When metal is extruded, as the temperature rises, the non-uniformity of metal fluidity will increase. During the entire extrusion process, the temperature of the ingot in the deformation zone also gradually increases, and the faster the extrusion speed, the higher the temperature, and the temperature rise can reach about 100C.
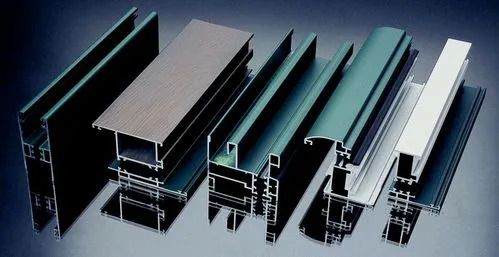
When the metal temperature in the deformation zone exceeds the maximum permissible critical deformation temperature, the metal will enter a hot brittle state and form extrusion cracks. Therefore, when the ingot temperature is high, the extrusion speed must be gradually reduced during the extrusion process. The 6063 aluminum alloy ingot is generally preheated to 480~520C, and the extrusion barrel is preheated to 400~450C.
So, what are the factors that affect the extrusion speed of aluminum profiles? Besides,3 extrusion processes are used to improve extrusion speed.
3 Factors for Extrusion Speed of Aluminum Profiles
1. Profile shape
The impact of size and shape The external dimensions and geometry of the concave profile have a significant effect on the metal outflow velocity of the extruded product.
For aluminum profiles, the geometric shape of the product is simple, the symmetry is good, and the product with a small width-thickness ratio can be relatively higher; on the contrary, the extrusion speed of the product with complex geometry, large width-thickness ratio, large wall thickness difference, and poor symmetry should be higher. Relatively slower.
Under the same conditions, the thinner the wall thickness of the product, the more uniform the deformation of the product along the cross-section, and the smaller the tendency to produce extrusion cracks. Therefore, the extrusion speed can be faster.
2. Influence of deformation degree
The greater the degree of deformation of aluminum profile products, the greater the extrusion force required, and the greater the heat of metal deformation, so the outflow speed of the product is slower; on the contrary, the degree of deformation is small and the metal flow is uniform, and the extrusion speed can be faster.
3. Influence of mold structure
When extruding aluminum alloy profiles, which type of core to use is determined by the characteristics of the profile. Generally, the solid profile adopts a flat die, and the hollow profile adopts a tongue type or a split combination die.
For 6063 aluminum alloy, the flat die has less resistance than the tongue die or the split die, so the extrusion speed can be higher. For the mold core with the same structure, the wider the working belt of the mold core, the greater the friction between the alloy and the working belt surface, the greater the additional tensile stress on the surface of the product, and the higher the tendency of extrusion cracks on the surface of the product. Therefore, the extrusion speed needs to be reduced accordingly.
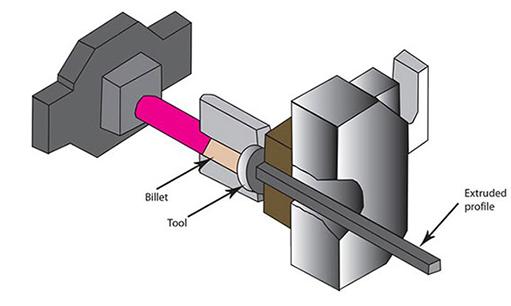
Secondly, from the perspective of the surface friction between the metal and the core working belt, the harder and smoother the core working belt, the faster the extrusion speed should be.
4 Extrusion Processes to Increase Extrusion Speed
With the development of modern technology, a new process to increase the extrusion speed has emerged, and new extrusion processes such as isothermal extrusion, isobaric extrusion, constant velocity extrusion, high-temperature extrusion, low-temperature extrusion, and nitrogen cold extrusion have been developed.
1. Isothermal extrusion process
Isothermal extrusion is to keep the temperature in the deformation zone within a constant range by automatically adjusting the extrusion speed, to achieve the purpose of rapid extrusion. In particular, some equipment is also equipped with a microcomputer device to achieve automatic control extrusion. The purpose of pressing speed.
2. Low-temperature rapid extrusion process
Low-temperature rapid extrusion temperature adopts 440~460C. This technology was applied earlier in Japan’s Beijing Aluminum Company. They used 430C to extrude 6063 aluminum alloy, the extrusion speed was 30~50 m/min, the upper limit was taken for the flat die, and the lower limit was taken for the hollow die.
The low-temperature technology refers to the temperature of the mold entering, and the temperature of the mold exit must reach the optimum temperature range of air cooling and quenching (515~525C), otherwise, the hardness and strength of the profile are unqualified. How to achieve the proper mold release temperature during extrusion is the trick of applying this technology.
3. High-temperature slow extrusion process
High temperature and slow extrusion temperature is 500~520°C, and it must not be fast during extrusion. The reason for this is:
- When the mold release temperature is higher than 525°C and the air cooling is insufficient, the product often has a large and coarse grain structure;
- Magnesium and silicon cannot be completely dissolved, and the hardness and strength of the alloy are low;
- For split-flow combined die, if the extrusion is too fast, the temperature is high, and the metal supply is insufficient, a loose structure will be formed along the split line, which will be easily corroded and exposed during alkali cleaning, which will affect the quality of the post-processing profile. So the extrusion speed should be slower.
4. Nitrogen cold extrusion process
During the extrusion process, cold liquid nitrogen stored in tanks is introduced to the working belt of the extrusion die.
- It can reduce the contact friction between the product and the core working belt;
- It can cool the extrusion die and deformation zone, and take away the heat of deformation. At the same time, the exit of the core is controlled by nitrogen, which not only reduces the oxidation of the product surface but also reduces the adhesion and accumulation of alumina.
Therefore, nitrogen cold extrusion not only improves the surface quality of the product but also greatly increases the extrusion speed.