Why use aluminum profiles in new energy vehicles?
In recent years, the new energy vehicle industry has developed rapidly. Different from traditional vehicles, new energy vehicles use batteries as their power to drive. It is restricted by the weight of the power battery, the mileage of the power battery, and the high pressure of the automobile energy saving and emission reduction policy. So in terms of vehicle design and material applications, the lightweight body of the vehicles has become the first issue that car companies must consider. Therefore, battery-driven new energy vehicles require more weight reduction than traditional vehicles which also opened up broader market space for Lightweight materials such as aluminum.
What is the advantage of aluminum profiles?
Aluminum profiles are also named aluminum extrusion. Among the lightweight materials for automobiles, the comprehensive cost performance of aluminum alloy materials is higher than that of steel, magnesium, and plastics are composite materials, and it has relatively large advantages in terms of application technology, operation safety, and recycling. The density of aluminum is only 1/3 of that of steel, and its weight reduction and energy-saving effects are obvious, and it can better improve ride comfort under the premise of ensuring safety. At the same time, aluminum is easier to recycle. The comprehensive cost-effective advantages of aluminum determine that it becomes the best choice for automotive lightweight applications.
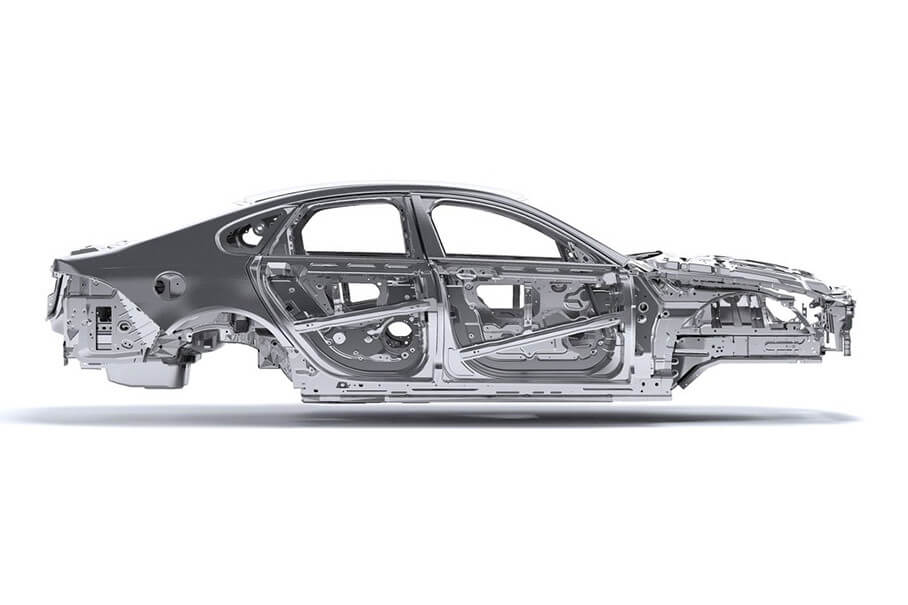
What are the applications of Aluminum profiles in the automotive industry?
The application parts of aluminum in new energy auto parts mainly include car body, wheel hub, chassis, anti-collision beam, power battery, and so on. According to the classification of processing forms, aluminum for automobiles is mainly divided into three forms: die-casting, extrusion, and rolling. Among them, the amount of die-casting parts account for about 80%, and the number of extrusion parts and rolling parts account for about 10%. Die-casting parts are mainly used for engines, wheel hubs, and other parts, extrusion parts are mainly used for cars, luggage racks, door beams, etc., and rolled parts are mainly used for the production of aluminum plates for car bodies. Here is an introduction to the aluminum car body, aluminum wheel hub, and aluminum chassis:
Aluminum profile in car body
The aluminum car body includes a vehicle frame made of high-performance aluminum profiles, a skin and doors made of high-precision aluminum plates. The all-aluminum car body is made of aluminum alloy extruded profiles. The world’s first aluminum alloy car body was the Audi A8 launched in 2011. The general vehicle frame assembly uses about 70 kinds of extruded profiles with different cross-sections. The quality of profile parts accounts for more than 80% of the total mass of the skeleton, plate parts account for 16.5%, and castings account for 2.8%, in addition, there are a small number of stamping parts. Extruded materials and punched parts are made of 6005A-T6 and 5005A alloys respectively, and castings are made of ZL301 alloy.
Aluminum profile in wheel hub
At present, the production methods of aluminum wheel hubs mainly include casting method, forging method, stamping method, and spinning method. Focusing on low-pressure casting, it gradually develops towards extrusion casting (liquid die forging) forming and semi-solid die forging forming. In terms of structure, there are various structural designs such as integral type and multi-piece combination type to meet the needs of use functions and markets.
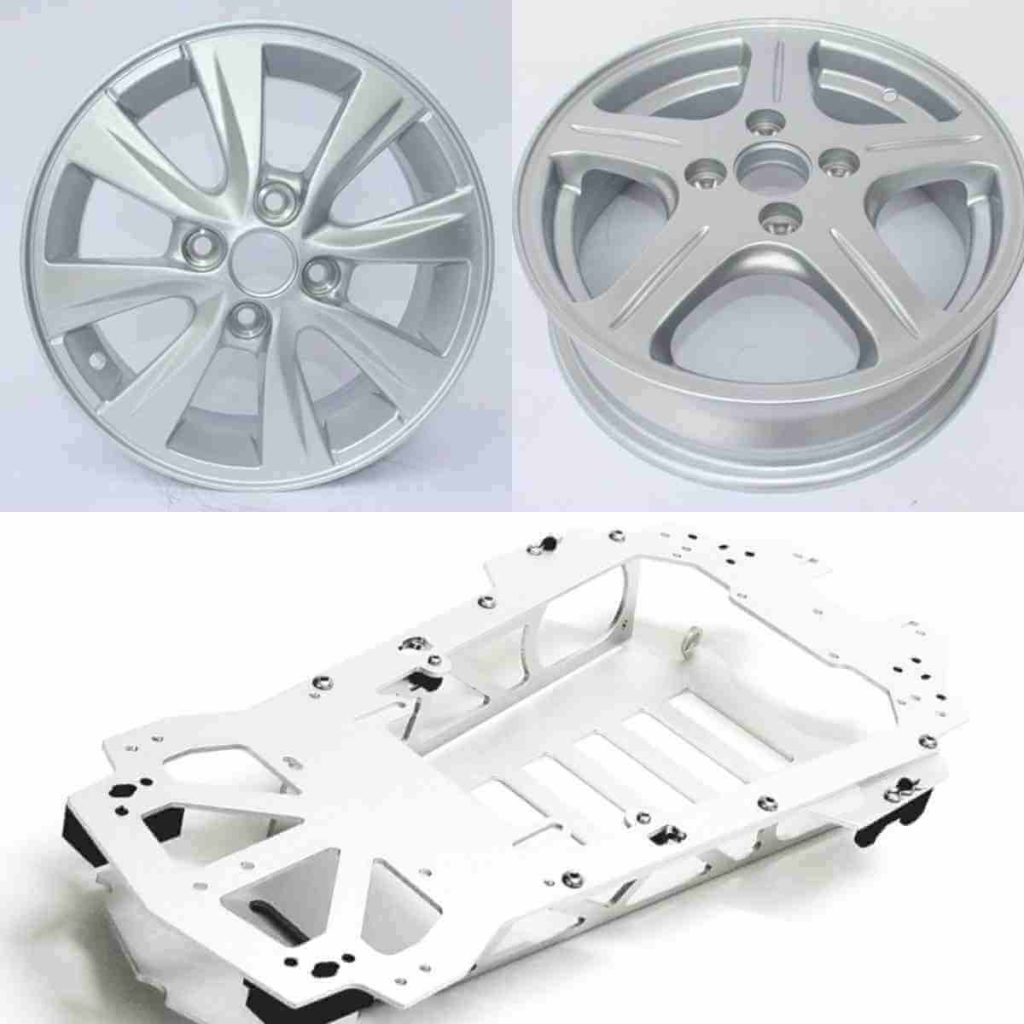
Aluminum profile in chassis
In an all-aluminum car, the chassis is also a large component. The Aluminum profile chassis must have high strength, corrosion and impact resistance, and excellent fatigue resistance. Chassis forgings are forged from 6082-T6 aluminum alloy, which can be manufactured by traditional casting-extrusion-roll forging-die forging-solid solution fire-artificial aging, or extrusion forging-die forging-solid solution Fire – Manufactured by artificial aging. The 6082 alloy is an Al-Mg-Si-Mn alloy developed by the European Aluminum Association and registered in the American Aluminum Association in 1972.
Besides the introduction above, when used as different components of the vehicle, the aluminum profile will use different production methods and present different excellent characteristics. If you want to get aluminum profile products, please feel free to contact us. CHAL is a professional aluminum profile supplier, our highly-skilled team has confidence in their ability to make the most complex aluminum profiles for a wide variety of industrial applications to satisfy your needs.