Aluminum, a remarkably versatile material, finds extensive use across a wide spectrum of industries, from construction to electronics and automotive manufacturing. However, not all aluminum sheets are created equal. Two prominent manufacturing processes, cold rolling and hot rolling, yield aluminum sheets with distinct characteristics that cater to various applications. Understanding the differences between cold rolled and hot rolled aluminum sheets is essential for making informed decisions in material selection.
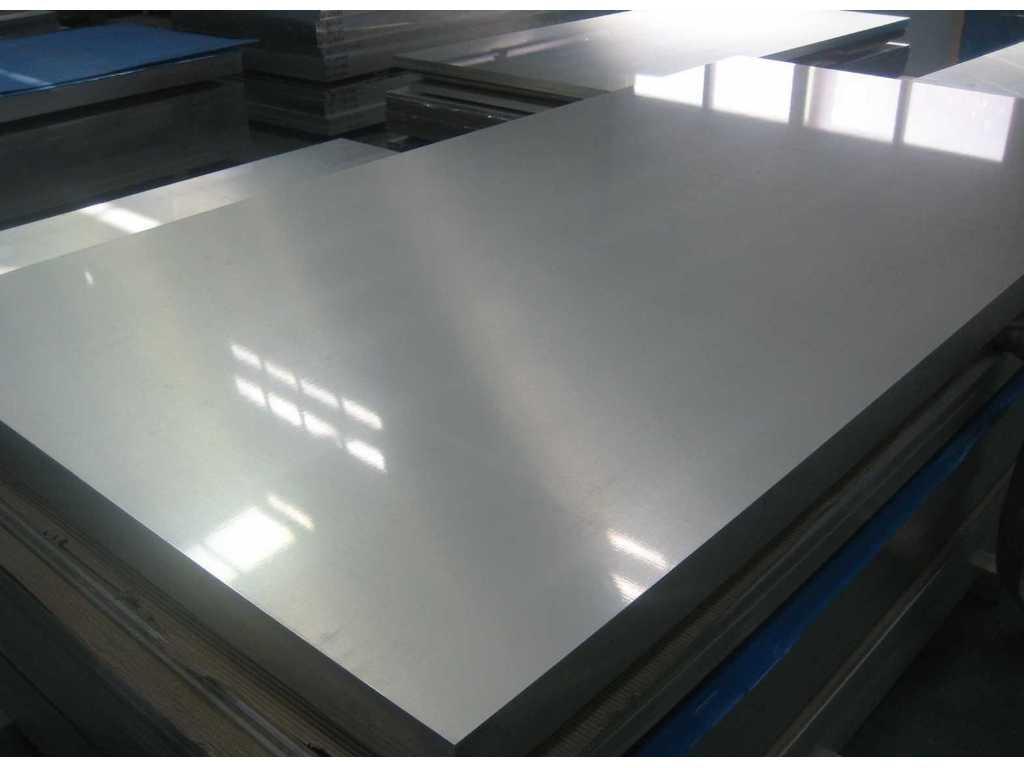
Cold Rolled Aluminum Sheet: Precision and Perfection
Cold rolling is a manufacturing process that involves reducing the thickness of aluminum sheets at room temperature. The process employs slow rolling speeds, resulting in an exceptionally smooth and uniform surface finish. This meticulous method is favored when precision is paramount.
Properties of cold rolled aluminum sheets include heightened hardness and strength. The gradual deformation of the metal at lower temperatures leads to greater mechanical properties. Moreover, the tight dimensional tolerances achieved through cold rolling ensure that the final product adheres closely to the specified measurements. These sheets are often characterized by their aesthetic appeal, making them an ideal choice for applications where appearance matters.
Industries that benefit from cold rolled aluminum sheets include electronics, machinery, and automotive manufacturing. The precise dimensions and smooth surfaces of these sheets make them suitable for intricate components in electronic devices and machinery. Additionally, they find use in automotive panels and body parts, contributing to both aesthetics and structural integrity. The combination of strength, precision, and visual appeal positions cold rolled aluminum sheets as a premium option for industries that demand excellence.
Hot Rolled Aluminum Sheet: Robustness and Adaptability
In contrast to cold rolling, hot rolling involves heating aluminum ingots above their recrystallization temperature before rolling them into sheets. The process is characterized by rapid rolling speeds, which can result in a rougher surface compared to cold rolling. Hot rolled aluminum sheets are recognized for their robustness and adaptability, making them a popular choice for a range of applications.
While hot rolled aluminum sheets exhibit reduced hardness and strength compared to their cold rolled counterparts, they possess certain advantages. Their larger dimensional tolerances make them suitable for applications where exact measurements are less critical. These sheets are often used in industries where mechanical properties and durability are prioritized over precision and aesthetics.
Industries such as construction, manufacturing, and heavy machinery benefit from hot rolled aluminum sheets. The sheets’ mechanical properties make them ideal for structural components that require strength and resilience. Large machinery parts also find application due to the sheets’ ability to withstand substantial mechanical stress. In scenarios where precise dimensions take a back seat to mechanical integrity, hot rolled aluminum sheets provide a reliable solution.
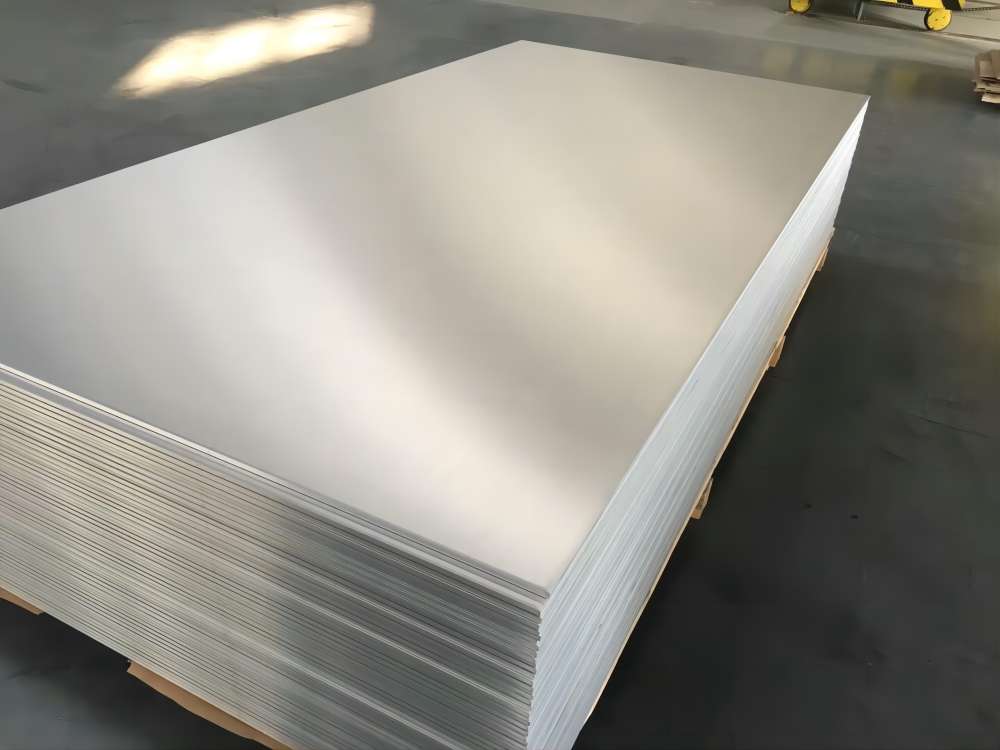
Comparing the Two Processing: Mechanical Properties, Surface Finish, and More
A comparative analysis of cold rolled and hot rolled aluminum sheets reveals crucial differences in various aspects. In terms of mechanical properties, cold rolled sheets tend to exhibit higher strength and hardness due to the controlled deformation process at lower temperatures. This makes them suitable for components requiring enhanced durability. On the other hand, hot rolled sheets may be less strong but compensate with increased ductility and formability, making them appropriate for applications that involve shaping or bending.
Surface finish plays a pivotal role in applications where appearance matters. Cold rolled sheets, with their smooth and uniform surfaces, are better suited for treatments like painting and coating. Hot rolled sheets, while potentially having a rougher surface due to faster rolling speeds, can still be suitable for applications where surface aesthetics are less critical.
Dimensional accuracy is another significant factor. Cold rolled sheets, with their tight tolerances, are preferred when components must fit precisely. Hot rolled sheets, with their larger tolerances, are often chosen when structural integrity is more crucial than exact measurements.
Factors Influencing Choice: Application, Production Volume, and More
Selecting between cold rolled and hot rolled aluminum sheets involves weighing several factors. The specific application requirements are perhaps the most critical. Industries that prioritize precision and aesthetics, such as electronics and automotive manufacturing, lean towards cold rolled sheets. Meanwhile, industries where mechanical strength and robustness are essential, such as construction and heavy machinery, favor hot rolled sheets.
Production volume is another key consideration. Cold rolling, with its slower process, might be better suited for smaller production runs where precision is paramount. Hot rolling’s quicker process makes it more suitable for larger-scale production.
Surface treatment plans also influence the choice. Cold rolled sheets, with their superior surface finish, are better candidates for applications that require subsequent treatments like painting or coating.
Finally, budget considerations play a role. Cold rolling involves more controlled and intricate processes, potentially leading to higher production costs. Hot rolling, with its simpler and faster approach, might offer cost advantages.
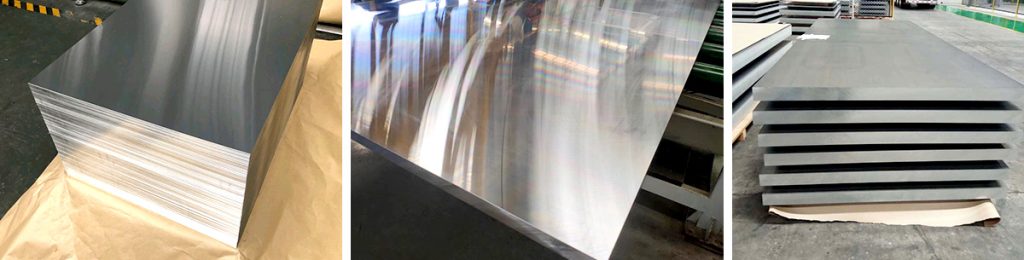
Conclusion
In the world of aluminum sheets, the choice between cold rolling and hot rolling is about achieving the right balance. Cold rolled aluminum sheets bring precision, strength, and a polished surface to industries that demand top-notch aesthetics and exact measurements. Hot rolled aluminum sheets, while sacrificing some precision, offer robustness and adaptability for industries that prioritize mechanical properties and structural integrity.
The key lies in understanding the demands of the application and making an informed decision based on the strengths of each process. As technology advances, refining these processes will continue to offer even more specialized solutions, enhancing the versatility of aluminum sheets across industries. Whether it’s sleek electronics or robust machinery, the choice between cold and hot rolling ensures that aluminum sheets remain a cornerstone of modern manufacturing.