Oxyacetylene welding commonly referred to as gas welding, is a process that relies on the combustion of oxygen and acetylene. The thermal efficiency of oxyacetylene welding is low, the welding heat input is not concentrated, flux is required when welding aluminum alloys, residues need to be removed after welding, and the quality and performance of the joints are not high. Because the welding equipment is simple, no power supply is required, and the operation is convenient and flexible, it is often used for welding aluminum alloy components with low-quality requirements, such as thin plates and small parts, as well as repairing welding aluminum alloy components and aluminum castings.
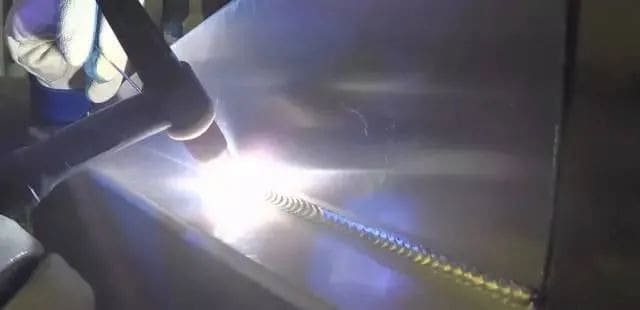
Selection of gas-welded joint forms
When gas welding aluminum alloys, it is not suitable to use lap joints and T-shaped joints, which are difficult to clean the residual flux and welding slag flowing into the gap, and butt joints should be used as much as possible. To ensure that the weldment is welded without collapse and burn-through, a backing plate with grooves can be used. The backing plate is generally made of stainless steel or pure copper. Welding with a backing plate can obtain good reverse forming and improve welding productivity.
Selection of gas welding flux
To make the welding process go smoothly and ensure the quality of the weld, it is necessary to add flux to remove the oxide film and other impurities on the aluminum surface during gas welding.
Gas welding flux is a flux in gas welding. Its main function is to remove the oxide film formed on the surface of aluminum during gas welding, improve the wetting performance of the base metal, and promote the acquisition of dense weld structures. Flux must be used for gas welding of aluminum alloys. Generally, the flux is directly sprinkled on the groove of the workpiece to be welded before welding or is added to the molten pool by dipping it on the welding wire.
Aluminum alloy flux is the chloride salt of potassium, sodium, calcium, lithium, and other elements. It is a powder compound prepared by sieving after crushing. For example, aluminum cryolite (Na3AlF6) can melt alumina at 1000 °C, and potassium chloride can convert refractory alumina into fusible aluminum chloride. This flux has a low melting point and good fluidity, and can also improve the fluidity of the molten metal and make the weld well-formed.
Selection of welding tip and flame
Aluminum alloys have strong oxidizing and gettering properties. During gas welding, to prevent the aluminum from being oxidized, a neutral flame or a weak carbonization flame (a carbonized flame with excess acetylene) should be used, so that the aluminum molten pool is placed under the protection of a reducing atmosphere without being oxidized. It is strictly forbidden to use an oxidizing flame because the use of an oxidizing flame with strong oxidizing properties will strongly oxidize the aluminum and hinder the welding process; and if there is too much acetylene, free hydrogen may dissolve into the molten pool, which will cause the seam to generate pores and make the welding seam lose.
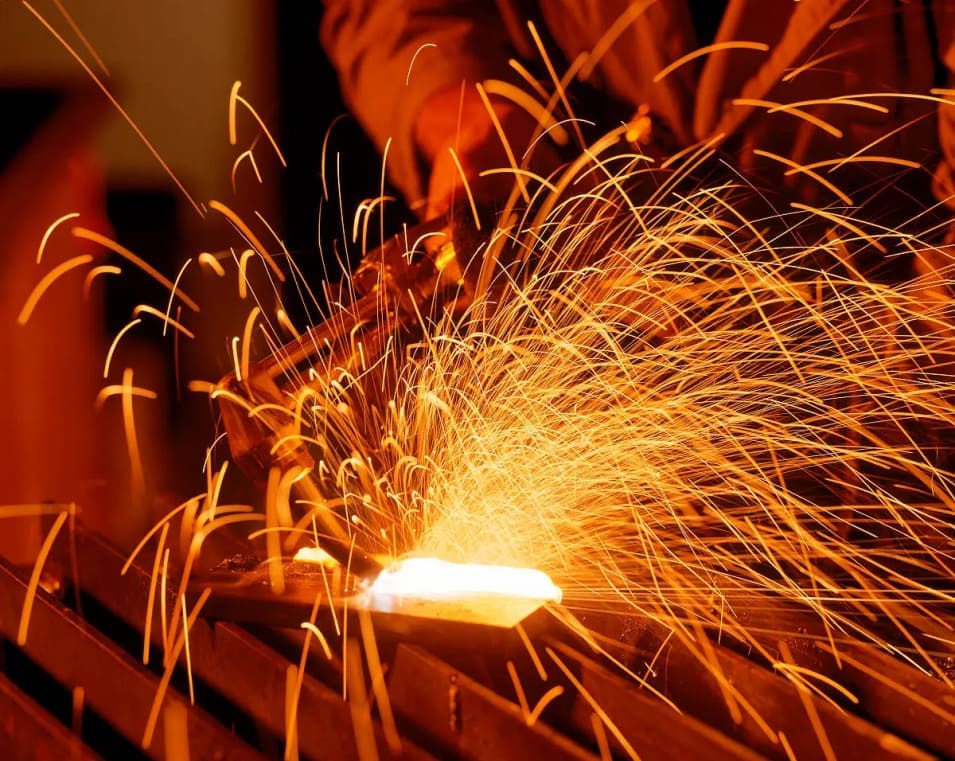
How to perform gas welding
When welding steel materials, the heating temperature can be judged by the color change of the steel. But when welding aluminum, there is no such convenient condition. Because the aluminum alloy has no obvious change in color during heating from room temperature to melting, it is difficult for the operator to control the welding temperature. However, the timing of welding can be grasped according to the following phenomena:
1. When the surface of the heated workpiece changes from bright white to dim silvery white, the surface oxide film is wrinkled, and the metal fluctuates at the heating place, it indicates that the melting temperature is about to be reached, and welding can be applied;
2. Use the end of the welding wire dipped in flux and the place to be heated, when the welding wire and the base metal can be fused, the melting temperature is reached, and welding can be performed;
3. When the edge of the base metal falls, the base metal reaches the melting temperature and can be welded.
Gas welding of thin plates can be done by the left welding method, the welding wire is located in front of the welding flame, this welding method is because the flame points to the unwelded cold metal, and part of the heat is dissipated, which is beneficial to prevent the molten pool from overheating, the growth of metal grains in the heat affected zone and burn through. If the thickness of the base metal is greater than 5mm, the right-hand welding method can be used. In this method, the welding wire is behind the welding torch, and the flame is directed to the welding seam so that the heat loss is small, the penetration depth is large, and the heating efficiency is high.
When gas welding thin parts with a thickness of less than 3mm, the torch inclination angle is 20-40°; when gas welding thick parts, the torch inclination angle is 40-80°, and the angle between the aluminum welding wire and the torch is 80-100°. Aluminum alloy gas welding should try to weld the joints at one time, and not deposit the second layer because the slag inclusion in the weld will be caused when the second layer is deposited.
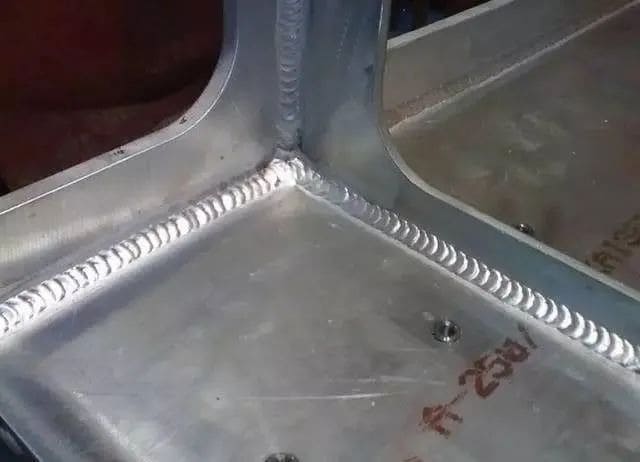
What treatment needs to be done after welding
The corrosion of the aluminum joint by the residual flux and slag on the surface of the gas welding seam is one of the reasons for the damage of the aluminum joint in future use. Within 1 to 6 hours after gas welding, the residual flux and slag should be cleaned to prevent corrosion of the weldment. The cleaning process after welding is as follows.
1. After welding, immerse the weldment in a hot water tank at 40-50°C. It is best to use flowing hot water to brush the welding seam and the places where the residual flux and slag remain near the welding seam until it is cleaned up.
2. Immerse the weldment in the nitric acid solution. When the room temperature is above 25°, the concentration of the solution is 15% to 25%, and the immersion time is 10 to 15 minutes. When the room temperature is 10~15℃, the concentration of the solution is 20%~25%, and the immersion time is 15min.
3. Immerse the weldment in the tank of flowing hot water (temperature is 40-50℃) for 5-10min.
4. Rinse the weldment with cold water for 5 minutes.
5. Dry the weldment naturally, or dry it in a drying oven or dry it with hot air.