Aluminum multi-channel tubes, also known as MPE tubes (Multi Port Extrusion) or multiport extruded aluminium tubes, are essential components in various industries, particularly in the manufacturing of heat exchangers, condenser coils, and refrigeration systems. These tubes consist of multiple small channels within a single tube, providing increased surface area for efficient heat transfer. To ensure proper connections, transitions, and branching in these applications, a variety of fittings are employed with aluminum multi-channel tubes. In this article, we will explore the different types of fittings used with MPE tubes and their significance in creating reliable and high-performance systems.
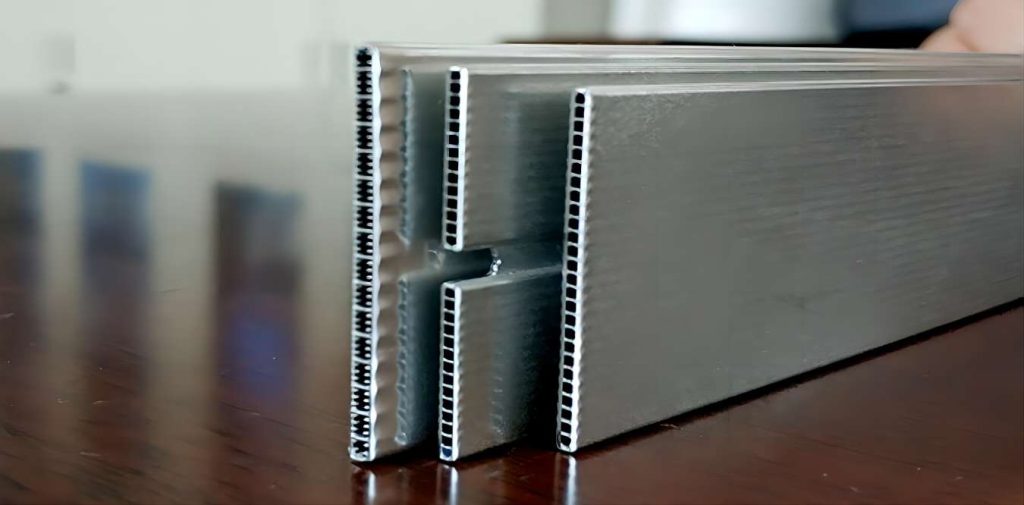
1. Compression Fittings Used with Aluminum MPE Tubes
Compression fittings are widely used for connecting aluminum multi-channel tubes without the need for soldering, welding, or brazing. These fittings typically comprise a compression nut, a compression ring (ferrule), and a body. When the compression nut is tightened, it compresses the ferrule against the tube, creating a tight seal. Compression fittings are suitable for low to medium pressure applications and are valued for their ease of assembly and disassembly.
2. Brazed Fittings Used with Aluminum MPE Tubes
Brazed fittings are essential components in the assembly of heat exchangers and refrigeration systems. Designed to be brazed to aluminum multi-channel tubes using a suitable brazing alloy, these fittings form strong, leak-tight joints. The brazing process involves heating the fitting and the tube to a specific temperature, allowing the molten filler material to flow and create a metallurgical bond. Brazed fittings offer excellent thermal and mechanical performance, making them a preferred choice in demanding applications.
3. Welded Fittings Used with Aluminum MPE Tubes
Welded fittings are used in situations where a robust and permanent connection is required. Aluminum multi-channel tubes can be joined to fittings or other components using various welding techniques, such as TIG (Tungsten Inert Gas) welding or laser welding. Welded fittings provide exceptional structural integrity and are commonly used in critical systems where reliability is paramount.
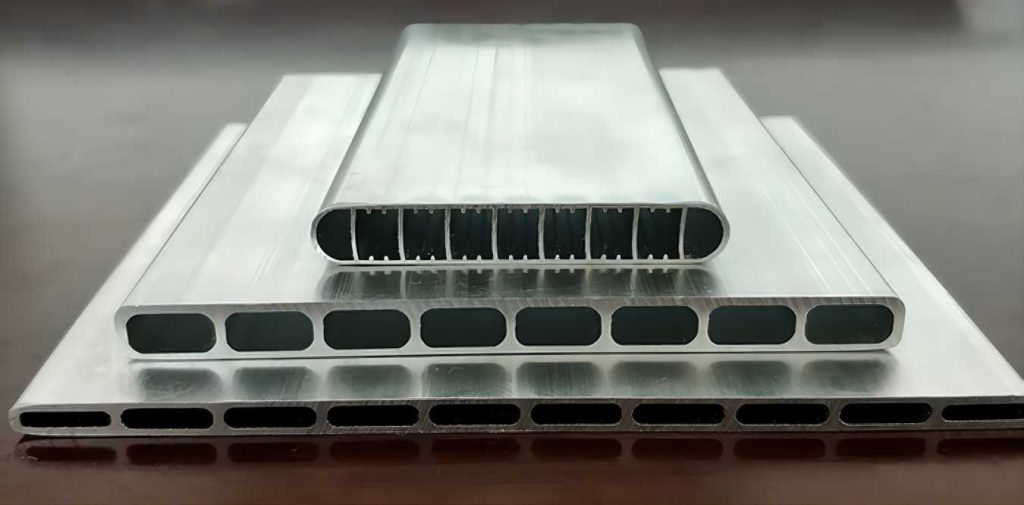
4. Flared Fittings Used with Aluminum MPE Tubes
Flared fittings are employed for connecting aluminum multi-channel tubes that have been flared at the end. The flared end of the tube is inserted into the fitting, and then a nut is tightened to secure the joint. Flared fittings create a reliable and leak-tight connection and are frequently used in refrigeration and hydraulic systems.
5. Push-to-Connect Fittings Used with Aluminum MPE Tubes
Push-to-connect fittings, also known as quick-connect fittings, offer a convenient and efficient means of joining aluminum multi-channel tubes. These fittings feature a push-in design that securely holds the tube in place, eliminating the need for additional tools or components. Push-to-connect fittings are ideal for applications where rapid assembly and disassembly are necessary.
6. Threaded Fittings Used with Aluminum MPE Tubes
Threaded fittings have male or female threads that allow them to be screwed onto corresponding threaded connections. They are used to securely connect aluminum multi-channel tubes to various parts of the system, such as manifold headers or other components. Threaded fittings provide a reliable and adjustable connection.
7. Manifolds and Distributors Used with Aluminum MPE Tubes
Mnifolds and distributors are specialized fittings used to distribute and collect the flow of refrigerant or fluid between multiple aluminum multi-channel tubes. Manifolds serve as central components in heat exchangers and play a crucial role in optimizing fluid flow and heat transfer efficiency.
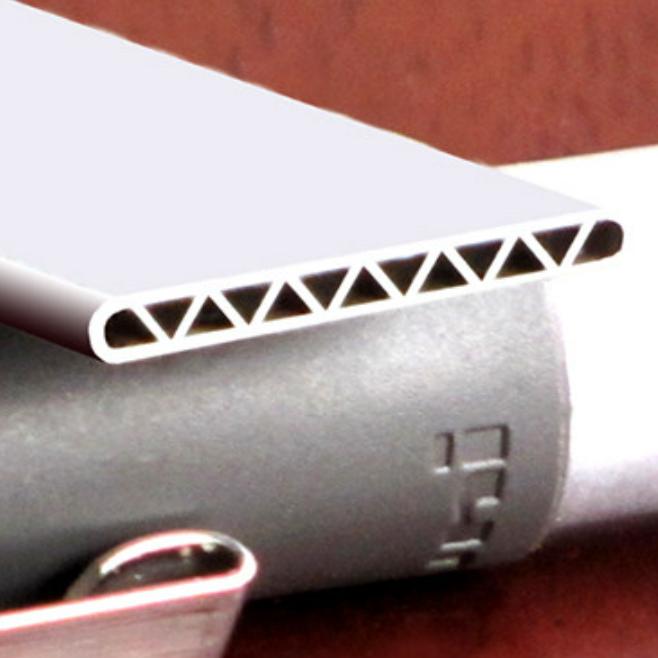
8. Transition Fittings Used with Aluminum MPE Tubes
Transition fittings facilitate smooth connections between aluminum multi-channel tubes and tubes or components made of different materials or sizes. These fittings ensure a seamless transition between different parts of the system and maintain the structural integrity of the overall assembly.
9. Elbows, Tees, and Crosses Used with Aluminum MPE Tubes
Elbows, tees, and crosses are fittings that allow for directional changes, branching, or splitting of the fluid or refrigerant flow within the system. Elbows provide angled bends, tees enable branching into two directions, and crosses allow branching into four directions. These fittings are instrumental in designing complex and efficient systems.
The choice of fitting type depends on various factors, such as the specific application, operating conditions, pressure requirements, and ease of installation. Manufacturers and engineers carefully select the most suitable fitting for each part of the system to ensure optimal performance and reliability of heat exchangers, condenser coils, and refrigeration systems using aluminum multi-channel tubes.
Conclusion
In conclusion, aluminum multi-channel tubes are indispensable components in modern heat exchangers and refrigeration systems, offering efficient heat transfer capabilities. To achieve reliable and leak-tight connections in these systems, various types of fittings are utilized with MPE tubes, including compression fittings, brazed fittings, welded fittings, flared fittings, push-to-connect fittings, threaded fittings, manifolds, distributors, transition fittings, and elbows, tees, and crosses. Each fitting type brings its unique advantages and characteristics, allowing engineers to tailor the assembly to the specific requirements of the application. By understanding the importance of these fittings and their proper implementation, professionals can create high-performance and energy-efficient systems that play a pivotal role in various industries and everyday life.