Seamless aluminum tubes are an important component in various industries, from aerospace and automotive to construction and manufacturing. These tubes are used for applications that require high strength-to-weight ratios, corrosion resistance, and excellent surface finish. There are different methods of producing seamless aluminum tubes, including extrusion, cold drawing, and rolling. In this article, we will compare and contrast these three types of seamless aluminum tubes.
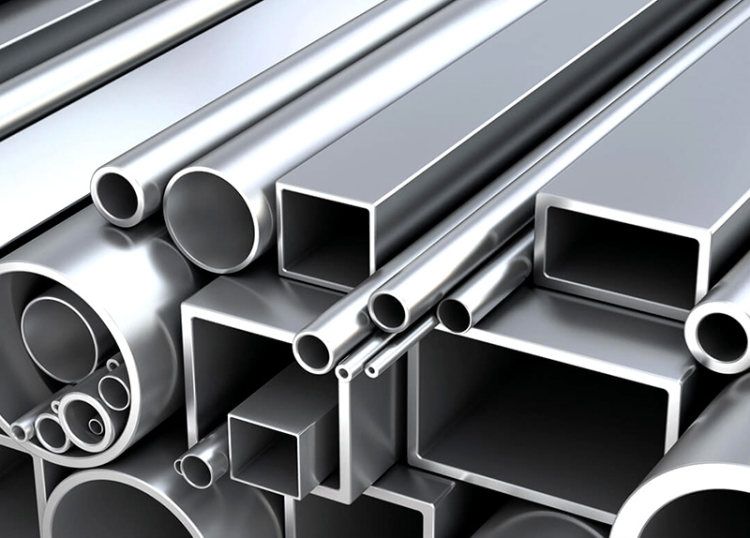
Type 1: Extruded Seamless Aluminum Tube
Extruded seamless aluminum tubes are produced by a process called extrusion, which involves pushing a heated aluminum billet through a die to create the desired shape. This method is ideal for producing long, uniform tubes with a consistent wall thickness. Extruded tubes have excellent dimensional accuracy, surface finish, and mechanical properties. The extrusion process ensures that the grain structure of the aluminum is aligned in the direction of the tube axis, which results in improved mechanical properties such as high strength and ductility.
Extruded tubes can be produced with a variety of alloys, including 6061, 6063, and 7075, among others. They are used in a wide range of applications, such as in the construction of aircraft frames, bicycle frames, and heat exchangers. Extruded tubes can be produced in a variety of shapes, such as round, square, rectangular, and hexagonal. They can also be produced with complex cross-sections, such as T-shapes and L-shapes.
Despite their many advantages, extruded tubes have some limitations. They are limited in terms of size and shape, and cannot be produced with very thin walls. Additionally, the extrusion process can create some residual stresses in the tube, which can affect the mechanical properties of the material.
Type 2: Cold Drawn Precision Seamless Aluminum Tube
Cold-drawn precision seamless aluminum tubes are produced by a process called cold drawing, which involves pulling a cold aluminum billet through a die to create the desired shape. This method is ideal for producing tubes with very thin walls and tight dimensional tolerances. The cold drawing process ensures that the tube has an excellent surface finish and dimensional accuracy. Additionally, the cold working process can increase the strength and hardness of the material, resulting in improved mechanical properties.
Cold-drawn tubes can be produced with a variety of alloys, such as 6061, 6063, and 7075, among others. They are used in a wide range of applications, such as in the manufacturing of precision parts, hydraulic cylinders, and instrumentation.
Cold-drawn tubes can be produced in a wide range of sizes and shapes, including round, square, and rectangular shapes. They can also be produced with a variety of cross-sections, such as oval, hexagonal, and custom shapes. The cold drawing process can also produce tubes with an excellent surface finish, which makes them ideal for applications where appearance is important.
However, cold-drawn tubes have some limitations. The cold working process can reduce the ductility of the material, which can lead to cracking or other defects. Additionally, the cold drawing process can create some residual stresses in the material, which can affect the mechanical properties of the tube.
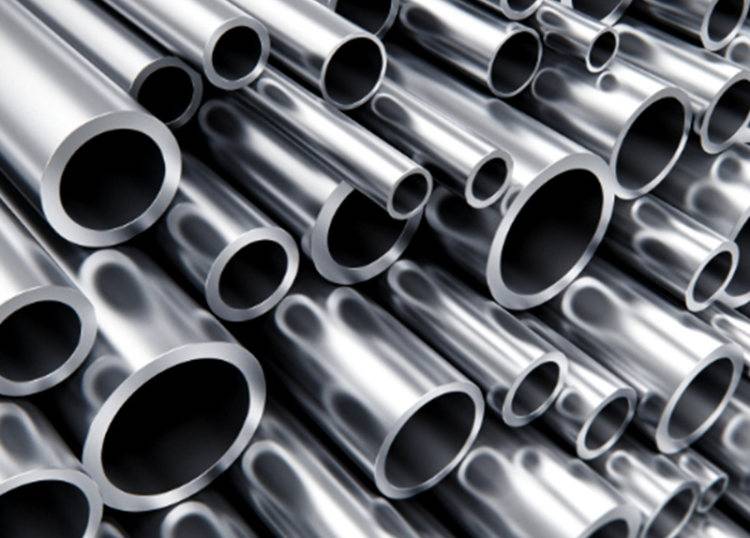
Type 3: Rolling Seamless Aluminum Tube
Rolling seamless aluminum tubes are produced by a process called rolling, which involves rolling a heated aluminum billet between two rollers to create the desired shape. This method is ideal for producing large-diameter tubes with a relatively thick wall. The rolling process can improve the mechanical properties of the material, resulting in a higher strength-to-weight ratio.
Rolling tubes can be produced with a variety of alloys, such as 6061, 6063, and 7075, among others. They are used in a wide range of applications, such as in the construction of large-scale structures, such as bridges and towers.
Rolling tubes can be produced in a wide range of sizes and shapes, including round, square, and rectangular shapes. However, the surface finish of rolling tubes may not be as good as extruded or cold-drawn tubes, and they may require additional finishing operations to achieve the desired surface finish. Additionally, the rolling process can create some residual stresses in the material, which can affect the mechanical properties of the tube.
One of the advantages of rolling seamless aluminum tubes is that it can produce large quantities of tubes quickly and at a relatively low cost. Rolling mills can produce tubes in continuous lengths, making them suitable for applications where long lengths of tubing are required, such as in the construction industry.
However, rolling seamless aluminum tubes have some limitations. They are not suitable for producing tubes with very thin walls or complex shapes. Additionally, the rolling process may not be suitable for producing tubes with high dimensional tolerances, which makes it unsuitable for precision applications.
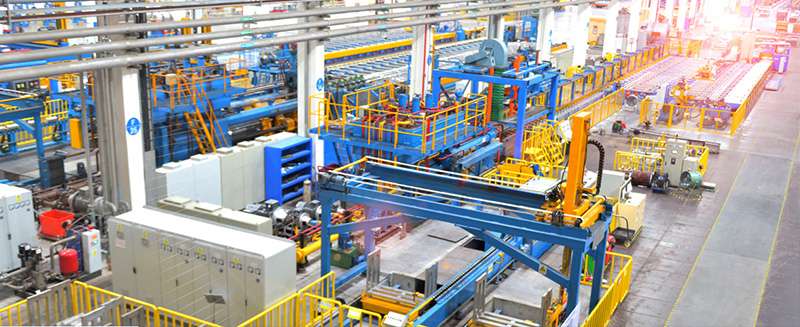
Conclusion
Choosing the right type of seamless aluminum tube depends on the specific requirements of the application. Extruded, cold-drawn, and rolling seamless aluminum tubes each have their strengths and weaknesses. By understanding the advantages and limitations of each type, it is possible to choose the most suitable seamless aluminum tube for a particular application. For example, if a high surface finish is required, extruded or cold-drawn tubes may be the best choice. If high mechanical properties are required, rolling tubes may be the best choice. Ultimately, the choice of the seamless aluminum tube will depend on the specific needs of the application.