6061 aluminum is one of the most versatile and widely used aluminum alloys. It is known for its good mechanical properties, machinability, weldability, and corrosion resistance. 6061 aluminum is available in a variety of tempers, or heat treatments, each of which has its own unique properties.
Two of the most common tempers for 6061 aluminum sheet are T6 and T651. T6 aluminum has been solution heat treated and artificially aged, resulting in a high tensile strength and yield strength. T651 aluminum has been solution heat treated, artificially aged, and stress relieved, resulting in even better flatness and stability than T6 aluminum.
Both 6061 T6 and 6061 T651 aluminum sheets are commonly used in precision machining applications. However, T651 is often preferred for its improved flatness and stability. This makes it ideal for applications where tight tolerances and a high surface finish are required.

In this article, we will compare and contrast 6061 T6 and 6061 T651 aluminum sheets in more detail. We will discuss their mechanical properties, machinability, flatness and stability, corrosion resistance, and cost. We will also provide recommendations on which alloy is better suited for different precision machining applications.
Comparison of 6061 T6 and 6061 T651 Aluminum Sheets
Mechanical Properties
Mechanical properties are paramount in precision machining, as they influence the aluminum material’s performance and the durability of the machined parts.
- Tensile Strength: 6061 T651 tends to have slightly higher tensile strength compared to 6061 T6 due to its improved tempering process.
- Yield Strength: Similarly, the yield strength of 6061 T651 is typically higher, making it less prone to deformation during machining.
- Elongation: Both alloys exhibit good elongation, with 6061 T6 being marginally more ductile.
- Hardness: The hardness of T651 aluminum sheets is usually slightly higher, offering better wear resistance.
Machinability
Machinability is a critical factor in precision machining as it affects tool life, surface finish, and chip formation.
- Tool Wear: 6061 T6 has better machinability compared to T651, but the difference is not substantial. Tool life may be slightly shorter when machining T651 due to its increased hardness.
- Surface Finish: T651 sheets typically provide a superior surface finish due to their improved flatness and stability, making them a preferred choice for applications requiring an excellent surface finish.
- Chip Formation: Both alloys produce manageable chips, but T651 aluminum sheets often result in more consistent chip formation due to their enhanced flatness.
Flatness and Stability
One of the most significant distinctions between the two alloys is their flatness and stability.
- 6061 T6: These sheets have good flatness, but they may exhibit some degree of residual stress, which can cause distortion during machining.
- 6061 T651: T651 aluminum sheets are known for their exceptional flatness and stability. They undergo a stress-relieving process that minimizes distortion during machining, making them an ideal choice for precision applications.
Corrosion Resistance
Corrosion resistance is essential, especially when parts are exposed to harsh environments or chemicals.
- 6061 T6: This alloy provides good corrosion resistance, suitable for many applications. However, it may not be the best choice for highly corrosive environments.
- 6061 T651: T651 aluminum sheets offer slightly improved corrosion resistance compared to T6 due to their stress-relieving process. They are often chosen when corrosion resistance is a concern.
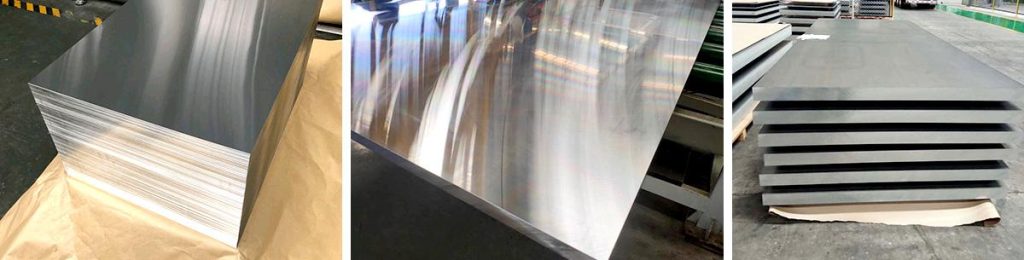
Which Alloy is Better for Your Precision Machining Needs?
- Mechanical Properties: If your application demands higher tensile and yield strength, opt for 6061 T651. For applications where ductility is more critical, 6061 T6 may suffice.
- Machinability: Consider the tool life and surface finish you require. If you prioritize surface finish and can manage tool wear, T651 may be the better choice. For rapid machining with less concern for surface finish, T6 is suitable.
- Flatness and Stability: When precision and minimal distortion are vital, as in aerospace or medical device manufacturing, 6061 T651’s superior flatness and stability shine.
- Corrosion Resistance: For applications in corrosive environments, the slight advantage in corrosion resistance of T651 makes it a safer choice.
Examples of Precision Machining Applications
6061 T6: This alloy is commonly used in the automotive industry for components requiring high strength and lightweight properties. It’s also favored for general-purpose machining where corrosion resistance isn’t a primary concern.
6061 T651: Aerospace components, precision instruments, and optical systems often utilize T651 aluminum sheets due to their exceptional flatness and stability. Medical devices and semiconductor manufacturing equipment also benefit from the improved surface finish.
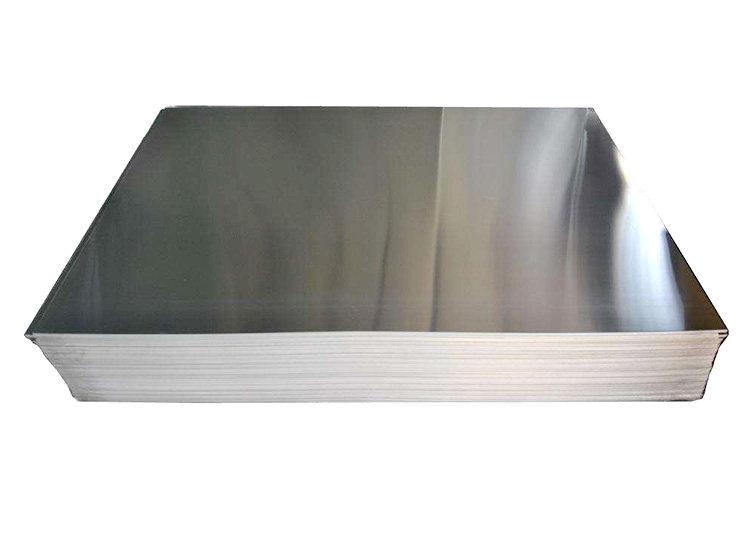
Conclusion
6061 T6 and 6061 T651 aluminum are both excellent alloys for precision machining. However, 6061 T651 aluminum is the better choice for high-precision applications where tight tolerances and a good surface finish are required. 6061 T6 aluminum is a good choice for applications where lower costs are a priority, or where the part does not require the same level of precision or performance as a part made from T651 aluminum.
When selecting an alloy for your precision machining needs, it is important to consider the specific requirements of your application. If you are unsure which alloy is right for you, consult with a qualified precision machining manufacturer.