As we know that aluminum is a common material in the die-casting process. Die-casting aluminum brings great convenience to our lives and is used in a wide range of markets. So do you know the difference between finale aluminum and finale aluminum alloy? If you don’t know enough, then this article will take you to understand the difference behind this in detail.
Two Main Types of Casting Aluminium
The casting aluminum alloy process is divided into two categories: sand casting and special casting. Special casting is more suitable for automotive aluminum alloy processing. Sand casting is the most traditional casting method for producing castings in sand molds, but the product accuracy is not high and the productivity is low; although gravity casting, which is further developed on its basis, can further improve the problem, it also has limitations on the volume of castings and requires strict control. Otherwise, the mold temperature will affect the quality of the casting.
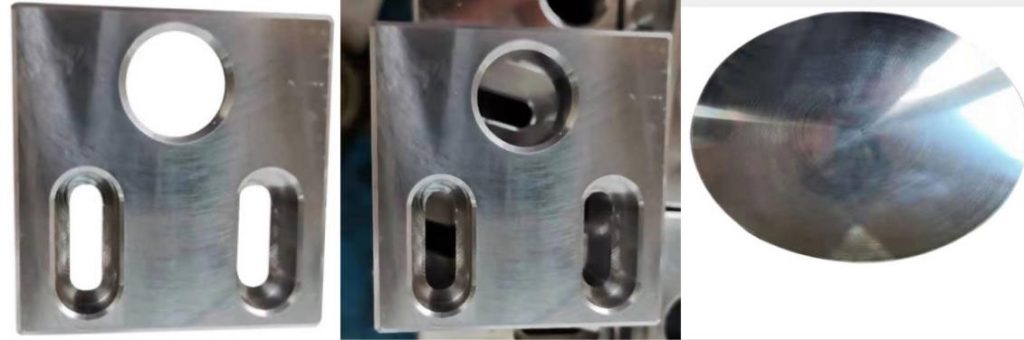
Therefore, sand casting is not widely used in auto parts. Casting processes other than sand casting are collectively referred to as special casting, including pressure casting, squeeze casting, centrifugal casting, and continuous casting. Among them, the die casting process is the most mature and efficient; the mechanical properties of the squeeze casting products are better than those of the general die casting process, and they have the advantages of high utilization rate of liquid metal, simplified procedures and stable quality, but it is difficult to produce components with complex structures, which affects the scope of product application.
The production of centrifugal and continuous casting products is relatively fixed. Centrifugal casting is generally used to produce tubular appliances, and continuous casting is used to produce long castings with unchanged cross-sectional shapes. Die casting is one of the most mature and efficient manufacturing technologies in the casting process and currently accounts for over 70% of automotive castings. Die casting is a manufacturing process that uses high pressure to press molten metal into a mold and cool it under pressure to form. According to the data analysis of China Nonferrous Metals Processing Industry Association, the proportion of aluminum die castings for automobiles is over 70%.
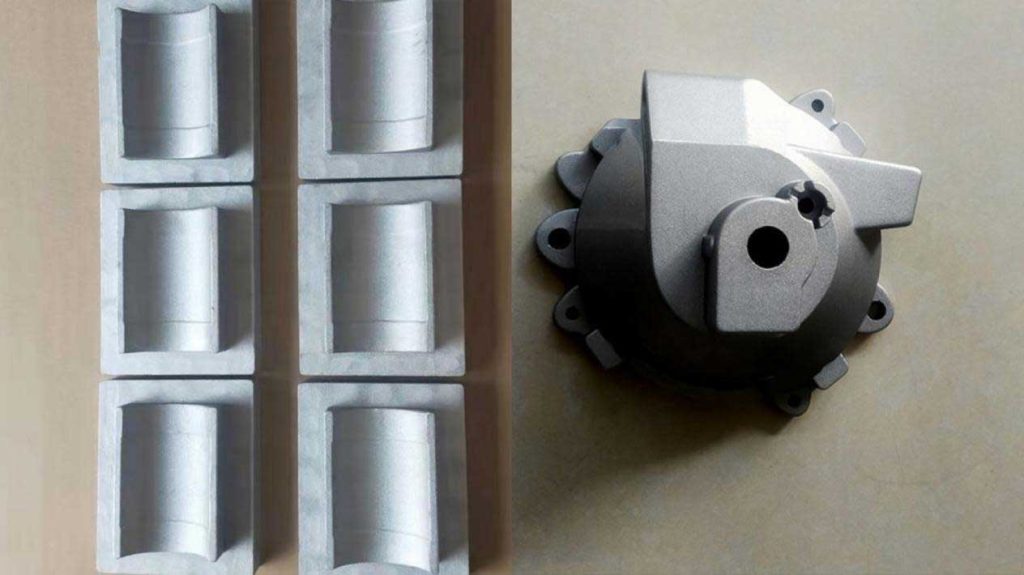
Difference Between Casting Aluminium and Aluminium Alloy
There is only one-word difference between casting aluminum and aluminum alloy. Many people mix the two together. In fact, these two types of die-casting are different. In order to better distinguish between casting aluminum and aluminum alloy, we will discuss the performance characteristics, application range and production advantages in detail. Explain the difference between the two. When purchasing die-casting products, customers can also choose suitable die-casting products according to their own needs.
- Aluminum Die Casting
The main raw material is aluminum. After the aluminum is heated to a liquid, it is injected into the mold of the die-casting machine and formed by die-casting, which is the basic process of aluminum die-casting. Aluminum has good fluidity and plasticity, and is widely used in the die-casting industry. The parts made of aluminum have a beautiful appearance, the price of aluminum is not high, and the production cost is greatly reduced, creating more wealth for the enterprise.
- Aluminum Alloy Die Casting
The main production materials are alloys and aluminum. The aluminum die-casting produced has good gloss. The aluminum die-casting factory needs to be ground after the die-casting molding. The aluminum die-casting adds nitric acid during grinding to inhibit corrosion and improve the grinding brightness. The processed aluminum die-casting Aluminum alloy die-casting is generally used in electronics, motors and other industries. It has better performance and greater toughness, and is an important part of mechanical components.
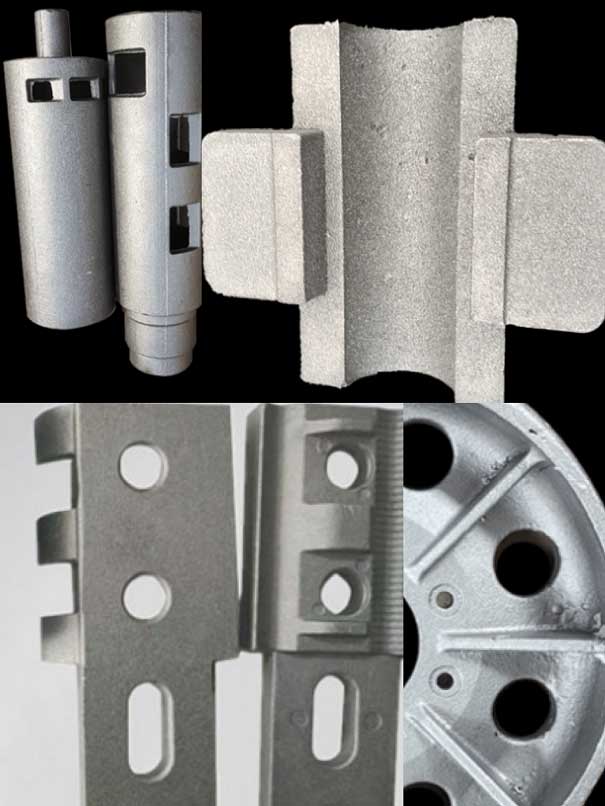
Advantages of Casting Aluminium Products
- Aluminum alloy has good thermal conductivity, electrical conductivity and cutting performance;
- Aluminum alloy wire shrinks less, so it has good filling performance;
- Aluminum alloy has a low density and high strength, and the ratio of its tensile strength to density is 9 to 15, it also maintains good mechanical properties when working at high temperature or low temperature;
- Aluminum alloy has good corrosion resistance and oxidation resistance, most aluminum alloys are in freshwater, seawater, concentrated nitric acid, nitric acid, hydrochloric acid, etc. It has good corrosion resistance in gasoline and various organic substances.
Advantages of Die Casting
- The metal liquid is subjected to high pressure and fast flow rate during die casting;
- The product quality is good, the size is stable, and the interchangeability is good;
- The production efficiency is high, and the die-casting mold is used many times; Mass production, good economic benefits.
Conclusion
Previously, the die-casting process was mainly used for engine cylinder heads and cylinder blocks, cantilever frames, transmissions, generator brackets, clutch shells, and automotive air-conditioning compressors. The body structure extends in the same direction. CHAL is an aluminum producer who can support various machined aluminium products, has customers around the world, with a good reputation, no doubt you will get the best product from here.