According to the usual estimation method, the direct economic loss caused by corrosion in China accounts for about 3% of GDP (gross national product) every year, and the steel consumed due to corrosion accounts for about 1/3 of the annual output, which accounts for about 1/1 of the total output. 10 is not recyclable.
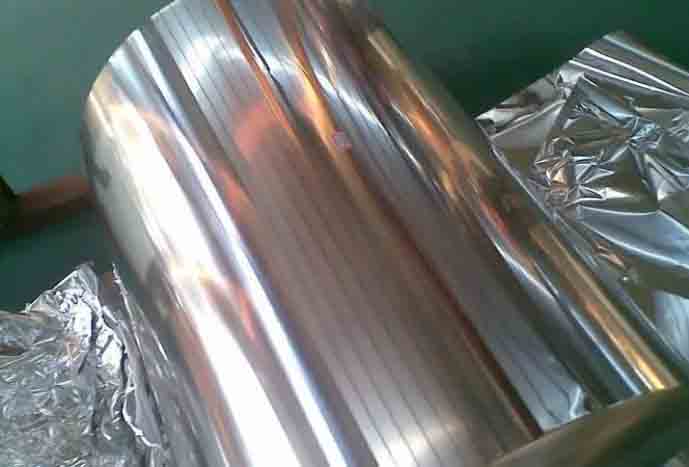
The corrosion resistance of aluminum and aluminum alloys is much higher than that of steel, and the corrosion loss is much smaller than that of steel, but no matter what metal material, no matter how high the corrosion resistance is, it will always be more or less in use. Corrosion loss occurs. The annual aluminum corrosion loss is about 0.5% of the annual aluminum production.
The corrosion of aluminum and aluminum alloys mainly includes pitting corrosion, intergranular corrosion, stress corrosion cracking, and layered corrosion. The 6000 series alloy has the largest output among the deformed aluminum alloys. Although its corrosion resistance is not as good as that of the 1000 series, 3000 series, and 5000 series aluminum alloys, it is much higher than the 2000 series and 7000 series aluminum alloys. The intergranular tendency of 6000 series alloys is also relatively large, and the 6000 series aluminum alloy materials used for important structures should be evaluated for intergranular corrosion susceptibility.
Classification of Aluminum Corrosion
From the appearance of corrosion, the corrosion of aluminum can be divided into general corrosion and local corrosion. The former is called uniform corrosion, also known as overall corrosion, which means that the material’s surface in contact with the environment is uniformly corroded and lost.
The aluminum corrosion in an alkaline solution is typical uniform corrosion, such as alkaline washing; the corrosion result is that the aluminum surface is thinned at approximately the same rate, and the quality is reduced. It should be pointed out. However, that uniform corrosion does not exist, and the reduction in thickness varies from place to place.
Localized corrosion means that the occurrence of corrosion is limited to a specific area or part of the structure and can be divided into the following categories:
Pitting
Pitting corrosion occurs in very localized areas or parts of the metal surface, causing caves or pits to expand and even cause perforations. If the diameter of the pit opening is smaller than the depth of the pit, it is called pitting corrosion; if the diameter of the pit opening is greater than the depth of the pit, it can be called pitting corrosion. There is no strict boundary between pitting and pitting.
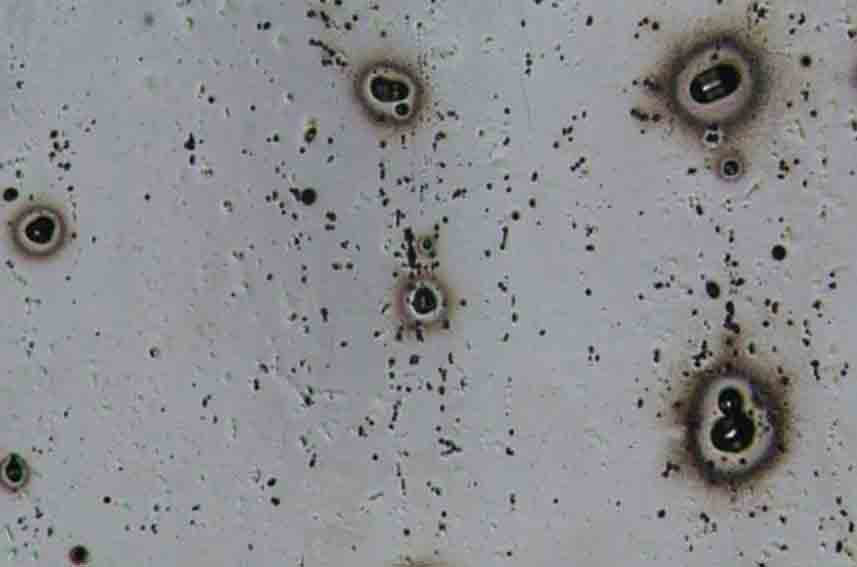
Typical pitting corrosion of aluminum in chloride-containing aqueous solutions. Among aluminum corrosion, pitting corrosion is the most common, which is caused by the potential of a certain area of aluminum being different from that of the substrate or by the presence of impurities whose potential is different from that of the aluminum substrate.
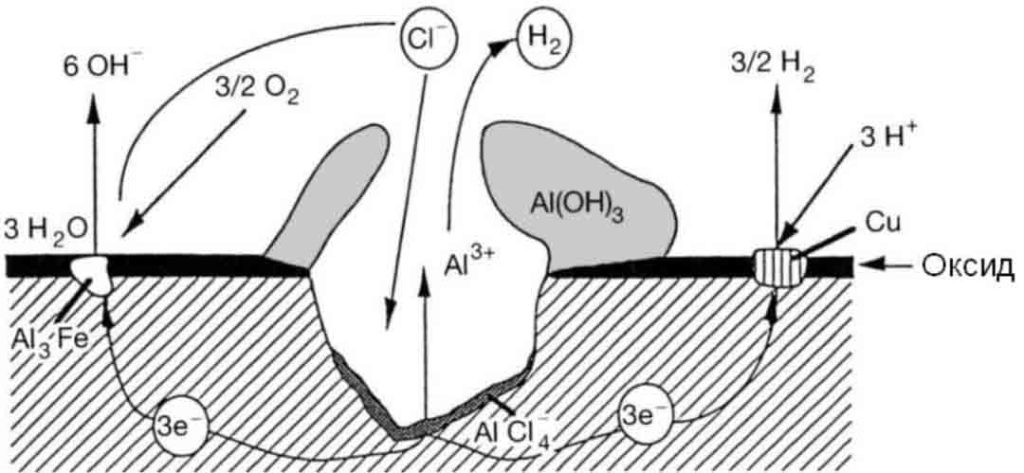
Intergranular corrosion
This kind of corrosion is selective corrosion that occurs at the grain boundaries of metals or alloys when the grains or crystals themselves are not significantly eroded, drastically reducing the mechanical properties of materials, and resulting in structural damage or accidents.
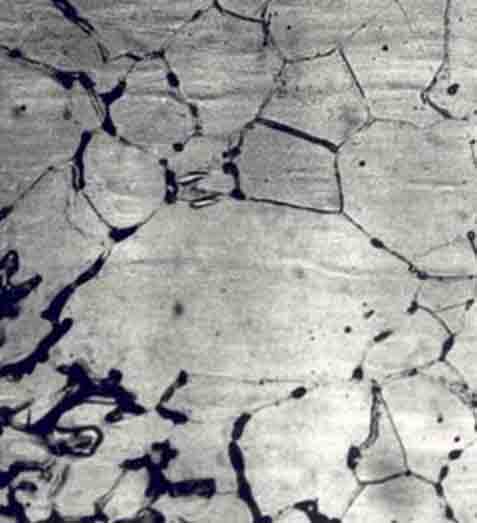
The reason for intergranular corrosion is that the grain boundary is very active under certain conditions, such as impurities at the grain boundary or an increase or decrease of an alloying element at the grain boundary; that is to say, there must be a thin layer on the grain boundary for the rest of the aluminum. Part of the electronegative region corrodes preferentially. Such corrosion can occur in high-purity aluminum in hydrochloric acid and high-temperature water. Al-Cu, AI-Mg-Si, Al-Mg, and Al-Zn-Mg alloys are all sensitive to intergranular corrosion.
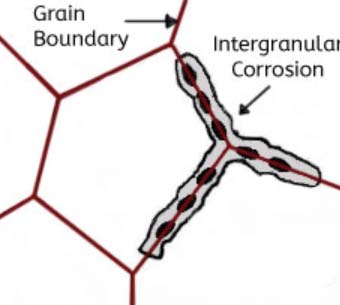
Galvanic corrosion
Galvanic corrosion is also a characteristic corrosion form of aluminum. Galvanic corrosion occurs when a less reactive metal and a more reactive metal, such as aluminum (anode), come into contact in the same environment or when conductors are connected, forming a galvanic couple and causing the current flow.
Galvanic corrosion is also known as bimetallic corrosion or contact corrosion. The natural potential of aluminum is very negative. When aluminum is in contact with other metals, aluminum is always anodic, and corrosion is accelerated. Almost all aluminum and aluminum alloys cannot avoid galvanic corrosion. The greater the potential difference between the two metals in contact, the more serious the galvanic corrosion.
It should be noted that in galvanic corrosion, the area factor is extremely important, and a large cathode and a small anode are the most unfavorable combination.
Stress corrosion cracking
Stress corrosion cracking is caused by the coexistence of tensile stress and specific corrosive media. Stress can be external or residual stress inside the metal; the latter may be caused by deformation during processing or caused by severe temperature changes during quenching, or volume changes caused by changes in internal structure.
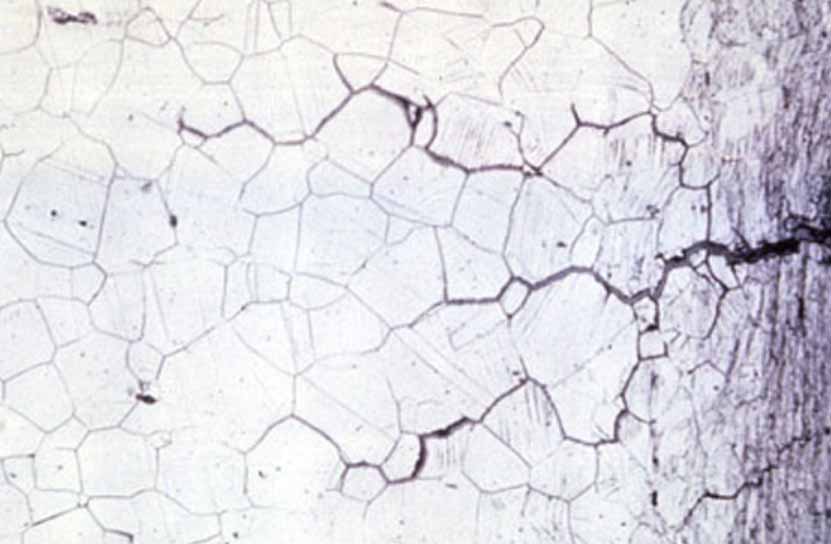
The stress caused by riveting, bolt tightening, press fit, and shrink fit is also residual stress. When the tensile stress on the metal surface reaches the yield strength Rp0.2, stress corrosion cracking will occur. The 2000 series and 7000 series aluminum alloy thick plates are in Residual stress will be generated during quenching, which should be eliminated by pre-stretching before aging treatment to avoid deformation or even carry into the parts when processing aircraft parts.
Laminar corrosion
Also known as delamination, exfoliation, and layered corrosion, it can be referred to as debonding. It is a special corrosion form of 2000 series, 5000 series, 6000 series, and 7000 series alloys. It is more common in extruded materials. Once it occurs, it can be like mica. Peel off layer by layer.
Filiform corrosion
It is a kind of corrosion that can develop in a worm-like form under aluminum paint film or other coatings, but no such corrosion under anodized film has been found, which generally occurs under the coating of aircraft aluminum structures and architectural or structural aluminum parts.
Filiform corrosion is related to material composition, pre-coating pretreatment, and environmental factors. Environmental factors refer to temperature, humidity, chlorides, and the like.