In the realm of modern engineering and construction, aluminum stands as an indispensable material, offering a blend of lightweight, durability, and versatility. Among the myriad of aluminum alloys available, the 60 series, comprising alloys like 6060 and 6061, holds particular significance for structural applications. Engineers, architects, and manufacturers often face the dilemma of selecting between 6060 T5 and 6061 T6 aluminum alloys, both renowned for their exceptional properties and performance characteristics. Understanding the nuanced differences between these alloys is paramount for informed decision-making, as it directly impacts the integrity, longevity, and efficiency of diverse projects. This comparative analysis delves into the distinctive attributes, applications, and considerations associated with 6060 T5 and 6061 T6 aluminum alloys, providing valuable insights for professionals navigating the complex landscape of material selection in contemporary design and engineering endeavors.
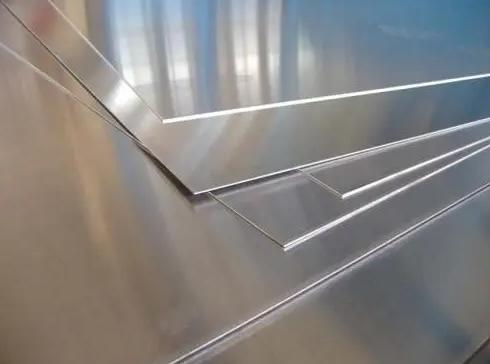
Why Choosing 60 Series Aluminum? 7 Reasons
Choosing 60 series aluminum, including alloys like 6060 and 6061, offers several advantages that make them popular choices across a range of industries and applications:
- Excellent Strength-to-Weight Ratio: 60 series aluminum alloys, including 6060 and 6061, offer exceptional strength while remaining lightweight. This makes them ideal for applications where weight reduction is crucial without compromising structural integrity.
- Versatility: 60 series aluminum alloys are highly versatile, offering a wide range of mechanical properties and characteristics that can be tailored to suit specific application requirements. They can be easily extruded, machined, welded, and formed into complex shapes, making them suitable for a variety of manufacturing processes.
- Corrosion Resistance: Aluminum alloys in the 60 series exhibit excellent corrosion resistance, especially when compared to other metals. This property makes them ideal for outdoor applications, structures exposed to harsh environments, and marine applications where corrosion protection is essential.
- Aesthetic Appeal: Aluminum alloys in the 60 series, particularly 6060, offer excellent surface finish and aesthetics. They can be anodized, painted, or coated to achieve desired colors and textures, making them popular choices for architectural elements, decorative fixtures, and consumer products.
- Environmental Sustainability: Aluminum is a highly sustainable material due to its recyclability and low environmental impact. Recycling aluminum requires significantly less energy compared to producing new aluminum from raw materials, making it an environmentally friendly choice for manufacturers and industries aiming to reduce their carbon footprint.
- Cost-Effectiveness: While aluminum alloys may have higher initial costs compared to some other materials, their long-term durability, low maintenance requirements, and recyclability contribute to overall cost-effectiveness throughout the product lifecycle.
- Wide Range of Applications: From automotive and aerospace components to architectural structures, consumer electronics, and packaging materials, 60 series aluminum alloys find applications across diverse industries due to their excellent properties and performance characteristics.
In summary, choosing 60 series aluminum offers numerous benefits including strength, versatility, corrosion resistance, aesthetic appeal, sustainability, and cost-effectiveness. These advantages make 60 series aluminum alloys preferred materials for a wide range of applications where lightweight, durable, and high-performance materials are required.
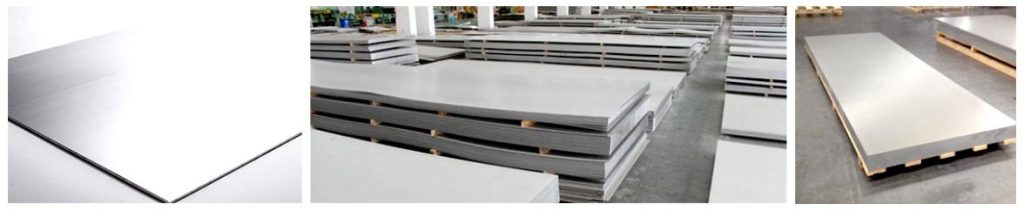
What is 60 Series Aluminum?
60 series aluminum alloys encompass compositions primarily composed of magnesium and silicon, contributing to their excellent formability and weldability. Alloys within this series, such as 6060 and 6061, are renowned for their excellent formability, weldability, and corrosion resistance, making them highly versatile for various engineering and construction applications.
6060 and 6061 aluminum alloy are characterized by their nominal composition of aluminum (Al), magnesium (Mg), and silicon (Si). 6060 Aluminum typically contains around 0.30-0.60% magnesium and 0.30-0.60% silicon, along with trace amounts of other elements such as iron (Fe) and copper (Cu). The magnesium-silicon combination enhances the alloy’s strength and corrosion resistance while maintaining good machinability and weldability. Compared to 6060, 6061 Aluminum contains slightly higher magnesium (0.8-1.2%) and silicon (0.4-0.8%) content, and with trace amounts of other elements like copper, chromium, and zinc, contributing to its superior strength and toughness.
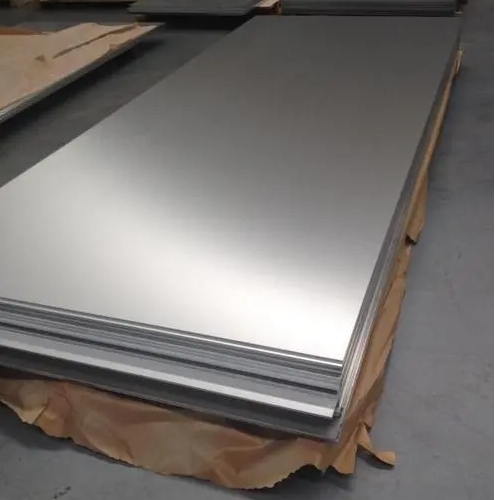
What is T5 and T6?
The designations T5 and T6 refer to the temper conditions applied to aluminum alloys, including those in the 60 series like 6060 and 6061. These temper conditions involve specific heat treatment processes designed to alter the mechanical properties of the aluminum, particularly its strength, hardness, and ductility.
Here’s the meaning of T5 and T6 in aluminum temper designations:
T5 Temper: In the T5 temper, aluminum undergoes an artificial aging process after being quenched. The aluminum is heated to a specific temperature range, typically around 160-180°C (320-356°F), and then held at that temperature for a certain duration. This aging process allows for the precipitation of fine particles within the aluminum matrix, enhancing its strength and hardness while maintaining good formability and toughness. T5 temper is known for providing a balance between strength and formability, making it suitable for a wide range of applications.
T6 Temper: The T6 temper involves a more rigorous heat treatment process compared to T5. After solution heat treatment, where the aluminum is heated to a high temperature to dissolve soluble phases, it is rapidly quenched to retain the supersaturated solid solution. Subsequently, the aluminum is artificially aged at a lower temperature, usually around 175°C (350°F), to precipitate the strengthening phases within the alloy. The T6 temper results in significantly higher strength and hardness compared to T5, making it suitable for applications requiring enhanced mechanical properties and structural integrity. However, T6 tempered aluminum may have slightly reduced formability compared to T5.
In summary, T5 and T6 represent specific temper conditions applied to aluminum alloys through controlled heat treatment processes. The choice between T5 and T6 depends on the specific requirements of the application and desired performance characteristics of the aluminum alloy, balancing factors such as strength, formability, and toughness.
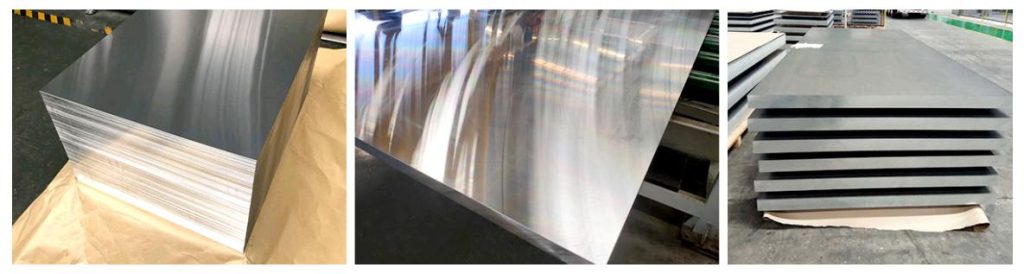
Differences of 6060 T5 vs. 6061 T6 Aluminum
6060 T5 and 6061 T6 aluminum alloys are both widely used in various industries due to their excellent properties and versatility. However, they differ in terms of mechanical properties, and applications. Here are the key differences between 6060 T5 and 6061 T6 aluminum:
Different Mechanical Properties:
The mechanical property differences between 6060 T5 and 6061 T6 aluminum alloys are significant and play a crucial role in determining their suitability for various applications. Here’s a comparison of the key mechanical properties:
1. Tensile Strength:
- 6060 T5: In the T5 temper, 6060 aluminum typically exhibits moderate tensile strength, ranging from 180 MPa to 210 MPa (26 ksi to 30 ksi). This level of strength is suitable for applications where structural integrity is important but not necessarily the primary consideration.
- 6061 T6: The T6 temper of 6061 aluminum provides significantly higher tensile strength compared to 6060 T5. It typically ranges from 270 MPa to 310 MPa (39 ksi to 45 ksi), making it ideal for structural applications where high strength and durability are paramount.
2. Yield Strength:
- 6060 T5: The yield strength of 6060 aluminum in the T5 temper ranges from 110 MPa to 160 MPa (16 ksi to 23 ksi). This indicates the stress at which the material begins to deform permanently.
- 6061 T6: In the T6 temper, 6061 aluminum offers higher yield strength compared to 6060 T5, typically ranging from 240 MPa to 280 MPa (35 ksi to 41 ksi). This higher yield strength makes 6061 T6 suitable for applications requiring superior load-bearing capabilities.
3. Elongation:
- 6060 T5: The elongation at break for 6060 aluminum in the T5 temper ranges from 8% to 10%. This indicates the material’s ability to deform before fracturing, reflecting its good ductility.
- 6061 T6: While 6061 T6 aluminum offers higher strength, its elongation at break is slightly lower compared to 6060 T5, typically ranging from 8% to 12%. Despite this, 6061 T6 still maintains reasonable ductility for many applications.
4. Hardness:
- 6060 T5: The hardness of 6060 aluminum in the T5 temper is relatively moderate, typically ranging from 60 to 75 Brinell hardness (HB).
- 6061 T6: In the T6 temper, 6061 aluminum exhibits significantly higher hardness compared to 6060 T5, typically ranging from 95 to 105 Brinell hardness (HB). This increased hardness contributes to its enhanced wear resistance and durability.
Here’s a comparison table outlining the mechanical property differences between 6060 T5 and 6061 T6 aluminum alloys:
Mechanical Property | 6060 T5 Aluminum | 6061 T6 Aluminum |
Tensile Strength (MPa) | 180 – 210 | 270 – 310 |
Tensile Strength (ksi) | 26 – 30 | 39 – 45 |
Yield Strength (MPa) | 110 – 160 | 240 – 280 |
Yield Strength (ksi) | 16 – 23 | 35 – 41 |
Elongation at Break (%) | 8 – 10 | 8 – 12 |
Brinell Hardness (HB) | 60 – 75 | 95 – 105 |
In summary, 6061 T6 aluminum offers superior mechanical properties, including higher tensile and yield strength, compared to 6060 T5 aluminum. While 6060 T5 may suffice for applications where moderate strength and good formability are sufficient, 6061 T6 is preferred for structural applications requiring exceptional strength, durability, and performance under high-stress conditions. The choice between the two alloys depends on the specific requirements of the application and the desired balance between mechanical properties and other factors such as formability and cost.
Different Applications
Here are examples of typical applications for 6060 T5 aluminum and 6061 T6 aluminum:
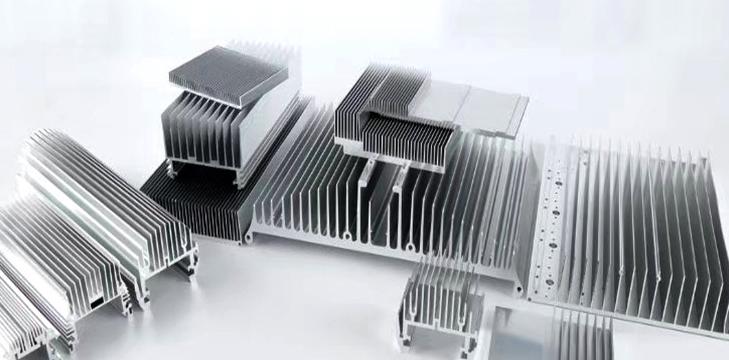
6060 T5 Aluminum:
- Architectural Components: 6060 T5 aluminum is commonly used for architectural components such as window frames, door frames, curtain walls, and handrails due to its excellent extrudability and surface finish.
- Decorative Fixtures: It is also utilized for decorative fixtures, lighting fixtures, furniture frames, and trim elements where aesthetics and intricate designs are important.
- Piping and Tubing: 6060 T5 aluminum tubing and piping find applications in various industries including construction, automotive, and marine for conveying fluids and gases due to its corrosion resistance and formability.
- Heat Sinks: This alloy is used for heat sinks in electronic devices and LED lighting systems to dissipate heat efficiently owing to its good thermal conductivity.
- Extruded Profiles: 6060 T5 aluminum is commonly extruded into a wide range of profiles and shapes for various industrial and commercial purposes, including signage, shelving systems, and frameworks.
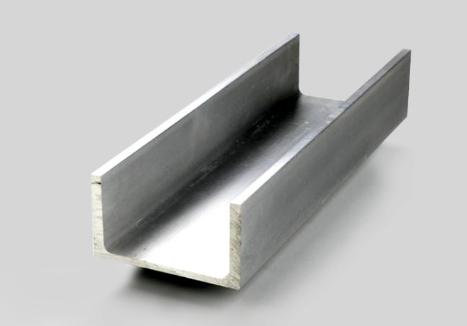
6061 T6 Aluminum:
- Aerospace Components: 6061 T6 aluminum is widely used in aerospace applications for aircraft structures, fuselage panels, wing skins, and structural components due to its high strength-to-weight ratio and excellent fatigue resistance.
- Automotive Parts: It is utilized for automotive components such as engine mounts, suspension components, wheels, and chassis parts due to its high strength, durability, and machinability.
- Bicycle Frames: 6061 T6 aluminum is a popular choice for bicycle frames and components due to its lightweight nature, stiffness, and ability to withstand the stresses encountered during cycling.
- Marine Hardware: It is used for marine hardware, boat fittings, and yacht components owing to its corrosion resistance and ability to withstand harsh marine environments.
- Structural Applications: 6061 T6 aluminum is widely employed in structural applications such as bridges, buildings, and trusses due to its exceptional strength, stiffness, and durability.
- Firearms Components: This alloy is also used in firearms manufacturing for parts such as receivers, handguards, and scopes due to its strength and machinability.
The choice between 6060 T5 and 6061 T6 depends on specific project requirements and desired material characteristics. For projects emphasizing intricate designs and aesthetic appeal, the 6060 T5 proves advantageous. Conversely, applications demanding robust structural integrity and high-performance capabilities lean towards 6061 T6. Understanding the strengths and weaknesses of each alloy enables informed decision-making, ensuring optimal performance and longevity in diverse applications.
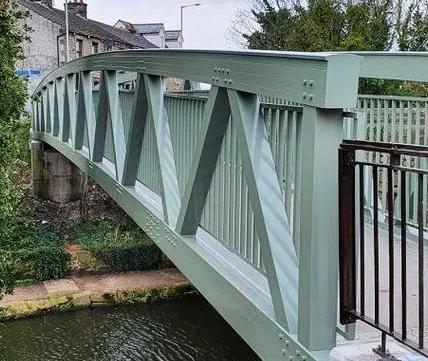
Conclusion:
In conclusion, the comparison between 6060 T5 and 6061 T6 aluminum alloys underscores the pivotal role of thoughtful material selection in achieving optimal performance and longevity across diverse applications. While both alloys exhibit commendable attributes such as strength, weldability, and corrosion resistance, their unique properties cater to specific requirements within the engineering spectrum. 6060 T5 aluminum excels in applications requiring superior extrudability, surface finish, and intricate designs, making it a preferred choice for architectural elements and decorative fixtures. Conversely, 6061 T6 aluminum stands out in high-stress environments, structural frameworks, and aerospace applications where strength and durability are paramount considerations.
As industries continue to evolve, the expertise and reliability of 6060 and 6061 aluminum suppliers become indispensable. These suppliers play a pivotal role in providing quality materials, technical support, and innovative solutions tailored to the evolving needs of engineers, architects, and manufacturers. By leveraging the insights gleaned from this comparative analysis, you can forge strategic partnerships with reputable 6060 and 6061 aluminum suppliers, ensuring seamless integration of superior materials into your projects.