Imagine a building material that’s lightweight yet strong, insulating yet fire-resistant, and environmentally friendly. That’s the magic of aerated concrete, and a crucial ingredient in its creation is a seemingly mundane element – aluminum powder.
Aerated concrete, also known as Autoclaved Aerated Concrete (AAC), is a revolutionary construction material rapidly gaining popularity worldwide. Its unique properties, including low density, high thermal insulation, and excellent fire resistance, make it a versatile choice for various applications, from residential buildings and schools to hospitals and industrial facilities. But how does this seemingly airy material achieve such impressive properties? The answer lies in a chemical reaction triggered by a key element – aluminum powder.
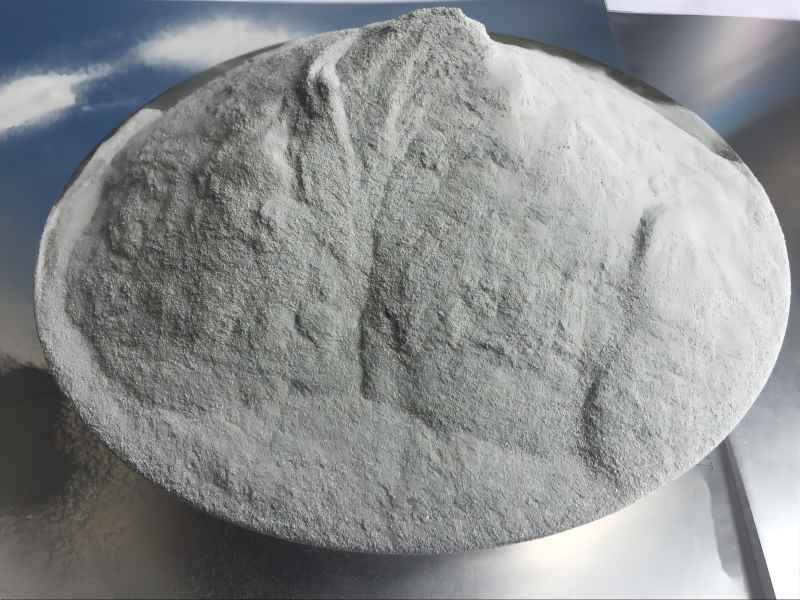
Aluminum Powder: The Foaming Agent Extraordinaire
In the production of both aerated concrete and AAC blocks, aluminum powder plays the role of a foaming agent. When mixed with the concrete slurry containing cement, lime, and other ingredients, the aluminum powder reacts with the alkaline environment, typically through a reaction with calcium hydroxide (lime). This reaction generates hydrogen gas, which gets trapped within the mixture, forming countless tiny air pockets throughout the material. These air pockets are the secret behind aerated concrete’s remarkable properties:
- Lightweight: The air pockets significantly reduce the overall density of the material, making it much lighter than traditional concrete. This translates to easier handling during construction and reduced structural loads on buildings.
- Excellent Insulation: The air pockets act as natural thermal barriers, trapping air and preventing heat transfer. This makes aerated concrete a superior insulator compared to traditional concrete, leading to improved energy efficiency and reduced heating and cooling costs.
- Fire Resistance: The air pockets also act as barriers against fire, slowing down the spread of flames and heat. This makes AAC blocks a valuable material for fire-resistant construction, especially in high-rise buildings and public spaces.
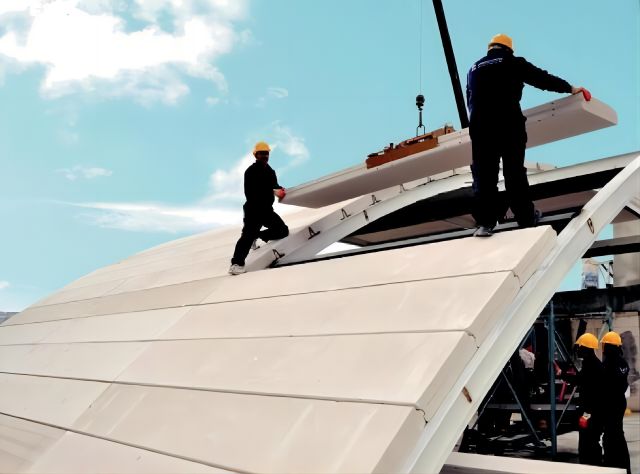
Aluminum Powder for Aerated Concrete: Unveiling the Similarities
While the terms “aerated concrete” and “AAC block” might seem distinct, they essentially refer to the same material with one key difference – production scale. Aerated concrete is often used for smaller projects or customized applications, while AAC blocks are produced in prefabricated, standardized sizes for larger-scale construction projects.
- Fine Particle Size: The aluminum powder needs to be finely ground to ensure even distribution throughout the mixture and efficient gas generation. This leads to a more uniform and consistent final product.
- High Purity: Impurities in the aluminum powder can affect the reaction with the alkaline environment, potentially compromising the quality and strength of the final material. Therefore, high-purity aluminum powder is essential for reliable performance.
- Specific Flake Shape: Flaky aluminum particles tend to react more readily with the alkaline solution compared to spherical ones, leading to faster and more efficient gas generation. This property is crucial for both small-scale and large-scale production.
Aluminum Powder for Aerated Concrete: Potential Differences
While the aluminum powder itself is essentially the same for aerated concrete and AAC blocks, there might be some slight variations in its use depending on the production context:
- Dosage: The specific amount of aluminum powder required can vary depending on the desired density and strength of the final product. Smaller projects using aerated concrete might allow for more flexibility in adjusting the dosage, while AAC block production often involves precise calculations to ensure consistent properties across large batches.
- Mixing Methods: Small-scale aerated concrete projects might rely on manual mixing techniques, while large-scale AAC block production often utilizes sophisticated automated mixing systems to ensure uniform distribution of the aluminum powder and other ingredients.
The Bigger Picture: Aluminum Powder and Sustainability
The use of aluminum powder in aerated concrete and AAC blocks offers several environmental benefits, including:
- Reduced Material Consumption: The lightweight nature of aerated concrete allows for thinner walls and lighter structures compared to traditional concrete, leading to a decrease in overall material consumption.
- Improved Energy Efficiency: The excellent thermal insulation properties of aerated concrete contribute to reduced energy consumption for heating and cooling buildings, ultimately lowering greenhouse gas emissions.
- Potential for Recycled Aluminum: While virgin aluminum is typically used in construction applications, research is underway to explore the feasibility of using recycled aluminum powder in aerated concrete production. This could further reduce the environmental footprint of the material.
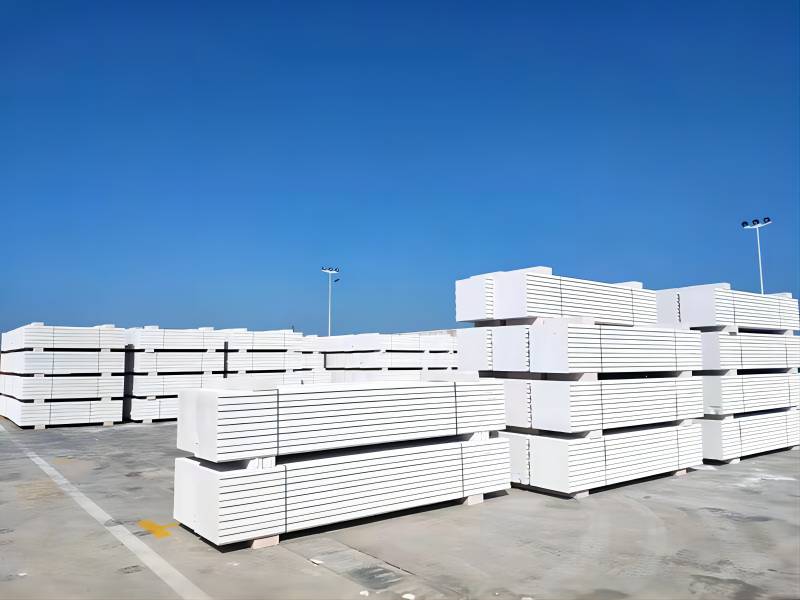
Conclusion: A Powdery Powerhouse for Building the Future
Aluminum powder may seem like a humble ingredient, but its role in the creation of aerated concrete and AAC blocks is truly transformative. This versatile material offers a sustainable and efficient alternative to traditional concrete, paving the way for a future of greener, more energy-conscious construction. As technology and research continue to advance, the potential of aluminum powder in innovative building materials like aerated concrete is only set to grow, shaping the skylines of tomorrow.