Aluminum cables have become increasingly popular due to their affordability and lightweight nature. However, for specific applications, understanding the limitations of regular aluminum cables and exploring the benefits of their enhanced version – aluminum alloy cables – becomes crucial. This article delves into the detailed differences between these two cable types, focusing on their composition, properties, applications, and factors to consider when making a choice.
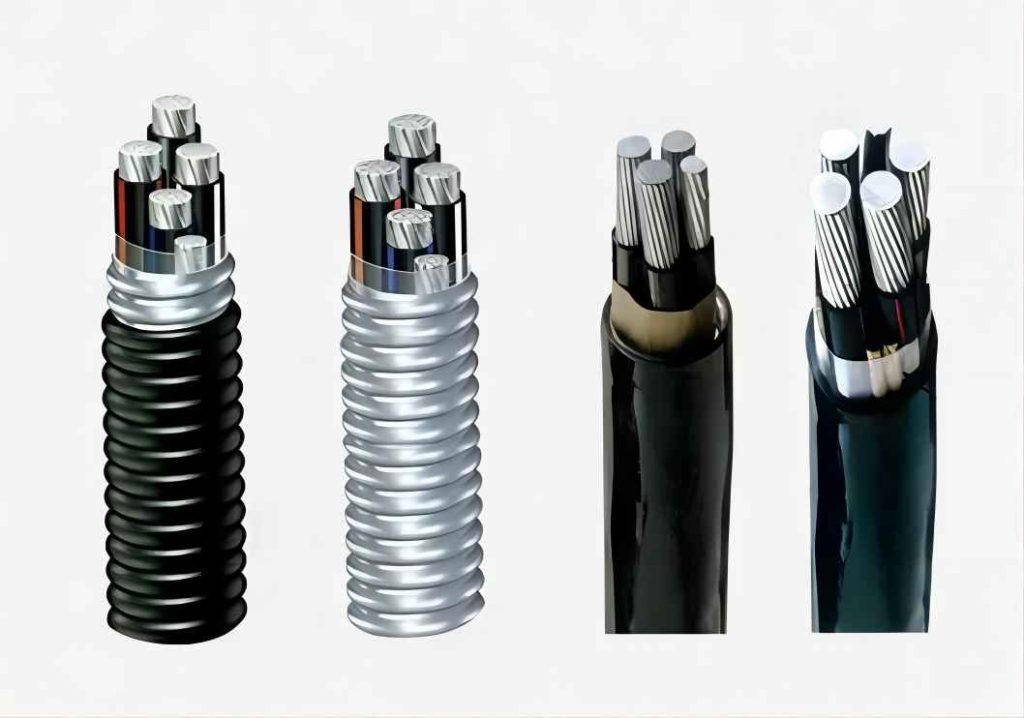
Compositional Differences: Unveiling the Core Elements
The primary distinction between the two lies in their composition. Aluminum cables are primarily composed of pure aluminum, with a minimum content of 99.5%. This high purity level ensures good electrical conductivity, making them suitable for various applications. However, pure aluminum possesses inherent limitations in terms of mechanical strength.
Aluminum alloy cables, on the other hand, take a step further by incorporating trace elements into the pure aluminum base. These elements, typically silicon, magnesium, or manganese, are added in small quantities to enhance specific properties of the cable without significantly affecting its conductivity. This addition results in a material with improved mechanical strength and durability, making it a viable alternative for applications where pure aluminum might not be sufficient.
Property Divergence: Understanding the Impact on Performance
While both cable types share the ability to conduct electricity, certain properties differ significantly, impacting their suitability for various applications.
1. Conductivity
Aluminum alloy conductors are new conductor materials that are formed by adding rare earth, magnesium, copper, iron, and other elements to pure aluminum and then processed using alloying technology. It is well known that when other alloying elements are added to aluminum, the conductivity will decrease. However, through process control, the conductivity can be restored to a level close to that of pure aluminum, so that it has a similar current carrying capacity to pure aluminum.
2. Mechanical Strength
a. Tensile strength and elongation
Aluminum alloy conductors have higher tensile strength and elongation than pure aluminum conductors. This is because the alloying elements that are added to aluminum alloys, such as magnesium and copper, can increase the alloy’s strength and ductility. This makes aluminum alloy conductors more resistant to breaking and more reliable.
b. Bending performance
Aluminum core cables have poor bending performance and are easily broken when bent. Aluminum alloy power cables have a bending radius of 7 times the cable diameter, which is far superior to the 10-20 times the cable diameter specified in GB/T12706 “Minimum Bending Radius of Cables During Installation”.
c. Flexibility
Pure aluminum cables can crack or break after only a few twists at a certain angle, which can easily lead to accidents. Aluminum alloy power cables can withstand dozens of bends, eliminating the hidden dangers of accidents that occurred during the installation and use of pure aluminum cables in the past, and greatly improving safety and reliability.
3. Corrosion Resistance
Pure aluminum has better corrosion resistance than copper, but aluminum alloy has even better corrosion resistance than pure aluminum. This is because the alloying elements that are added to aluminum alloy, such as rare earth elements, can increase the alloy’s resistance to corrosion, especially electrochemical corrosion. This solves the problem of electrochemical corrosion that occurs at the joints of pure aluminum cables over time.
4. Creep Resistance
Aluminum alloy cables are gradually entering the domestic market because of the shortage of copper metal resources and the continuous increase of copper prices. Aluminum alloy materials have advantages over copper in terms of toughness, tensile strength, and weight. In addition, under the same current carrying capacity, the cross section of aluminum alloy is only 1.1-1.2 times larger than that of copper. The price is also lower than the copper price.
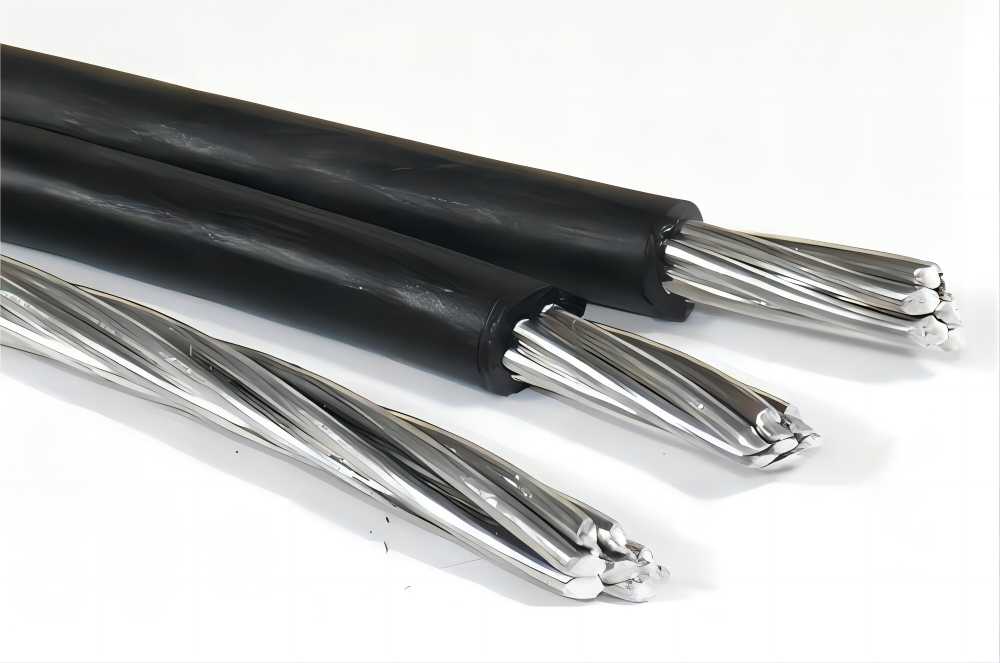
5. Weight
Both aluminum and aluminum alloy cables are considerably lighter than their copper counterparts. This weight advantage makes them ideal for applications where weight reduction is crucial, such as in overhead power lines and aircraft wiring. However, it is worth noting that the addition of trace elements in the alloy can lead to a slight increase in weight compared to pure aluminum cables.
6. Cost
While both are significantly cheaper than copper, there is a subtle cost difference between the two. Pure aluminum cables are the most cost-effective option, followed by aluminum alloy cables. The additional processing and element inclusion in the alloy contributes to the slightly higher cost.
Application Diversification: Choosing the Right Cable for the Job
The choice between aluminum and aluminum alloy cables depends heavily on the specific application and its requirements. Here, we explore some scenarios where each type excels:
1. Aluminum Cables
Widely used in overhead power lines: Due to their affordability and lightweight properties, aluminum cables are a popular choice for overhead power lines. Their high conductivity makes them efficient for transmitting electricity over long distances.
Limitations in applications with high physical stress or vibrations: However, their lower mechanical strength can limit their suitability in applications where they might encounter significant physical stress or vibrations. These scenarios can lead to cable damage and potential safety hazards.
2. Aluminum Alloy Cables
The enhanced strength and durability of aluminum alloy cables solidify their position as the preferred choice for a variety of applications, including:
- Underground power distribution networks: Their ability to withstand the physical demands of being buried makes them suitable for underground power distribution networks.
- Building wiring applications: The improved strength of these cables makes them well-suited for building wiring, particularly in areas prone to vibrations or movement. This ensures the cables remain securely in place and function reliably over time.
- Automotive applications: Combining their lightweight nature with improved strength compared to pure aluminum, these cables are increasingly utilized in the automotive industry for various electrical components. This combination contributes to both vehicle performance and weight reduction.
Factors to Consider Choosing the Right Cables
When making a choice between aluminum and aluminum alloy cables, it is crucial to consider the following factors:
- Application requirements: Analyze the specific demands of the application, including the expected electrical load, physical stress, and environmental conditions.
- Cost considerations: While aluminum cables are generally cost-effective, the slightly higher cost of the alloy might be justified if the application demands improved strength and durability.
- Weight limitations: If weight reduction is a critical factor, both aluminum options offer a significant advantage over copper. However, the slight weight increase of the alloy should be considered if minimizing weight is paramount.
- Regulations and standards: Certain applications might have specific regulations or standards regarding the type of cable allowed. It is crucial to ensure the chosen cable complies with all relevant regulations.
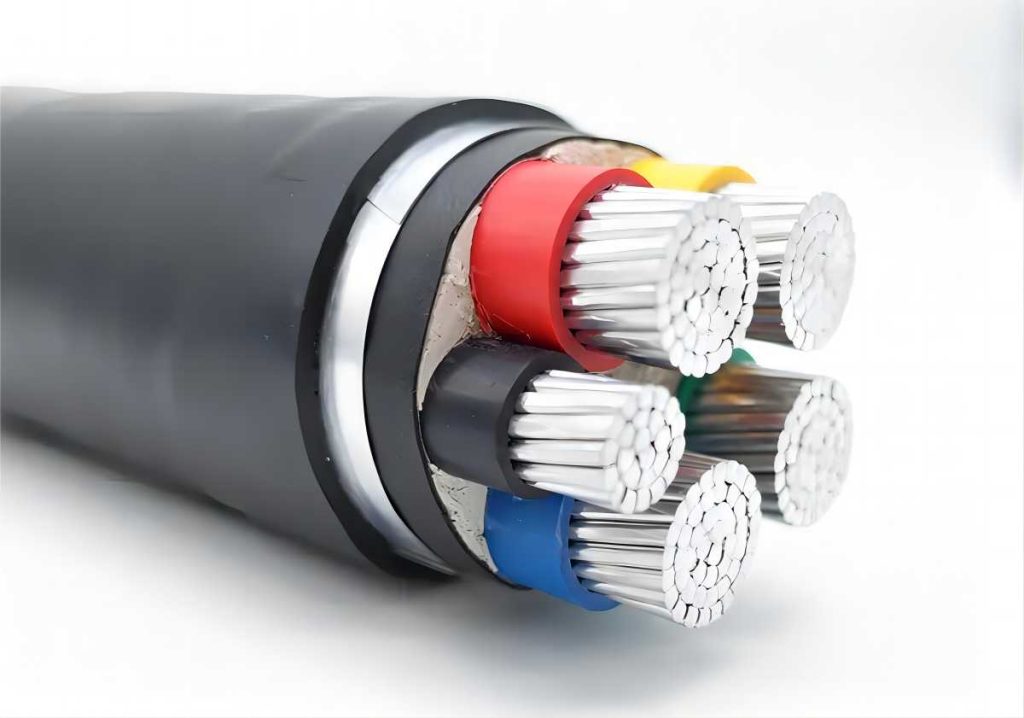
Conclusion
Understanding the fundamental differences between aluminum and aluminum alloy cables empowers engineers, electricians, and individuals to make informed decisions when selecting the appropriate cable for their specific needs. While aluminum cables offer affordability and lightweight properties, their limitations in strength might not be suitable for all applications. Conversely, aluminum alloy cables provide the necessary strength and durability in situations where pure aluminum falls short, albeit at a slightly higher cost. Ultimately, a comprehensive understanding of both options, coupled with careful consideration of the application’s specific requirements, ensures the selection of a reliable, cost-effective, and long-lasting cable solution.