Aluminum MIG welding is a versatile and efficient method for joining aluminum components. This process utilizes a consumable electrode, known as aluminum MIG wire, to create a strong and durable weld. Different types of aluminum MIG wire are available, each with its own unique characteristics and applications. In this comprehensive guide, we will delve into the world of aluminum MIG wire, exploring its properties, types, and applications.
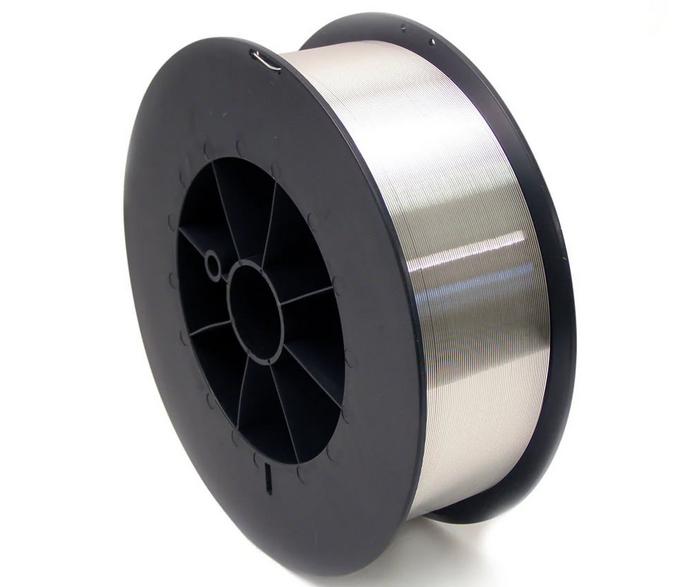
Understanding What Is Aluminum MIG Wire
Aluminum MIG wire, also referred to as GMAW (Gas Metal Arc Welding) wire for aluminum, is a specialized filler metal specifically designed for MIG welding aluminum alloys. It consists primarily of aluminum, along with various alloying elements that enhance its properties and weldability. The most common alloying elements include silicon, magnesium, and manganese.
Types of Aluminum MIG Wire
There are two primary types of aluminum MIG wire: 5356 and 4043. Each type offers distinct characteristics and applications that make them suitable for different welding scenarios.
5356 Aluminum MIG Wire
5356 aluminum MIG wire is a popular choice for structural aluminum welding due to its high strength and good corrosion resistance. It is composed of approximately 95% aluminum, 3.5% magnesium, and 1.5% silicon. The magnesium content contributes to the wire’s strength and weldability, while the silicon enhances fluidity and reduces cracking.
Characteristics of 5356 Aluminum MIG Wire
- High tensile strength: 5356 aluminum MIG wire offers excellent tensile strength, making it suitable for applications where structural integrity is critical.
- Good corrosion resistance: 5356 aluminum MIG wire exhibits good corrosion resistance in various environments, including marine settings.
- Easy to weld: 5356 aluminum MIG wire is relatively easy to weld, making it a good choice for both experienced and novice welders.
Applications of 5356 Aluminum MIG Wire
- Welding structural aluminum: 5356 aluminum MIG wire is widely used for welding structural aluminum components, such as those found in buildings, bridges, and vehicles.
- Welding marine aluminum: The corrosion resistance of 5356 aluminum MIG wire makes it a suitable choice for welding marine aluminum structures, such as boats and ships.
- Welding aircraft aluminum: 5356 aluminum MIG wire is also used in the aerospace industry for welding aircraft components.
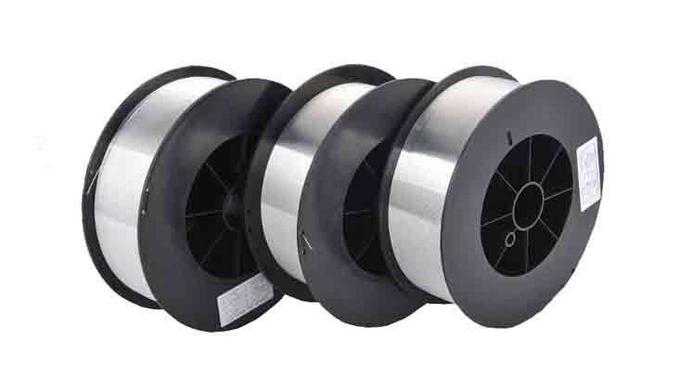
4043 Aluminum MIG Wire
4043 aluminum MIG wire is known for its excellent flow and good appearance, making it a popular choice for welding non-structural aluminum. It is composed of approximately 95% aluminum and 5% silicon. The high silicon content contributes to the wire’s fluidity and low melting point, resulting in smooth welds with minimal distortion.
Characteristics of 4043 Aluminum MIG Wire
- Excellent flow: 4043 aluminum MIG wire flows smoothly through the welding torch, producing consistent and even weld beads.
- Good appearance: The welds produced with 4043 aluminum MIG wire have a good appearance, making it suitable for applications where aesthetics are important.
- Non-heat treatable: 4043 aluminum MIG wire is not heat treatable, meaning it cannot be strengthened through heat treatment.
Applications of 4043 Aluminum MIG Wire
- Welding non-structural aluminum: 4043 aluminum MIG wire is primarily used for welding non-structural aluminum components, such as those found in housings, enclosures, and signage.
- Welding thin-gauge aluminum: The excellent flow and low melting point of 4043 aluminum MIG wire make it a good choice for welding thin-gauge aluminum, where minimizing distortion is crucial.
- Welding aluminum with minimal distortion: 4043 aluminum MIG wire is often used for welding aluminum applications where minimal distortion is required, such as welding sheet metal or cosmetic parts.
Aluminum MIG Wire 5356 vs 4043
When selecting between 5356 and 4043 aluminum MIG wire, it is essential to consider the specific requirements of the welding application. Here’s a comparison of the two wire types:
Strength
- 5356 aluminum MIG wire is stronger than 4043 aluminum MIG wire.
- For applications where high strength is critical, 5356 is the preferred choice.
Corrosion Resistance
- 5356 and 4043 aluminum MIG wires have similar corrosion resistance.
- Both wires are suitable for welding in various environments, including marine settings.
Weldability
- 4043 aluminum MIG wire is easier to weld than 5356 aluminum MIG wire.
- The excellent flow of 4043 makes it easier to control and produce consistent welds.
Appearance
- 4043 aluminum MIG wire produces welds with a better appearance than 5356 aluminum MIG wire.
- The lower silicon content of 4043 results in welds with less porosity and smoother surfaces.
Applications
- 5356 aluminum MIG wire is a good choice for structural aluminum applications where high strength and corrosion resistance are required.
- 4043 aluminum MIG wire is a good choice for non-structural aluminum applications where appearance and minimal distortion are important.
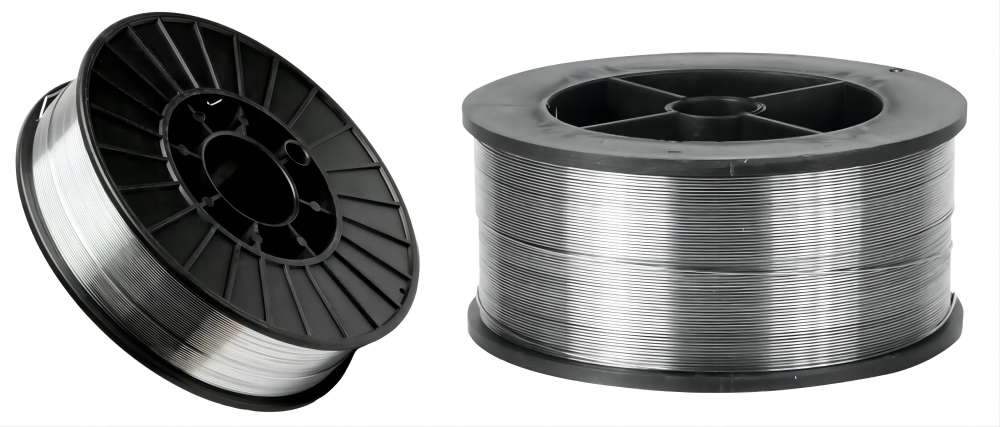
Conclusion
The selection of the appropriate aluminum MIG wire depends on the specific requirements of the welding application. 5356 aluminum MIG wire offers high strength and good corrosion resistance, making it suitable for structural applications. In contrast, 4043 aluminum MIG wire provides excellent flow and good appearance, making it ideal for non-structural applications where aesthetics are important.
In general, 5356 aluminum MIG wire is a versatile and reliable choice for various welding applications. It is relatively easy to weld and offers a balance of strength, corrosion resistance, and weldability. However, for applications where appearance is paramount or where thin-gauge aluminum is being welded, 4043 aluminum MIG wire is a better option due to its superior flow and low distortion characteristics.