Aluminum alloys have played a pivotal role in modern engineering, offering a combination of lightweight properties and high strength. Among these alloys, 7075 aluminum stands out as a remarkable material due to its impressive composition and characteristics. In this article, we will delve into the components and properties of 7075 aluminum alloy, as well as its versatile applications.
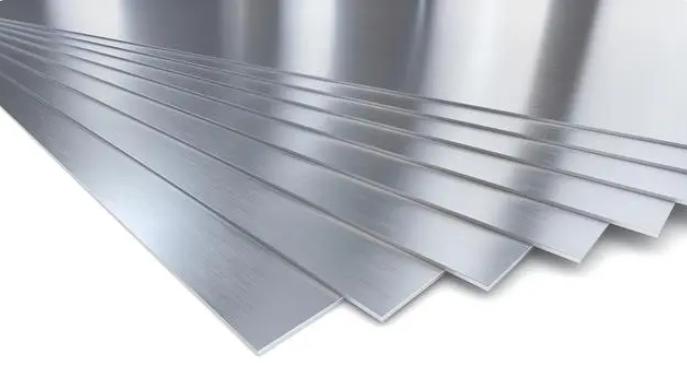
Understanding What is 7075 Aluminum Alloy
7075 is an aluminum alloy that has been cold-treated and forged, endowing it with superior strength compared to conventional steel. It is considered one of the most robust aluminum alloys used in commercial applications. The 7075 aluminum alloy boasts a dense structure and strong corrosion resistance, making it particularly suitable for aerospace and marine applications. Its general corrosion resistance, excellent mechanical properties, and anodic reaction make it highly sought after. Additionally, its fine grain structure enhances deep-hole drilling performance and tool wear resistance.
Main Alloying Elements
The primary alloying element in 7075 aluminum is zinc. The addition of magnesium in alloys containing 3% to 7.5% zinc forms MgZn2, which significantly enhances the alloy’s heat treatment effectiveness compared to aluminum-zinc binary alloys. Increasing the zinc and magnesium content in the alloy further improves its tensile strength but may reduce its stress corrosion resistance and exfoliation corrosion resistance. After heat treatment, extremely high strength properties can be achieved. Typically, small amounts of copper, chromium, and other alloys are also added to 7075 aluminum. Among these variations, 7075-T651 aluminum alloy stands out as exceptional and is often hailed as the best aluminum alloy product. It offers high strength, surpassing conventional steel by a considerable margin. This alloy also exhibits excellent mechanical properties and anodic reaction. Typical applications include aerospace, mold processing, machinery equipment, and fixture tools, especially in the production of high-strength and corrosion-resistant aircraft structures and other high-stress components.
Characteristics of 7075 Aluminum Alloy
7075 aluminum alloy is a cold-treated alloy known for its high strength and hardness, surpassing that of common steel. It exhibits general corrosion resistance, excellent mechanical properties, and anodic reaction. Its fine grain structure enhances deep-hole drilling performance, improves tool wear resistance, and facilitates thread rolling. This makes it the preferred choice for applications that demand low density and high hardness in a metal material.
The 7 Series Aluminum Alloys
The 7 series aluminum alloys belong to the Al-Zn-Mg-Cu superhard aluminum series. These alloys found their way into the aerospace industry in the late 1940s and have continued to be widely used in aviation. They are known for their good plasticity after solution treatment, particularly outstanding heat treatment strengthening, high strength at temperatures below 150°C, and excellent low-temperature strength. However, their welding performance is subpar, and they are prone to stress corrosion cracking. Protective treatments, such as aluminum coating, are often required. Secondary aging can enhance the alloy’s resistance to stress corrosion cracking. Its plasticity in the annealed and quenched state is slightly lower than 2A12 but better than 7A04 in the same state. The static fatigue and notch sensitivity of the plates are superior to 7A04, with a density of 2.85 g/cm³.
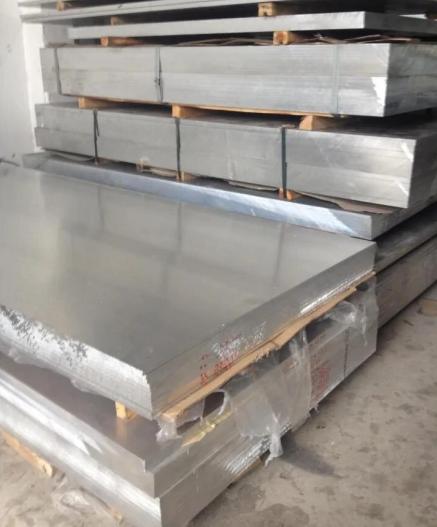
Physical and Mechanical Properties
- Tensile Strength: 524 MPa
- 0.2% Yield Strength: 455 MPa
- Elastic Modulus (E): 71 GPa
- Hardness: 150 HB
- Density: 2.81 g/cm³
Chemical Composition
- Silicon (Si): 0.40
- Iron (Fe): 0.50
- Copper (Cu): 1.2-2.0
- Manganese (Mn): 0.30
- Magnesium: 2.1-2.9
- Chromium (Cr): 0.18-0.28
- Zinc (Zn): 5.1-6.1
- Titanium (Ti): 0.20
- Aluminum (Al): Remaining balance
- Other (Individual): 0.05, Total: 0.15
Key Features of 7075 Aluminum Alloy
- High-strength heat-treatable alloy
- Excellent mechanical performance
- Good machinability
- Easy to work with and high wear resistance
- T7351 state enhances corrosion and fracture resistance
- Ideal for high-stress structural components
Applications of 7075 Aluminum Alloy
7075 aluminum alloy is widely employed in aerospace, mold processing, machinery equipment, and various other fields where high strength and corrosion resistance are required for high-stress structures. Its versatility, high strength, excellent mechanical properties, and corrosion resistance make it an ideal choice for numerous industrial applications.
Mechanical Performance
Unless otherwise specified, the properties of alloying elements in the combination are expressed as the highest percentage. To determine appropriate value ranges, observations or calculated values obtained from the analysis are represented within a defined range based on standard rules (ANSI Z25.1). Unless the alloy is non-alloyed, the specified quantity of elements in the alloy is usually indicated in the analysis report. However, if there is suspicion of additional or excessive elements during the analysis, further analysis is required until confirmation is obtained.
Unrefined non-alloyed aluminum contains the difference between the total amount of other metals and 100% pure aluminum—usually differing by 0.01% or slightly more (the second decimal place after the percentage point). It may contain up to 0.25% zirconium and titanium.
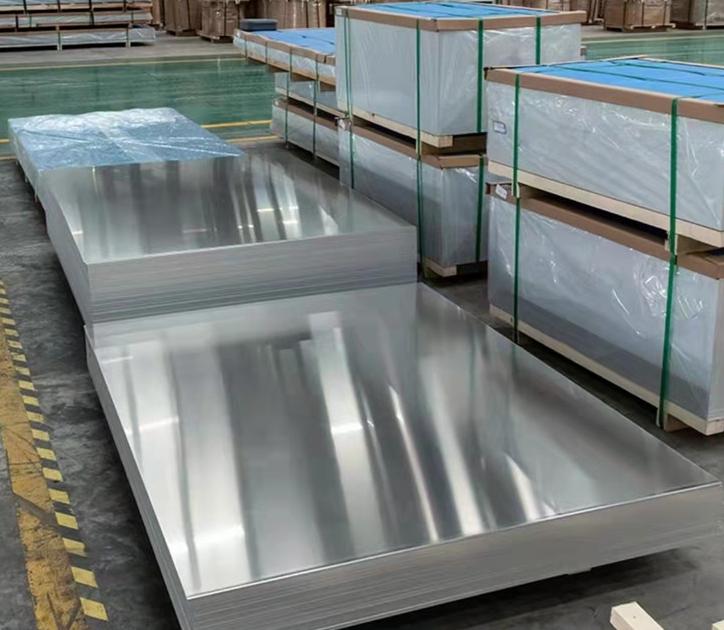
Conclusion
7075 aluminum alloy is a high-strength, corrosion-resistant cold-treated forging alloy that finds extensive applications in aerospace, aerospace, mold processing, machinery equipment, and more. Its high strength, excellent mechanical properties, and corrosion resistance can be further enhanced through heat treatment, making it suitable for manufacturing high-stress structures that demand strength and corrosion resistance. This alloy also exhibits excellent machinability, wear resistance, and heat resistance, making it an ideal choice for many industrial applications. Careful control of alloy elements and heat treatment processes is essential to ensure that the alloy performs with excellence and reliability in accordance with application requirements.
For reliable sources of 7075 aluminum alloy products, you can consider reputable manufacturers such as CHAL (China Aluminum Group Co., Ltd), known for their commitment to quality and innovation in the production of aluminum alloys.