Aluminum jacket and aluminum cladding play a crucial role in optimizing the performance of pipe systems, particularly in the realm of thermal insulation. This article mainly delves into the various aspects of aluminum jackets, exploring their properties, benefits, types, installation processes, and applications across different industries. By understanding the significance of aluminum jackets in pipe systems, stakeholders can make informed decisions to improve efficiency and reduce energy consumption.

Properties of Aluminum Jackets
Aluminum, as a material for pipe insulation, boasts several key properties that contribute to its effectiveness. The low thermal conductivity of aluminum ensures that heat transfer is minimized, making it an excellent choice for thermal insulation. Additionally, its corrosion resistance and durability make it suitable for a wide range of environments, from industrial settings to chemical processing plants. The lightweight nature of aluminum further facilitates ease of installation and reduces the load on the pipe system.
Advantages of Aluminum Jacket for Pipe Insulation
1. Corrosion Resistance and Weatherability
Aluminum boasts exceptional resistance to atmospheric corrosion due to the formation of a tenacious passivating oxide layer. This inherent property shields the underlying insulation from the detrimental effects of acid rain, salt spray, industrial pollutants, and even harsh coastal environments. Unlike alternative materials like galvanized steel, aluminum exhibits minimal oxidation, preventing unsightly rust stains and prolonging the lifespan of the entire pipe insulation system. Furthermore, its high reflectivity mitigates thermal expansion and contraction, minimizing stress on the jacketing and underlying insulation during extreme temperature fluctuations.
2. Workability and Easy to Install
Compared to heavier materials like steel, aluminum excels in its lightweight and malleable nature. This translates to significantly easier handling and installation, particularly in situations with intricate piping configurations or tight spaces. Aluminum jacketing can be readily cut, bent, and formed to seamlessly conform to complex pipe shapes, minimizing installation time and labor costs. Additionally, its thinner profile reduces the overall weight of the insulated pipe assembly, simplifying handling and reducing strain on support structures.
3. Thermal Performance and Energy Savings
Aluminum’s inherent high reflectivity plays a crucial role in enhancing the thermal performance of insulated pipes. Its polished surface effectively reflects radiant heat away from the insulated core, minimizing heat gain and contributing to improved energy efficiency. This is particularly advantageous in applications where maintaining precise temperature control is paramount, such as HVAC systems or cryogenic facilities. By reducing heat gain, aluminum jacketing helps minimize energy consumption for cooling or heating requirements, leading to significant cost savings over the long term.
4. Aesthetically Pleasing and Versatile
Unlike the dull or rusting appearance of some alternative materials, aluminum jacketing presents a clean and polished aesthetic. Its bright, reflective surface enhances the visual appeal of exposed piping, particularly in applications with architectural considerations. Furthermore, aluminum readily accepts custom paint finishes, allowing for seamless integration with existing color schemes or branding elements. This versatility makes it a compelling choice for installations where both functionality and aesthetics are important factors.
5. Cost-Effective
While the initial cost of aluminum jacketing may be slightly higher than certain plastic alternatives, its long-term value proposition proves undeniably superior. Its exceptional durability, minimal maintenance requirements, and potential for energy savings through improved thermal performance translate to significant lifecycle cost reductions. Additionally, aluminum’s recyclability aligns with sustainability initiatives, offering environmental benefits compared to virgin materials. When considering the total cost of ownership over the entire lifespan of the pipe insulation system, aluminum jacketing often emerges as the most cost-effective and sustainable solution.
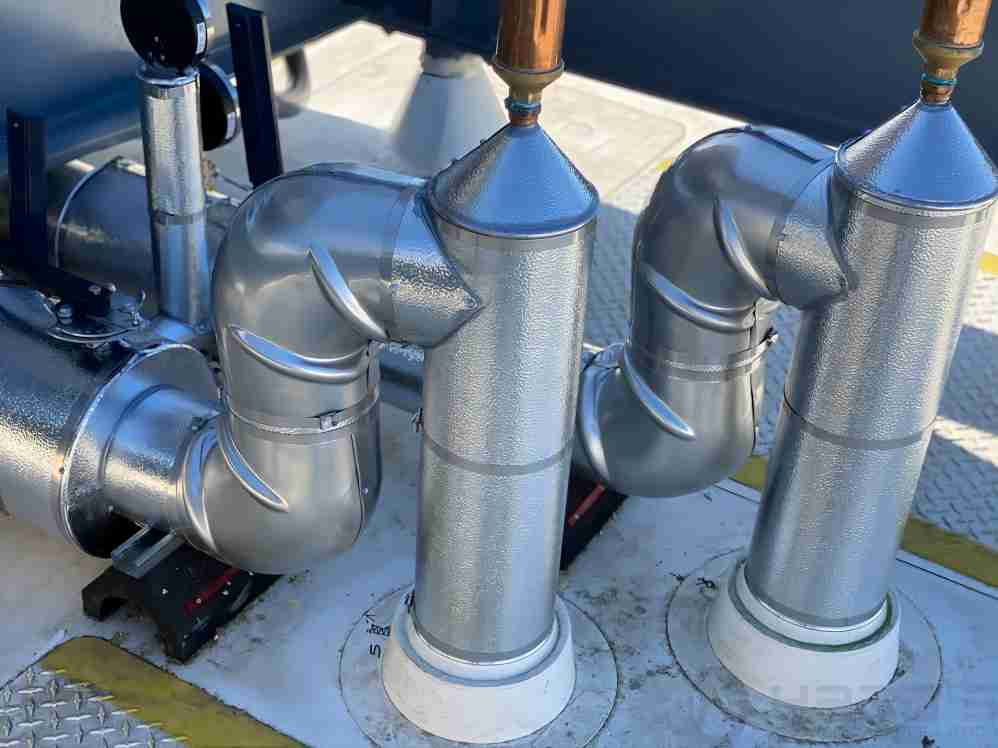
Applications of Aluminum Jacket in Pipe Systems
The versatility of aluminum jackets extends far beyond mere aesthetics, finding critical applications in a diverse array of industrial landscapes. Its unique combination of physical properties, including exceptional corrosion resistance, weatherability, and high reflectivity, make it the preferred choice for protecting and optimizing insulated pipe systems in demanding environments.
1. Mechanical Insulation Protection
Aluminum jacket serves as a crucial barrier against physical damage, moisture ingress, and wind uplift, safeguarding the integrity and performance of the underlying insulation. Its inherent strength and resilience shield the insulation from accidental impacts, abrasion, and punctures that could compromise its thermal performance and lead to costly repairs. Furthermore, aluminum’s watertight properties prevent moisture infiltration, which can degrade the insulation material and promote the growth of mold and mildew. Additionally, its robust construction withstands wind uplift forces, ensuring the insulation remains securely in place even under extreme weather conditions.
2. HVAC System Optimization
In the intricate network of heating, ventilation, and air conditioning systems, aluminum jacket plays a vital role in optimizing thermal performance. It efficiently insulates hot and cold water pipes, ductwork, and air handling units, minimizing heat gain or loss depending on the application. This enhanced thermal control translates to improved energy efficiency, reducing operating costs and environmental impact. Additionally, aluminum’s reflective properties contribute to reduced radiant heat transfer, further enhancing the system’s overall efficiency.
3. Industrial Piping Protection
Within the complex world of industrial facilities, the aluminum jacket provides a robust shield for pipes carrying diverse fluids. In refineries, chemical plants, and power plants, it protects against the corrosive effects of chemicals, acids, and high temperatures, preventing leaks and ensuring the safe and efficient flow of critical materials. Its exceptional weatherability withstands harsh industrial environments, minimizing the need for frequent maintenance and replacement. Furthermore, aluminum’s lightweight properties minimize the overall weight burden on pipe support structures, particularly in large-scale industrial installations.
4. Aboveground Oil and Gas Pipeline Integrity
For aboveground oil and gas pipelines, the aluminum jacket offers a crucial line of defense against the elements. Its weatherproofing properties shield the pipes from the detrimental effects of UV radiation, rain, snow, and wind, preventing premature degradation and ensuring pipeline integrity. Additionally, its corrosion resistance protects against the corrosive effects of saline environments or acidic soil conditions, minimizing the risk of leaks and ensuring the safe and reliable transportation of these vital resources.
5. District Heating and Cooling System
In district heating and cooling systems, aluminum jacket plays a critical role in maintaining optimal temperature control. It efficiently insulates pipes transporting hot or cold water, minimizing heat loss or gain during transmission. This improved thermal performance translates to reduced energy consumption for heating or cooling buildings, leading to significant cost savings and environmental benefits. Additionally, aluminum’s reflective properties further enhance the system’s efficiency by minimizing radiant heat transfer, contributing to a more sustainable and cost-effective operation.
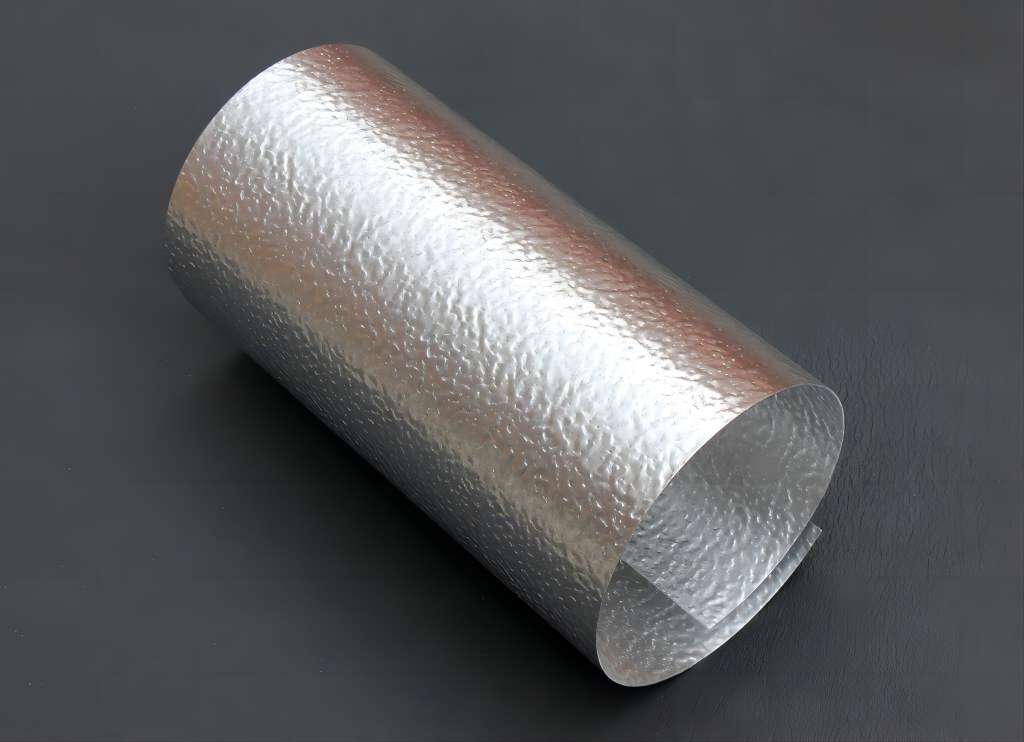
Types and Installation Techniques of Aluminum Jacket for Pipe Insulation
1. Aluminum Roll Jacketing
This versatile format consists of thin aluminum sheets, typically ranging from 0.012″ to 0.024″ in thickness, continuously rolled into coils for ease of application. Roll jacketing offers exceptional adaptability, allowing for custom cutting and forming to seamlessly conform to any pipe diameter or configuration. The installation process often involves mechanical fastening techniques such as banding or crimping, providing a secure and durable attachment to the underlying insulation. This flexibility makes roll jacketing ideal for complex piping layouts, elbows, and irregular shapes where pre-formed options may not be readily available.
2. Pre-formed Aluminum Jacketing
For applications requiring quicker installation or precise fit, pre-formed aluminum jacketing provides a convenient solution. These prefabricated sections are manufactured to specific pipe diameters and configurations, including elbows, bends, tees, and other fittings. This eliminates the need for custom cutting and forming, streamlining the installation process and minimizing material waste. Pre-formed jacketing typically employs mechanical fastening or adhesive bonding for secure attachment, depending on the specific design and application requirements. This option is particularly advantageous for large-scale projects or applications with repetitive piping configurations.
3. Installation Methods
The optimal installation method for an aluminum jacket depends on various factors, including pipe diameter, application requirements, and desired level of permanence. Several techniques are commonly employed:
- Mechanical Fastening: This established method utilizes metal bands, straps, or clips to secure the aluminum jacketing to the underlying insulation. Banding can be applied manually or with specialized banding tools, providing a robust and long-lasting attachment.
- Adhesive Bonding: In situations where minimizing visual disruptions is crucial, adhesive bonding offers a clean and seamless installation approach. Specialized high-performance adhesives formulated for compatibility with both aluminum and the underlying insulation material are required for optimal performance. This method is particularly favored for architectural applications or situations where exposed piping aesthetics are a concern.
- Combination Techniques: On complex piping configurations or situations with demanding requirements, a combination of mechanical fastening and adhesive bonding may be employed. This hybrid approach leverages the strengths of both methods, ensuring secure attachment while minimizing visual impact.
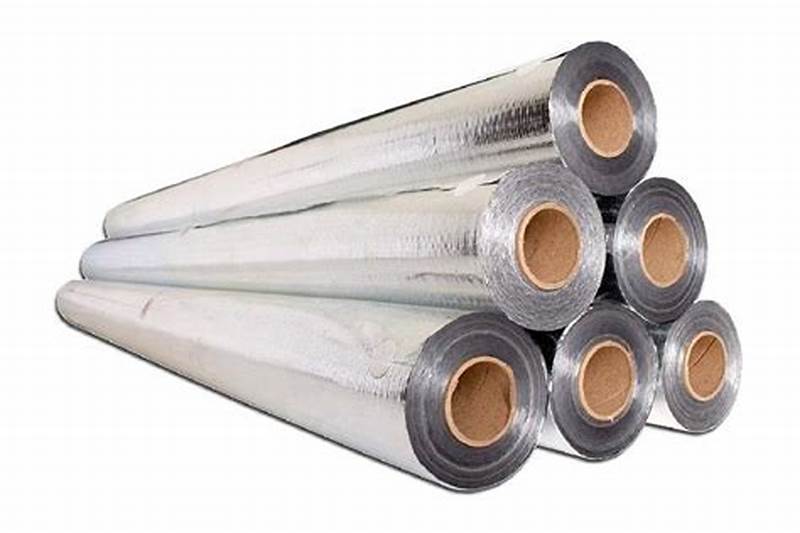
Considerations and Limitations of Aluminum Jackets in Pipe Systems
While undeniably effective, an aluminum jacket is not without its considerations and limitations. A comprehensive understanding of these factors is crucial for informed decision-making and maximizing its performance in specific applications.
1. Mechanical Susceptibility
Aluminum can be susceptible to dents and punctures, particularly compared to heavier materials like steel. This necessitates careful handling during installation and maintenance to avoid compromising the jacketing’s integrity and thermal performance. Protective measures, such as using corner guards or avoiding sharp cornering during installation, can minimize the risk of mechanical damage. Additionally, choosing a thicker gauge aluminum for applications prone to physical impact can enhance its robustness.
2. Galvanic Corrosion Potential
Direct contact between aluminum and dissimilar metals, particularly copper, can lead to galvanic corrosion. This occurs due to the differing electrical potentials of the metals, causing the less noble metal (aluminum) to corrode at an accelerated rate. To mitigate this risk, proper isolation mechanisms such as insulating gaskets or non-metallic spacers must be employed at contact points with dissimilar metals.
3. Cost Comparison with Plastic Alternatives
While offering superior performance in terms of durability, weather ability, and reflectivity, the aluminum jacket may carry a slightly higher initial cost compared to some plastic jacketing options. However, a comprehensive lifecycle cost analysis often reveals that aluminum’s extended lifespan, minimal maintenance requirements, and potential energy savings outweigh the initial cost difference. Additionally, the recyclability of aluminum aligns with sustainability initiatives, offering environmental benefits over virgin plastic materials.
4. Additional Considerations
- Application Temperature: Depending on the specific aluminum alloy used and installation methods, some limitations may exist regarding maximum operating temperatures. Consult manufacturer specifications for compatibility with specific temperature ranges.
- Fire Resistance: While inherently fire-resistant compared to most plastics, certain applications may require additional fire-retardant measures for optimal safety. Consider fire-rated adhesive bonding or cladding with specialized fire-resistant materials for high-risk environments.
- Maintenance and Inspection: Periodic inspections and maintenance are essential for maintaining the integrity and performance of aluminum jackets. Regularly check for signs of mechanical damage, corrosion, and loose fasteners to ensure the system’s long-term effectiveness.
By acknowledging these considerations and limitations, architects, engineers, and contractors can make informed decisions regarding the suitability of aluminum jackets for their specific needs. In many cases, its superior performance and long-term value proposition outweigh the initial cost and potential limitations, making it the preferred choice for a wide range of pipe insulation applications.
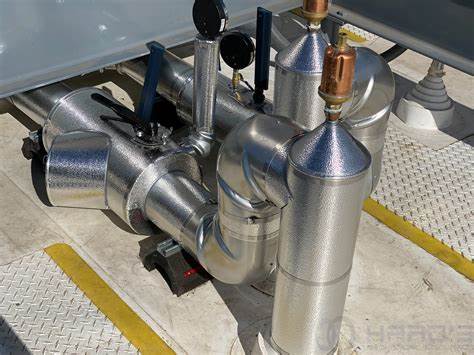
Conclusion
In conclusion, the application of aluminum jackets in pipe systems brings numerous benefits, including thermal insulation, corrosion protection, and mechanical durability. By understanding the properties and advantages of aluminum jackets, industries can make informed decisions to enhance the efficiency and longevity of their pipe systems. As technology continues to advance, the widespread adoption of aluminum jackets and aluminum cladding is likely to contribute to a more sustainable and energy-efficient future in various industrial sectors.