Aluminum foil is often used in material packaging because of its good freshness, moisture resistance and corrosion resistance. However, in real life, aluminum foil often produces many large pinholes. Once the diameter of pinholes is greater than 5 and reaches 1000 per square meter, it will directly affect the quality of packaging. The pinhole is a measure of aluminum foil quality index, it must be controlled within a certain range.
2 Reasons Might Cause Pinholes in Aluminium Foil
There are two main factors that might cause pinholes in aluminium foil, which are material and processing methods.
1. Materials
- Improper Chemical Composition of Materials Will Lead to False
The Fe and Si contents in aluminum foil will directly affect the generation of pinholes. If Fe>2.5, Al and Fe are easy to form coarse intermetallic compounds. Aluminum foil is prone to pinhole when calending, and Fe and Si will interact with each other to form a firm compound. The number of pinholes of 1060 pure aluminum foil is much greater than the number of pinholes of 1035 Foil, because the Fe and Si content of 1035 pure aluminum is much higher than that of 1060. But when the Ti content in aluminum foil >O.05, it is easy to form hard TiB2 compound, brittle when rolling, which will also lead to a lot of pinholes.
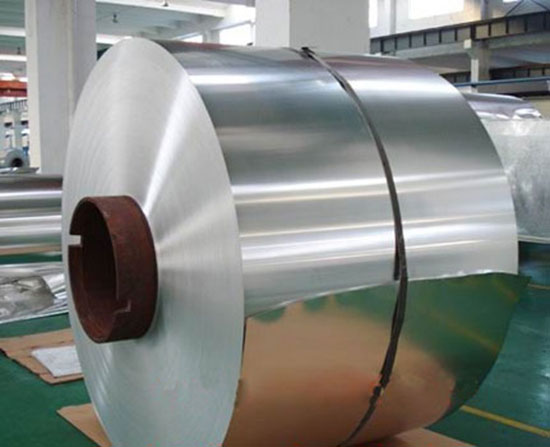
- The Level of Materials Surface
The surface of the billet is scraped, or there are serious corrosion spots and metal pressing on the surface. These problems will produce more large and small pinholes or even holes with the thinning of the thickness during rolling.
- Casting Process of Materials
This mainly includes casting will be some external particles and dust involved in the rolling of the pinhole, and there are bubbles and oxide film when casting. As the rolling thickness becomes thinner and thinner, the bubbles are crushed into pinholes and the oxide film finally falls off from the foil surface to form pinholes.
2. Processing Methods
- Tension
When the post-tension is too large, the front slip value is greatly reduced, which is easy to lead to the roller is not consistent with the aluminum foil. If the surface of the aluminum foil slips at this time, it will twist the surface, greatly increasing the probability of pinhole.
- Rolling oil
There are some small solid particles in the rolling oil, which can easily lead to aluminum foil pinhole. To remove these particles must be filtered, but in the actual filtration, it is easy to appear that the ash content of rolled oil exceeds a certain range, which is easy to lead to pinholes. In addition, the flow of oil through the filter must be greater than the flow of cooling oil, but in fact, often appear dirty oil backflow, rolling oil viscosity is too large, and eventually make the aluminum foil pockmarked surface is very rough, the rougher it is more likely to lead to pinhole.
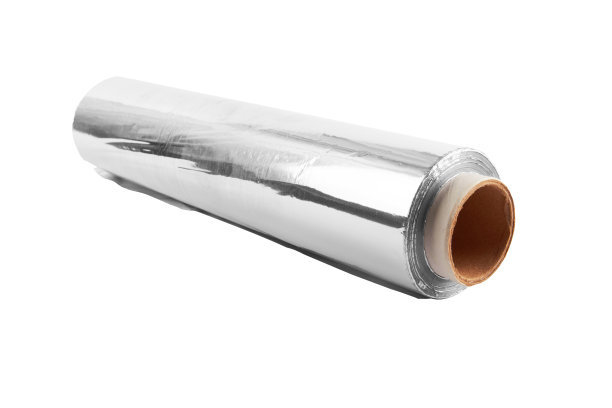
Aluminum Foil Pinhole Preventive Measures
1. Control casting and rolling process
(1) Control chemical composition
The chemical composition of aluminum foil must conform to the relevant production standards and specifications, in order to better control the subsequent process. Therefore, it is necessary to control the exact content of Fe, Ti and Si elements to ensure the appropriate alloying element content.
(2) Control the melt in the mixing casting and rolling process
In casting and rolling, each stirring time should be 7min ~ 8min, and the best time interval is LH ~ 2h. Each manufacturer shall establish effective supervision methods.
(3) Degassing and alkali metal control
At present, it is best to use argon + chlorine gas mixture refining method, and conduct argon gas degassing refining in melting furnace and holding furnace, the degassing effect is good, hydrogen content can reach 0.12mL/100gAl below, and alkaline metal can also be fully controlled.
(4) Filtration process control
Filtration must be all-aluminum liquid filtration. The key point is to implement whether all-aluminum liquid, inspection, supervision, replacement and assessment are the top priority to ensure the quality of filtration. Guangxi Nanan aluminum foil Co., Ltd. uses the most advanced tubular ceramic filter tubes for filtration, and the filtration effect is very good.
(5) Segregation control
Segregation defects of L ××× series aluminum alloys are generally less. But in 8××× series aluminum alloy is more frequent, casting and rolling speed is slightly faster, segregation will appear, the faster the speed, the more serious segregation. Generally speaking, segregation defects can be well controlled when the velocity is reduced.
(6) Slag hanging defect control
Slag hanging defects can be controlled from the following aspects:
Do the above refining and filtering work, so that the content of impurities in liquid aluminum is as low as possible; Ensure the temperature of liquid aluminum, so that there is no abnormal condensation phenomenon; Ensure the integrity of the casting nozzle, do not use the damaged casting nozzle; Adjust the gap between the casting nozzle and the roller; Speed up slag running with the same production cycle.
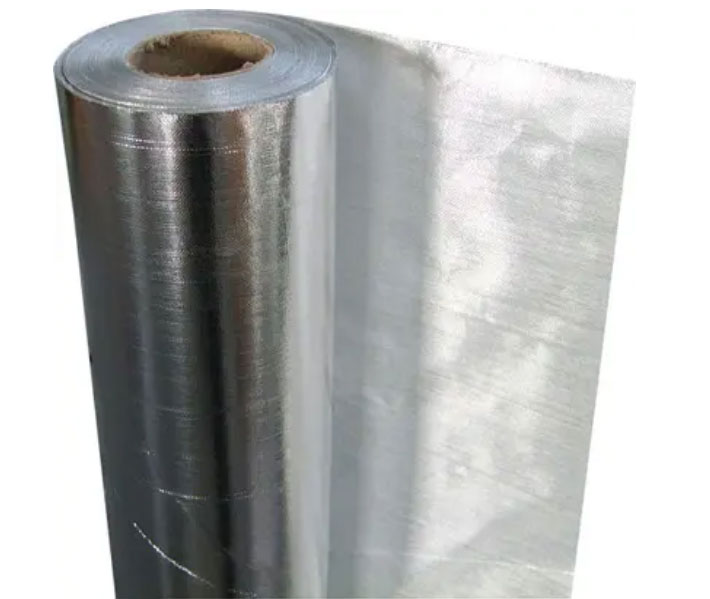
2. Control calendering process
(1) rolling oil quality
Rolling oil is particularly prone to problems, so the control of rolling oil is very important.
① Prevent hydraulic oil leakage of rolling mill
Once the hydraulic oil leaks into the rolling oil, the viscosity of the rolling oil will rise. The residue increases, the transmittance decreases, and the efficiency of the purging device decreases when rolling, which increases the residual aluminum powder and impurity particles on the surface of the aluminum coil, thus increasing the probability of pinhole generation.
Preventive measures:
A) Do a good job of leak detection of the equipment. If the oil level drops abnormally, the machine will be stopped for inspection, and the machine will be started after repair;
B) Using unstained hydraulic oil, although the price is high, it has little influence on product quality;
C) The total amount of leakage shall be controlled. The monthly leakage shall not exceed 200L. When the leakage exceeds 15 barrels, the oil shall be completely changed.
② Rolling oil filtration control
Filtering cannot be ignored. The type and usage of filter aid and clay should be adjusted according to different passes, different products and different machines, so that the filtration work is periodic and regular.
General principles:
A) The cold mill uses coarse filter aid to ensure flow, and the foil mill uses fine filter aid to ensure filtration accuracy;
B) After the two passes of cold rolling and the first two passes of foil rolling, the filtration cycle should be appropriately shortened due to the large amount of aluminum powder produced and the slightly larger amount of clay used.
C) Monitoring filter shall be used. The filter core shall generally be 3m ~ 5m, and it shall be replaced every three months under normal production conditions.
③ Control of spraying amount of rolling oil
In order to ensure the spraying amount of rolling oil, the following improvement measures can be formulated:
A) Try to control the shape well l ~ 3 passes before foil rolling;
B) One pass and one pass before stacking shall be combined with automatic spraying, and the spraying opening time of each nozzle shall be more than 20% by manual control mode:
C) Maintain good lubrication performance index of oil products.
(2) Control of adhesion and scratches
These two defects occur from time to time in almost all aluminum processing plants, resulting in black bars, string holes or holes during the rolling process. Improvement measures:
① Improve the intermediate annealing process, for a certain product, according to its specifications and alloy type, develop a special process;
② Aluminum coil is best tied with aluminum tape when annealing. After annealing, aluminum coil must be stored overhead to prevent local heat can not be distributed, resulting in aluminum sticking:
③ Keep the rolling channel clean and clean the rolling mill regularly;
④ Roller grinding must be carried out in strict accordance with the standard process, and the grinding time of a pair of foil rollers is generally between 2.5h and 4.0h. The grinding time is short, rough grinding may not be carried out, the last fatigue layer is not ground off (even the last scar is not ground off), such a roll is easy to be injured, the service life is very short; If the grinding time is too long, many short scratches (about 2mm ~ 3mm) will be formed on the roller surface, so it is very important to set the grinding time strictly. In the inspection of the roll, it is better to print the roughness pattern of the platform rather than the peak, so that the roughness of the roll can be maintained for a longer time, and it is not easy to be injured.
(3) Production environment improvement
Workshop air to maintain positive pressure; Double doors for personnel access, with transition area; Section for rolling mill, scuttling, annealing and packaging, with isolation; Equipped with anti-mosquito lamps; Floor brush floor paint.
The first three points above are particularly important.
(4) Casting and rolling roll homogenization annealing
The aim of homogenizing annealing is to treat the non-equilibrium Fe and Mn phases in aluminum alloy. In the homogenization annealing process, the non-equilibrium (AlFeSi) phase and FeAl6, FeAlm. The phase gradually dissolves and transforms into the equilibrium (AlFeSi) phase and FeAl3 phase respectively, while the original (AlFeSi) phase and FeAl3 phase grow up. MnAl6 in the eutectic. In the process of homogenization at high temperatures and long time, phase tends to change from non-equilibrium crystallization to equilibrium state and gradually dissolve into matrix. And the nascent MnAl6. The shape of phase is irregular block or sheet, and its sharp corner can be dissolved and spheroidized under certain conditions, which can reduce the risk of cracking during rolling. Improvement of homogenizing annealing process:
- Ensure that the homogenization annealing temperature of aluminum alloy cast-rolled coil is between 570℃ ~ 600℃, the best is 580℃, and the holding time is generally controlled within 10h ~ 13h according to the size of the coil and the amount of furnace loading;
- The homogenization annealing of aluminum alloy with more Fe and Mn elements has a good effect;
- Generally, the casting and rolling coil is annealed directly or after cold rolling. In addition, a metallographic microscope with photography is added to analyze the morphology, distribution and size of pinholes in each inspection and establish pinhole files for each batch of products, which is of great help to the control of pinholes.
Among are the report on how CHAL dealt with pinhole issues during Aluminium foil production, we have a professional team to analyze this kind of problem, to accelerate the speed of our production, in order to shorten the time for our customers to get our products. You can put 100% of your faith in us, please do not hesitate to contact us.