Aluminum, with its incredible versatility and strength-to-weight ratio, reigns supreme as a material choice for countless applications. But within the aluminum realm, two distinct manufacturing methods – casting and extrusion – each offer unique advantages and drawbacks. Whether you’re an engineer envisioning the next revolutionary car component or a homeowner seeking the perfect aluminum fence, navigating the nuances of cast and extruded aluminum is crucial. This comprehensive guide delves into the strengths, weaknesses, and ideal applications of both casting and extrusion. By comparing factors like cost, strength, design flexibility, and surface finish, you’ll be equipped to confidently partner with the perfect casting or extruded aluminum manufacturer to bring your vision to life.
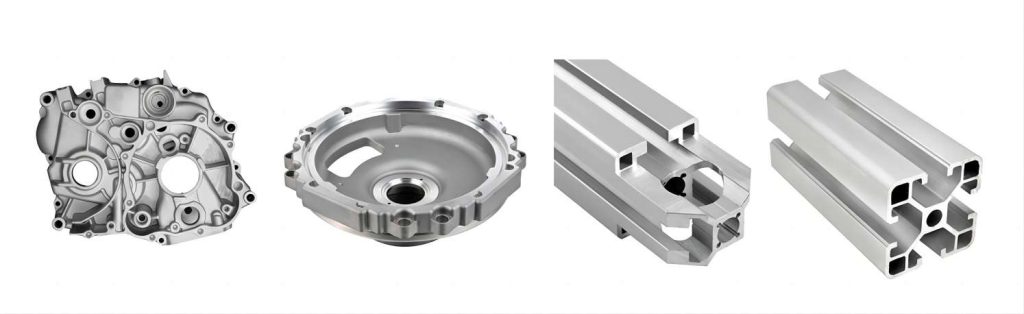
What is Cast Aluminum and Extruded Aluminum?
Cast Aluminum
Cast aluminum, a vital material in various industries, is created through a fascinating process of transforming molten aluminum into intricate or simple shapes.
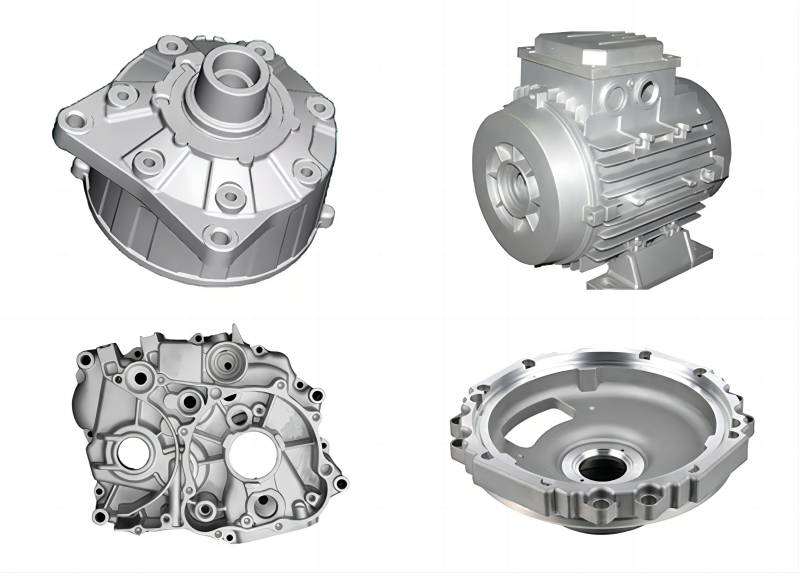
What are the Casting Methods?
- Sand casting: Uses sand molds. Most versatile and cost-effective, ideal for complex shapes and low-volume production.
- Die casting: Uses reusable metal molds for high-precision, high-volume production of intricate parts.
- Investment casting: Uses wax patterns. Creates intricate and high-precision parts with excellent surface finish, often used for aerospace and medical applications.
- Lost-foam casting: Uses a polystyrene pattern that melts away during casting, leaving the desired aluminum form.
Extruded Aluminum
Extruded aluminum is a versatile material formed by forcing heated aluminum alloy through a precisely shaped die, much like squeezing toothpaste from a tube. This process creates long, continuous profiles with intricate cross-sections, from simple squares and rectangles to complex, hollow shapes like I-beams and window frames.
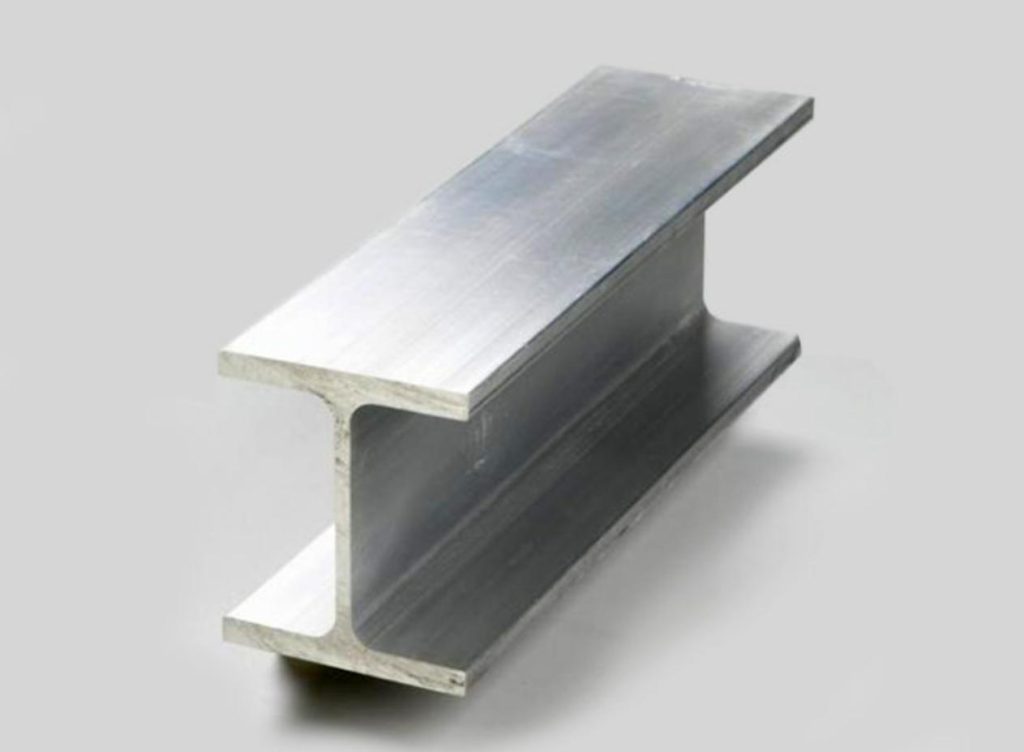
What are the Extrusion Methods?
Extruded aluminum can be formed through several different methods, each with its own advantages and limitations. Here are the most common extrusion methods:
1. Direct Extrusion:
This is the most common and widely used method. In direct extrusion, the heated billet is placed in a container and a hydraulic ram pushes it directly through the die. The ram pressure forces the aluminum to flow through the die opening, forming the desired cross-section as it exits.
- Advantages: Simple setup, suitable for a wide range of shapes, cost-effective for large production runs.
- Disadvantages: Limited length of extrusions due to container size, potential for friction wear on the billet and container.
2. Indirect Extrusion
In indirect extrusion, the billet remains stationary, while the container and die move together towards the ram. The ram pushes against a pressure plate that forces the aluminum through the die.
- Advantages: Capable of producing longer extrusions than direct extrusion, better surface finish and less friction wear.
- Disadvantages: More complex setup compared to direct extrusion, limited to hollow or semi-hollow sections.
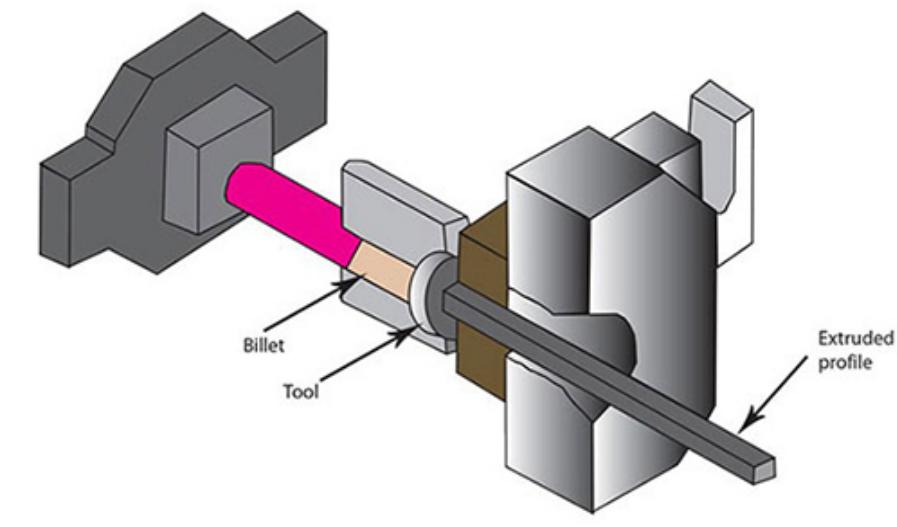
Comparison between Cast Aluminum and Extruded Aluminum
Both cast aluminum and extruded aluminum are widely used in various industries due to their versatility, strength, and lightweight properties. However, they differ significantly in their properties, pros and cons, and applications. Here are some of the comparisons:
Cast Aluminum | Extruded Aluminum | |
Properties | Good dimensional stability, corrosion resistance, lower strength, porosity possible | High strength-to-weight ratio, good surface finish, less corrosion resistant in some alloys, limited shape complexity |
Advantages | Complex shapes, lower tooling cost for simple designs, high-volume production | High strength, consistent dimensions, diverse shapes, good surface finish |
Disadvantages | Limited shape complexity, potential porosity, lower strength, rougher surface | Higher tooling cost for complex shapes, limited shape design, less suitable for high-volume production of complex parts |
Products | Engine blocks, car wheels, furniture, decorative items. | Building frames, window frames, heat sinks, bicycle frames, electrical components. |
How to Choose the Proper Forming Processes?
Choosing between cast aluminum and extruded aluminum depends on several key factors:
Part Design and Geometry:
- Cast aluminum: excels at creating complex shapes with internal cavities and thin walls. Ideal for intricate details and decorative elements.
- Extruded aluminum: limited to cross-sectional shapes that can fit through a die (e.g., tubes, channels, H-beams). Offers precise dimensional control and consistent wall thickness.
Strength and Weight:
- Cast aluminum: generally weaker than extruded aluminum due to potential porosity and grain structure. However, specific alloys can offer high strength.
- Extruded aluminum: stronger due to denser material and work hardening during the extrusion process. Ideal for load-bearing applications.
Production Volume and Cost:
- Cast aluminum: suitable for low to medium production runs due to higher tooling costs but lower per-unit cost for complex shapes.
- Extruded aluminum: cost-effective for high-volume production due to lower tooling costs per unit. However, complex shapes might require custom dies, increasing costs.
Surface Finish and Appearance:
- Cast aluminum: requires additional machining or polishing for smooth surfaces. Can achieve textured finishes.
- Extruded aluminum: offers smooth, consistent surfaces with various pre-painted or anodized finishes.
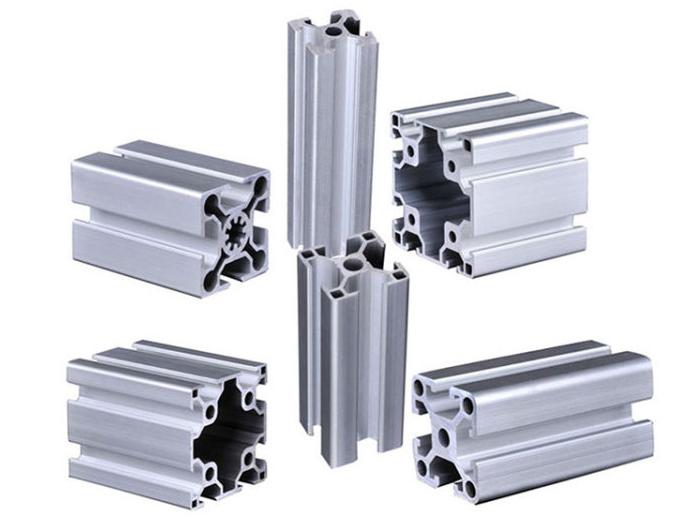
Common Q&A of Cast Aluminum vs. Extruded Aluminum
- Which is stronger, cast aluminum or extruded aluminum?
Extruded aluminum is generally stronger than cast aluminum, especially for tensile strength (resistance to pulling forces) and yield strength (the point at which the material begins to deform permanently). This is because the extrusion process aligns the aluminum grains in the direction of the extrusion, creating a more uniform and stronger material.
- Which is lighter, cast aluminum or extruded aluminum?
Cast aluminum can be lighter than extruded aluminum for the same part, depending on the design. This is because casting allows for hollow sections and thin walls, which can reduce weight. However, extruded aluminum can also be lightweight if it is designed with hollow sections or thin walls.
- Which is more expensive, cast aluminum or extruded aluminum?
The cost of cast aluminum and extruded aluminum can vary depending on the complexity of the part, the size of the production run, and the specific aluminum alloy used. In general, casting is more expensive than extrusion for small production runs, but extrusion can be more expensive for large production runs of complex parts.
Conclusion
Choosing between cast and extruded aluminum is no mere toss-up. Each manufacturing process possesses distinct strengths and weaknesses, dictating its suitability for specific applications. This guide has hopefully illuminated the intricacies of both, empowering you to make an informed decision.