The modern air conditioner, a ubiquitous marvel of human ingenuity, has revolutionized thermal comfort and reshaped our built environment. At the heart of this cooling prowess lies a seemingly simple material – aluminum foil. While often relegated to the realm of kitchen duty, aluminum foil plays a crucial role in enhancing the efficiency, performance, and durability of air conditioners. This article delves into the multifaceted applications of aluminum foil in these essential climate control systems and dissects its intricate contributions.
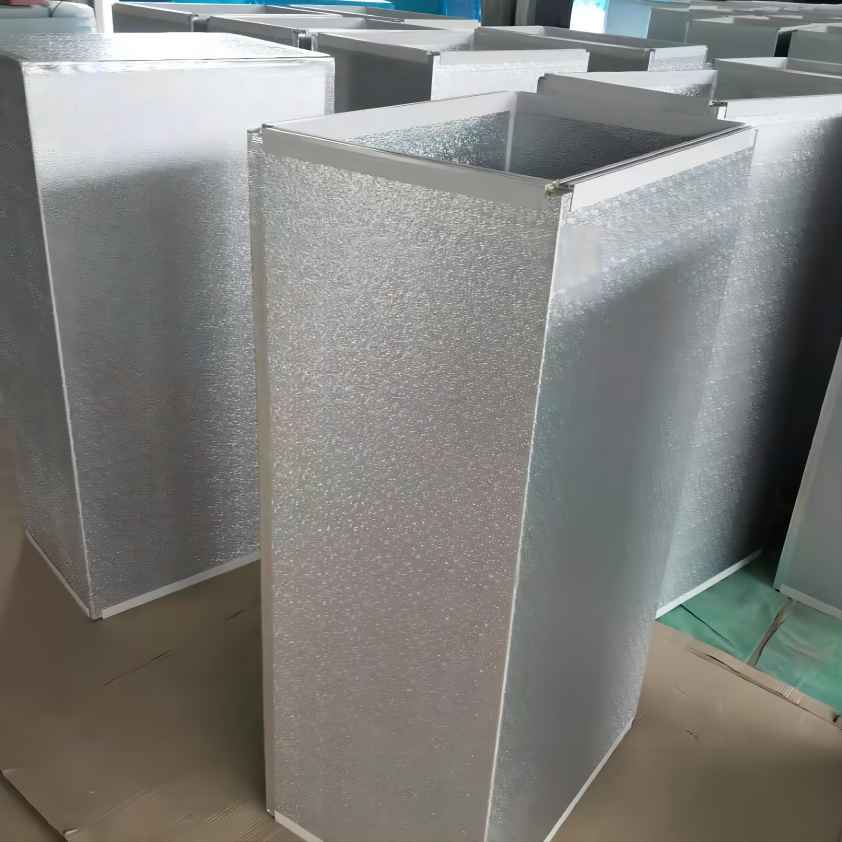
Types of Aluminum Foil for Air Conditioners
The utilization of aluminum foil within air conditioners is not a singular approach; rather, it employs two distinct variants, each tailored for specific functions:
1. Hydrophilic Aluminum Foil
This specially engineered foil boasts a microscopically modulated surface that promotes the formation and uniform distribution of thin water films across the evaporator coil. This enhanced wettability optimizes contact between the refrigerant and the water film, leading to several crucial advantages:
- Augmented Heat Transfer: The increased surface area of the water film facilitates rapid heat absorption from the refrigerant, significantly boosting the cooling capacity of the evaporator.
- Nucleate Boiling Enhancement: The microstructured surface promotes the formation of numerous nucleation sites for refrigerant bubbles, further accelerating heat transfer and reducing refrigerant charge requirements.
- Reduced Thermal Resistance: The thin water film minimizes thermal resistance between the refrigerant and the coil, further improving heat transfer efficiency.
2. Bare Aluminum Foil
This conventional foil variant reigns supreme in the construction of fins for both evaporator and condenser coils. Its thin, corrugated profile serves two primary purposes:
- Extended Heat Transfer Surface: The corrugated design dramatically increases the surface area exposed to the surrounding air, enabling efficient heat exchange between the refrigerant within the coil and the ambient environment.
- High Thermal Conductivity: The inherent thermal conductivity of aluminum facilitates rapid heat transfer from the refrigerant within the coil to the air in the evaporator or from the air to the refrigerant in the condenser.
The selection of foil type depends on the specific function and desired performance characteristics. Hydrophilic foil excels in maximizing heat transfer within the evaporator, while bare aluminum foil prioritizes efficient heat exchange with the surrounding air. Both variants contribute significantly to the overall cooling performance and energy efficiency of air conditioners.
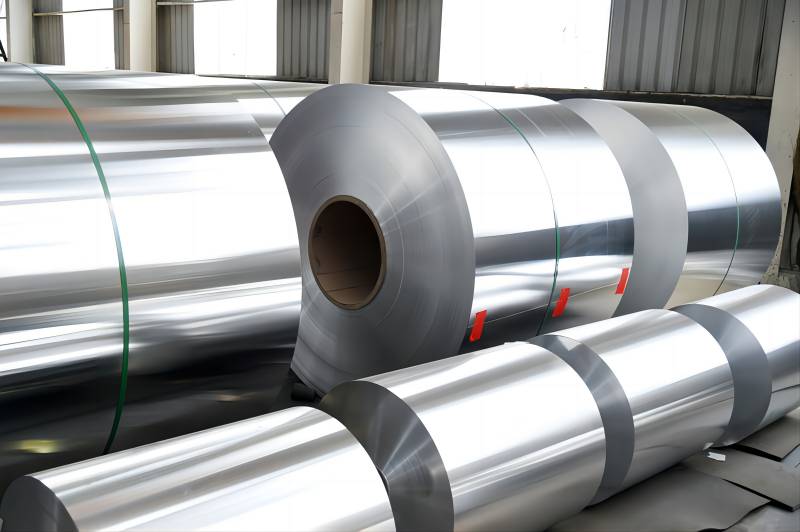
Applications of Aluminum Foil in Air Conditioners
The versatility of aluminum foil extends beyond its primary role in the evaporator and condenser coil fins, contributing to various aspects of air conditioner performance and efficiency. Let’s delve into these diverse applications:
1. Evaporator Coil Fins
This constitutes the most prevalent application of aluminum foil in air conditioners. The corrugated fins significantly increase the surface area of the evaporator coil, facilitating enhanced heat transfer between the refrigerant and the surrounding air. This translates to:
- Improved Cooling Capacity: The expanded surface area allows for greater absorption of heat from the warm indoor air, leading to more efficient cooling.
- Reduced Refrigerant Charge: The optimized heat transfer enables efficient cooling with less refrigerant, minimizing environmental impact and operational costs.
2. Condenser Coil Fins
Similar to the evaporator, aluminum foil fins on the condenser coil maximize the surface area exposed to the ambient air. This facilitates efficient heat rejection from the hot refrigerant to the environment, resulting in:
- Enhanced Cooling Efficiency: The effective heat dissipation improves the overall cooling cycle, leading to better performance and reduced energy consumption.
- Improved System Stability: Efficient heat rejection prevents overheating of the refrigerant and compressor, enhancing system reliability and lifespan.
3. Thermal Insulation
Strategic placement of aluminum foil within the air conditioner unit serves as a valuable thermal barrier. Its inherent reflective properties mitigate radiant heat transfer, contributing to:
- Reduced Heat Gain: The foil reflects unwanted heat back towards its source, minimizing heat absorption by internal components and reducing the cooling load on the system.
- Improved Energy Efficiency: This thermal insulation translates to lower energy consumption and operating costs.
4. Ductwork Applications
Aluminum foil plays a crucial role in optimizing airflow and minimizing noise within the ductwork system. Its properties offer several benefits:
- Reduced Condensation: The smooth surface of the foil minimizes moisture build-up within the ducts, preventing condensation and potential water damage.
- Improved Airflow Efficiency: The low friction coefficient of the foil allows for smoother air passage, reducing energy losses and ensuring efficient delivery of cooled air throughout the building.
- Noise Reduction: The sound dampening properties of aluminum foil help to attenuate noise generated by the air conditioner’s fan and compressor, creating a quieter environment.
These diverse applications showcase the multifaceted role of aluminum foil in air conditioners. Its ability to enhance heat transfer, provide thermal insulation, optimize airflow, and reduce noise contributes significantly to the overall performance, efficiency, and comfort provided by these essential climate control systems.
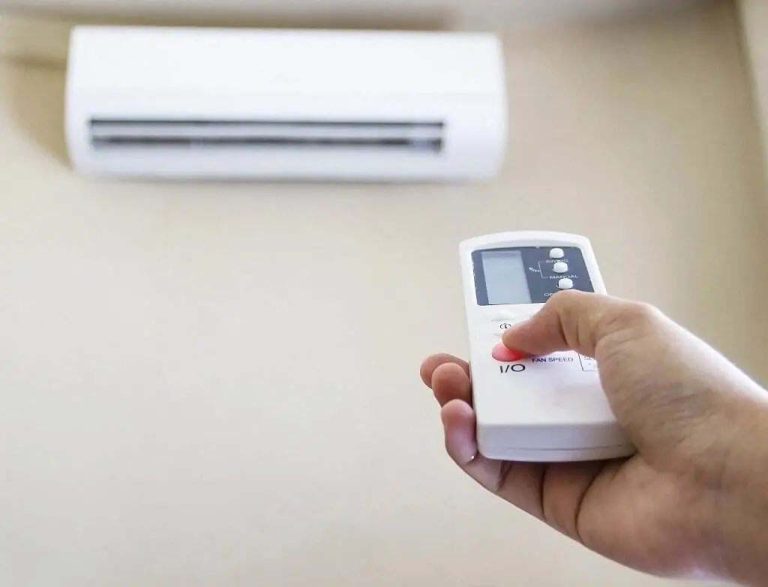
Benefits of Utilizing Aluminum Foil in Air Conditioners
The incorporation of aluminum foil in air conditioners extends beyond mere material choice; it delivers a multitude of benefits that contribute to enhanced performance, durability, and cost-effectiveness. Let’s delve deeper into these advantages:
1. Enhanced Efficiency and Performance
The high thermal conductivity and surface area expansion provided by aluminum foil fins in the evaporator and condenser coils facilitates rapid heat exchange between the refrigerant and the surrounding air. This translates to:
- Increased Cooling Capacity: Efficient heat absorption from the warm indoor air in the evaporator and heat rejection to the environment in the condenser lead to improved cooling performance.
- Reduced Energy Consumption: The optimized heat transfer process minimizes the need for excessive compressor operation, resulting in lower energy consumption and operating costs.
2. Durability and Corrosion Resistance
Aluminum foil exhibits inherent resistance to corrosion and weathering, making it ideal for the demanding environment within air conditioners. This translates to:
- Extended Lifespan: The robust nature of aluminum foil minimizes degradation and wear, contributing to a longer lifespan for air conditioner components.
- Reduced Maintenance: The corrosion resistance of aluminum foil reduces the need for frequent maintenance and component replacements, lowering overall operational costs.
3. Cost-Effective Solution
Compared to alternative materials like copper or stainless steel, aluminum foil offers a significantly more cost-effective solution for air conditioner manufacturers. This contributes to:
- Competitive Pricing: The use of aluminum foil allows for the production of more affordable air conditioners, making them accessible to a wider consumer base.
- Improved Market Penetration: The cost-efficiency of aluminum foil incentivizes manufacturers to adopt this material, leading to broader market penetration and increased availability of energy-efficient cooling solutions.
4. Lightweight and Easy to Install
Aluminum foil is lightweight and malleable, making it easier to fabricate into intricate fin shapes and readily adaptable to various air conditioner designs. This translates to:
- Simplified Manufacturing: The ease of working with aluminum foil facilitates efficient production processes for air conditioner manufacturers.
- Reduced Installation Costs: The lightweight nature of aluminum foil simplifies installation and handling, potentially lowering labor costs associated with air conditioner installation.
By employing aluminum foil, air conditioner manufacturers can reap numerous benefits, encompassing increased efficiency, enhanced durability, cost-effectiveness, and ease of installation. This multi-faceted approach ultimately translates to improved performance, reduced environmental impact, and broader accessibility of these essential climate control systems.
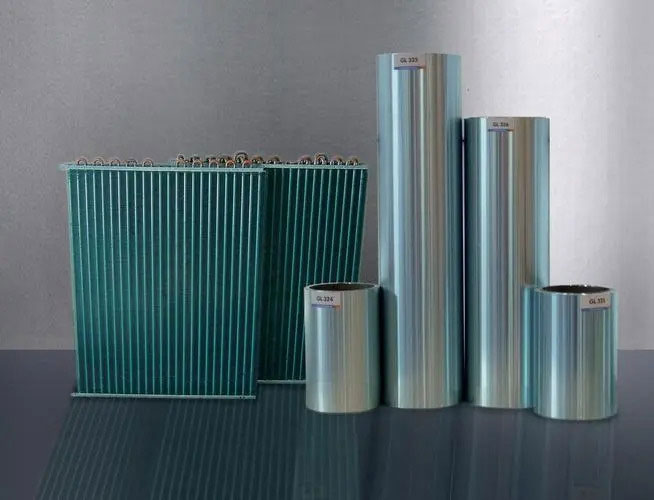
Conclusion
In conclusion, the utilization of aluminum foil within air conditioners transcends its humble appearance. Its diverse applications, encompassing enhanced heat transfer through optimized fin surfaces, effective thermal insulation via radiant heat reflection, and noise mitigation within ductwork, significantly contribute to the performance, efficiency, and longevity of these ubiquitous climate control systems. As the pursuit of ever-increasing cooling efficacy and environmental sustainability intensifies, aluminum foil stands poised to remain an indispensable ally in the ongoing battle against sweltering temperatures, ensuring a comfortable and energy-efficient future for generations to come.