Aluminum extrusion has revolutionized various industries with its versatility, lightweight properties, and excellent strength. To achieve high-quality aluminum profiles, it is essential to follow proper processing methods and adhere to strict guidelines. This article will delve into the workflow of aluminum extrusion machines and the considerations for aluminum extrusion dies, providing valuable insights for optimizing the production process and maximizing die lifespan.
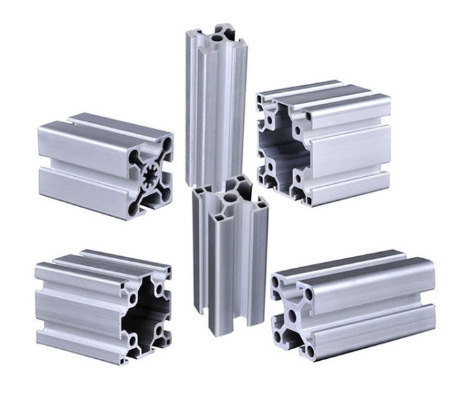
Workflow of Aluminum Extrusion Machine
The workflow of an aluminum extrusion machine involves several crucial steps that ensure smooth and efficient production.
Firstly, it is important to inspect the hydraulic system for any signs of oil leakage and ensure that the air pressure is within the normal range. Any issues with the system can lead to subpar extrusion results and potential machine breakdowns.
Next, a thorough inspection of the equipment is necessary. Conveyor belts, cooling beds, and material storage platforms should be checked for any damage or scratches that could affect the quality of the aluminum extrusion profiles.
Preparation for stretching is another vital step. The length of the aluminum extrusion profiles should be confirmed, and the desired stretching rate should be determined based on the profile type. Clamping methods must be carefully chosen, considering the profile’s shape and ensuring sufficient clamping area.
During the stretching process, it is crucial to ensure that the profiles have cooled to an appropriate temperature before initiating the stretching operation. Additionally, any bending or twisting issues should be addressed beforehand to prevent further complications.
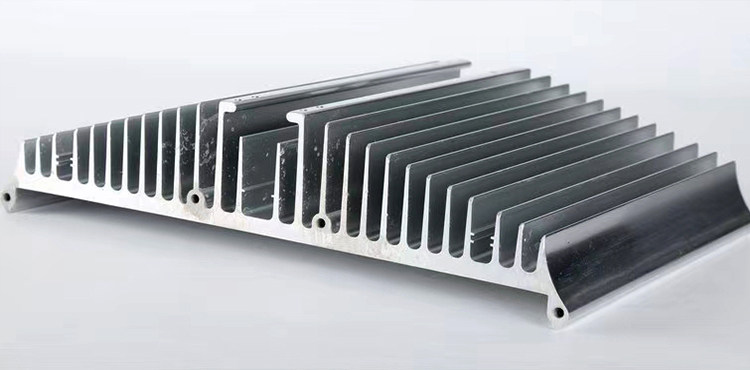
Trial stretching of the first and second profiles is essential to evaluate the stretching rate and clamping method. Visual inspection for defects like bending, twisting, and gaps should be performed. If necessary, adjustments can be made to the stretching rate.
In case the stretching process fails to eliminate defects or meet the required dimensional standards, it is crucial to halt the extrusion and notify the operator. Troubleshooting at an early stage can prevent the wastage of resources and minimize production downtime.
Proper handling and cooling of the profiles on the cooling bed are of utmost importance. Profiles should be carefully arranged to avoid friction, collision, and overlapping, which can cause surface damage.
Considerations for Aluminum Extrusion Dies
Aluminum extrusion dies play a significant role in shaping aluminum profiles. Several considerations should be taken into account to optimize the die performance and prolong its lifespan.
The complexity of profile sections poses a challenge in die design and production. Specialized die designs and production processes are often required to accommodate the diverse range of profile shapes.
- Choosing the right extrusion machine is critical. The tonnage of the machine should be determined based on the dimensions, complexity, and extrusion ratio of the profiles to achieve optimal extrusion results.
- Billet selection and heating temperature significantly impact the extrusion process. Uniformity in the billet’s alloy composition and grain size should be ensured. Controlling the heating temperature helps prevent issues such as gas release or excessive softening of the metal structure.
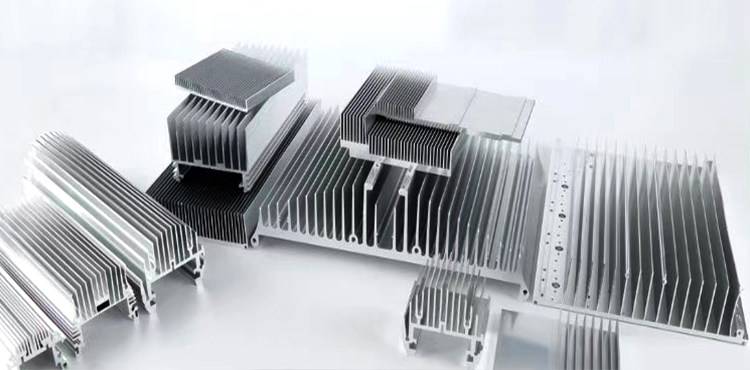
- Process optimization is essential to maximize die lifespan. Proper control of extrusion speed promotes uniform metal flow, reducing die wear. Selecting suitable extrusion temperatures based on the die and billet conditions helps maintain optimal extrusion performance.
- Surface treatment and maintenance of dies are critical for their longevity. Surface nitriding treatment should be applied to enhance durability. Regular polishing of the working surfaces to a mirror finish ensures smooth extrusion. Additionally, thorough cleaning of the die cavities is necessary to remove any residue or foreign particles that can compromise the extrusion quality.
- Proper handling and support systems, such as die supports and cushions, are essential to avoid deformation or breakage during the extrusion process.
- Implementing the correct alkali washing method after extrusion prevents die cracking during the cooling process. Careful control of the cooling rate minimizes thermal stress and extends die lifespan.
- Gradual usage intensity is recommended for the lifespan of extrusion dies. During the initial stages of die usage, lower intensity is advised to allow the die to adapt and stabilize. As the die reaches a stable state, the usage intensity can be gradually increased. Towards the end of the die’s lifespan, it is important to reduce the usage intensity to prevent premature failure and ensure the die’s safe operation until it is deemed unfit for further use.
- Maintaining comprehensive records of die usage and maintenance is crucial for effective management. Each set of dies should be properly tracked, and a maintenance log should be maintained, including information on usage duration, extrusion parameters, cleaning and polishing schedules, and any observed issues. These records aid in identifying patterns, optimizing maintenance practices, and planning for die replacements.
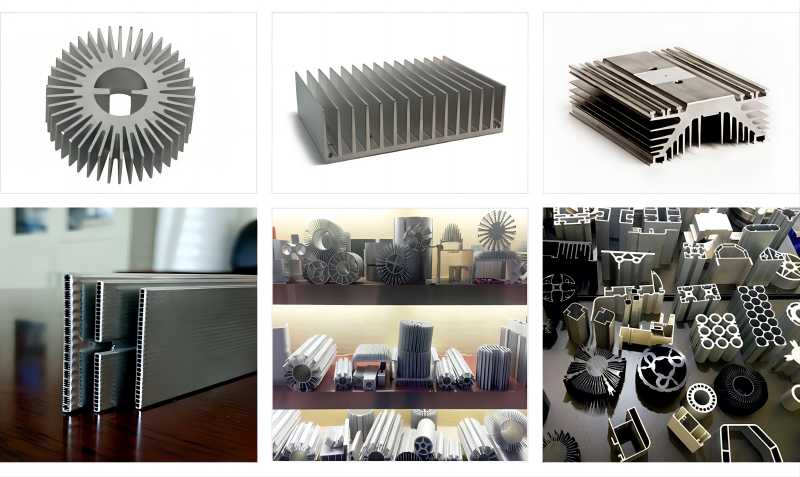
Conclusion:
Efficient and effective aluminum extrusion processing methods are essential for achieving high-quality aluminum profiles while maximizing the lifespan of extrusion dies. By following a systematic workflow for the extrusion machine and considering key factors in die design and maintenance, manufacturers can optimize production processes, minimize defects, and improve overall productivity. Moreover, proper record-keeping and regular monitoring of die performance enable proactive maintenance and timely replacement, leading to cost savings and enhanced operational efficiency. With these guidelines in place, the aluminum extrusion industry can continue to meet the demands of various sectors and leverage the advantages of this versatile material.