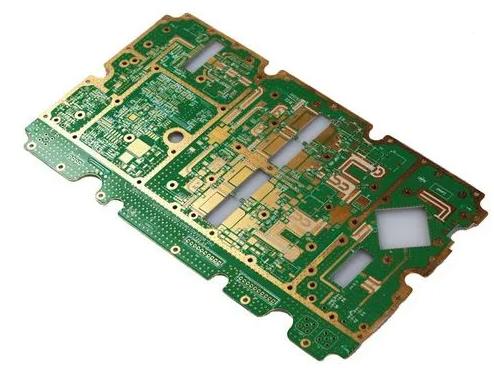
Conclusion
Thin aluminum foil plays a vital role in enhancing the performance, efficiency, and reliability of electronic devices. Its exceptional conductivity, flexibility, and corrosion resistance make it a preferred material in various applications, ranging from thermal management to EMI shielding and battery packaging. As technology continues to advance, the utilization of thin aluminum foil is expected to expand further, driving innovation and pushing the boundaries of electronic device design and functionality. By leveraging the unique properties of aluminum foil, engineers can continue to develop next-generation electronic devices that meet the demands of modern consumers and industries.