Seamless aluminum tubes have become an indispensable material in many industries due to their lightweight, high strength, and corrosion resistance characteristics. From aerospace and automotive engineering to the demand in the construction industry, these pipes play a crucial role. In order to meet the strict requirements for high precision and performance in these applications, meticulous control of the entire seamless aluminum tube production process is crucial. This article delves into the key steps involved in achieving this precision and their impact on the final product.
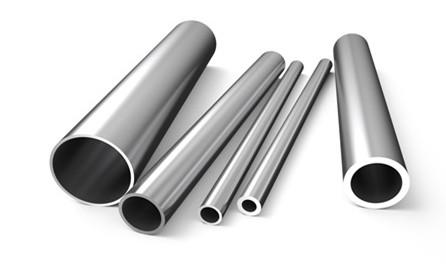
1. Material Selection and Casting
Choosing the right materials is the cornerstone of the entire production process. Different applications have different performance expectations for aluminum tubes. For example, the aerospace industry, which is crucial for high strength and excellent corrosion resistance, may favor high-strength aluminum alloys such as 7075 or 6061. In contrast, the construction industry may prioritize the formability and ease of processing of pipes.
Melting and casting are the initial steps in the production of seamless aluminum pipes. At this critical stage, precise control of aluminum alloy composition and melting temperature is crucial to ensure the quality of the ingot. Deviations from the required components may introduce impurities and defects into the ingot, thereby damaging the accuracy and performance of the subsequently produced pipes. In addition, precise control of melting temperature is also crucial. Excessive temperature can have a negative impact on the microstructure and mechanical properties of the ingot, while too low temperature can hinder the complete melting of the alloy.
2. Homogenization Treatment of Ingots
Even after melting and casting, ingots often exhibit inconsistencies in composition and microstructure. In order to improve the overall quality of the ingot, homogenization treatment is adopted. This treatment involves heating the ingot to a specific temperature and maintaining it for a predetermined duration at that temperature. The purpose of this process is to make the composition and microstructure of aluminum alloy uniform, thereby improving the mechanical properties and machinability of the ingot.
The success of homogenization treatment depends on precise control of temperature and holding time. Excessive temperature or prolonged insulation time may cause the ingot to overheat and may result in new defects. On the contrary, insufficient temperature or holding time may not achieve the required uniformity.
3. Extrusion Mold and Perforation Pin Positioning
Extrusion is one of the most critical stages in the production of seamless aluminum tubes. During this process, it is necessary to carefully align the extrusion cylinder, mold, perforated pin, and spindle. The accuracy of this alignment directly affects the dimensional accuracy and surface quality of the final pipe. Any deviation from proper alignment may result in inconsistent pipe dimensions and surface defects.
Another key factor is the precise positioning of the perforation needle. The pin plays a crucial role in forming the hollow aspect of the seamless tube during the extrusion process. Inaccurate positioning of the perforation needle may hinder the perforation process or lead to the formation of cracks and other defects inside the tube.
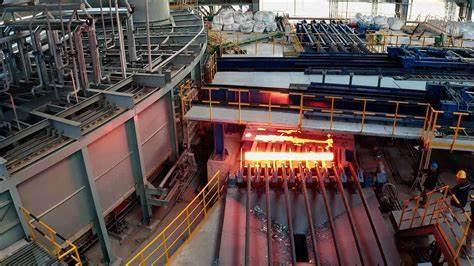
4. Cooling Treatment
After extrusion, the newly formed pipe is cooled to solidify its shape and determine its final size. Water cooling is a commonly used method for this purpose, which can ensure rapid and effective cooling of pipes. The cooling rate at this stage significantly affects the performance and microstructure of the tube.
A very rapid cooling process can cause residual stress to form inside the pipe, ultimately affecting its mechanical performance. On the contrary, a slow cooling process may lead to unstable size of the final pipe. Therefore, achieving the optimal cooling rate is crucial.
5. Stretching and Artificial Aging
In some applications, it may be necessary to further enhance the performance of seamless aluminum pipes. Drawing is the process of achieving this goal. By changing the microstructure of pipes through drawing, their strength and hardness can be improved. However, it must be acknowledged that drawing can also lead to a decrease in the ductility of pipes. Therefore, it is necessary to carefully customize the drawing process according to the specific requirements of each application.
After the stretching process, manual aging is usually performed to eliminate residual stresses introduced during the stretching process and further improve the mechanical properties of the pipe. This usually involves keeping the tube at a specific temperature for a predetermined period of time. This holding time allows for changes in the microstructure of the tube, ultimately leading to stable performance.
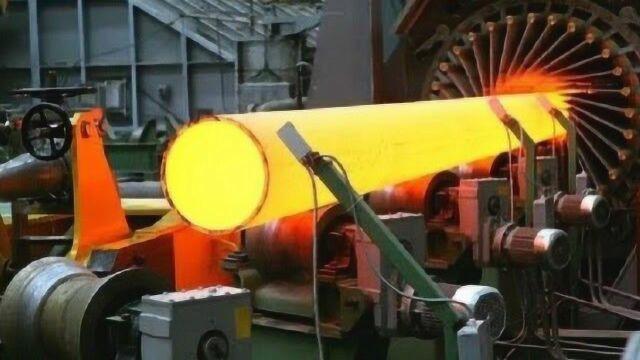
Conclusion
The production of seamless aluminum tubes is a complex process involving a series of interrelated steps, each of which plays a crucial role in ensuring that the final product meets the high standards required for aerospace, automotive, and building applications. The art and science behind this process require a profound understanding of the principles of materials science, thermodynamics, and mechanical engineering. With the continuous advancement of technology, methods and equipment for producing seamless aluminum pipes are also constantly evolving, with the potential to provide more advanced materials, enabling engineers to design and construct structures that can meet future challenges.