Metal fabrication is a complex and intricate process that involves the manipulation of various metals to create structures, components, and products for a wide range of industries. Among the diverse materials used in metal fabrication, aluminum stands out for its versatility, lightweight nature, and corrosion resistance. Within the realm of aluminum processing, the use of strip coils has become a cornerstone in achieving precision and efficiency in metal fabrication.
What are Aluminum Strip Coils?
Aluminum strip coils are thin, flat pieces of aluminum that are wound into a coil shape. These coils serve as a foundational material in metal fabrication, providing a malleable and easily formable base for creating a myriad of products. The art of forming aluminum strip coils lies in the meticulous manipulation and shaping of this material to meet specific design requirements.
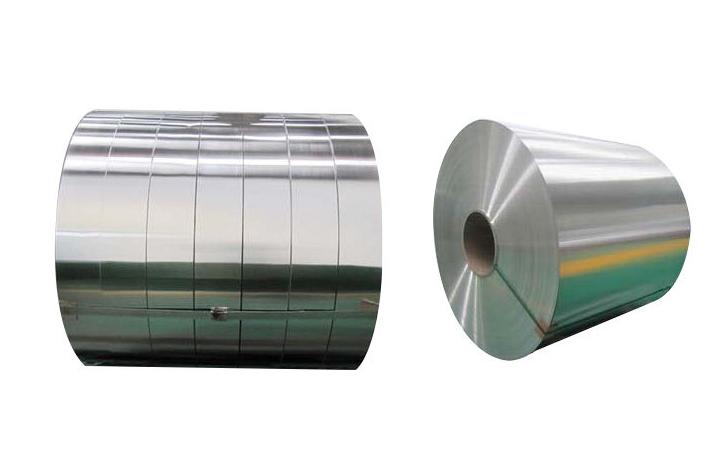
6 Advantages of Aluminum Strip Coils in Metal Fabrication
1. Versatility in Forming
One of the key advantages of aluminum strip coils is their adaptability to various forming processes. Metal fabricators employ techniques such as rolling, bending, stamping, and extruding to mold the coils into the desired shapes and dimensions. This versatility allows for the creation of intricate and complex components that are crucial in industries ranging from aerospace to automotive.
2. Precision in Dimension
Precision is paramount in metal fabrication, and aluminum strip coils play a crucial role in achieving exact dimensions. The uniform thickness and consistency of these coils contribute to the accuracy of the final product. Whether it’s the creation of structural components or intricate parts for electronic devices, the dimensional stability of aluminum strip coils is instrumental in meeting tight tolerances.
3. Lightweight Advantage
The lightweight nature of aluminum makes it an ideal material for applications where weight is a critical factor. Aluminum strip coils, being thin and light, contribute to the overall weight efficiency of the fabricated product. This is particularly significant in industries like transportation, where reducing weight can enhance fuel efficiency and overall performance.
4. Corrosion Resistance
Aluminum’s inherent resistance to corrosion makes it a preferred choice in applications where exposure to the elements is a concern. The use of aluminum strip coils ensures that the fabricated components maintain their structural integrity over time, even in challenging environmental conditions. This corrosion resistance extends the lifespan of the products and reduces the need for frequent maintenance.
5. Innovations in Aluminum Strip Coil Technology
As technology advances, so does the art of forming aluminum strip coils. Modern manufacturing processes leverage computer numerical control (CNC) machining, laser cutting, and other cutting-edge technologies to enhance precision and efficiency. These innovations empower metal fabricators to push the boundaries of design, creating products that were once deemed impossible.
6. Sustainability in Metal Fabrication
In the current era of heightened environmental awareness, the sustainability of materials used in manufacturing processes is a crucial consideration. Aluminum, being fully recyclable, aligns with the principles of sustainable production. The ability to recycle aluminum strip coils not only reduces the environmental impact but also contributes to the circular economy.
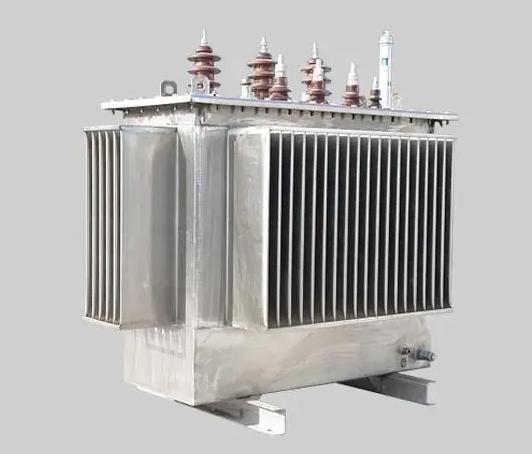
10 Applications of Aluminum Strip Coils in Metal Fabrication
Aluminum strip coils find a wide range of applications in metal fabrication due to the unique properties of aluminum, including its lightweight nature, corrosion resistance, and versatility. Here are some specific applications of aluminum strip coils in metal fabrication:
1. Automotive Industry:
Trim and Molding: Aluminum strip coils are used for creating decorative trim and molding in automobiles due to their lightweight nature and ability to withstand harsh weather conditions.
2. Construction and Architecture:
Weather Stripping: Aluminum strip coils are employed for weather stripping in doors and windows to provide a durable and corrosion-resistant barrier against the elements.
Roofing and Siding: Aluminum strips are used in roofing and siding applications due to their corrosion resistance and ability to withstand exposure to the elements.
3. Electrical Industry:
Transformer Windings: Aluminum strip coils are used in the production of transformer windings due to their excellent conductivity and lightweight properties.
4. Heat Exchangers:
Fins for Heat Exchangers: The malleability and thermal conductivity of aluminum make it suitable for creating fins in heat exchangers, contributing to efficient heat transfer.
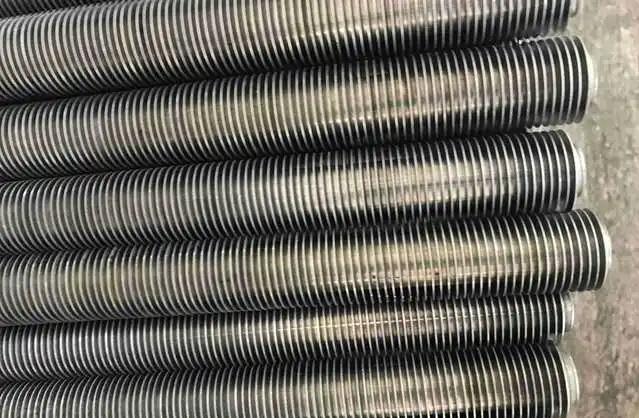
5. Consumer Electronics:
Electronic Enclosures: Aluminum strip coils are used for creating casings and enclosures for electronic devices due to their lightweight nature and ability to dissipate heat effectively.
6. HVAC Systems:
Ductwork and Components: Aluminum strips are employed in the fabrication of HVAC ductwork and components due to their corrosion resistance and light weight.
7. Appliance Manufacturing:
Appliance Trim and Panels: Aluminum strips find applications in the manufacturing of appliances for creating decorative trim and panels.
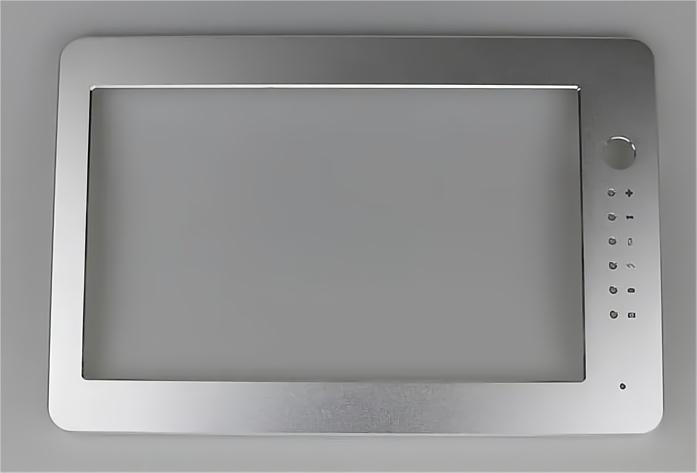
8. Signage and Displays:
Signs and Channel Letters: Aluminum strip coils are commonly used in the fabrication of signs and channel letters due to their versatility and ease of shaping.
9. Aerospace Industry:
Aircraft Components: Aluminum is widely used in the aerospace industry for fabricating various components, including structural parts and panels, due to its lightweight and high strength-to-weight ratio.
10. Marine Applications:
Boat Building: Aluminum strip coils are utilized in the fabrication of boat hulls and components due to their resistance to corrosion in marine environments.
The applications of aluminum strip coils in metal fabrication are diverse and continue to evolve as new technologies and fabrication methods emerge. The versatility and favorable properties of aluminum make it a popular choice in various industries for a wide range of applications.
Conclusion
The art of forming aluminum strip coils is a dynamic and integral aspect of metal fabrication. From the aerospace industry’s demand for lightweight components to the automotive sector’s need for precision-engineered parts, aluminum strip coils play a pivotal role in shaping the world around us. As technology continues to advance, the marriage of traditional craftsmanship with cutting-edge innovations ensures that the art of forming remains at the forefront of metal fabrication, driving progress and efficiency in various industries.