Aluminum die casting is a widely used manufacturing process that offers many benefits, such as lightweight and high-strength parts. However, to ensure the production of high-quality parts, it’s important to implement effective quality control measures throughout the die casting process. Additionally, as technology continues to evolve, there are exciting new developments on the horizon for aluminum die casting. In this blog post, we’ll explore the importance of quality control in aluminum die casting and the potential for future advancements in the field.
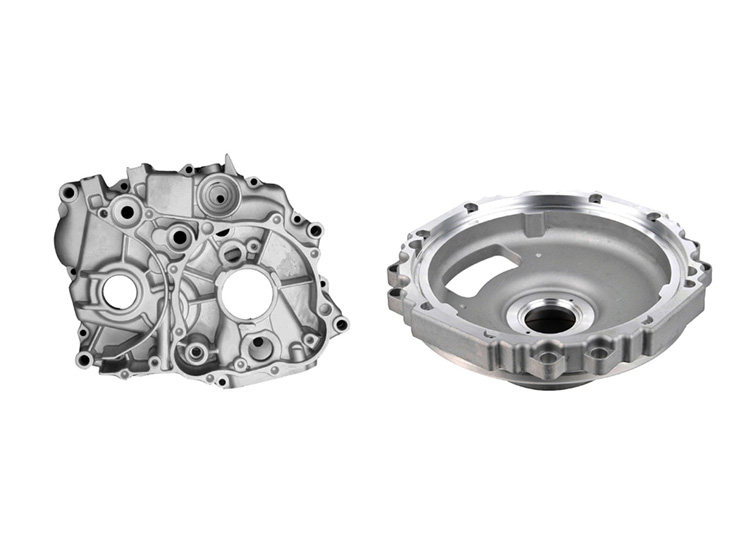
Quality Control in Aluminum Die Casting
Quality control is a critical aspect of any manufacturing process, including aluminum die casting. By implementing effective quality control measures, manufacturers can improve part quality, reduce scrap rates, and minimize the risk of defects. Some common quality control measures used in aluminum die casting include:
- Mold maintenance: Regular mold maintenance is essential for ensuring that the mold is free from damage or wear that could impact part quality. This includes cleaning the mold, checking for wear, and making any necessary repairs.
- Process monitoring: By monitoring the die casting process, manufacturers can identify any issues or deviations from the desired process parameters. This allows them to make adjustments and ensure that each part meets the required specifications.
- Material testing: Testing the metal alloy before and after casting can help ensure that it meets the necessary standards for mechanical properties, chemical composition, and surface finish.
Future Developments in Aluminum Die Casting
As technology continues to advance, there are several exciting developments on the horizon for aluminum die casting. Some of the emerging trends and advancements include:
- Simulation software: The use of simulation software can help optimize mold designs by predicting the flow of molten metal and identifying any potential defects before production begins.
- Sensors and automation: Incorporating sensors and automation into the die casting process can improve process control and reduce the risk of defects. For example, sensors can monitor the temperature and pressure during casting, while automation can control the injection speed and timing.
- New alloys: Researchers are developing new aluminum alloys with improved properties, such as higher strength, better thermal conductivity, and increased corrosion resistance. These new alloys could open up new possibilities for aluminum die casting in industries such as aerospace, automotive, and electronics.
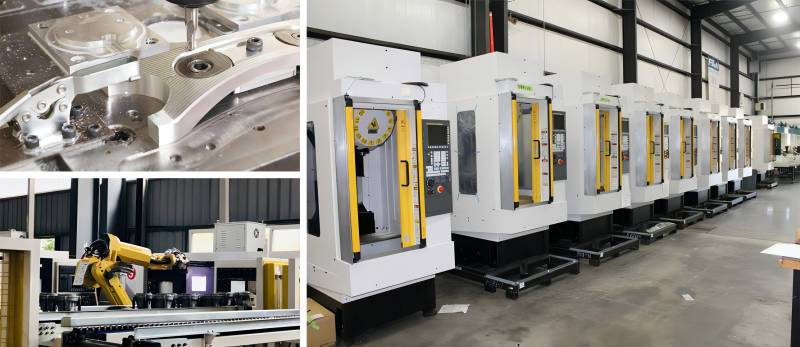
Case Studies of Aluminum Die Casting
To illustrate the importance of quality control and the potential for future advancements in aluminum die casting, let’s take a look at a few case studies.
- BMW
The automotive company BMW uses simulation software to optimize mold designs and minimize waste. By simulating the die casting process before production begins, BMW can identify potential issues and make design adjustments to ensure that each part meets the required specifications. This has led to a reduction in waste and an increase in efficiency, as well as improved part quality.
- Philips
The lighting manufacturer Philips has incorporated sensors and automation into its die casting process to improve process control and reduce scrap rates. By using sensors to monitor the temperature and pressure during casting, and automation to control the injection speed and timing, Philips can ensure that each part is produced consistently and meets the required specifications. This has led to a reduction in scrap rates and an increase in efficiency.
- Apple
Apple uses a specialized aluminum alloy called “Apple Alloy” in the production of its products, including the iPhone and MacBook. This alloy is designed to be lightweight, strong, and durable, with excellent corrosion resistance. By using this specialized alloy in its products, Apple can achieve the desired combination of strength and weight, while also reducing its environmental impact.
These case studies highlight the importance of quality control and the potential for future advancements in aluminum die casting. By prioritizing quality control and staying up-to-date with emerging trends and technologies, companies can improve efficiency, reduce waste, and produce high-quality parts that meet the demands of their customers.
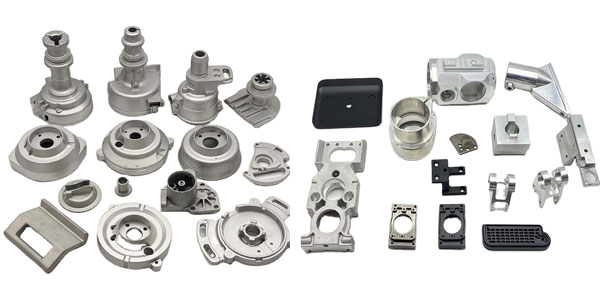
Conclusion
Effective quality control is essential for ensuring the production of high-quality parts in aluminum die casting. By implementing measures such as mold maintenance, process monitoring, and material testing, manufacturers can reduce the risk of defects and improve part quality. Additionally, as technology continues to evolve, there are exciting new developments on the horizon for aluminum die casting. By staying up-to-date with emerging trends and technologies in the field, manufacturers can improve efficiency, reduce waste, and stay competitive in an ever-changing market.