In the market for a lightweight, durable, and decorative metal product manufactured with holes in a wide range of sizes? Aluminum perforated sheet panels are the answer. Whether your project requires punched perforations for enhanced aesthetics, water drainage, light control, acoustic elements, or privacy applications, aluminum perforated sheet panels combine high-end design and functionality for interior and exterior designs.
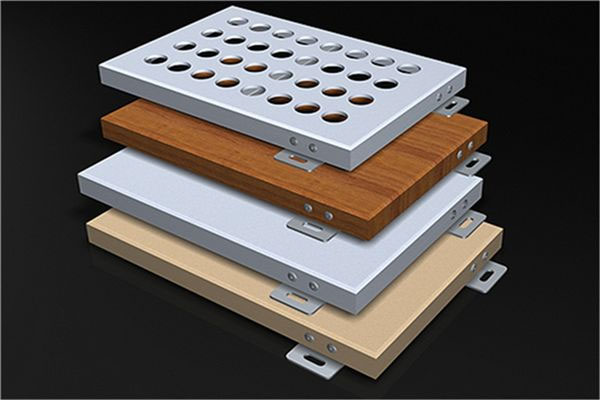
What is the Perforated Aluminium Sheet?
Aluminum sheet that has been punched with a variety of holes in different sizes and patterns to add aesthetic appeal is called a perforated aluminum sheet. The perforated aluminum sheet provides a decorative or aesthetic effect while reducing weight and allowing the passage of light, liquid, sound, and air. Corrosion-resistant perforated aluminum sheets are frequently utilized in both interior and exterior design.
The perforated aluminum plate is used as a decorative plate, which is beautiful and elegant. It can be made into various utensils, which are corrosion-resistant, durable, and high-temperature resistant in kitchen products. It has a wide range of applications in daily life.
- Specifications: 3003-H14, ASTM B209, QQ-A-250/2
- Applications: security, sifting, machinery guards, enclosures, sign panels, & more.
- Workability: Easy to Weld, Cut, and Form with proper equipment
- Mechanical Properties: Non-magnetic, Tensile= 22K+/-, Yield= 21K+/-
Types of Perforated Aluminum Sheet
There are many types of perforated aluminum sheets. In order to meet the requirements of different construction engineering fields and consumer decoration. Perforated aluminum sheets are usually classified according to their alloy composition and thickness.
Alloy composition: high-purity aluminium plate, pure aluminum plate, alloy aluminum plate, composite aluminum plate or welding plate and aluminum-clad aluminum plate, etc.
Thickness: thin plate (0.15mm-2.0mm), conventional plate (2.0mm-6.0mm), medium plate (6.0mm-25.0mm), thick plate (25mm-200mm), five-rib pattern aluminum plate and ultra-thick plate (>200mm) etc.
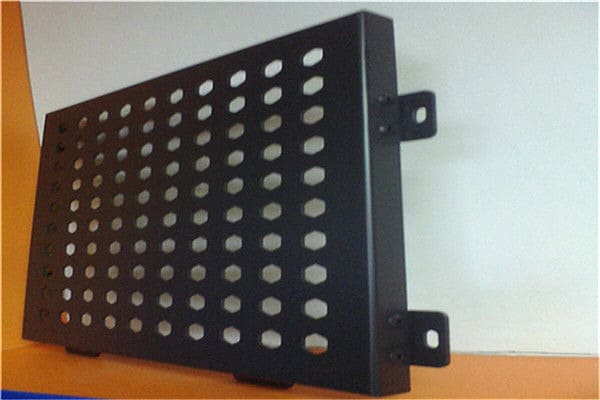
Four Elements of Perforated Aluminum Sheet
- Perforation Rate
Perforation rate is the key to reducing the energy consumption of the architecture and affecting its visual integrity. And the core factor affecting the perforated aluminum plate unit. Different perforation rates create different degrees of permeability in the building. The change of the perforation rate can control the amount of light entering the room, and with the increase of the perforation rate, the daylighting coefficient continues to rise. According to the current mechanical equipment, the maximum perforation rate can reach about 65%, and the size of the perforated plate is required to be within the range of 1500*3000. The higher the perforation rate of the perforated aluminum plate, the greater the influence on the flatness of the formed aluminum plate.
- Aperture
Controlling the hole diameter, hole spacing, and arrangement of the perforations can adjust the visual clarity and visual image. Combined with factors such as perforation rate and plate thickness, it can reduce solar radiation heat and energy consumption. The fixed aperture of the perforated aluminum plate unit can create a homogeneous visual effect, and the change of the processing aperture can form a gradient or pattern effect.
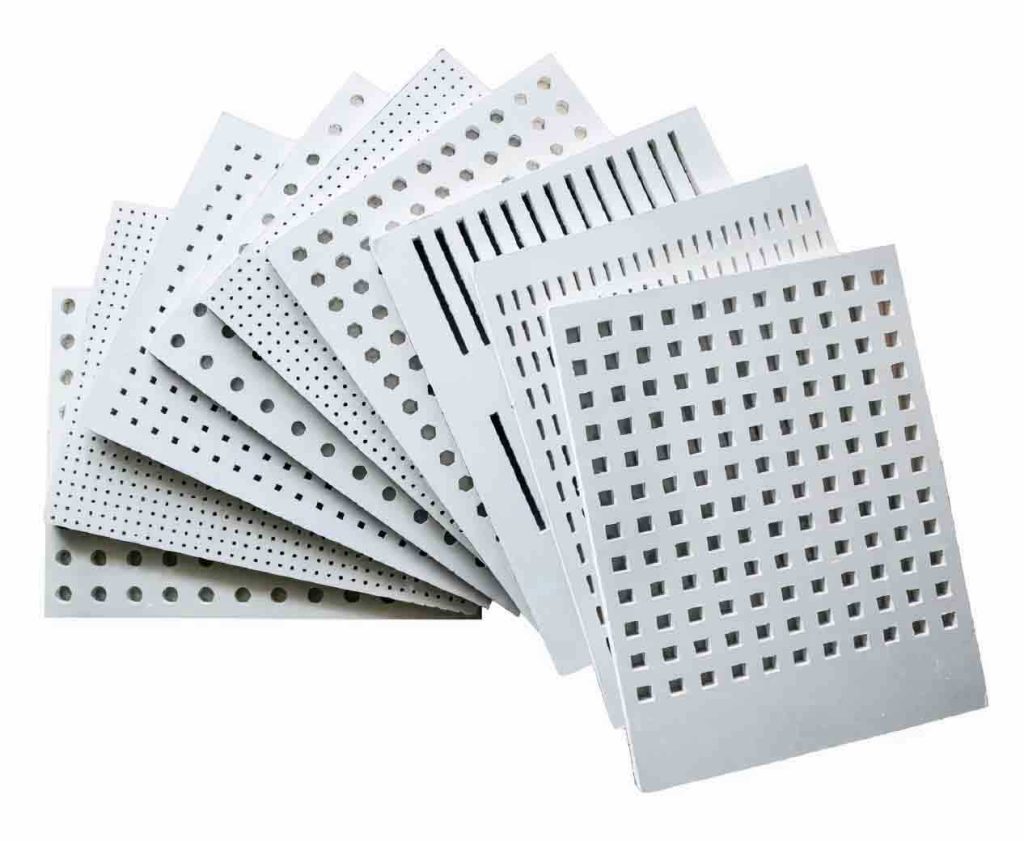
- Thickness
Influenced by factors such as processing cost, unit weight, unit flatness, etc., the thickness of the perforated aluminum plate used as the external is usually 1.0mm ~ 6.0mm conventional plate, and the perforated sound-absorbing plate is basically within 3mm. With the increase of the perforation rate, the flatness of the plate is affected, While increasing the thickness of the plate can improve the strength of the unit.
- Shapes
There are flat, folded, zigzag, wavy, and short-sided folded plates. As the perforation rate increases, the strength of the perforated plate decreases. The choice of plate type can affect the strength of the perforated aluminum plate, which affects the size of the perforated plate module, the number of keels that connect, and the whole effect.
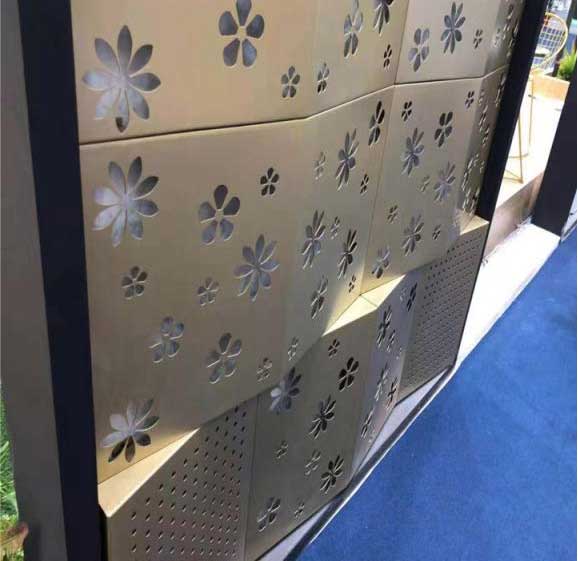
Process of Perforated Aluminum Sheet
The perforated plate commonly used as building skin is usually made of the metal aluminum plate as raw material. Through mechanical punching, it can create a regular or irregular hole effect on the surface of the plate, which forms a special texture and texture of hollow. The early perforated aluminum plate holes were simple and regular shapes (square, rectangle, cross, etc.) arranged neatly or dislocated according to rules.
The perforated aluminium plate can produce different shapes and surface treatments according to customer requirements. It also can be made in various styles such as arc-shaped hollow plates, wavy ceiling shape perforated aluminum ceiling, bending at any angle. Different shapes, sizes, densities, and holes bring rich and varied surface forms to sheet metal. This laid the foundation for the creation of individual architectural skins. Along with people’s pursuit of artistic beauty, hollowed-out aluminum plates have also begun to discard the regular and conventional form of holes, while arising irregularly arranged hole textures and patterned plates with various hollowed-out patterns and other artistic material forms.
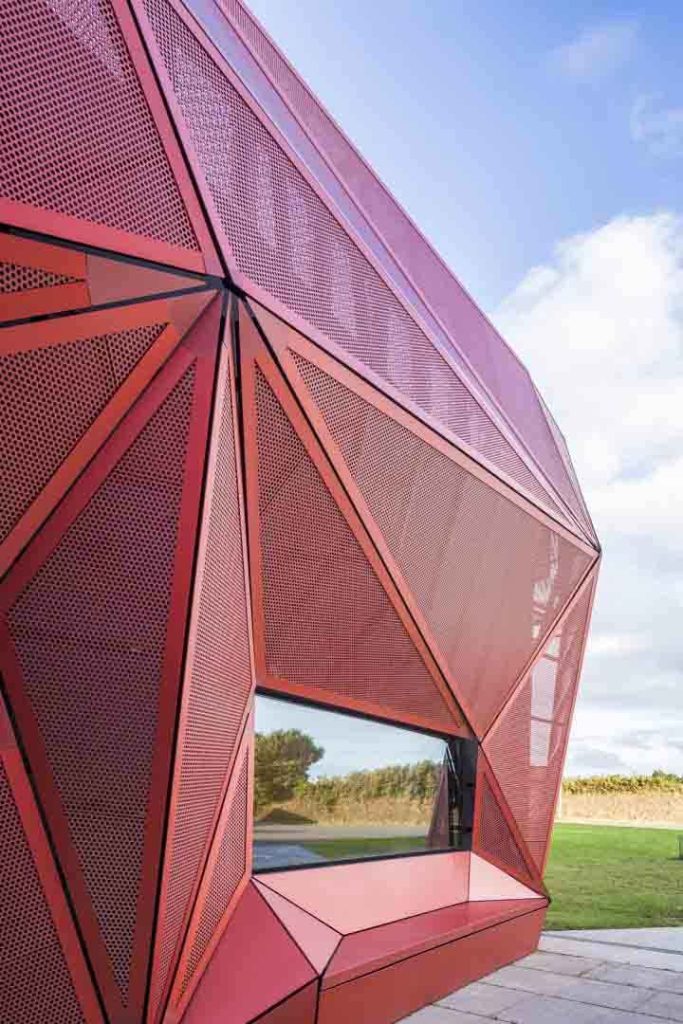
Advantages of Perforated Aluminum Sheet
- As the external skin of the building, the impact of the perforated aluminium plate on the ventilation, shading, lighting, and other aspects of the building can influence the thermal performance of the building. Various factors such as different metal plate types, metal plate perforation shape, perforation aperture, perforation rate, plate thickness, and material may have an impact on the indoor thermal environment of the building.
- Light weight and high strength. For example, an aluminum plate with a thickness of 3.0 mm weighs about 8 kilograms per square plate. It is very easy to construct and safe to use.
- Corrosion resistance and strong plasticity. Some analysts pointed out that the average service life of aluminum veneer will not fade for more than 25 years. Due to the material properties, aluminium veneer can be made into various shapes, such as plane, arc and spherical.
- Due to the good non-stick properties of films formed by the coating, it is easy to clean and maintain. In addition, a variety of colors can be applicated to different scenes.
- Aluminum is green and safe, recyclable, environmentally friendly, and energy-saving.
- Easy to install and maintain, saving construction costs.
- Well-bending strength and high wind pressure resistance.
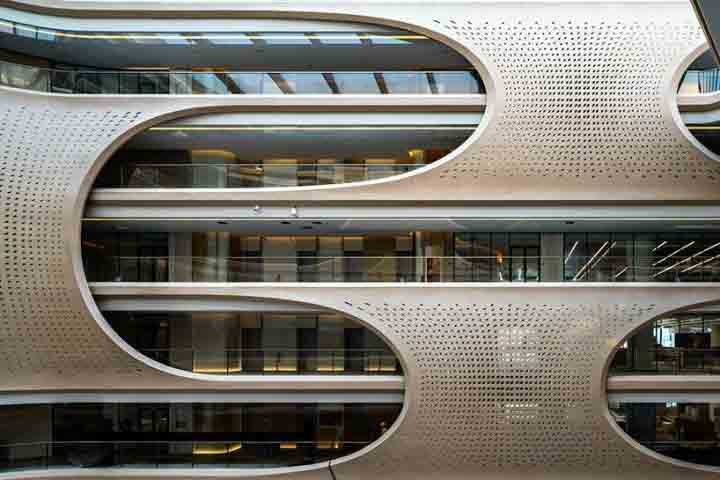
Conclusion
Perforated aluminum sheets are popular in projects, which can meet the environmental requirements of sustainable development and provide a decorative and durable appearance. CHAL focuses on aluminum products and has decades of aluminum manufacturing experience. If you have any questions about aluminum, please contact us and we will help you.