Refrigeration is a vital part of our modern lives. Efficient refrigeration is crucial for both domestic and industrial applications, ensuring food preservation, medical storage, and various other essential functions. The quest for efficiency has led to numerous innovations, among which hydrophilic coated aluminum foil stands out. This article delves into why this material is indispensable for modern refrigeration systems, exploring its properties, benefits, and applications.
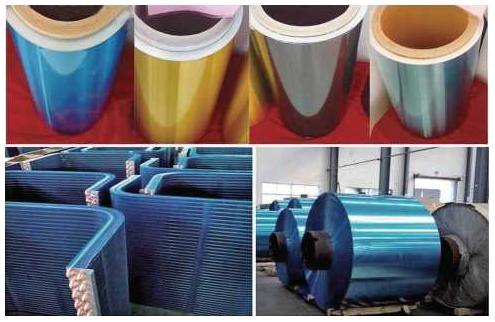
What is Hydrophilic Coated Aluminum Foil?
Regular aluminum foil is a great conductor of heat, which is why it’s commonly used in heat exchangers within refrigerators. However, standard foil struggles with water condensation. As moisture forms on the coils, it can bead up, reducing the surface area available for heat exchange.
Hydrophilic coated aluminum foil addresses this issue. A hydrophilic coating is a thin layer applied to the foil that makes it “water-loving.” This creates a surface where water condenses into a thin film instead of droplets.
Materials and Technology Used in Creating the Hydrophilic Coating
The exact materials used in hydrophilic coatings can vary depending on the manufacturer. However, they typically consist of microscopic particles or polymers that attract and spread water molecules. These coatings can be applied through various methods, such as spraying, dipping, or electrochemical processes.
How Does the Hydrophilic Coating Work?
The hydrophilic coating works by altering the surface tension of the aluminum foil. Water naturally forms beads on a hydrophobic (water-repelling) surface. In contrast, the hydrophilic coating creates a surface where water molecules spread out evenly, forming a thin film. This maximizes the contact area between the water vapor and the cooling coils, enhancing heat transfer.
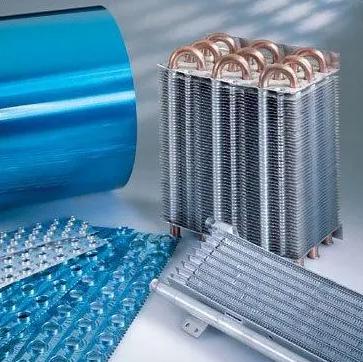
Advantages of Using Hydrophilic Coated Aluminum Foil in Refrigeration
Hydrophilic coated aluminum foil offers several significant advantages that enhance the efficiency and longevity of refrigeration systems. These benefits are pivotal for both domestic and industrial applications, ensuring optimal performance and cost savings.
1. Enhanced Heat Transfer Efficiency
One of the primary advantages of hydrophilic coated aluminum foil is its ability to improve heat transfer efficiency. The hydrophilic coating allows water to spread evenly across the surface, forming a thin film rather than water droplets. This uniform water film facilitates better thermal conductivity between the refrigerant and the air, leading to more efficient cooling. Improved heat exchange means that refrigeration systems can reach and maintain desired temperatures more quickly and with less energy consumption, enhancing overall efficiency.
2. Corrosion Resistance
Aluminum is naturally resistant to corrosion, but it can still oxidize over time, especially in moist environments. The hydrophilic coating provides an additional layer of protection against corrosion. By preventing direct contact between water and the aluminum surface, the coating helps to significantly reduce the risk of oxidation and corrosion. This protective barrier extends the lifespan of refrigeration components, reducing the need for frequent replacements and maintenance.
3. Reduction of Frost and Ice Formation
Frost and ice buildup on refrigeration components, such as evaporator coils, can impede airflow and reduce the system’s efficiency. The hydrophilic coating minimizes this issue by ensuring that any moisture that forms spreads into a thin film rather than accumulating as droplets. This thin water film is less likely to freeze into thick layers of ice, thereby reducing the frequency of defrost cycles required and maintaining optimal airflow and heat transfer.
4. Energy Efficiency
The combined effects of enhanced heat transfer and reduced frost formation lead to significant energy savings. When refrigeration systems operate more efficiently, they consume less electricity to achieve and maintain the desired cooling levels. This reduced energy consumption translates into lower operational costs for both households and businesses. Additionally, improved energy efficiency contributes to a lower environmental impact by reducing the carbon footprint associated with refrigeration.
5. Improved Air Quality and Hygiene
In refrigeration units, especially those storing food, maintaining good air quality and hygiene is essential. The hydrophilic coating helps by preventing the formation of large water droplets that can harbor bacteria and mold. By spreading moisture into a thin film that can evaporate more easily, the coating reduces the risk of microbial growth, thereby enhancing the cleanliness and safety of the stored products.
6. Reduced Noise Levels
Efficient heat transfer and reduced frost buildup can also contribute to quieter operation of refrigeration systems. When components work efficiently and without obstruction, the system operates more smoothly and quietly, providing a more comfortable environment in both domestic and commercial settings.
7. Longevity and Durability
The protective properties of the hydrophilic coating help to extend the overall lifespan of the refrigeration system. By minimizing corrosion and reducing the strain on components caused by frost buildup, the coating ensures that the system remains functional for a longer period. This durability reduces the need for frequent repairs and replacements, offering long-term cost benefits.
In summary, hydrophilic coated aluminum foil is an essential material in modern refrigeration systems due to its numerous advantages. It enhances heat transfer efficiency, offers corrosion resistance, reduces frost and ice formation, and improves overall energy efficiency. These benefits contribute to lower operational costs, better hygiene, quieter operation, and increased system longevity, making hydrophilic coated aluminum foil a critical component for efficient refrigeration.
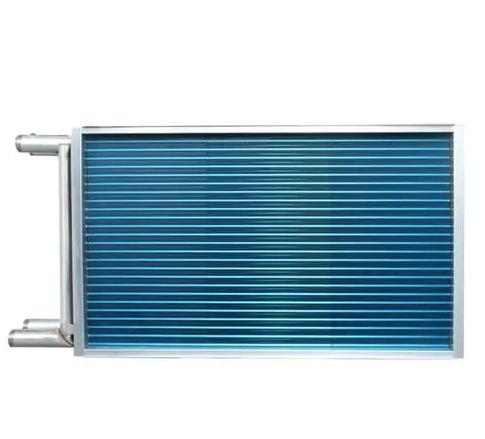
Applications in Refrigeration Equipment
Hydrophilic coated aluminum foil is utilized in various components of refrigeration systems, enhancing performance and efficiency. Here are the specific applications:
Application | Function | Benefits | |
Domestic Refrigeration | Evaporator Coils | Absorbs heat from the refrigerated space, allowing the refrigerant to evaporate | Better heat transfer efficiency, Reduced frost buildup, Enhanced cooling efficiency |
Condenser Coils | Releases heat absorbed from the refrigerated space to the outside environment | Maintains efficient heat dissipation, Reduced energy consumption | |
Drip Pans and Drain Lines | Collects and channels away condensate water from the refrigeration system | Smooth water flow, Reduced risk of blockages and bacterial growth | |
Commercial and Industrial Refrigeration | Air Conditioning Units | Utilized in heat exchangers | Improved heat exchange efficiency, Reduced maintenance needs |
Cold Storage Facilities | Preserves perishable goods | Efficient cooling, Reduced defrost cycles, Minimized energy consumption | |
Supermarket Display Cases | Maintains optimal temperatures for displayed products | Enhanced cooling performance, Reduced condensation, Improved visibility of products | |
Industrial Refrigeration Systems | Provides cooling for various industrial processes | Efficient heat transfer, Reduced system downtime, Longer lifespan, Reduced maintenance | |
Refrigerated Transport | Used in trucks and containers for transporting perishable goods | Improved temperature control, Reduced energy usage, Prevention of moisture-related issues | |
Specialized Applications | Medical Refrigeration Equipment | Stores vaccines, medications, and sensitive biological materials | Precise temperature control, Reduced risk of contamination |
Wine Coolers and Beverage Refrigerators | Stores wine and beverages at optimal temperatures | Enhanced cooling efficiency, Reduced condensation, Preserves flavor and quality |
In summary, hydrophilic coated aluminum foil plays a crucial role in various refrigeration applications, from household appliances to large-scale industrial systems. This structured table provides a clear overview of the specific applications of hydrophilic coated aluminum foil in refrigeration equipment, along with their functions and associated benefits, helping you know why hydrophilic coated aluminum foil is essential for efficient refrigeration.
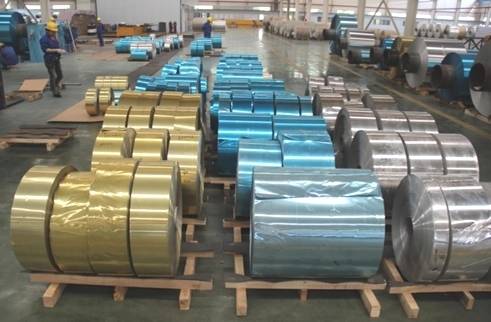
Maintenance and Cleaning Requirements for Hydrophilic Coated Aluminum Foil
Maintaining and cleaning hydrophilic coated aluminum foil is essential to ensure its longevity and effectiveness in refrigeration equipment. Here are the maintenance and cleaning requirements for hydrophilic coated aluminum foil:
Maintenance Requirements:
1. Regular Inspection:
Conduct periodic visual inspections of the hydrophilic coated aluminum foil to check for any signs of damage, wear, or corrosion.
Look for scratches, dents, or other surface imperfections that may compromise the integrity of the coating.
2. Handle with Care:
Handle the coated aluminum foil with care to avoid scratching or damaging the hydrophilic coating.
Use appropriate tools and techniques during installation and maintenance to minimize the risk of damage.
3. Preventive Measures:
Implement preventive measures to minimize exposure to harsh chemicals, abrasive materials, and physical impact.
Consider using protective coatings or barriers to shield the hydrophilic coated aluminum foil from potential sources of damage.
Cleaning Requirements:
1. Gentle Cleaning Products:
Use mild, non-abrasive cleaning agents and solutions specifically formulated for aluminum surfaces.
Avoid harsh chemicals, abrasive cleaners, or solvents that can damage the hydrophilic coating.
2. Soft Cleaning Tools:
Use soft cloths, sponges, or brushes with gentle bristles to clean the coated aluminum foil.
Avoid using abrasive scrubbers or cleaning pads that may scratch or abrade the surface.
3. Warm Water Rinse:
Rinse the coated aluminum foil with warm water to remove any loose debris, dust, or contaminants.
Ensure thorough rinsing to prevent residue buildup and maintain the effectiveness of the hydrophilic coating.
4. Gentle Wiping:
Gently wipe the surface of the coated aluminum foil with a damp cloth or sponge soaked in the cleaning solution.
Use light pressure and circular motions to remove dirt and stains without causing damage to the hydrophilic coating.
5. Drying:
After cleaning, thoroughly dry the coated aluminum foil with a clean, dry cloth or towel.
Ensure that no moisture remains on the surface to prevent water spots or streaks from forming.
6. Avoiding Abrasive Techniques:
Avoid using abrasive cleaning techniques such as scrubbing or scraping, as these can damage the hydrophilic coating and compromise its effectiveness.
7. Regular Maintenance Schedule:
Establish a regular maintenance schedule for cleaning the hydrophilic coated aluminum foil, taking into account the specific requirements of the refrigeration equipment and operating environment.
By following these maintenance and cleaning requirements, you can ensure that hydrophilic coated aluminum foil remains in optimal condition, contributing to the efficient operation and longevity of refrigeration equipment.
Conclusion
In essence, hydrophilic coated aluminum foil is more than just a material—it’s a critical component that plays a vital role in the efficiency, reliability, and sustainability of refrigeration systems. As the demand for energy-efficient and environmentally friendly cooling solutions continues to grow, the importance of hydrophilic coated aluminum foil in modern refrigeration technology cannot be overstated. If you are looking for a hydrophilic coated aluminum foil supplier, please feel free to contact CHAL. They are professional Aluminum Foil manufacturer and supplier. Believe you will get reliable products and services from them.