Aluminum extrusions play a vital role in modern engineering, providing versatile solutions for diverse industries like construction, transportation, and electronics. The variety of available profiles, from standard designs to custom configurations, ensures that engineers can find the perfect match for their project requirements. In this article, we will explore the types of aluminum extrusion shapes, their applications, and key considerations for choosing the right profile to meet your engineering needs.
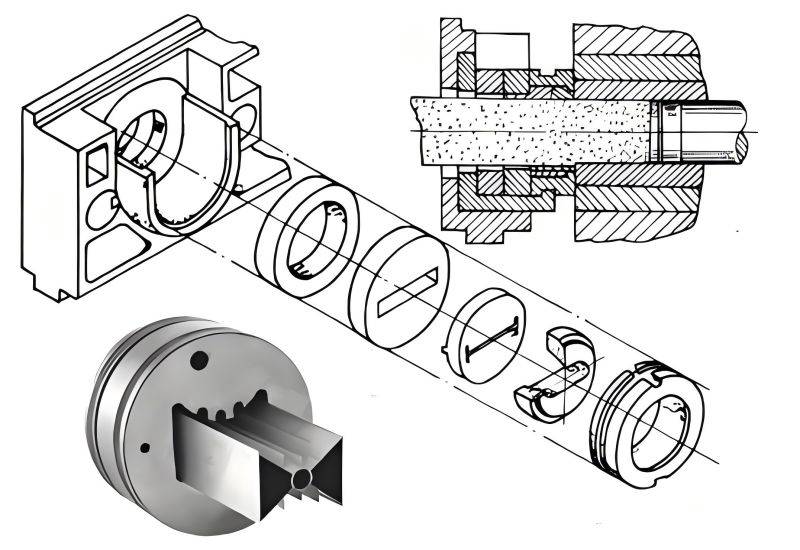
How Aluminum Extrusion Shapes are Formed?
Aluminum extrusion is a process that transforms aluminum alloy into precisely shaped profiles. Imagine pushing a soft metal through a die—much like squeezing toothpaste from a tube. That’s essentially how aluminum profile extrusion works. During extrusion, a heated aluminum billet is forced through a die, which is a specialized tool that determines the final shape, ranging from simple forms like rods and tubes to complex custom designs. Once extruded, these profiles can be further processed through cutting, machining, and finishing, ready to integrate into various designs and meet specific application needs.
This efficient and flexible manufacturing method is why aluminum extrusions are so prevalent in industries from aerospace to consumer goods.
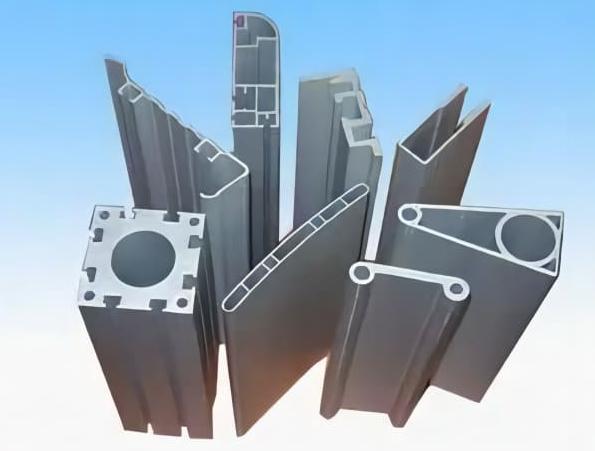
Common Types of Aluminum Extrusion Profiles
The vast array of aluminum extrusion shapes available can initially seem daunting. However, each shape serves a distinct purpose, often optimized for specific structural, aesthetic, or functional requirements. The choice of alloy also plays a crucial role, with common options like 6061 and 6063 offering different balances of strength, weldability, and corrosion resistance. Let’s delve into some of the most frequently used profiles and their typical applications, summarized in the table below for quick reference.
Aluminum Extrusion Shape | Ideal Applications | Key Characteristics | Common Alloys |
L-Shaped Aluminum Extrusion | Structural support, bracing, corner protection, general fabrication, solar panel frames. | Two perpendicular legs; versatile for various framing and joining needs. | 6063, 6061 |
T-Shaped Aluminum Extrusion | Structural frameworks, connectors, mounting rails (e.g., T-slot systems), machine bases. | Flat top with central stem; excellent for modular assembly and fastening. | 6063, 6061 |
U-Shaped Aluminum Extrusion | Channels, tracks, guides, decorative trim, wire enclosures, sliding door tracks. | Flat base with two parallel flanges; ideal for containment or linear motion. | 6063, 6061 |
C-Shaped Aluminum Extrusion | Precise guides, structural channels with tighter tolerances, specialized tracks for automation. | Similar to U-channel but often with specific internal dimensions for precision. | 6061, 6063 |
H Shape Aluminium Extrusion | Joining panels, lightweight structural members, partition wall framing. | Resembles an “I-beam” or “H”; efficient for connecting and distributing loads. | 6063, 6061 |
D-Shaped Aluminum Extrusion | Architectural trim, handrails, cable management, decorative accents. | One flat side, one rounded side; offers aesthetic and ergonomic benefits. | 6063 |
Oval Aluminum Extrusion | Decorative elements, furniture frames, ergonomic handles, specialized piping. | Smooth, curvilinear form; provides modern aesthetics and comfortable grip. | 6063 |
Z Shape Aluminum Extrusion | Mounting brackets, decorative trim, creating offsets between surfaces. | Two parallel flanges offset by a perpendicular web; useful for specific mounting angles. | 6061, 6063 |
F Shaped Aluminum Extrusion | Edge trim for panels (glass, wood), panel retention, concealing panel edges. | Features a flange to secure panels and a perpendicular leg for mounting. | 6063 |
Triangular Aluminium Extrusion | Architectural features, artistic designs, specialized corner bracing, unique framing. | Distinct geometric shape; offers unique aesthetics and structural rigidity in corners. | 6063, 6061 |
Round Corner Aluminum Extrusion | Consumer electronics, medical equipment, furniture, public spaces where safety is paramount. | Refers to any profile with intentionally rounded corners; improves safety, aesthetics, and cleanability. | 6063, 6061 (applied to rectangular/square) |
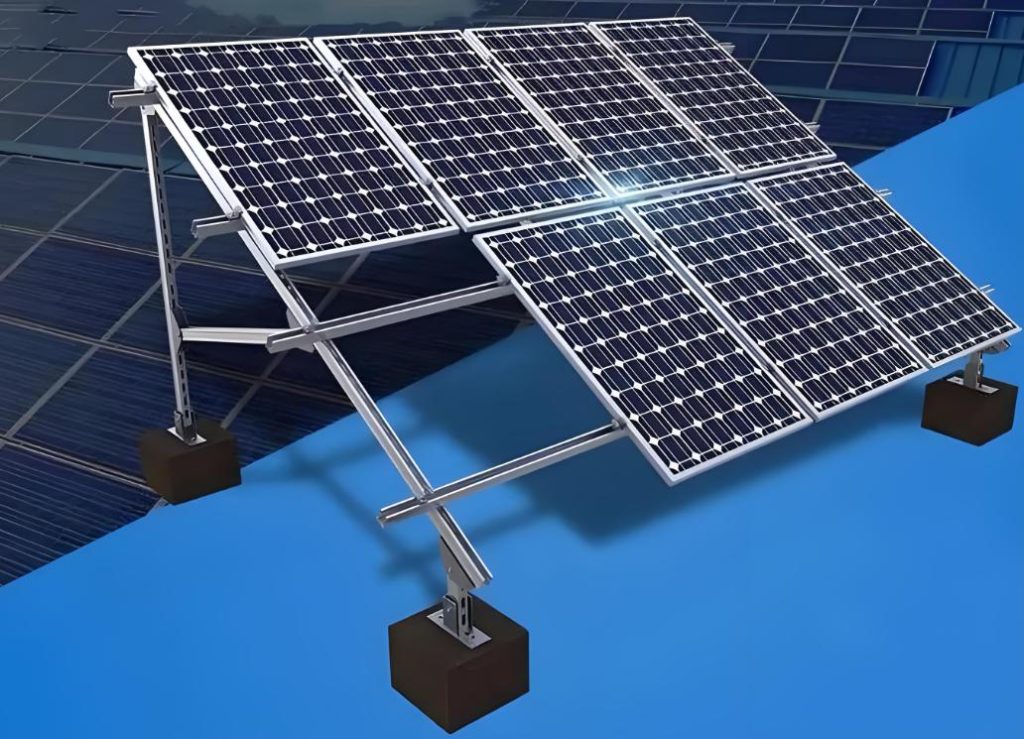
When Specific Shapes Aren’t Enough: Consider Customization
Sometimes, standard shapes cannot fully meet engineering requirements. In such cases, custom aluminum extrusions offer the flexibility needed to create tailored solutions. Here are some considerations for custom aluminum extrusions:
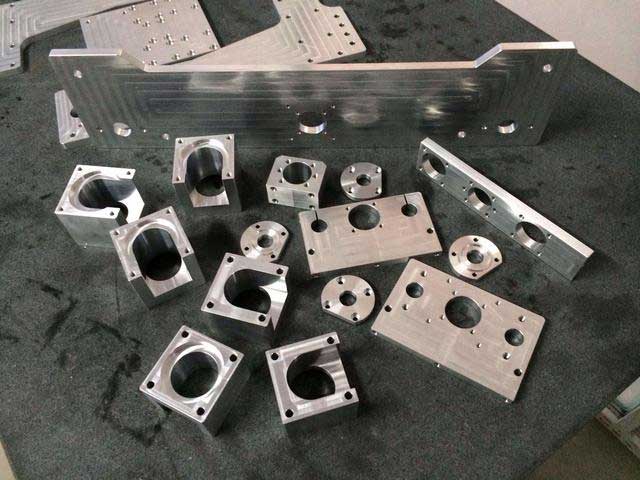
- Die design and tooling costs
The most significant upfront cost for a custom extrusion is the creation of the die. This is a precision-engineered steel tool that defines the cross-section of the profile. Die design can be complex, requiring specialized knowledge to ensure the aluminum flows correctly and the final part meets specifications. Costs can range from a few hundred dollars for simple dies to several thousand for intricate, multi-hollow designs. This initial investment is typically a one-time charge, amortized over the production run. For instance, a complex hollow profile might cost $2,000-$5,000 for the die, while a simple angle could be $500-$1,000.
- Minimum order quantities (MOQs)
Due to the setup costs involved in extrusion (die changes, press warm-up, scrap material), aluminium profile suppliers often have MOQs for custom runs. These can vary significantly, from a few hundred pounds to several thousand, depending on the supplier and the complexity of the profile. It’s crucial to discuss MOQs early in the design process to ensure alignment with project volume needs. For a new custom die, an MOQ of 500-1000 lbs (227-454 kg) is common, but it can be higher for very specialized or large profiles.
- Lead times for die creation and production
Designing and fabricating a custom die takes time. Once the design is finalized, die creation can range from 2 to 6 weeks, sometimes longer for highly complex geometries. After the die is approved, the initial production run of the custom profile will also have a lead time, typically an additional 2 to 4 weeks. These lead times must be factored into the overall project schedule to avoid delays. For example, if a project needs parts in 8 weeks, ordering a custom extrusion with a 4-week die lead time and 3-week production lead time leaves little room for error.
Role of aluminium profile suppliers in providing tailored solutions
Choosing the right aluminium profile supplier becomes even more critical when venturing into custom extrusions. A reputable supplier offers more than just manufacturing; they become a true partner. They should possess in-house design and engineering expertise to assist with optimizing the profile design for extrudability, ensuring it meets performance requirements while being cost-effective to produce. They can advise on alloy selection, surface finishes, and secondary fabrication processes. Their experience can often identify potential issues in die design or production before they become costly problems, saving time and money. A good supplier acts as a collaborative expert, translating your engineering needs into a tangible, high-quality aluminum extrusion.
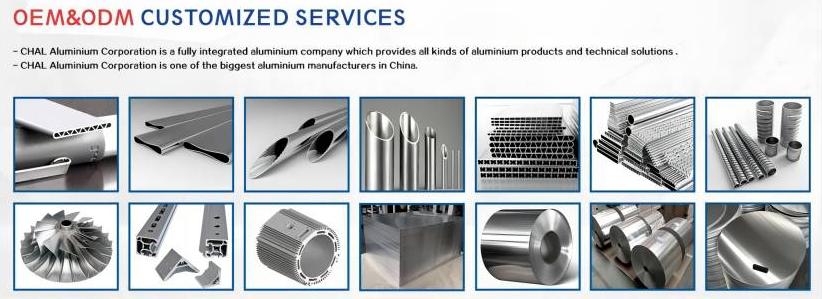
Factors to Consider When Choosing an Aluminum Extrusion Shape
Selecting the right aluminum extrusion shape is a multi-faceted decision, influenced by a blend of functional requirements, material considerations, cost implications, and the capabilities of your chosen aluminium profile supplier. A holistic approach to this decision-making process will yield the most optimal results for your project.
Factor | Description | Recommended Practices |
Functional Requirements | Assess structural demands, such as load-bearing capacity and flexibility. | Match profile dimensions and shape to design constraints. |
Material Properties | Consider alloy composition for strength, corrosion resistance, and machinability. | Select alloys like 6061 or 6063 based on application needs and environmental conditions. |
Cost Implications | Factor in costs of raw materials, die production, and secondary processes like anodizing. | Evaluate long-term savings through reduced waste and increased durability. |
Supplier Capabilities | Choose suppliers with experience in delivering high-quality extrusions. | Verify the supplier’s ability to meet customization needs and production timelines. |
By carefully considering the functional requirements, material properties, cost implications, and the capabilities of your aluminium profile supplier, you can unlock the full potential of aluminum extrusion profiles.
Whether you opt for the proven reliability of standard aluminum extrusion shapes like the versatile L shaped aluminum extrusion or the robust rectangular aluminum extrusions, or if your needs demand the precision and integration of custom aluminum extrusions, the principles remain the same. Collaborate closely with experienced suppliers, leverage their expertise, and always consider the total cost and value proposition. This meticulous approach ensures that your chosen aluminum extrusion shape not only meets your immediate engineering needs but also contributes to the long-term success and innovation of your designs.