Aluminum stamping and aluminum die casting are two popular manufacturing processes used for producing aluminum parts. Both processes have their unique advantages and disadvantages, making it essential to choose the right one depending on the specific project’s requirements. In this article, we will compare aluminum stamping and aluminum die casting, discussing their pros and cons and helping you decide which process is best suited for your project.
What is stamping and die casting?
Stamping is a metal forming process that involves cutting, punching, bending, and shaping metal sheets or coils to produce parts. This process is typically used for low volume production and produces high accuracy, precise parts with tight tolerances.
Die casting is a manufacturing process that involves injecting molten metal into a mold cavity at high pressure. Once the metal solidifies, the mold is opened and the finished product is removed. Die casting is a high-volume production process that can produce complex parts with excellent surface finishes.
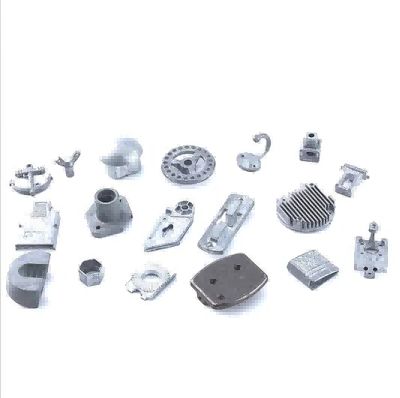
What are the pros and cons of aluminum stamping and aluminum die casting?
Aluminum Stamping
Advantages:
- High Accuracy and Precision: Stamping is a highly precise process, and aluminum stamping can produce parts with high accuracy and tight tolerances.
- Complex Geometries: Aluminum stamping can produce parts with complex geometries, making it ideal for applications where precise shapes and sizes are necessary.
- Low Tooling Cost for Simple Parts: Stamping requires less tooling than other manufacturing processes, making it a cost-effective choice for simple parts.
- Suitable for Low Volume Production: Stamping is ideal for low volume production runs, making it a great choice for prototyping or custom parts.
- Quick Setup and Production Time: Aluminum stamping has quick setup and production times, making it ideal for time-sensitive projects.
Disadvantages:
- Limited Complexity: While aluminum stamping can produce parts with complex geometries, it has limitations on the complexity of parts it can produce compared to other manufacturing processes.
- High Tooling Cost for Complex Parts: Stamping requires specific tooling for each part design, and the cost can be high for complex parts with intricate designs.
- Material Wastage: Stamping can result in material wastage, especially when producing complex parts with intricate designs.
- Limited Part Thickness: Aluminum stamping has limitations on the thickness of the parts it can produce, making it unsuitable for applications where thick parts are necessary.
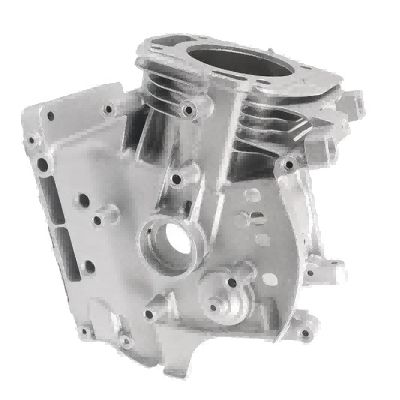
Aluminum Die Casting
Advantages:
- High Production Efficiency: Aluminum die casting is a high-speed, high-volume process that can produce complex parts quickly and efficiently.
- High Strength-to-Weight Ratio: Die-cast aluminum parts have a high strength-to-weight ratio, making them ideal for applications where weight reduction and strength are critical.
- Consistency and Repeatability: Die casting can produce consistent, high-quality parts with little variation, making it ideal for high-volume production runs.
- Excellent Surface Finish: Aluminum die casting can produce parts with excellent surface finish, making it ideal for applications where aesthetics are important.
- Versatility: Die casting can produce parts in various shapes and sizes, making it suitable for different applications.
- Low Assembly Cost: Die-cast aluminum parts often require less assembly than other manufacturing processes, making it a cost-effective choice for high-volume production runs.
Disadvantages:
- High Initial Tooling Cost: The tooling cost for die casting can be high, especially for low-volume production runs, making it less cost-effective for smaller projects.
- Limited Part Size: Die casting has limitations on the size of parts it can produce, making it unsuitable for applications where large parts are necessary.
- Porosity: Porosity can be a concern with die-cast parts, which can lead to a reduction in strength and surface finish.
- Limited Material Options: Die casting is limited to a few specific alloys, making it less versatile than other manufacturing processes.
- Potential for Cracking: Aluminum die casting has a risk of cracking or other defects due to thermal stresses, which can affect the quality of the parts.
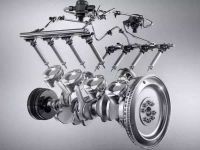
How to Choose Aluminum Stamping or Aluminum Die Casting?
The choice between aluminum die casting and aluminum stamping depends on several factors, including the part’s design, complexity, production volume, and cost.
Aluminum die casting is ideal for high-volume production runs, where speed and efficiency are essential, and parts require a high strength-to-weight ratio, excellent surface finish, and consistent quality. It is also suitable for parts that require complex geometries, thin walls, and precise details.
On the other hand, aluminum stamping is ideal for low to medium volume production runs, prototyping, and custom parts that require high accuracy, tight tolerances, and precise shapes. It is a cost-effective process for simpler parts and can produce parts with complex geometries, but with limitations.
In conclusion, both aluminum stamping and aluminum die casting have their unique advantages and disadvantages. Aluminum stamping is precise and cost-effective for low to medium volume production runs and is ideal for simpler parts and prototyping. On the other hand, aluminum die casting is efficient and cost-effective for high-volume production runs and is suitable for parts requiring a high strength-to-weight ratio, excellent surface finish, and consistent quality. When choosing between the two, it is essential to consider the part’s design, complexity, production volume, and associated tooling costs. Both processes are effective for aluminum parts manufacturing, and the choice depends on the specific project requirements.
If you are not sure about the production method, please feel free to contact us, and we will give you more suggestions. We CHAL is a fully integrated aluminum company that provides all kinds of aluminium products and technical solutions. We are committed to being the leading supplier of aluminum profile, aluminum micro-channel tube, aluminum high frequency welded tube, aluminum drawn tube, aluminum seamless tube, aluminum machining parts and stamping parts, aluminum wire, aluminum heat transfer material, aluminum plate, sheet, strip, foil, rod and bar, die forgings, die castings. The products manufactured are widely used in the automotive industry, construction industry, HVAC/R and heat transfer industry, aviation, rail transportation, oceanic industry, etc. Believe us and you will receive quality service and products.
Related Products
Related Articles